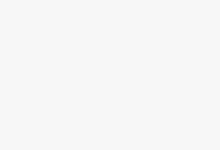
Design of automobile test system based on C8051F and Zigbee wireless network
[ad_1]
The automobile performance test system is a key component of the automobile test engineering. It is an organic whole composed of a number of interconnected and interacting sensors, instruments and equipment to achieve the test of the various performances of the automobile. The performance of the automobile test system Often has an important impact on the utility of the entire car test. Existing automobile test systems mostly use wired connections, and this method has two drawbacks: 1) Automobile tests need to be carried out in harsh environments such as large-scale special test sites or typical areas, and the on-site wiring tasks are cumbersome and error-prone; 2) Some automobile tests For example, the serpentine test has a high risk, and it is more important for a test system that can reduce test losses. The system uses Cygnal’s C8051F020 single-chip microcomputer as the control core, and is based on Zigbee wireless network technology to design, for example, a multi-channel data comprehensive acquisition system. It uses fewer peripheral devices to achieve performance parameter testing in automotive tests, shortens the field wiring time, and improves Test efficiency, and reduce accident losses when a test accident occurs.
1 System overall structure design
Automobile tests mainly include test items such as power performance, fuel economy, handling stability and emission characteristics. The main performance parameters include speed, acceleration, fuel consumption, temperature, and dynamic motion parameters in handling stability tests, etc., which are obtained by sensors The test signals of these parameters are processed by the front-end processing module (shaping, filtering, amplifying, etc.) and then sent to the C805l-F020 microprocessor. After the analog-to-digital conversion and data processing are performed inside the microcontroller, the connection with the Zigbee terminal node is realized through the serial port. Then, the terminal node sends out the data in the WLAN, and the Zi-gbee central node communicates with the host computer through the serial port after receiving the data. The central node can also send the command of the upper computer to the terminal node to control the execution of the terminal node. The overall structure diagram of the system is shown in Figure 1.
Figure 1 The overall structure of the system
2 System hardware design
2.1 Front-end processing module
The sensor converts various common non-electricity signals into electric quantity signals, which are generally weak. The front-end processing module processes these signals and sends them to the A/D conversion port of the single-chip microcomputer. The system has a total of 8 sensor signals, including 2 voltage sensor signals, 2 -5~+5 V voltage signals, 2 4~20 mA current signals and 2 thermocouple signals for front-end processing. Among them, the front-end processing hardware circuits of the pressure sensor signal and the thermocouple signal are shown in Figure 2 and Figure 3 respectively.
Figure 2 Signal front-end processing circuit of pressure change sensor
Figure 3 Thermocouple signal front-end processing circuit
AD620 is a low-cost, high-precision instrumentation amplifier. It only needs 1 external resistor to set the gain, and the gain range is l~10 000. The front-end processing of the pressure variable sensor signal adopts the amplifying circuit composed of AD62-0 and AD705. This part uses a single power supply. AD705 is a voltage follower, which provides the zero point of the output voltage for AD620. Send VREF and AGND to the AIN1.0 and AIN1.1 ports of the 8-bit precision AD-Cl of the MCU, and use the software program to realize the calculation of the reference voltage and analog ground of the signal.
The thermocouple sensor is used to measure the temperature of the key parts of the car, and its front-end processing circuit adopts the OP07 adjustable gain amplifier circuit. OP07 is a low-noise, non-chopping and zero-stabilized bipolar operational amplifier integrated circuit. It has a very low input offset voltage, low offset, and high open-loop gain. The OP07 is particularly suitable for high-gain measurement equipment and amplifier sensors. Weak signal, etc. In occasions where accuracy is not required, the offset voltage of OP07 can be ignored. In this circuit, R25 and R24 are used to adjust the system magnification. When different types of thermocouples are selected, the resistance of the two can be adjusted appropriately.
2.2 C8051F020 module
C805lF020 is a mixed-signal SOC 8-bit single-chip microcomputer of Cygnal Company. It is a fully integrated mixed-signal system-level MCU device with 64 digital I/O pins. The single-chip microcomputer uses a high-speed 805l microcontroller core with a speed of up to 25 MI/s, 8 I/O ports, 5 general-purpose timers, 5 capture/compare modules and dedicated watchdog timers, and SM can be used at the same time -Bus, SPI and 2 UART serial ports, built-in 64 kB high-speed memory. In terms of analog peripherals, the device has 1 12-bit A/D converter, 1 8-bit A/D converter, 2 12-bit D/A converters and 2 analog comparators. These digital and analog peripherals inside the device make the design of the system simpler and more integrated.
This module mainly designs the reset circuit, external crystal oscillator circuit and grounding processing of C8051F020, and leads all pins to expand the application. The system needs to run at a high speed in order to collect data in a timely and effective manner, so the single-chip microcomputer uses the internal oscillator as the clock source under normal circumstances. However, due to the large error of the internal clock, in the process of serial communication, an external clock should be selected, and the internal and external clocks can be switched through software settings. Connecting to the analog ground through the decoupling capacitor at the power supply can reduce the area of the interference loop and reduce the electromagnetic interference radiation. The interference caused by the digital current can be coupled to the ground instead of appearing in the ground of the external circuit. In order to minimize capacitive coupling, there is no overlap between the two, two independent grounds are connected together at the common “star” ground of the power supply through ceramic beads, and similar treatments are used at the power supply to prevent interference.
2.3 Zigbee node module
The automobile test system studied in this paper initially uses 2 terminal nodes and a central coordinator to form a star network topology. All 3 nodes use SZ05-ADV wireless transceiver modules, and Zig-bee terminal nodes and central nodes pass through standard serial ports. Connect with C8051F020 module and PC equipment respectively to realize wireless transmission of data. SZ05-ADV is a high-performance embedded wireless transceiver module, and its core device is Freescale’s MCl3213. It is the second-generation standard ZigBee wireless communication platform. It integrates a low-power 2.4 GHz RF transceiver and 8-bit microcontroller in a 9 mmx9 mmxl mm 7l-pin LGA package. The MCl3213 device has 60 kB of flash memory, which is solved by MCl32lx. The solution can be used as a wireless connection in a simple point-to-point connection to a complete ZigBee mesh network. The combination of a radio transceiver and a microcontroller in a small footprint package makes it a cost-effective solution. The RF transceiver in MCl321x The converter works in the 2.4 GHz ISM frequency band and is compatible with the 802.15.4 standard. The transceiver includes a low noise amplifier, 1 mW RF output power, a power amplifier (PA) with VCO, an integrated transmit/receive switch, and a power supply regulator on the board. With full spread spectrum encoding and decoding, the microcontroller in MCl32lx is based on the HCS08 series microcontroller unit (MCU), HCS08 A version, up to 60 kB of flash memory and 4 kB of RAM.
[ad_2]