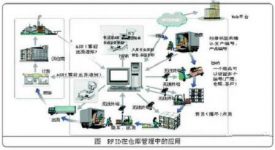
How to use RFID technology in computer room equipment management and solutions
[ad_1]
1. Introduction to the system
For companies, important fixed asset management has always been a headache. Check the actual accounts; understand the configuration parameters of important assets at a glance; master the operation and maintenance of important assets. How to accurately and quickly grasp the relevant information is the problem to be solved by this system.

RFID is a kind of radio frequency identification technology, which is composed of readers, antennas and tags. When the tag is close to the sensing range formed by the reader and antenna, the tag will send the data stored in the chip to the reader, and the reader will upload the data to the information system.
Due to the large amount of stored data, fast reading speed, and no need for human intervention in the process of reading data, RFID can perform rapid asset identification and inventory. Achieve accurate and rapid grasp of important fixed asset information.
The system consists of: electronic tags, fixed reading and writing equipment for on-site inventory, RFID handheld reading and writing equipment, multi-antenna splitter antenna, control computer and system management software, etc.
Second, the system architecture
The system hardware architecture includes: fixed readers, antennas, RFID handheld devices, tags and back-end servers;
Data exchange method: It can be implemented in two ways, choose one according to the cost requirements:
1) Online data exchange, real-time transmission of field data back to the background information system for processing and analysis through a fixed reader/writer;
2) Offline data exchange, after collecting the data in the field through the handheld device, import it to the background information system for processing and analysis;
The overall system structure is: Multi-tire C/S combined with Browser/Web Server/DB Server.

Three, business operation process
1. Encode the cabinet in the computer room, enter the coding information into the system and the RFID tag, and fix the RFID tag on the cabinet.
2. Encode the server, enter the encoded information into the system and the RFID tag, and fix the RFID tag on the server.
3. Arrange antennas and readers in the cabinet according to the requirements for reading the tag range.

Fourth, the server enters the computer room process
After querying the location of the cabinet in the computer room where the system server is placed, a list of production warehousing operations. The job list must at least include information such as the cabinet number and server number. The operation and maintenance personnel transport the server to the designated computer room according to the requirements of the operation list, and the personnel on duty in the computer room confirm the warehousing operation through the warehousing work order generated by the RFID handset. After the operation and maintenance personnel put the server in the designated location according to the requirements of the warehousing operation sheet, scan the cabinet number and server number through the RFID handheld to confirm that the operation is correct and complete the warehousing operation list. The staff on duty in the computer room confirms the cabinet number, server number and server location through the RFID handset to complete the warehousing work order.

Five, computer room inventory process
The person on duty in the computer room opens the system inventory interface and imports the inventory information to the RFID handset. The staff on duty first read the RFID tags of the cabinets for confirmation, and then read the tags of the servers in the cabinets in turn. If the tag data read in the cabinet is consistent with the inventory data imported to the handheld, the interface will be green, indicating that it has passed. If the inconsistent handset interface shows a red interface to indicate failure, you can choose to restart the inventory or end the inventory after checking. Finally, import the inventory data into the system.
[ad_2]