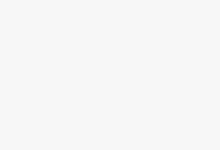
Analysis of the problems and solutions faced by the acetylene industry
[ad_1]
The high-pressure gas industry is one of the foundations of various light and heavy industries. Therefore, the more developed the industry, the greater the demand for the high-pressure gas industry. The annual output value of the gas industry is about 20 billion Taiwan dollars. There are more than 1.3 million high-pressure seamless steel cylinders. There are United States, Japan, Mainland China and so on. The type of industry is (1) Small oxygen (GOX) and acetylene manufacturing plants. (2) Air separation plants, pressure swing adsorption equipment (PSA/VSA) and underground gas pipelines. (3) Helium, ultra-high purity gas, mixed gas, special gas, electronic material gas and on-site supply plants.
Among them, acetylene is a highly dangerous gas. Because of its strong activity, it can be used to produce an unlimited amount of organic compounds. It is mostly used in industry to transport gas with specially designed pipelines. The main purpose is to use steel bulbs to hold acetylene and oxygen to cooperate with gas welding, cutting, heating, scraping and other operations. It is widely used in light and heavy industries. With the vigorous development of Taiwan’s steel industry and shipbreaking industry, the demand for acetylene has surged, but accidents are still frequent. Accidents in the acetylene industry, such as fires and explosions, average about 6 per year. Other minor accidents, such as leaks, occur many times a month; in addition, bad steel flasks are currently only concentrated in the factory corners, and there is no good recycling mechanism, and the steel flasks contain porous substances. , If discarded randomly, it will have a bad impact on the environment.
In 1989, the China Industrial Gas Association signed a commission contract with Yuanrong Company to establish Taiwan’s first acetylene cylinder inspection station to strengthen the protection of life and property. Only because of the incomplete history of the cylinder, the pressure test cannot be implemented, which is also a regret in industrial safety. In order to strengthen the two motivations for safety and green management of the acetylene cylinder industry, Yuanrong and Dongjie cooperated on this project, with the expectation that through the establishment of a management system and the application of RFID+B2B technology, the problems faced by the acetylene industry can be improved.
Before importing, the cylinder inventory should be recorded in the gas plant with a passbook
Situation description
The total number of acetylene cylinders currently in circulation is about 300,000, and Yuanrong Company imports and exports about 5,000 cylinders every day. Cylinders are transported from outside the factory to the factory. The guards need to copy the serial number on the cylinder and then type in the computer to understand the condition of the cylinder. After entering the factory, the operator must also enter the cylinder number into the computer when the cylinder is weighed. If the weight of acetone is insufficient, acetone needs to be refilled. After the replenishment is completed, the weight of acetone is determined to be sufficient before the acetylene gas can be filled. After filling the gas and before shipping, it is necessary to weigh and input the bottle number once. When shipping, copy the bottle number and send it to the guards to check the status of the cylinder shipment.
Each distributor has its own steel cylinders and delivery vehicles. Most of the steel cylinders are stored in the gas plant and recorded in a passbook. The supply order process still adopts the traditional telephone and fax contact methods. A car will go to the gas factory to transport the steel cylinders ordered by the customer once a day. When the self-owned steel cylinders are insufficient to respond, the gas factory’s steel cylinders will be used. The internal system operator of the gas plant needs to manually key in the number of the bottle, through the hub, and then through the signal collector, to the computer, and finally the information is integrated to the main computer. There is no B2B connection between gas plants.
Figure 1. Operation process of the gas plant before introduction
Problems facing the gas industry
Cylinder identification tracking management cannot be implemented
The steel bottle lacks a set of high-quality identification methods. Due to the poor working environment, the use of barcodes is easy to be fouled and broken, and the practicality is low. The frequent movement of acetylene steel bottles between upstream and downstream, coupled with the disconnection of the information systems of various gas plants, makes it difficult to track them.
Steel bottle inspection and safety management need to be strengthened
The steel cylinder is a container of acetylene gas, which bears high pressure, is dangerous, and uses harsh conditions. Safety management in filling, inspection, and transportation needs to be strengthened; in addition, the automatic collection of cylinder history data is insufficient and cannot be shared across units. Information, resulting in incomplete cylinder resume data, unable to implement the implementation of air tightness inspection (for fear of explosion).
Cylinder recycling management cannot be implemented
After poor appearance inspection, the steel bottle needs to be discontinued. At present, it can only be collected in various factories and has not been recycled. Due to the porous material contained in the steel container, it has a negative impact on the environment. At present, no centralized treatment equipment has been established, and it is easy to form an environmental protection dead angle.
There is no control mechanism for the amount of gas used in the middle and downstream
The supply of acetylene gas is traded in the traditional way, and the gas is delivered only after the downstream phone calls the goods. The roving delivery is not possible to save transportation costs and meet the delivery time; in addition, the dealers use the passbook to manually record the dealers stored in the gas plant Steel bottle inventory, but unable to understand the inventory of the gas plant itself, unable to flexibly allocate steel cylinders to meet changes in customer demand, but mostly use a large amount of steel bottle inventory to meet customer needs and increase industrial operating costs.
Imported RFID, cylinder inventory only needs to read the bottle number with a handheld reader
Import RFID application system operation process
Enter the factory from the cylinder>Wait for weighing in the weighing area>Confirm the acetone capacity>Add acetone and then weigh>Confirm the acetone capacity to fill the acetylene gas>Weigh after the filling is completed>Wait for shipment and count the number of cylinders>Cylinders leave the factory, work In the process, the staff can know the status of each cylinder as long as they read the cylinder number with a handheld reader.
Figure 2. Operation process of gas plant after RFID introduction
B2B operation mode of gas plants, distributors and direct customers
Cylinder transportation process between gas plant and distributors and direct sales customers:
When the gas factory delivers the cylinder to the direct sales customer, the delivery notice is first sent to the customer. When the truck arrives at the client, the cylinder information is read with an RFID Reader, and the information is uploaded to the system for tracking and approval when the goods are returned to the factory. The merchant sends the empty bottles to the gas factory by trucks. After the automatic counting, the dealer updates the inventory of the steel cylinders in the gas factory, and returns the number of empty bottles to the dealer, and the truck returns the filled cylinders to the gas factory. At the time, the gas plant will once again update the cylinder inventory quantity and deliver the actual cylinder quantity to the dealer after the automatic check-in. When the truck arrives at the dealer to unload the goods, the dealer will read the cylinder information with an RFID Reader and confirm the reply Gas manufacturers.
Cylinder inventory sharing:
Distributors can check the inventory of steel cylinders stored in the gas plant and the inventory of the gas plant’s own steel cylinders at any time. At this time, the dealer can consider the gas plant’s own steel cylinders as a shared inventory, and the dealer can flexibly allocate according to the changing needs of customers. Self-owned steel cylinders or gas factory steel cylinders can help meet customer needs with a smaller number of self-owned steel cylinders, and achieve the synergistic effect of increasing turnover and reducing operating costs at the same time. Gas plants use e-inventory, RFID cylinder in and out automatic check-in and inventory operations to effectively manage the number of cylinders stored by their own and dealers; at the same time, gas plants can quickly centralize order information through e-commerce, which can promote roving delivery Mode to reduce transportation costs. Direct sales customers can check the inventory status of the cylinders in the gas plant at any time, and improve the efficiency of procurement management operations through e-ordering.
Cylinder inspection and recycling process:
When cylinders are undergoing airtight pressure inspection or recycling operations, the information stored in the Tag and common application system information need to be updated simultaneously, and the platform will save the complete history data of the cylinder; in addition to allowing users to query related information through the platform, it is also possible In response to the needs of government authorities and gas associations, provide relevant information or online inquiries, so that acetylene cylinder inspection conditions can be grasped at any time in peacetime, reduce acetylene accidents, implement cylinder safety inspections, and achieve industrial safety goals; in addition, centralized treatment of bad steel bottles Real-time monitoring of recycling will help promote green management operations and strengthen environmental protection.
The steel bottle ordering and sales process between enterprises has been improved (as shown in the figure below). The distributors have their own steel bottles and delivery vehicles. The transaction method is no matter whether it is gas factory>distributor>customer or gas factory>direct customer or Yuanrong and Tong inflated each other , Are all traded through the gas industry common application system. The gas plant has its own vehicles to transport steel cylinders, mainly to direct customers. Distributors also have their own vehicles to transport steel cylinders, mainly for general customers.
Figure 3, steel bottle order and sales process (to-be between enterprises)
Acetylene cylinder inspection and recycling operations
The acetylene steel bottle inspection and recovery process (as shown in the figure below), if the cylinder leaks or has bad appearance or the inspection date expires, it will be sent back to the gas plant inspection site. After the cylinder inspection, the latest information about the cylinder specifications, inspection date, and inspection will be transferred to the common application system of the gas industry via B2B. Competent authorities, distributors or customers can learn about the inspection status of steel cylinders online. Use RFID to assist in confirming the recycling of the steel bombs on the street corners to ensure industrial safety and environmental protection.
Figure 4. Steel bottle inspection and recycling process (To-Be between enterprises)
RFID Gas Industry Common Application System Planning
Figure 5. Schematic diagram of system architecture
Establishment of cylinder tracking management mechanism:
In view of the frequent movement of acetylene steel bottles and the difficulty of tracking, the use of RFID+B2B information technology is used to establish a cylinder identification and tracking management system. At the same time, RFID can be used to assist in finding lost cylinders, which can effectively prevent the fraudulent use of steel bottles.
Establishment of the cylinder inventory transparency mechanism:
Distributors manage their own steel bottle inventory stored in gas plants through e-passbooks. Gas plants’ own steel cylinders are treated as buffer stocks and provide online query to satisfy dealers’ orders due to customer demand variations.
Establishment of ordering and sales (inventory) management system, steel cylinder inspection management and recycling management mechanism:
Record and update the use date and frequency of steel cylinders through RFID, implement regular inspections of steel cylinders, establish a recycling notification mechanism and green management.
Combined application of steel cylinder inspection and recycling management system and RFID:
RFID is used to assist gate guards and on-site operations such as filling, weighing, and handling in the factory to collect cylinder information, so as to save a lot of manpower, increase work efficiency, and implement cylinder assets.
Table 1. RFID gas industry common application platform system function list
Application mechanism and management benefits
Cylinder tracking management:
Integrate RFID and B2B information technology to establish a cylinder identification tracking and inventory mechanism; in addition to finding lost cylinders through RFID technology, it can also effectively prevent the fraudulent use of unknown cylinders.
Order sales (stock) management:
Use Reader to read Tag (electronic tag) data, and control the inventory of cylinders through the e-platform. Both gas plants and distributors can easily manage the inventory stored in the gas plant through the e-platform.
Cylinder inspection and recycling:
The latest inspection date will be recorded on the cylinder Tag (electronic tag), and the date of each inspection can be quickly queried in the e-commerce platform; the use date and frequency of the cylinder are recorded through RFID, the regular inspection of the cylinder is implemented, and the recycling notification mechanism is established. , Implement green management.
On-site process management:
Use the Reader to read the tag (electronic tag) data of the cylinder, which saves weighing, filling time, and manpower for inventory, increases work efficiency, and can effectively enhance the accuracy of cylinder data.
Figure 6. System architecture of RFID application platform for gas industry
The above four management mechanisms can enable acetylene gas plants to communicate with competent authorities, distributors, and corporate users through e-platforms and shorten mutual transaction procedures, thereby achieving information transparency; Dongjie Gas Industry RFID application platform will help Improve the overall benefits of acetylene industry operating efficiency (saving operating costs, reducing cylinder inventory costs), green management (reducing the loss of cylinder loss) and industrial safety (replacement of powder cylinders to reduce the risk of accidents).
Figure 7. The new business model of gas steel bottle will enhance the overall efficiency of the industry
[ad_2]