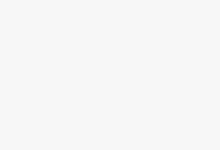
New Force Mine Vehicle Management and Intelligent Weighing System
[ad_1]
1. System overview
There are a large number of mining vehicles entering and leaving the mine every day, and procedures such as parking, registration, and weighing are required. The operator manually enters the data into the computer. This is not only time-consuming, but also has a large error rate. In addition, it is easy to breed fraudulent behaviors. Enterprises cause a lot of economic losses.
The mine vehicle management system combines RFID technology, electronic truck scale technology, communication technology, automatic control technology, database technology and computer network technology to automatically record the license plate number, weight information, time information, etc. of vehicles equipped with electronic tags, and write them The mainframe database can effectively eliminate human error, prevent over-balance blockage, cheating, etc., ensure the accuracy of original data collection, and reduce economic losses.
At the same time, three monitoring points are set up on the ore transportation route, which are the loading point, the midway detection point and the unloading point. Each monitoring point has a weighing point. When the vehicle enters the weighing point, the reader is triggered to read the card, and The detailed information of the vehicle is transmitted to the PC, and the tag information is used for matching to check whether the vehicle has lost ore during transportation.
Two, system goals
This solution implements intelligent management for all vehicles entering the mine, and requires each vehicle entering the mine to be assigned a special mining label. The special label contains the name of the owner of the mining vehicle, tare weight/license plate number/ Material type/net weight/loading location/destination/printing time year, month, day and other information. Three key points are set in the transportation route. When the mining truck is weighed by the truck scale, the reader is triggered to read the card. The reader transmits the information in the on-board tag to the host, and at the same time instructs the electronic scale to transmit the vehicle weight information. The mine management system can automatically measure the weight of the ore from the information when the ore truck passes through the weighing point, and call the data in the host database at any time to query or form a report.
Three, system composition
The mine vehicle management system is composed of two parts: the automatic weighing system of trucks and the computer monitoring and management system. Among them, the automatic weighing system of automobile weighing is mainly composed of weight sensors and weighing display instruments. It mainly completes the functions of weight data collection and communication with the upper computer. The computer monitoring and management system is composed of computers, printers, radio frequency identification systems, controllers, and channels. It is composed of brakes, vehicle detectors, cameras, and video cards. It mainly completes weighing monitoring, printing scales, identifying identities, generating various summary statistical reports and comprehensive query functions.
620)this.style.width=620;” border=0>
Figure 1 Schematic diagram of the system
3.1 Auto weighing system
The system has all the functions of GM truck scales, and can automatically weigh, record and print the results of mining vehicles entering the truck scale without being on duty; when the mining vehicles enter the truck scale for weighing and measurement At the same time, the system can input information such as number, tag card number, license plate, unit, driver, etc. of mining vehicles, and can generate reports and print at the same time.
3.2 Computer monitoring and management system
The computer monitoring and management part is composed of computers, printers, radio frequency identification systems, controllers, barriers, vehicle detectors, cameras, and video cards. The radio frequency identification system consists of a reader, an antenna and a tag. The tag is attached to the windshield of the car. When the reader reads the tag, the camera takes a photo of the vehicle, and the tag card number, vehicle The picture and the vehicle’s information are transmitted to the host and stored in the host database.
Fourth, the system process
The mine vehicle management process is as follows:
4.1 Admission registration
The mine registration office first registers the vehicles entering the mine, and installs an RFID reader at the entrance. The reader can identify the vehicle’s special tag for transporting the mine, and then the card number, vehicle plate number, owner’s name, The admission time and relevant information about the admission location are stored in the mainframe database.
4.2 Billing
Only customers who have been issued a special tag for ore transportation can go to the ticketing office of the mine to issue an invoice for ore transportation.
4.3 Empty vehicle weighing
After the customer issues the ticket, the ore truck can be driven into the truck scale channel for weighing. The vehicle detector installed at the crossing senses the entry of the car and transmits the signal to the front barrier and signal light. The barrier is immediately closed and the signal light turns red. Prompt the driver to drive slowly, and at the same time ask the weighing instrument and reader to start working. After the tag on the mine truck is read by the reader, the reader antenna transmits the information of the car to the host, and instructs the electronic scale to start transmitting the weight information of the car. At the same time, the camera monitors whether the car is parked at the designated position and captures the image. When the host receives the card number and weight information, it accurately records and backs up the information, and then issues an instruction to open the barrier, and the mine truck drives into the mine for loading.
4.4 Loading ore
After the empty ore truck has been weighed, it can be driven into the mine to load the ore.
4.5 Loading and weighing
After loading the ore, the truck needs to enter the truck scale again for weighing. The vehicle detector installed at the crossing senses the entry of the car and transmits the signal to the barrier and signal light in front. The barrier is immediately closed and the signal light turns red to indicate The driver drove slowly, and at the same time asked the weighing instrument and reader to start working. After the tag on the mine truck is read by the reader, the reader antenna transmits the information of the car to the host, and instructs the electronic scale to start transmitting the weight information of the car. At the same time, the camera monitors whether the car is parked at the designated position and captures the image. When the host receives the card number and weight information, it accurately records and backs up the information.
4.6 Weighing at the monitoring point
There is a monitoring point on the way of transporting the ore. The vehicle will be intelligently weighed when passing the monitoring point. The reader will recognize the tag attached to the vehicle and record the detailed information of the tag and the weight of the vehicle. During the entire weighing process , The vehicle travels at a speed of 10-20km/h.
4.7 Intelligent weighing for unloading
After the truck arrives at the destination, it is unloaded. An intelligent weighing system is installed at the entrance to the destination. When the car enters the intelligent weighing system, the reader reads the detailed information of the car tag and instructs the electronic scale Start to transmit the weight information of the vehicle. When the host receives the card number and weight information, it will accurately record and backup the information. According to multiple readings during transportation, it can be known whether the car has lost ore during transportation.
Five, system characteristics
Compared with the previous mine vehicle management and intelligent weighing systems, the use of RFID technology for mine vehicle management has the following advantages:
5.1 Information collection automation: The weighing data output by the truck scale and the electronic tag card number installed on the mining truck are processed by related equipment and transmitted to the computer. The computer displays the weight of the cargo carried by this car and stores it in the computer’s database. Users can perform operations such as querying, summarizing, and printing according to their needs, thereby realizing information collection automation.
5.2 Strengthen management and eliminate the phenomenon of favoritism: One card for one car, the electronic label is pasted on the windshield of the car, and the weight of the weighbridge each time corresponds to one card and one car. Cooperate with the camera’s image capture function to ensure that the entire system data is foolproof and accurate.
5.3 Establish a corporate image, improve work efficiency, and reduce operating costs: The system performs computer automated network management on all truck scales (weighbridges) in the mine, and can easily measure the weight of the mine truck when it is empty and full, and understand it in real time The actual weight of the cargo loaded on the mine truck, thereby greatly improving the work efficiency of the enterprise.
5.4 Protect the safety of this area and prevent illegal vehicle intrusion: This system can be integrated with the parking lot management system. Only vehicles with legally authorized electronic tags can enter the mine loading and weighing area, thereby improving the safety of this area.
5.5 Avoid human operation loopholes: Due to the way of automatically reading data, all over-balanced vehicles are automatically counted by the computer, eliminating manual intervention, automatically recording data, and automatically verifying and releasing.
5.6 Distance dynamic recognition: The recognition distance is more than 5 meters, and the vehicle speed can be as high as 80km/h.
5.7 Simple structure, convenient debugging and installation, wide weighing range, strong adaptability
5.8 Can remotely transmit information: remote control and group control can be carried out to make the system truly automatic and intelligent, and can be connected to the computer to automatically analyze, calculate and print data records and reports
5.9 Improve efficiency: By realizing automatic measurement, the operation time of each operation link can be greatly shortened, the connection and unloading capacity of the measurement system can be improved, labor intensity can be reduced, and labor costs can be saved;
5.10 Security: The data in the label is highly confidential, and the electronic label cannot be forged or copied, which fundamentally eliminates the phenomenon of copying, forgery, and cheating;
5.11 Fast automatic collection speed: fast weighing can be realized, the efficiency of weighing is improved, and the phenomenon of overbalance in queuing is avoided.
[ad_2]