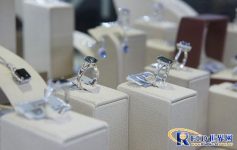
RFID jewelry management system
[ad_1]
1. System background
Jewelry management is an important part of the daily work of jewelers. For jewelers, how to manage these expensive assets and achieve maximum profit is particularly important. At present, there are several problems in jewelry management: sales and inventory are mainly based on manual operations, daily counts can only be performed, not every individual can be checked, and work efficiency is low, and accurate inventory data cannot be provided; store jewelry Inventory counts need to be closed for a period of time, resulting in a decline in turnover, and additional labor costs are required to count jewelry. There is a lack of real-time tracking and management of jewelry. Once lost and not returned to the container for a long time, there is a lack of information-based prompts and cannot guarantee the safety of jewelry; there is a lack of statistical methods for customers’ previous purchase records, and data such as attention cannot be effectively mined. It is not conducive to data analysis, leading to a high share of funds and a long time to withdraw from circulation.
2. System principle
Introduce RFID technology to jewelry management and attach valuable jewelry productsRFIDThe label, combined with the jewelry inventory equipment installed on the counter, is used to monitor, control and track the labeled jewelry, to achieve rapid inventory, real-time tracking and sales management intelligence. In this way, the all-round tracking and recording of the entry and exit of jewelry products and the sales process are carried out, and the cumbersome and inefficient manual management and barcode scanning mode are replaced with new methods of automation, accuracy and efficiency. Jewelry tags are RFID tags. Each tag has a unique ID number. The tag records the weight, purity, grade, warehouse, cargo area, shelf and other jewelry information on the national inspection certificate. RFID technology introduces jewelry management, attaches RFID tags to precious jewelry products, and combines jewelry inventory equipment installed on the counter to monitor, control, and track labeled jewelry to achieve rapid inventory, real-time tracking, and intelligent sales management.
Three, system design
A jewelry counter is installed under each display cabinet of the jewelry store, and the jewelry counter is connected to the jewelry management software of the computer. Each piece of jewelry in the jewelry store is affixed with a jewelry label before it is put into the display cabinet. These labels can store data and information, and can be encrypted. Increase the thickness of the product without destroying the characteristics and habits of the product. During the labeling process, radio waves can automatically identify a piece of jewelry. Then, RFID master control tags were issued to every employee. As long as the master control tags are detected while the jewelry is removed, it will be regarded as a normal operation. They can record their whereabouts on the main server and prevent employees from triggering any alarms when they are in contact with jewelry. The system gives employees one minute to take the jewellery items out of the box and place them in the display tray. After the mobile display tray is placed on the inspection table, the antenna installed in the middle will continue to monitor until the tray returns to the shelf or display box.
If there is any abnormal operation in the process of sales, transfer, consignment or safe replenishment, such as when jewelry is illegally taken from the sales plate, the reader will not be able to read the label information, and the system will warn at the same time. Record the time when the warning occurred.
After the daily work is over, the employees start the “automatic inventory” function, and the RFID system will automatically identify and ensure that all the goods are stored in the designated display cabinet, which is used to inform the RFID system that all the jewelry is intact.
4. System benefits
At present, this jewelry inventory system has achieved good results in a jewelry store in Weihai City, Shandong Province.First of all, speed up the inventory. According to user feedback from the trial operation of the RFID jewelry management system, for example, the inventory time for 6000 pieces of jewelry after use has been reduced from 4 working days to 0.5 working days; secondly, the safety of jewelry should be strengthened with high powerReaderCombining multi-antenna technology and excellent anti-collision performance to track and manage jewelry, increase the accuracy of jewelry liquidation and inventory, and reduce jewelry loss and other incidents;
Intelligent sales management, placing an antenna under the jewelry counter can automatically identify the number of jewelry on the shelf, reflect the sales situation of the day in real time, and provide great convenience for management planning; it is convenient for data mining and decision support. After the application of the RFID system, the information The system can collect new data such as the frequency of the appearance of customers in a specific location, the trajectory of customers’ movement, and the time spent by customers in different locations. Through data mining of these data, new information that helps decision-making can be obtained. For example, statistics can be made on the frequency of customers appearing around counters and booths and the time spent by customers in a certain period, so as to obtain hot jewelry that customers pay attention to, and provide a basis for decision-making for targeted procurement and marketing.
Five, system advantages
◇ High safety performance
● RFID tag combined with one-dimensional bar code to ensure complete identification of material evidence
● Each electronic tag has a unique code, which can quickly identify the physical evidence and will not cause confusion due to code duplication
● Prevent “entrainment” of material evidence that is not registered in the system from being mixed with the material evidence that is normally out of the warehouse and taken away
● The hand-held machine is matched with the fixed reader to improve the accuracy of the system
◇ Automatic data upload to improve work efficiency
● Automatic collection of inbound and outbound data to reduce human error
● Improve the accuracy and reliability of physical evidence management
● Reduce labor management costs
◇ Easy to install and easy to expand
● Various labels can be selected according to the actual situation
● It can be easily expanded to increase the positioning function of valuable equipment, fixed assets and physical evidence
● Combined with peripheral equipment, it can realize visual management and easy to expand
Six, system topology diagram
[ad_2]