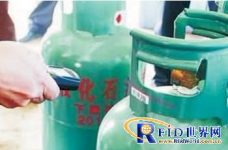
Hanyue RFID Cylinder Management Solution
[ad_1]
At present, there are many problems in the gas cylinder filling industry, such as unknown number of gas cylinders, unclear safety status, and unclear property rights information. The large circulation of gas cylinders in the society makes it difficult to implement safety responsibilities, causing great safety hazards.
Regular safety inspections cannot be implemented, or gas cylinder users do not use gas cylinders in accordance with safety requirements or illegally modify or refurbish gas cylinders, causing a large number of gas cylinders on the market that have not been inspected normally, some of which may have been damaged to varying degrees, and Unable to identify and verify, there are serious security risks.
Some units and individuals fill or pour gas between gas cylinders without permission. Some licensed gas cylinder filling units operate in violation of regulations, resulting in overfilling or wrong filling of gas cylinders, resulting in a large number of gas cylinder accidents occur.
The loss of property and the problem of not being able to trace back:
The number of internal gas cylinders in the industrial gas filling unit is unknown, and it is difficult to distinguish the internal gas cylinders from the external gas cylinders, which can easily cause the loss of their own property.
Management efficiency and cost issues:
Dynamic management of gas cylinders entering and exiting the filling station, testing station, and gas exchange station cannot be realized, and the inventory status, production and sales status cannot be controlled and inquired in real time.
It is difficult to strictly control the circulation of gas cylinders between various operations within the enterprise, and gas cylinders that have exceeded their service life or have been judged to be scrapped may enter the filling and circulation links.
The historical records of the circulation process of gas cylinders inside and outside the enterprise cannot be inquired, the root cause of the problem cannot be determined when needed, and the hidden danger of accident cannot be discovered in time, which may produce more serious consequences.
Although existing enterprises have partially used modern management methods, there is a gap in the integration of information applications and actual needs.
Plan to achieve goals
1. Perform dynamic statistics and management of gas cylinders entering and exiting filling stations and gas exchange stations. Industrial gas companies can know the production and sales status of gas at any time; statistics and certification of internal gas cylinders of industrial gas companies can prevent confusion or loss; Dynamic statistics and analysis of inventory cylinders and spare parts can restrict the circulation of cylinders that have not passed the safety inspection and ensure the safety of people’s lives and properties; it can conduct daily work in industrial gas companies, such as hazard inspections and the presence of personnel on duty. Confirmation and management
2. Identification of industrial gas cylinders
The only corresponding to the identification electronic tag of the industrial gas cylinder is a group of data information closely related to the gas cylinder. The label can be flexibly installed during installation, so that it can be removed and reinstalled during detection. The data in the label is stored through encryption, so the reinstalled label can be guaranteed to be the label of the system. Relevant enterprise operators can create files, edit and maintain this information through the system software. All operators and management personnel involved in the filling and circulation of gas cylinders can inquire part or all of the information through tag reading and writing equipment or management software according to their authority.
3. User identification and management
All users in the system are issued with readable and writable electronic tag user cards as the basis for identification and transaction. All users must first go to the company to go through the relevant procedures, receive the card and recharge. The delivery personnel send air to the door, confirm and deduct the corresponding amount of the user card through the tag handheld reading and writing device, and correspond the bottle number to it; or in the industrial gas station, the user can collect and return the gas bottle with the card, and the reading and writing device automatically judges the user card Whether it is legal and whether the number of gas cylinders on the card meets the requirements. When the conditions are met, the device automatically modifies the relevant information in the card, and the transaction data is immediately reported to the central management system.
4. Identification and management of operation personnel; industrial gas station receiving and dispatching management personnel; filling station entry management personnel; gas cylinder inspection personnel; gas cylinder filling personnel; gas cylinder entry and exit management personnel; equipment inspection personnel. System Information management personnel. Decision-making or corporate management personnel. System management and maintenance personnel. The system will issue a unique user card for each employee. The system automatically judges its legitimacy and authority and controls its operation during operations. . After each operation is completed, the reading and writing device will report its identification code and operation information to the central management system of the system. So as to achieve real-time tracking and inspection of all personnel operations. For the 7th to 9th types of users, the system directly checks the identity and authority through the user name and user password.
When the user returns the bottle, the handheld device determines whether the gas cylinder is a legal gas cylinder. Under no abnormal conditions, modify the current circulation status of gas cylinders to “at gas station”. Then send it to the filling station.
The operator in charge of entering the filling station uses a handheld device to register the received gas cylinder into the station. If there is a problem with the gas cylinder, the handheld device will start an alarm through text and sound, and the operator is asked to send the gas cylinder to the bottle inspection program. After the operator confirms, the cylinder is automatically set to the state to be inspected. In addition, if the inbound operator deems it necessary to inspect the steel cylinder based on actual judgment, the inspection can also be completed through a handheld device, and the steel cylinder will also be changed to a pending inspection state. If the cylinder enters the state to be inspected, the cylinder will be locked by the system before the registration of the inspection result is completed and the conclusion is qualified. If the steel cylinder is found at any link other than the bottle inspection, the handheld device will alarm and require the operator to deal with it. Cylinders that pass the bottle inspection and do not require bottle inspection can enter the filling process. For the sake of safety, the operator shall check and register with the handheld device again before filling, in order to eliminate the steel cylinders that have entered the process due to the negligence of the previous operations.
After the filling is completed, the operator uses the handheld device to register the filling result. If a problem is found, an alarm will be issued. When the filling weight does not meet the specified error requirements, it must be sent back to the filling process.
The filled steel cylinders are then sent to the designated warehouse, and the warehouse management personnel use the handheld device for warehousing registration. The outbound registration is carried out before the cylinders are sent to the industrial gas station.
Then, when the user provides a valid user card and the number of gas cylinders that can be collected meets the conditions, the user can withdraw the gas cylinders, and the handheld device is responsible for determining the user’s identity and registering the bottles. The user’s ventilation process uniformly replaces the industrial gas supply certificate printed with RFID electronic tags or bar codes, and completes registration so that the industrial gas company can keep track of the user’s usage. The user’s industrial gas supply certificate includes a ventilation ticket with an RFID electronic tag or bar code identification, which is scanned during ventilation and collected and managed by the industrial gas station staff to provide a basis for reimbursement with the industrial gas company. When the user ventilates, the employees of the supply station first use a handheld device to scan the RFID electronic tag or bar code of the supply certificate to confirm the user’s identity. Scan the empty bottles brought by users, dynamically add them to the database, record the empty bottles in storage, and then perform ventilation. After the user’s changed industrial gas is scanned, it is also dynamically added to the library, so that the database has a record of the daily out of the library. If the ventilation interval of a ventilation voucher is less than the set number of days, the system will automatically prompt and send out an alarm message to notify the staff to refuse to ventilate it; at the same time, it also avoids the phenomenon of personal fraud by the staff of the industrial gas station.
The testing station mainly includes incineration, pressure measurement, leak testing, shot blasting, painting, etc. The high temperature of the incinerator will cause the label to be damaged. In order to ensure the uniqueness of the gas cylinder information, remove the gas cylinder label before incineration. Attach an iron clip mark to the label and the gas cylinder, so that the entire information chain is connected, and the label of the gas cylinder is reinstalled, no matter how to ensure the uniqueness of the gas cylinder information, and avoid potential safety hazards.
Equipment inspection process by installing special electronic tags on important equipment, equipment inspection management can be realized, equipment maintenance personnel are urged to conduct regular inspections, and the system automatically records their inspection behaviors. If equipment maintenance personnel are found to be dereliction of duty, the system will notify immediately Related management personnel.
[ad_2]