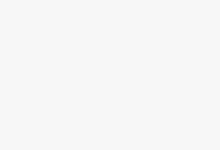
RFID tobacco logistics management system solution
[ad_1]
1. Project background
The tobacco industry is a fast-moving consumer product, which belongs to the fast-moving industry. In the competition among the major tobacco companies, in addition to the distinction of high, medium, and low-end brands, the construction of channels such as terminal distribution is the most intense way of competition. All tobacco companies try their best to improve management level, optimize business processes, and use some high-tech methods to enhance their market competitiveness and enhance resilience, hoping to remain invincible in market competition.
Huiqi IoT Technology uses RFID technology and combines the status quo of tobacco companies. Realize the automation of tobacco storage and the efficient management of the warehouse. The system uses middleware as a supporting platform, attaches RFID tags to cigarette boxes, pallets, and shelves, installs an RFID access control system at the receiving place, and sends the actual receipt and storage information to the back-end upper position, and the back-end system arranges the storage At the same time, install the on-board computer terminal on the forklift, connect the RFID read-write device, and transmit the information of the front-end system and the back-end system through the wireless local area network to realize the exchange and update of data, and the system locates the position of the forklift in real time to facilitate the dispatch of the forklift.
1.1 Current situation
First of all, the current tobacco management generally has the problem of low inventory efficiency. From single products, packaging boxes, to trays, information is manually entered. The efficiency of some links is low, and the degree of informatization of the whole process is not high;
Secondly, the traditional barcode system has obvious shortcomings, such as easy contamination, breakage, need to stop waiting for scanning one by one, etc., batch reading efficiency is not high, and cannot meet the needs of fast and accurate.
In response to the above problems, we use RFID technology, that is, radio frequency technology. And as a more feasible solution. Use digital management system to carry out the overall integration of warehouse management, which is the digital warehouse management system of tobacco companies. It can not only meet the requirements of the distribution operation mode in modern logistics, but also be suitable for large-scale busy logistics distribution to ensure high-quality data exchange in the supply chain; at the same time, through tracking from the enterprise production line and increasing its transparency in the supply chain, It can effectively curb or even eliminate extracorporeal circulation, and can play a huge role in tobacco monopoly management.
2. System composition
2.1 System composition
Hardware system: RFID tags, readers, antennas, on-board computer terminals, wireless LAN equipment, and application servers;
Software system: database and process packages such as warehousing, inventory, forklift positioning/dispatching, etc.;
Middleware system: It is the operation support platform of the entire system, with functions such as data collection, filtering, sorting, encapsulation, and forwarding.
2.2 Main hardware equipment functions
RFID tag: logistics information carrier, used to store packaging boxes, pallets and other related data information.
Fixed reader/writer: tag data collection equipment, used to collect the data information inside the electronic tag and transfer the read tray information to the upper system for corresponding processing.
Handheld reader: It can read labels and barcode information for manual stacking. First read the tray information, and then read the barcode information on each stack of cigarettes one by one, and upload the information to the back-end system for association in the database.
RFID forklift: used for stacking. The tray information is read through the RFID reader, and then the wireless scanner is used to scan the barcodes on the removed or added cigarettes one by one, upload all the data to the system, and update the database.
3. Application process
3.1 Online packaging
Before the goods are put into storage, set up a packing area, according to the actual warehouse management application requirements, pack the corresponding single products into independent packages according to the specified quantity, write the operation information into the label, and paste the RFID label on the packing box.
3.2 Warehousing process
1) When the goods arrive at the distribution center, after zeroing, scanning, loading pallets, passing through the RFID access control system, the actual receipt information is transmitted to the back-end management system, and the goods information is written to the RFID tag of the pallet;
2) The pallet enters the warehousing temporary storage area, and the back-end system generates warehousing instructions according to requirements;
3) The back-end management system retrieves the idle forklifts through the wireless network, and issues the warehousing operation order to them;
4) The front-end system of the forklift receives the warehousing operation order and arrives at the warehousing temporary storage area;
5) The front-end system reads the pallet information and checks it with the instructions of the back-end system. If it matches, it instructs the forklift to send the pallet to the designated location;
6) The forklift enters the storage area, and the front-end system reads the RFID tag of the storage area and checks it with the instructions of the back-end system. If it matches, it instructs the forklift to enter the warehouse, and the RFID system updates the location tag data; if it does not match , Then call the police;
7) After the forklift completes the warehousing operation, the driver confirms that the warehousing is complete. The front-end system transmits the operation result to the back-end system through the wireless network, and the back-end system updates the relevant data in the system and puts the forklift idle.
3.3 Delivery
The forklift receives the shipping instruction and picks up the pallet goods at the designated cargo space. Take the front forklift reader to reconfirm the accuracy of the pallet goods, and then send the pallet goods to the conveyor belt at the outgoing port. The conveyor belt reader at the outgoing port reads whether the pallet label information is accurate, and the goods can be shipped after the verification is correct.
3.4 Receiving at the distribution center
The electronic tag information is collected by the fixed RFID reading and writing equipment and the buried antenna, and uploaded to the central management system. The pallet stays in the reading area for 2 to 3 seconds to complete the scanning of the cargo box on the entire pallet without unpacking a single piece. Scan the code and stack again.
3.5 Product tracking
The State Tobacco Administration started to establish the “Cigarette Production and Operation Decision Management System” in 2003. The system was designed in accordance with the requirements of “planned code retrieval, logistics tracking, and delivery confirmation” to achieve the realization of cigarette production and logistics through “one cleaning and two sweeps”. The whole process of monitoring.
Realizable process:
1. According to the characteristics of the tobacco project, process requirements, equipment investment, etc., use handheld reading and writing equipment to collect the data information in the label;
2. Embed RFID tags in the final logistics unit, which records the information of the logistics unit;
3. Perform accuracy verification when leaving the warehouse;
4. Use high-frequency hand-held reading and writing equipment and GPRS technology to realize vehicle tracking in half the whole journey;
5. The retail terminal keeps the label for inspection at any time; realizes the authenticity monitoring of the tobacco logistics from the warehousing link to the retail link;
[ad_2]