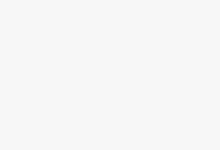
RFID asset management solution product inventory management and anti-counterfeiting and anti-channeling system solutions
[ad_1]
This program is only applicable to product inventory management and anti-counterfeiting management.
1. Overview
1.1 Construction background
At present, many manufacturers only record the batch number and quantity for the product, and do not manage and trace the whole box. The warehouse management uses the existing software to record the quantity of in and out of the warehouse, and the quantity of inventory. There is no management of the location, and the inventory management is not in place. Corresponding finished products and batches are relatively difficult, and accounting is not timely when entering and leaving the warehouse. At the same time, there is also the risk of human error. The goods after leaving the warehouse cannot be traced, and there is a risk of fleeing and being counterfeited.
In order to solve the above series of problems, scientifically manage the warehouse, use UHF technology to comprehensively manage the warehouse, upgrade the existing warehouse system, realize luggage code traceability, prevent cross-stocking, enter and exit the warehouse accurately in real time, visualize data, and operate by operators , The purpose of finding convenience, improving operation efficiency, greatly improving the level of warehouse management, and laying the foundation for subsequent warehouse management upgrades.
RFID technology has the following advantages in smart manufacturing:
1. There is no need to contact, the whole process does not need manual intervention, can complete the automatic data collection and is not easy to damage;
2. Information can also be collected for objects that are moving in the production state, and multiple cards can be recognized at the same time, making the operation more convenient;
3. It can be applied to a series of requirements such as harsh production environment, unreachable personnel, large data storage capacity, high real-time data transmission requirements, and reliable and effective data transmission.
Through the construction of the RFID system, it can accumulate experience for intelligent production and expand the direction for subsequent improvement of various problems in the production process. Generally speaking, RFID is very useful for real-time data collection in the working environment of intelligent manufacturing, warehousing, and logistics. Big application prospects can realize the integrated management of raw materials, factory manufacturing, warehousing, sales, and customer needs, and can flexibly produce on time, on-demand, and in-sequential production, realizing truly intelligent manufacturing.
1.2 Construction content
Through the construction of an intelligent warehouse system, this project realizes the information management of finished product packaging boxes, the number of finished products is checked with the actual warehousing quantity, automatic inspection and registration of warehousing and exiting, accurate and visual management of inventory products, efficient inventory management, and products that have been out of the warehouse. The box code traceability and anti-fleeing cargo management system communicates with the existing system in real time, synchronizes product production records, warehousing records to the factory system, and links with sales orders and bills of lading, combined with the forklift system to achieve full digital warehouse management, and the system provides Multi-dimensional complete production, storage, and inventory reports, and provide real-time inventory kanban by warehouse, and a sub-authorization anti-fleeing inquiry system. At the same time, the system reserves the corresponding data interface to provide support for later interaction with the MES system.
1.3 Construction ideas
UHF tags and NFC tags are used: UHF tags are used to achieve warehousing, asset inventory function NFC tags to achieve anti-counterfeiting and anti-fleeing verification functions, and the two are bound during assembly line production.
Associate the information on the product (color, location, production date, etc.) with the electronic tag TID and store it in the database. When scanning out and in the warehouse, scan through RFID ultra-high frequency technology in batches to obtain all the electronic tag TIDs. The barcode is uploaded to the database for query, and the operator will import the corresponding barcode into the system through batch processing.
1) Inbound and outbound scan inventory, batch scan the entire pallet luggage electronic tags through the RFID access control channel, realize the function of replacing the barcode scanner, export the results to the database, and the specific business system will perform batch processing to complete the batch import of barcodes;
2) Anti-counterfeiting and anti-tampering, through the bound NFC tag, consumers can scan the NFC tag with a mobile phone that supports the NFC function, and verify the authenticity by logging in to the APP or browser;
2. System design
2.1 Construction scope
Through the construction of the RFID system, visualized management of the finished product is carried out in the warehouse, and the system documents are automatically generated to realize traceability and anti-fleeing management.
Monitoring range:
Production lines, warehouse entrances and exits and locations, product flow and traceability;
Scalable:
Personnel access control, production process monitoring, quality analysis, warehouse management;
Monitor the logistics chain:
1. Storage process: production and processing → paste barcode → assembly line packaging → barcode scanning → finished product stacking (automatically associated with pallet label) → waiting for storage cache → storage scanning (verification) → shelf → upload system → warehouse management (moving warehouse) , Demolition, stacking) → report query;
2. Inventory process: handheld terminal to obtain inventory task→scan inventory→export inventory result→tray query→report query;
3. Outgoing process: sales order → delivery order → forklift picking task and shipping plan → forklift picking and unloading → outgoing scanning (verification) → uploading system → generating flow information → outgoing completion → anti-fleeing goods inquiry →Report query;
2.2 Construction key points and difficulties
The production environment of the factory is stable and reliable, with good maintainability, and the ability to monitor and manage all equipment through the management platform is the basis for the success of the system;
Being able to accurately identify the type and quantity of objects is the key to the success of the project;
The device supports dual-signal output, and the collected data can be transmitted to the collection server at the same time as the same data can be transmitted to the local workstation, which greatly improves the real-time performance of the system and ensures the integrity of the data to cope with different abnormal conditions. This is the success of the project. Protection.
2.3 Standards and specifications
GB/T 8567-2006 Computer software documentation specification
GB/T 9385-2008 Computer Software Requirements Specification Specification
GB/T 14258-2003 Information Technology Automatic Identification and Data Collection Technology Barcode Symbol Printing Quality Inspection
ISO/IEC18000-6 “Information Technology-Radio Frequency Identification (RFID) for Item Management-Part 6: Air Interface Parameters for Contactless Communication with a Frequency of 860-930MHz”
ISO/IEC 19762-3-2012 Information Technology Automatic Identification and Data Acquisition Technology
GB/T 191-2008 Packaging, Storage and Transportation Graphical Sign
GB/T 18220-2000 General specification for handheld personal information processing equipment
GB 9254-2008 Information Technology Equipment Radio Disturbance Limits and Measurement Methods
GB/T 15425-2002 EAN·UCC system 128 barcode
“RFID Middleware Web Interface Specification”
“RFID Middleware JMS Interface Specification”
2.4 Conditions and restrictions
1. The production line and warehouse need to provide the necessary Ethernet wired network interface and 220V power supply access;
2. Box code coding rules, shelf coding rules, different product pallet specifications, batches, storage and shelf picking rules, naming rules, etc. need to be defined in advance;
2.5 System function and architecture
The system is mainly composed of tray label identification equipment, radio frequency identification channel, handheld terminal, middleware management software and business management software. The data of all readers are transmitted to the collection server through the network and stored in the database. At the same time, it is extended to support local RS485 interface transmission. To the local IPC (workstation), the readers of each functional area (work section) upload the read RFID data to a specific collection server, which is logically processed by the business management software, and is connected to the upper-level system through the data interface.
The system is divided into hardware equipment layer, data collection layer and business application layer. The RFID middleware management software performs unified management, maintenance and data reading of the equipment, and is connected with the business system. The business system only needs to focus on business applications, which greatly simplifies the difficulty of deployment , Enhance system reliability, and provide convenience for system expansion.System internal server
The overall process of the system:

Hardware system deployment:

1. Outbound and inbound collection

The hardware equipment directly communicates with the server through the network, and there is no need to deploy workstations on site, which can realize automatic operation without manual intervention.
2.6 Detailed business description
Through the construction of the RFID system, the user operation steps are greatly reduced, and all data input and output are interlocked, reducing the probability of error, and providing a strong guarantee for improving production efficiency and strengthening the strength of the enterprise.
2.6.1 Storage
1) The forklift picks up the pallet to be put into the warehouse, and the forklift reader reads the pallet label to obtain the batch, name, and number of boxes of the current pallet;
2) The system automatically matches according to product type, batch and current warehouse information, finds free or allow repeated storage of the same batch of storage locations, and outputs recommended storage location information;
3) The forklift moves to the warehouse gate, the radio frequency identification channel reads the pallet label information, and obtains the batch, name, number of boxes, and pallet number;
4) The system matches the current warehousing information with the warehousing task. If the current pallet number exists in the warehousing task, the green light will be released. If it does not exist, it means abnormality, the red light will be lit and an alarm will be displayed, and the system will record the abnormal information;
5) The forklift moves to the corresponding location, puts the pallet into the location, the forklift reader reads the pallet label, and reads the location label at the same time, the forklift industrial computer displays the pallet information and the location code, and the operator manually confirms if The current recommended location cannot meet the requirements, then the pallet storage location shall be subject to the final storage location, and the operator shall manually confirm it;
The forklift puts the pallet to the final position → manually click to confirm → complete
6) After the shelves are completed, the system updates the electronic kanban to display the current location and the storage status of the location, and statistics show the type of material, the number of finished products in stock, etc.;
7) Synchronize the warehousing information to the production management system through API;
2.6.2 Warehouse Management
1) Move the warehouse, move the pallet from one location to another location;
The handheld terminal scans the pallet label → moves the pallet to the new location → the handheld terminal scans the new location label → complete
The warehouse moving operation can also be completed by a forklift.
2) Disassemble the board and split one pallet into two pallets;
The handheld terminal scans the pallet to be split → the handheld terminal scans the new pallet → moves the finished box to the new pallet and scans the barcode of the finished box → repeats the finished box and scans → complete
3) Stacking, the principle and operation method are the same as that of dismantling;
4) Product search, hand-held terminal input product batch or name, you can query the specific storage location;
2.6.3 Inventory management
1) All inventory, use the handheld to scan all the pallet information in the warehouse, obtain the finished product information, and compare it with the inventory to form a report;
2) Partial inventory, according to the inventory task generated by the production management system, take inventory of some finished products and form an inventory report;
The handheld terminal imports part or all of the inventory task → scan the trays to be inventory → complete
2.6.4 Delivery
1) Warehouse management personnel scan or enter the bill of lading number, the system obtains the content of the sales order, and automatically generates picking tasks and shipping plans;
The warehouse manager enters the bill of lading number in the operation interface → the system displays the content of the pickup → click to confirm the pickup → complete
2) The forklift receives the picking task, selects one of the picking tasks, and starts picking, the system automatically prompts the location that can be picked, and the forklift directly moves to the corresponding location for picking;
The forklift operator selects a picking task → click to confirm to start → automatically complete a certain amount through the warehouse gate system → complete
3) For outbound verification, the forklift passes through the warehouse gate, the RFID channel reads the pallet label, the system obtains the corresponding category, quantity, and batch, and matches it with the shipping plan. The matching is correct and the green light is on, and the red light is abnormal;
4) The shipment is matched correctly, and the corresponding quantity of forklift picking tasks is reduced until the picking is completed;
5) The shipment is matched correctly, and traceability records are generated for category, quantity, batch, sales order, dealer, time, warehouse information, etc., which is convenient for traceability query;
6) Update the electronic billboard information;
7) The outbound record is synchronized to the production management system through API;
2.6.5 Anti-Fleeing Goods Query
NFC working mode:
Reading mode (active mode): Reading mode generally requires an NFC tag or NFC card. A card reader device (which can be an NFC mobile phone or a separate card reader) is required to communicate with an NFC tag or NFC card.
In the early stage, the luggage information was bound to dual-frequency tags (NFC tags and UHF tags) in the station binding. The verification process is as follows:

1) The administrator prevents counterfeit goods inquiries. After the administrator logs in, the NFC scan can be performed to inquire all the traceable dealers, production time, out-of-warehouse time, sales orders, batches, etc., without recording the number of inquiries;
Administrator login→NFC scan→Display traceability information→Complete
2) Ordinary query, the customer scans the NFC tag information through a mobile phone or other device that supports NFC function, calls the NFC function through the APP software, reads the NFC tag information, and can query the production time, whether it is genuine, and the number of queries;
NFC scan → display traceability information → complete
Examples are as follows:

2.7 System benefits
Automatic inspection, automatic binding, automatic inventory management, and automatic warehouse-in/out verification can save personnel input, speed up warehouse-in/out time, and save money;
Form a complete data stream, and real-time statistics, you can understand the status of production but not warehousing, daily warehousing, inventory real-time information, etc., without waiting for inventory to understand;
Construct an intuitive electronic billboard, which can clearly display the current warehouse inventory, and display the category, quantity, and status of each location;
Through a complete data query system, it can provide a basis for preventing cross-country goods;
The system can be expanded, adding hardware equipment and configuration can be applied to other warehouses, laying the foundation for the later production process transformation, warehouse expansion, and the construction of automated three-dimensional warehouses;
The information management system stores, analyzes, and processes the data in the background to ensure the accuracy and efficiency of the data;
Building intelligent production lines and warehouses can achieve accurate control of production and inventory, make full use of existing resources, and rely on modern information software technology to integrate production and storage systems.
3. System advantages
3.1 Advanced equipment
The construction adopts integrated readers and split readers. Various types of readers can be flexibly selected according to the actual scene, and there are diversified choices in the case of satisfying the application, which can reduce the cost while reducing the deployment time.
In areas that need to be identified in large quantities, the reader supports dual or multi-machine extended use, and can identify more than 200 pieces of goods in large quantities.
The reader has dual outputs. It can transmit data to a local workstation through the local RS485 while collecting data through the network. It can realize the synchronization processing or data backup of multiple systems, which greatly improves the integrity and real-time performance of the system. At the same time, the reader has the feature of automatic sleep, which can sleep when there is no label, reducing the energy consumption of the reader, suitable for long-term work, energy saving and consumption reduction, and the equipment is more stable.
3.2 System advancement
The system uses middleware management software for centralized collection, and uses management programs for centralized equipment supervision, which can comprehensively control the operating status of the equipment, and can timely notify the malfunctioning equipment by email or SMS. The administrator can use the PC or mobile phone. , View and process on the tablet.
The middleware software can manage multiple devices at the same time, reduce the number of workstations invested, and can remotely restart, upgrade, and read the devices, so that the system can operate efficiently and orderly.
3.3 System scalability
The system can be expanded in terms of capacity, which can increase the number of related storage areas and the number of reads in a single batch, and can be expanded in an orderly manner;
Functional expansion can make later warehouse management more refined, precise warehouse areas, locations, automatic entry and exit, and even seamless docking with automatic three-dimensional warehousing, and can expand the functions of station management and asset management to achieve one-time deployment and multiple dimensions Use, maximize the use of investment rationally, and realize orderly and efficient management of the enterprise.
4. Risks and countermeasures
1) Demand change risk
It is the first time for users to use RFID solutions, so there may be situations where the requirements details are not clear.
Countermeasures:
In the process of design and development, communicate with users more often, and there is a risk of misreading the label
2) Risk of misreading
Countermeasures:
By delimiting a certain isolation area near the identification channel, try to delineate an isolation area of at least 2 meters to physically isolate other tags;
By installing metal shielding partitions, the wireless signal is physically shielded;
Set the sensitivity of the reader, filter the electronic tags with weaker signals, and technically shield the remote electronic tags;
By setting the status bit of the electronic label, the empty pallets without tasks are shielded from the software to avoid the identification risk caused by the empty pallet transfer.
5. Introduction of main equipment
5.1 Four-channel fixed reader
Support agreement: ISO/IEC 18000-6C/6B
Reading distance: 0m-12.0m.
Write distance: up to 6.0m.
Reading speed: >400 sheets/sec
GPIO: 4 general I/O signals
Recognition ability: anti-collision protocol, multi-tag recognition.
5.2 Handheld Reader
It supports Android and Wince operating platforms, and complies with mainstream UHF standards such as Europe (ETSI EN 302 208), the United States (FCC part 15), Japan TELEC, and China CMII. Designed according to ergonomics, the appearance is exquisite, the protection level is high, the operation is comfortable, simple, easy to carry, high flexibility, suitable for working in various environmental conditions. Mainly used in warehousing logistics, asset management, library management, financial management, production management, ticket management and other fields.
Typical applications of handheld readers
Logistics industry such as container operation management, warehouse inventory management, cargo allocation tracking, etc.;
Intelligent vehicle management such as vehicle inspection, customs clearance, vehicle certificate inspection, etc.;
Production automation, process management of parts and components, etc.;
Electronic ticket inspection and personnel ID card inspection, etc.;
Asset equipment patrol management, asset storage management, etc.
[ad_2]