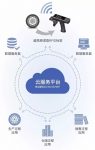
Tire RFID solution
[ad_1]
In recent years, the United States, Japan, the European Union, South Korea, China and other countries and regions have successively issued tire labeling regulations, requiring tires to be labeled to indicate the level of fuel efficiency, rolling resistance, rolling noise, and grip on wet roads. At present, tire labels generally adopt the method of sticking bar codes on the surface of the carcass. The amount of information is limited and it is easy to wear and cause the loss of information, which causes difficulties in the management of tire production, storage, transportation, sales, quality tracking and anti-counterfeiting.
On July 1, 2016, the 4 industry standards for “Radio Frequency Identification (RFID) Electronic Tags for Tires” approved by the Ministry of Industry and Information Technology were officially implemented. Based on the application of RFID technology, Internet of Things, and mobile Internet technology, various information of each tire life cycle is stored in the enterprise database, and the information management of tire production, storage, sales, quality tracking and other links is realized, which is conducive to reducing Production and management costs, optimizing inventory management, and strengthening the ability to respond quickly to the market, thereby improving corporate management efficiency and enhancing corporate core competitiveness.
1. Application Introduction
The tire RFID solution is mainly composed of tire RFID tags, RFID handheld terminals, data service centers, application systems and other parts. Read and write tire RFID tags through the UHF RFID read and write function of the handheld terminal to complete data collection and write; use the handheld terminal 3G/4G network, WIFI to realize real-time data transmission; the data service center saves business data and applies the system Complete specific business logic.
2. System Architecture

1. Tire production
status quo
Tire companies now mainly use barcode technology to identify and store information in the tire production process, which easily leads to the following problems:
(1) In the production process, the information of each link is manually input, which is prone to errors, which makes the work steps unable to connect normally and affects the production efficiency;
(2) When a product quality problem occurs, due to imperfect data records, it is impossible to trace back to the specific link where the quality problem occurred;
(3) The manager cannot directly understand the production status of the production line, and cannot adjust the operation plan in time according to the actual production situation in order to solve the actual problems in the production.
(4) The production department’s incomplete grasp of on-site information can easily cause a backlog of semi-finished tires and affect production and management;
UHF handheld terminal
After applying RFID technology and Shenzhen becoming an RFID UHF handheld terminal, production management and monitoring of semi-finished products, vulcanization, and quality inspection can be realized:
(1) Use the UHF function of the handheld terminal to read and write RFID electronic tags, collect and record the information of semi-finished tires in each process, and support the group reading function, which can collect a large amount of tire tag information at one time, and transfer the data through 4G or WIFI Real-time upload to the management system to realize the intelligent information collection and management of each production link of tires, which significantly improves work efficiency and reduces enterprise costs.
(2) Through 4G or WIFI network, real-time query of warehouse data information, understanding of warehouse storage conditions, so as to formulate production plans.
(3) Through seamless integration with the tire enterprise management execution system, the processing information of each process of the tire can be tracked and located, and the production quality and efficiency can be improved.
2. Tire storage
status quo
(1) Tire storage, allocation, outgoing, and inventory management lack informational records, and managers cannot grasp the storage situation in real time;
(2) Warehouse management lacks information technology, it is difficult to control first-in-first-out according to the actual warehouse age, and it is easy to cause the tires to be out of the warehouse for a long time and cause customer complaints;
Use handheld terminal
(1) By scanning the tire label, the tire production date, batch number, model, manufacturer and other information can be quickly and accurately obtained, and operations such as automatic storage, storage, movement, and inventory can be realized;
(2) According to the results of data collection, companies can fully control and manage inventory to avoid overstocking and shortage of inventory tires, so as to reduce inventory, reduce capital occupation, and ensure the smooth progress of production and operation activities.
3. Tire sales
status quo
(1) Distributors at different levels in the tire marketing channel are likely to flee goods driven by their interests, disrupting the price system of the company’s entire distribution network.
(2) Disputes are likely to arise when claims for tire problems occur, and the production time, sale time, and warranty time are likely to cause disputes.
(3) Tire companies are deeply troubled by counterfeit tires and retreaded tires, and lack of information technology to contain the phenomenon, causing economic losses to the company.
(4) In tire rental or car rental management, there is a lack of technical means to improve management efficiency and prevent tire swapping.
Use handheld terminal
(1)Using the ultra-high frequency function of the handheld terminal to read the tire RFID chip information to record sales data, so that the tire sales data of different dealers and different regions can be recorded, thereby effectively preventing dealers from “sending goods” sales phenomenon;
(2) When a claim is settled, by reading the RFID chip information of the claim tyre, the relevant logistics and production details can be quickly traced to provide a data basis for the claim.
(3) Use the handheld terminal to read the tire RFID tag, check the sales data and the claim data for verification. When the claim product information does not match the information originally sold to the dealer, it can be judged that the claim does not belong to the normal claim scope, and it is effectively controlled Settlements for counterfeit tires or retreaded tires, reduce corporate losses.
(4) In tire leasing, the handheld terminal UHF is used to collect tire RFID information and upload it to the enterprise information system to provide informational means for leasing, effectively prevent the phenomenon of contract swaps, and improve the efficiency of enterprise management.


Product Features
Chainway C4000UHF and C4050UHF are self-developed UHF high-performance industrial smart handheld terminals developed by Shenxun. They are fully functional, reliable and durable. They use Android smart operating system and integrate powerful UHF UHF reading and writing functions to support Group reading, can read a large number of label information at one time; build a high-performance extremely fast processor, with a large-capacity dual-battery design, long battery life; industrial-grade IP64 high protection level, sturdy and durable; support 3G or 4G network, WIFI function , To make data interaction faster, help users quickly realize information management, and improve enterprise operating efficiency.
[ad_2]