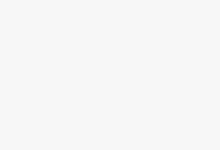
RFID cabinet asset management solution
[ad_1]
1. Main function description and problems to be solved:
1. The main functions of the cabinet asset intelligent manager hardware include:
(1) Realize positioning, inventory and query functions for each U-bit asset on the network cabinet in the computer room;
(2) The hardware equipment is convenient to load and unload, and the connection is convenient;
(3) U-position asset positioning, inventory and query.
2. Specific meaning: An electronic label is hung on each U-position device in the cabinet, and the electronic management of the label is more beautiful, simpler, more scientific, and easier to maintain. Using five-digit LCD electronic label display, the link number of a port in any distribution frame in the cabinet (1—42U) can be queried and displayed on-site and remotely, and the system network management, equipment installation and assets can be marked manage.
3. Problems to be solved:
(1) The equipment in the cabinet is transferred and installed from one place to another. If the relevant equipment transfer and installation records are not done, it will be chaotic for a long time and the physical positioning of the equipment cannot be achieved;
(2) The equipment in the network cabinet can be installed and removed at will. Unauthorized installation of external equipment may cause hidden dangers of data leakage of the unit. Disassembly will cause the loss of unit equipment and cause property damage. The smart cabinet (1—42U) must be equipped with Switch quantity sensor electronic label.
2. Entry label and installation prerequisites:
1. Before the equipment enters the smart cabinet for installation, first scan and authorize the system;
2. Legal installation should be carried out within five minutes after confirmation;
3. Installation that is not authorized by the system is considered illegal, and the system will always voice alarm;
4. Voice prompts throughout the installation and operation of the equipment.
3. Function:
1. It can automatically track and manage the physical location changes of all equipment in the cabinet;
2. It can accurately grasp the physical location of the equipment in the system, greatly improving the effectiveness of asset management;
3. Reduce manual input workload, avoid management disorder caused by human negligence, and improve management efficiency.
4. Labels and components:
1. Label: The card type electronic label is adopted, the specification is 20mm×20mm. There is a small round hole in the upper right corner for fixing the label.
The following picture shows the label design pattern:
2. Components: nylon rope connection method: string knot type. The specifications of the nylon rope are: 0.8-1.1mm in diameter and 200-300mm in length.
The fixing method is: the two ends of the nylon rope are embedded (plastic pressing) and embedded in the PVC board to be connected to the asset (ie, the U position). The fixing method of the PVC board and the assets is the fixing method of super-strong 3M glue. Specification of PVC board: 30mm×30mm.
5. Card reader (including card reader module):
Specifications: 125K (only ID number can be written) module or 522S (4k content can be written) module.
The card slot connection method is: up and down connection, up to 200 units of card slots can be connected, and 485 lines are connected in parallel.
Product renderings of Guangzhou Jianyong Cabinet Assets:
6. Server:
The server is the company’s existing host ERP management service system, which reads data and uploads it to the ERP server center with a 485-line connection module.
7. Customized service:
Taking into account the particularity of the horizontal bars in your driver’s cabinet that affect the effect, it is recommended that your company adopt a one-to-one card slot fixing method for effect considerations, that is, other conditions remain unchanged, only change the card slot to a single connection, not serial In rows.
[ad_2]