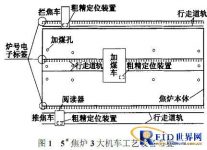
Application of RFID technology in automatic control of three major coking locomotives
[ad_1]
Preface
In the coking production, the automatic positioning control of the coke pushing car, the coke blocking car, and the coal loading car (referred to as the three large locomotives) is extremely important. In the previous control schemes, the main ones are:
·Camera technology: Affected by the environment and the surface position of the object, such as snow, rain, fog and other climates, the surface position of the object can not be used at different heights, and there are no examples of successful application.
Barcode technology: It has strict requirements on the environment and reading conditions, and cannot be used for dynamic data updating. It is difficult to make a difference in coking production where conditions are poor in all aspects.
Acoustic surface technology: The code is compiled by the manufacturer at one time, but the length of the data code is limited, and it can only be read at close range, and the data cannot be dynamically updated, which is greatly affected by the environment.
GPS (Satellite Positioning System) technology: continuous positioning and tracking, dynamic data reading, writing and refreshing. The disadvantage is that the cost is too high, the operating cost is expensive, and the positioning accuracy is greater than 2 m, which cannot meet the basic requirements of locomotive positioning (usually less than 10 cm). The above four schemes have defects in varying degrees, and none of them have been widely used in coking production.
Jinan Iron and Steel Group Corporation draws on the experience and lessons of the predecessors and draws on the successful examples of foreign advanced coking production. Radio frequency induction identification system) locomotive control management scheme. Practice has proved that RFID wireless microwave technology has strong adaptability to the environment, can resist the interference of dust, oil, vibration, ice, snow, rain and fog or tarpaulin coverings, realizes all-day work, and can dynamically store the position information of the furnace number, ensuring 3 Fast and reliable completion of large locomotive positioning control and locomotive information management.
1 Introduction to the control technology of coking locomotives
Jinan Iron and Steel Group Coking Plant 5 # coke oven hole 65 holes; the total length of the carbonization chamber is 14 280 mm; the effective length of the carbonization chamber is 13 480 mm; the effective height of the carbonization chamber is 4 074 mm; the furnace height is 4 300 mm; the furnace width is 450 mm; furnace The length is 14 280 mm; the coking time is 16 to 17 h. The entire coke oven is equipped with coke pushing car, coke blocking car, coal charging car, quenching car, electric locomotive and other equipment. Among them, the interlocking control of the three locomotives of coke pushing car, coke blocking car and coal charging car is very important. The layout of the coke oven locomotive control process equipment is shown in Figure 1. 3 The automatic control system of the large locomotive introduces RFID technology to complete the identification of the furnace number and the coarse positioning control. Fully automatic control between. With the center of each carbonization chamber as the boundary, install electronic tags with stored furnace number data on the track of the coke pushing car, coke blocking car, and coal charging car, and install them on the coke pushing car, coke blocking car, and coal charging car respectively. An electronic tag reader and precise positioning device realize the automatic rough positioning, precise positioning and automatic completion of coke pushing, coke blocking, and coal charging for each locomotive.
2 Introduction to RFID technology
2.1 RFID single system composition
The RFID single system consists of two parts: ① Sensor, also called electronic tag (Tag). Each electronic tag has a unique 32 b serial number and is installed on the surface of the object to be identified. ②Radio frequency signal processing control system (also called reader or reading device), including antenna, radio frequency processing module RFM, control module CTL and upper host system (application software system part). The control module mainly includes data communication processing and external input and output interfaces. The front-end device mainly completes data capture and data transmission; the host part mainly completes system control management and remote communication. The reader can read or modify the electronic data stored in the electronic tag without contact, achieving the purpose of automatically identifying and loading information and managing objects. Management functions such as the collection, processing and remote transmission of object identification information can be further realized through computers and computer networks.
2.2 Classification and working principle of RFID system
Radio frequency technology can be divided into two categories: low-frequency system and high-frequency system according to the different frequencies used; according to whether the electronic tag is equipped with battery power supply, it can be divided into two major categories: active and passive; the method of saving data from the electronic tag It can be divided into three categories: integrated circuit curing type, on-site wired rewriting type and on-site wireless rewriting type; according to the technical means of reading and writing electronic tag data, it can be divided into broadcast transmission type, frequency doubling type and reflection modulation Formula 3 categories.
Low-frequency system refers to its operating frequency less than 30 MHz, typical operating frequencies: 125 kHz, 225 kHz, 13. 56 MHz, etc. Its main features are the lower cost of the electronic tag, the smaller amount of data stored in the tag, the shorter reading distance (passive case, the typical reading distance is 10 cm), and the various shapes of the electronic tag (card shape, ring shape, button) (Shaped, pen-shaped), easy to protect, and the reading antenna is not directional. The operating frequency of the high-frequency system is greater than 400 MHz, and the typical operating frequency bands are: 915MHz, 2 450MHz, 5 800 MHz, etc. The advantages of the high-frequency system are that the amount of data stored in the tag is larger, the reading distance is longer (up to a few meters to a dozen meters), it is suitable for high-speed movement of objects, the shape is card-shaped, and the reading antenna and electronic tag antenna are strong. Directionality; the disadvantage is that the cost of electronic tags and readers are relatively high.
The active electronic tag is equipped with a battery and has a long reading distance. The disadvantage is that the battery life is limited; there is no battery in the passive electronic tag, and its working electricity is completely supplied by the charging pulse generated by the reader through the RF method. When working, the reader first emits a radio frequency pulse signal for a certain amount of time to charge the capacitor on the electronic tag, and then discharge the capacitor to allow the internal circuit to work for a short time. Generally, it can be maintenance-free. Compared with the active system, the passive system has a slight limitation in the reading distance and the speed of adapting to the movement of the object. The data information in the integrated solidified electronic tag is generally solidified in the ROM process mode when the integrated circuit is produced, and the stored information is unchanged; the field wired rewrite electronic tag generally writes the information stored in the electronic tag into its internal In the E2PROM storage area of the E2PROM, a dedicated programmer or writer is required for rewriting, and power must be supplied to it during the rewriting process; the on-site wireless rewriting electronic tag has specific rewriting instructions, which can generally be done directly by the reader. The saved information is also located in the storage area in its E2PROM, which can generally be rewritten more than 1 million times.
The implementation method of the broadcast transmission type radio frequency identification system is relatively simple. Electronic tags must work in an active way, and the stored data and information are broadcast uninterruptedly in real time, and the reader is only used as a receiver. The disadvantage of this system is that the electronic tag must continuously transmit information, which consumes a lot of power, causes electromagnetic pollution to the surrounding environment, and reduces the security and confidentiality of the system. It is more difficult to implement a frequency-doubled radio frequency identification system. In general, the reader sends out the query signal, and the signal carrier frequency returned by the electronic tag is the frequency multiplier of the radio frequency sent by the reader. This working mode provides convenience for the reader to receive and process the response signal. However, for passive electronic tags, when the electronic tag converts the radio frequency energy received from the reader into the multiplier response carrier frequency, the energy conversion efficiency Lower, the cost of the electronic tag rises, the system work needs to occupy two working frequency points, generally seldom used.
2.3 Selection basis
There are many types of RFID, and its application selection needs to be determined according to the characteristics of the control and management of the coking locomotive and the actual environment analysis.
1) The coking environment is harsh, and it is hoped that the less maintenance the better, therefore, choose passive electronic tags as much as possible.
2) Since the three large locomotives run on dedicated rails, the trajectory is exactly the same each time, a reading distance of not less than 2 to 3 cm can be allowed, the direction is fixed, and the locomotive running speed is less than 1 m/s. Considering cost and system simplification, low-frequency system is selected. It should be noted that the microwave system has a certain degree of diffuse emission. When more precise coarse positioning is required, the direction of the microwave must be limited to achieve a positioning detection accuracy of 8 cm (5 # coke oven process requirements). The easy way to achieve this is to use shielded pipes for directional reception on the reader.
3) Each electronic tag installed next to the track indicates the physical location of the process. The process position is fixed and can be distinguished by the unique 32 b serial number of each electronic tag. But when the electronic label is replaced, it will bring the trouble of revising the location recognition program. Therefore, by choosing the electronic label with 1 KB storage space, the system maintainer can redefine the electronic label at any time and replace the electronic label in use on the spot without changing the control program.
4) Frequency doubling radio frequency identification is obviously not what we want. The reflective modulation radio frequency identification system can be clearly selected.
5) The reader on the locomotive must transmit the data to the PLC controller at a distance of 20 m, and be sure to use RS232 communication technology.
In view of the harsh application environment of the RFID system, we chose the 1K5012B electronic tag and IR4040 B reader from Finland Idesco, which can basically meet the design requirements. 1K5012B electronic label: storage capacity 1 024B, working environment temperature 25 ~ 85 ℃; protection grade IP67. IR4040 B reader: carrier frequency is 24 kHz, communication interface is RS232 + RS485, working environment temperature is 20~70 ℃, protection grade is IP67. Due to enhanced protection, the maximum reading distance between the two is 4 cm.
3 Locomotive control system
3.1 System configuration
The system configuration is shown in Figure 2.
It contains 4 sets of Control Logic PLC of AB Company, each locomotive is equipped with 1 set of PLC, the main station is the coke oven body control system, which mainly completes the information reception and transmission between the main control computer and the PLC controller of each locomotive. Data management. The slave station 1, the slave station 2, and the slave station 3 carry out manual and automatic control of coke pushing, coke blocking, and coal charging, and automatic control of the coarse positioning and fine positioning of the locomotive according to the wireless instructions sent by the master station. At the same time, the three PLCs are equipped with operating terminals, which can display the position of the coke oven and the manual setting of the coke oven number in real time and the calibration of the automatic equipment. The main control computer is set on the main control system to complete the system management of the coke discharge plan. .
Wireless communication uses master-slave wireless communication to complete the transmission and reception of information between stations. Wireless carrier frequency 406.6 MHz; channel spacing 25 kHz; frequency stability <±1.5 kHz; communication rate 9 600 b/ s; communication mode is half-duplex protocol; emission type F1D. The furnace number data stored in the electronic label and the control flow of coarse and fine positioning are shown in Figure 3.
3.2 Control process
Coke pushing car: The main control computer issues the target furnace number to be coke pushed, and the slave station 1 controls the operation status of the coke pushing car according to the data of the furnace number electronic label, and reaches the designated furnace number. After the focus pushing car is correctly aligned, the process sequence control is carried out to make the focus pushing rod accurately positioned. After receiving the signal to allow the focus to be pushed, it starts to push the focus. After pushing the coke, the flat coal rod is accurately positioned. After receiving the signal of allowing coal leveling, the coal leveling is completed and the next cycle is waited.
Coke blocking car: The main control computer issues the target furnace number to be blocked, and the slave station 2 controls the operation status of the coke blocking car according to the data of the furnace number electronic label, and reaches the designated furnace number. After the alignment of the focus car is correct, the process sequence control is carried out to accurately position the focus guide grid and send out a signal to allow the focus to be pushed. After receiving the exit signal of the focus guide grid, the focus guide grid is completed and retreated, waiting for the next cycle.
Stoker: The main control computer issues the target furnace number that needs to be refueled, and the slave station 3 controls the operation status of the stoker truck according to the data of the furnace number electronic label, and reaches the designated furnace number. After the coal filling truck is correctly aligned, the process sequence control is carried out to start coal filling, and when the coal filling ends, a signal to allow coal leveling is issued. After that, the slave station 3 continues to control the coal filling truck to reach the coal tower to replenish coal. After finishing, wait for the next cycle. Production control process requirements: 3 large locomotives must realize automatic identification of up to 195 process position points on a running track of up to 60 m, and the accuracy of the identification position deviation is not more than 8 cm. Only in this way can the interlocking control between the locomotives be realized, so as to avoid the misalignment accidents of the three major locomotives, and it also creates good technical conditions for the precise positioning and control of the start-stop and acceleration/deceleration operation of the locomotives, thereby realizing an efficient locomotive control system.
4 Conclusion
Since RFID technology has been put into use in the coking plant #5 of Jinan Iron and Steel Group Corporation in June 2002, it has greatly improved the automation of coking production, avoided human operation errors, improved labor productivity, and has a very low system failure rate. , The effect is remarkable, it is a high-tech metallurgical industry control technology worthy of vigorous promotion.
[ad_2]