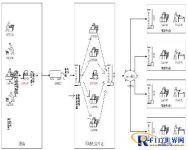
Application of RFID Technology in Comprehensive Management of Vegetable Quality Traceability
[ad_1]
1. System overview
Today, when the price of vegetables is getting higher and higher, how to control the overall control of the enterprise supply chain is in front of enterprises, and the competition is becoming more and more fierce. To be invincible in the market competition, the vegetable wholesale industry must continuously improve production efficiency. Shorten the turnaround time of vegetables. According to market research and analysis, the entire vegetable supply chain logistics industry can greatly improve production efficiency and shorten the capital turnover time through informatization. At present, most of the vegetable logistics industry is all manual work, without any informatization, resulting in poor information feedback. When problems occur, they cannot be discovered and dealt with in a timely manner, which leads to the lack of work in many links. At the same time, the situation of product sales can not be grasped in time, leading to the out-of-stock of the best-selling products and the under-sales products, which also reduces the profit.
RFID automatic collection technology can automatically collect data from all aspects of vegetable procurement, quality inspection, vegetable transportation, vegetable storage, logistics transportation, distribution, and vegetable sales. Provide users with real-time dynamic tracking and query throughout the whole process; realize the monitoring and management of processing information, system operation status, and business operation quality, while providing real, effective and timely management and decision support information for managers at all levels to provide support for the rapid development of business , So that enterprises get rid of the outdated model of relying on human manual entry and relying on empirical management. Provide enterprises with accurate, time-to-time, dynamic and objective first-hand data, so that enterprise management decision makers can provide scientific data basis for comprehensive, timely and accurate management. Since then, costs have been reduced, and profits and competitiveness have been improved.
2. System structure and function
This system uses RFID electronic tags as the identification of items. The hardware of the warehouse management system based on RFID technology includes: host, printer, pallet tags, tractor tags, turnover box tags, inbound/outbound readers, portable handheld readers, RS-485 interface card, reader support, antenna telescopic column, alarm detection device, etc. The host computer is installed with management software, which is connected to the access/access reader and all position readers through the RS-485 interface card and controls them, such as setting permissions, reading limit records and statistical inquiries, etc.; The reader controls the electric door, collects the entry and exit records of the goods, etc.
The system structure is shown in the figure
The system management software mainly includes five modules: system setting, warehouse-in management, warehouse-out management, material management, and database management.
System settings include functions such as password modification, warehouse area, reader address, serial port and alarm settings;
Material management includes functions such as reading/writing electronic tags, adding and deleting records, and generating reports;
Material management includes functions such as material, inventory, statistics and report generation;
Database management performs operations such as browsing, querying, and sorting the database, and can only modify or edit part of the information, such as the degree of damage, remarks, etc., without the right to add or delete any records.
1. Procurement (broker)
The specific implementation process is:
1. When the broker purchases a certain amount of vegetables, the information center will send vehicles and personnel to purchase. The purchaser needs to scan the turnover box label information and pallet information, and upload it based on the 42/48 information. The uploaded box The number cannot be greater than the vehicle-mounted capacity. Once the uploaded data is confirmed, an admission slip will be generated at the same time. The purchaser also needs to collect tags for the number of tractors in order to calculate the mileage of the tractors. The information center counts vehicle mileage to provide data for vehicle maintenance.
2. Distribution Center
Figure 2 Warehousing management flow chart
When the tractor arrives at the distribution center, it needs to scan the front box tag to record the mileage of the vehicle. When unloading starts, the unit is pallet, and the turnover box on each pallet is 42/48. The turnover box automatically collects the pallet label and turnover box data through the access control reader. If it is consistent with the access slip issued by the purchaser, the storage slip will be automatically generated through the background software. If it is inconsistent, an alarm will be automatically prompted to indicate the relevant personnel.
In the outbound process, perform the opposite operation to the inbound process. The system will automatically generate an outbound order. If it is abnormal, the system will give an alarm and remind the relevant personnel that the outbound order cannot be generated.
Intelligent distribution warehousing
Warehouse receipt, delivery, and inventory work: The most important task in warehouse management is to ensure that the booked quantity is consistent with the actual quantity. The use of electronic tags can easily achieve the accuracy of the receipt of goods and the automation of delivery and distribution. , So that inventory will not be missed or lost.
(1) First-in, first-out: The shorter the vegetable turnover time, the better. For the above reasons, due to the large variety of products, it is difficult to ensure accurate first-in, first-out products through manual records and custodian records in actual warehouse management. Through the single tracking technology, a clock can be built into each product, and the intact state of each product can also be recorded, and this information can be provided to the relevant personnel, so as to ensure that the vegetables are shipped out of the warehouse within the specified time limit, so as to achieve First in, first out.
(2) Out-of-stock alarm: When there is a shortage of a certain product in any warehouse, not only can the alarm be automatically prompted, but also the details of the product composition such as vegetable category and vegetable quantity can be subdivided. That is: if a certain kind of vegetable is out of stock, the safekeeping staff can be immediately reminded to replenish the stock in time.
(3) Statistics of unsalable products: the storage of unsalable products in the vegetable industry is a very headache. Through the statistics of unsalable products, the residence time of each product (subdivided into categories and quantities) can be obtained, and it is possible to quickly discover which products are unsalable , You can easily provide price reduction decisions, accelerate vegetable sales and capital turnover.
The distribution center can realize the optimal management of the entire supply chain process of “sales replenishment demand-distribution center-vegetable broker procurement”.
3. Sales terminal
The turnover box is delivered to the sales terminal. When unloading, the pallet is used as the unit to pass through the access control like a card reader. The system automatically collects the pallet information and the turnover box information and compares it with the distribution center outbound order. If the warehousing list of sales outlets is inconsistent, the system will alarm and remind relevant personnel.
When leaving the warehouse through the sales terminal, the turnover box will automatically reduce the inventory through the access card reader of the sales terminal, and automatically generate accounts receivable.
There is an LED display screen in the sales center, which scrolls to display vegetable price information, discounts, vegetable varieties and other information.
Intelligent sales management
(1) Sales statistics: The statistics of daily sales reports are very important to the sales department of an enterprise. It requires accurate results as quickly as possible. It can help the sales department to allocate and replenish goods in time.
(2) Sales automation at sales outlets: Use an access control card reader to read the electronic tags and generate various statistical reports of the day, and send them to the headquarters or local offices for sales analysis.
(3) Sales pre-replenishment: The varieties of vegetables sold in different seasons are different, and they need to be restocked in time when they are out of stock. An early warning inventory line can be set. When the current inventory is below the warning line, a pre-replenishment application will be generated. The pre-replenishment application and the actual sales outbound order will be accumulated. When a certain amount is reached, the replenishment delivery will be carried out. Through sales statistical analysis, it is possible to predict the possibility of stock out in advance, so as to notify timely replenishment.
(4) Sales reconciliation: Receiving payments is a headache for corporate accountants every month. Using the sales automation system, the daily sales records in the data collector are automatically corresponded to the various accounts of the sales outlets, so that the reconciliation work is clear at a glance.
(5) Dynamic statistics of hot-selling vegetables: According to the degree of concern of all customers for a certain vegetable, real-time tracking is carried out according to the sales situation, and mathematical models can be established to analyze consumer needs and better sell. 13439254652 Zhao
[ad_2]