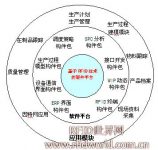
Application of RFID in traditional manufacturing MES
[ad_1]
1. System introduction
Informatization, automation, networking, intelligence, and flexibility have become the distinctive features of modern manufacturing enterprises. With the popularization and development of information technology and network technology, especially Internet technology, it has solved the standard problem and cost problem of information sharing and information transmission, making information more widely used as the basis and basis for control and decision-making. In order to reduce costs and speed up capital turnover, it is necessary to further solidify new processes or new management systems so that they can be implemented in a standardized manner. The role of information systems is to solidify management and optimize operations.
The tracking of materials and work-in-progress (WIP) and JIT and MES are new concepts put forward by the American management community in the 1990s. In the past 10 years, these aspects have developed rapidly abroad, and some professional development companies have gradually formed. At present, the domestic understanding of these aspects and the level of research and application are not high, and the gap with foreign countries is widening.
Building an RFID-based material and work-in-process tracking management system, making full use of the advanced management concepts and basic methods of JIT and MES, processing data analysis and monitoring through real-time feedback of workshop production information, strengthening workshop production control, is to improve the manufacturing industry , Especially the important measures of traditional manufacturing technology innovation ability, market response speed, and comprehensive competitiveness.
The application of RFID in the traditional manufacturing industry is a set of industrial production process automation management system developed for the materials and products in the workshop production line based on the information application of production enterprises. The precise collection, integration, integration, analysis and sharing of “work-in-process” information provides basic information solutions for the management of enterprise production materials and product life cycle management, and is the core content of the workshop manufacturing management system. The application of the system and ERP, CRM, SCM system form a good complement, effectively solve the ERP system in material and product data collection, data accuracy and real-time input and other issues, is to achieve the overall informatization of the factory or production enterprise Hub information system. In particular, the independent research and development of electronic label terminal products suitable for traditional manufacturing applications and the manufacturing application system of electronic labels based on this can meet the needs of the country in different fields, especially the market for electronic label applications in key industries such as manufacturing and medicine. need. The system has the following design concepts:
- The integrated application of RFID technology in the workshop field data terminal (such as the kanban terminal or touch screen) fully adapts to the complex requirements of the industrial environment. It does not need to look directly or use manual scanning, and effectively and concisely solves the data collection, data accuracy and real-time input, etc. Aspects of the problem;
- Provide data module design for “individual” or “batch” level, real-time, accurate, precise and efficient traceability and tracking of materials and work-in-progress, and use this as the core to establish a real-time file at the individual level of the product to realize the life of the product Cycle tracking and management;
- Apply RFID, JIT, MES, network technology, etc. to production control, accurately, real-time, and comprehensively reflect the production process status information, effectively and agilely guide the industrial process, form a good complement to ERP, CRM, SCM, and promote the “transparent factory” Construction, promote the optimization of production, management and organizational structure, and promote the realization of the JIT production model;
- The tracking management of “materials” and “work in progress” is closely integrated with quality, benefit, efficiency, warehouse management, logistics, etc., to encourage workshop workers, manufacturers and material suppliers to form a community of interests.
The Application of RFID in Traditional Manufacturing (MES) project makes full use of the characteristics of RFID, adopts specific RFID data collection terminals that can be installed in complex industrial sites, adapts to the environmental requirements of traditional domestic manufacturing workshops, and is moisture-proof, oil-proof, and lightning-proof , Electromagnetic interference, heat resistance, etc., meet the needs of non-contact automatic collection of materials and products in progress, and provide information input interfaces and query interfaces for the management system.
At the same time, on the basis of the RFID data collection terminal, a workshop-level production execution management system with a software basic platform and a series of application modules can be developed with the tracking of materials and work-in-progress as the core. In the design process of the system, through the design of data modules oriented to “individual” or “batch” levels, the traceability and tracking of materials and work-in-progress will be realized in real time, accurately, meticulously, and efficiently. This is the core to establish individual products. Level of real-time archives. In addition, in the system design concept, RFID, JIT, MES, network technology, etc. are applied to production management and control, accurately, real-time, and comprehensively reflect the status information of the production process, effectively and agilely guide the industrial process, and form a good relationship with ERP, CRM, and SCM. Complementary, promote the construction of “transparent factory”, promote the optimization of production, management and organizational structure, and promote the realization of the JIT production model.
The application of RFID in the traditional manufacturing industry is an industrial information application system for the manufacturing industry. The use of high-tech, especially automation technology, information technology to carry out beneficial transformation and information services to the traditional industry (manufacturing industry) is to promote my country’s export-oriented The main manufacturing industry develops high-tech products. The application of RFID in traditional manufacturing is aimed at my countrymanufacturingThe actual situation of the development of advanced, integrated, production line-oriented management software can effectively improve the operating economy and service quality of discrete manufacturing enterprises. The successful development of this project will undoubtedly have a significant driving effect in the industry .
The use of RFID technology can improve the traditional working mode and realize the full-process control and traceability of products in the manufacturing industry. And to develop a complete RFID-based production process control system is to integrate RFID technology through the entire production process (order→plan→task→material preparation→cold processing→hot processing→finishing→inspection→package→warehouse→transportation) to form Closed-loop production of the enterprise.
From a development perspective: the implementation of RFID technology in the manufacturing industry can also extend from raw material manufacturing, procurement to semi-finished products processing, finished product manufacturing, wholesale, distribution to retail, through every link of the supply chain of the whole society, until the final consumer. Therefore, the use of RFID tags in the manufacturing industry can break the isolation of a system’s internal use and extend RFID technology to the upper end of the supply chain. The research results can also be extended to other related product manufacturing applications, which has good application prospects and industry demonstration effects. These industries that can apply the research results even include food manufacturing companies.
2. System Features
RFID workshop manufacturing and execution system or work-in-process tracking and management system has the following characteristics:
-
Production plans and processes are directly transferred to procedures and equipment (while ERP and MRPII can only be transferred to varieties and workshops), they directly guide equipment processing, prevent cross-process processing, and reduce process errors;
-
Real-time data collection, plan assessment can be carried out in time, and production progress can be monitored in real time;
-
The functional departments of each workshop can share production data, understand the production progress of related processes, and facilitate production coordination. Accurately confirm the delivery time and realize batch management;
-
Process feedback correction: correct process errors in time and shorten the process correction cycle;
-
Processing data is effective, reducing manual input and paper transfer;
-
Facilitate quality traceability;
-
Smart Kanban: complete quality information collection and quality analysis;
-
Extended logistics management: RFID batch number-barcode-product;
-
The RFID data collection terminal used at the workshop site is used to provide the system with information about materials, products, equipment status, personnel information, etc., to achieve two-way communication between the system and specific operators. Has the following functions and advantages:
Ø Automatic collection: can automatically collect materials, work-in-progress, workstations, and personnel information without contact;
Ø Information query: can query production plan, production process, product batch and other information;
Ø Information input: equipment status information, processing quantity, processing status, quality information, etc.;
Ø Resistance to harsh environments: It has the performance of moisture-proof, oil-proof, lightning-proof, electromagnetic interference discharge, and heat-proof.
The system includes the following tasks:
-
Construction of overall architecture and system model: Through in-depth analysis of network architecture, factory equipment, communication routing, software and hardware combination, and system scale and performance, establish the hierarchical relationship between monitoring system software and data acquisition hardware equipment, and determine each functional module The division of modules and the interfaces between modules complete the construction of the overall architecture. Fully consider the Integratability, Configurability, Adaptability, Extensibility and Reliability of the system;
-
Software platform architecture construction: Based on object-oriented design technology, distributed network, and various advanced database and configuration technologies, build a system software basic platform suitable for real-time, on-site, and remote monitoring, easy to expand and modify, and fully reflect the orientation The system application integration of discrete objects supports real-time activities and realizes the combination of management and control based on on-site management rules and comprehensive management knowledge. It mainly includes the construction of software system function positioning, platform selection and data collection (Data Collection), data storage (Data Storage), network application (NET/Web Application), client query browsing (Client/Web Viewer) and other structures;
-
Specific software development of functional modules, including:
Production process modeling (CONFIG)
Production planning and production management
Field data collection
Material tracking query
Work in progress tracking query
Product Life Cycle Archive
Quality and performance analysis query
Internet applications
-
Workflow research: design workflow models and network data flow planning, support various control and communication strategies, support various workflows in the production process, and realize automatic driving, recording, tracking, analysis, and information sharing of manufacturing production and management processes, etc. , And easily integrate CORBA/STEP to achieve seamless integration with ERP, PDM, SFC, etc., forming a smooth channel for information flow;
-
Device communication and integration and data interface technology: standardize different industries and different types of monitored devices and system interfaces, including digital or analog sensors, programmable controllers (PLC), direct digital controllers (DDC), control actuators, video Image devices, etc.; research on data formats and protocol conversion methods of various equipment and systems to meet large-capacity and high-speed data storage and access, with real-time and continuous historical data retrieval and playback functions, and provide complex and special data queries ;
-
The realization of intelligent decision support function: the purpose of real-time monitoring is to provide data for the decision-making of dispatching and operation operators. If the system can reflect the production status while having data analysis functions, and then propose operation plans and suggestions, its practicality can be achieved Really manifest. The solution of this problem depends on the application of intelligent technology and the generalized expression of expert experience;
-
System testing: including unit testing, overall testing and comprehensive testing.
3. Application technology scheme
1. The overall architecture of the system
Figure 3-1 shows the typical architecture diagram of each level of the system, including the software platform and application module system, as well as the hardware platform on which the system depends.
The software platform is the basic core component of the system, including a series of components that implement various core logics, and encapsulated into different component packages:
- Scheduling Strategy Component Package
- Interface development component package
- Production process model component package
- WIP component package
- SPC analysis component package
- Device communication interface component package
- ERP interface component package
RFID terminal component package
Figure 3-1 System typical architecture diagram
The application module system is built on the framework of software platform and hardware platform to realize various specific management functions of the system, including:
- Production process modeling
- Production planning and production management
- Field data collection
- Material tracking query
- Work in progress tracking query
- Product Life Cycle Archive
- Quality and performance analysis query
-
Internet applications
2. Hardware platform foundation: RFID data integration terminal
1) RFID data integration terminal (RFID DCS)
The RFID DCS terminal (reader) will be mainly installed at the production station of the production line to provide the MES system with information about materials, products, equipment status, personnel information, etc., as well as to provide specific operators with operating information. Two-way communication.
-
The need for automatic collection: the information of materials, work-in-progress, workstations, and personnel can be collected automatically without contact;
-
The needs of the collection environment: the data collection site is diversified, and the collection equipment and the collection terminal are required to have moisture-proof, oil-proof, lightning-proof, electromagnetic interference, and heat-proof performance;
-
Query needs: can query production plan, production process, product batch and other information;
- Information input needs: equipment status information, processing quantity, processing status, quality information, etc.
The specific method is to add LCD display circuit, PVC keyboard input circuit, digital display measuring instrument communication interface circuit, RS485 serial communication circuit, TCP/IP network to the electronic label reader (data integration terminal, RFID DCS) based on RFID technology. Modules such as communication interface circuit. The liquid crystal display can display the issued production plan, production process, product batch and other information, and the keyboard can submit equipment status information, processing quantity and quality information, etc., so as to fully track the normal flow of workpieces in the normal process route and handle various abnormalities It records the completion status of each work piece in each process and the current position and online status of each work piece. It can automatically record the status of each work piece (pending inspection, qualified, Unqualified), all-round recording of the circulation (process, station, time, status) of each workpiece in the manufacturing platform.
2) Communication method:
The RS485 serial communication circuit and the TCP/IP network communication interface circuit can be selected as one of the communication methods to interface with the PC. After the information collected by the terminal enters the PC through the communication interface, the PC then stores the information, processes the information, and saves the results to the server. The PC can also transmit the production plan of the workshop on the day and the production situation of the workshop to the terminal through the communication interface and display it on the terminal’s LCD screen. After the workers see the feedback information, they know the production tasks of the day and the current working conditions to execute them. production task. In the RFID DCS terminal collection system, there is a certain communication protocol between the PC and the terminal to ensure the successful communication of terminal data. The communication flowchart of the data acquisition terminal based on RS485 communication is shown in Figure 3-2:
3–2 Workshop communication method
3. Application architecture and functional modules
“RFID-based material and work-in-progress tracking management system” uses RFID-based data collection terminal equipment as the main component of the functional stations of each production unit in the workshop, and through data collection and feedback of each production unit, it forms the entire plant or the entire assembly line. An open network that meets the needs of closed-loop production management. The system uses a database server for real-time data access and comparison, and realizes the monitoring and control of production information and the management of the production process. The system supports dual-machine architecture, provides high-efficiency and high-availability services. It is designed based on large databases to facilitate the storage, comparison and operation of large amounts of real-time data, generate various statistical analysis reports, and provide standard Internet browsing based on web applications. Inquiry and remote information request.
As can be seen from Figure 3-3, each functional station interacts with the system server through the local area network, while other query terminals also query the data, reports and graphics provided by the server through the local area network. Outside the enterprise, you can connect to the server through the Internet, and perform information publishing or reading operations on the system within the set permissions. The company’s internal management and external related business units are linked through this system to form a close whole, achieve real-time information sharing, and make business processes orderly and efficient.
picture3-3 System application architecture diagram
1) Production process modeling (CONFIG)
“Production process modeling” is mainly used to set the production-related data of various products. It describes the processing technology and route of the product by simulating the actual production situation, defines the material information and defect information of the product, and describes the processing machine Important information such as production capacity and processing methods, and in turn, provides the infrastructure and system configuration for follow-up tracking behavior, establishes a production business model, and also defines database storage details. Of course, the “Production Process Modeling” module can also add settings according to customer needs.
-
Describe the processing technology of the product
-
Describe the processing method of the processing machine
-
Set the product’s production line, production zone, production group, production station, etc.
-
Set production period (define time arrangement format)
-
Expected output target (or describe the production capacity of the processing machine)
-
Production process setting, flexible setting of product production route process (Routing Control)
-
Work Order management, flexible setting of various workstation operating modes (such as assembly mode, test mode, etc.)
-
Define/modify product defect (or defect) phenomenon table (Error Code)
-
Define/modify the product defect (or defect) reason table (Reason Code)
-
Set the material data information of the product
-
Important parts (Key Parts) settings, set and modify the main parts requirement table (Key Parts BOM)
-
Customer management, set customer name
-
Supplier management, supplier information can be set
-
User authority setting and staff management
-
Standard information code management: mainly for electronic label code management, formulating the identification code format of products, materials, work-in-progress, etc. The coding rules of product identification codes are determined mainly according to corporate rules and industry rules to ensure product regularization and unique identification.
-
Data settings (database storage details)
2) Production planning and production management
In this module, work planning and production management are combined to reflect the integrated effect of planning and management and timely comparison, which specifically includes the following:
- Automatic generation of daily plan
The independent daily plan generation service program is used to directly communicate with the terminal host computer through the local area network, which can reduce the frequency of accessing the database when querying and transmitting terminal data, greatly reducing the burden of the database management system. - Production planning management
The workshop operation plan management module first uses the ERP interface components to obtain the requirements of the production plan passed down by the factory or ERP management system, and then calls the scheduling strategy component to combine the resources required for the production operation, including equipment, personnel, materials, and history Records, etc., in a short period of time to predict the production situation of the workshop (such as mastering the weekly production status of each work order), prepare the workshop operation plan, and ensure that the resource allocation meets the goal of planning and scheduling optimization. The workshop operation plan is directly distributed to production units such as workshops and warehouses to guide specific production operations and meet BTO production standards. At the same time, it provides real-time production status query connection, which is convenient for timely adjustment of plans.
Ø Resource allocation and status management: guide workers, machines, tools and materials how to coordinate production, and track their current working status and just completed status
Ø Detailed process scheduling: used for scheduling and implementation of production plans
Ø Production unit allocation: used for scheduling and implementation of production plans
Ø Human resource management: provide minute-level update of employee status information data (working hours, attendance, etc.), and guide the work of employees based on changes in personnel qualifications, work patterns, and business needs
Ø Exception management: some special settings for planning
Ø Arrange and set the production plan according to the order situation, go online, modify, close and delete the plan
Ø Generate product serial numbers according to coding rules; compile data sheets to the warehouse picking system according to the order and BOM, and generate batch numbers and serial numbers of product parts according to the coding rules for easy tracking
-
Production management module
After the product enters the production process, it begins to involve production management. The production management module provides real-time production status inquiries, which is convenient for timely adjustment of plans.
Ø View the system layout of each production line in the whole factory, and monitor each station in real time
Ø Query the production status of each production line according to the product model (Model)
Ø Query the production (input, output, delay and completion) of the plan and instruction according to the plan or work order (Work Order).
Ø Statistical analysis of the test results of each test station and the main bad conditions of the product
Ø Query the product inventory situation on the workshop site
Ø Query the process card (Travel Card) of the online production machine
Ø Query standard production reports and EXCEL output capacity analysis, according to work instructions, date settings to draw graphs to show capacity analysis
3) Field data collection
The field data acquisition module relies on the RFID DCS and other equipment communication interface components and field equipment for information interaction, and runs various interfaces or keyboards composed of interface development components to provide on-site operators with information input interfaces to help the system have first-hand information. Collect all necessary information related to manufacturing.
Data input sources include:
Ø RFID system
Ø Bar Code Scanner
Ø Personnel system (working hours and absenteeism rate)
Ø Quality inspection system
Ø Test system
Ø Machine and process monitoring system
Ø Other computer systems
Ø Personnel input
Ø The production information log file of the product at each workstation
4) Material tracking query
-
Speed up the picking speed, improve the utilization rate of materials and production efficiency;
-
Contribute to the standardized management of materials and eliminate the messy conditions of materials;
-
It is convenient for material tracking management and statistics, helping to achieve reasonable material inventory preparation, effectively reducing inventory costs, and shortening the time occupied by corporate funds;
-
It is conducive to the establishment of material quality inspection files, linking with purchase orders to establish an evaluation system for suppliers, and improving the quality control of supplier supplies;
-
Staff training is easy and standardized; reduce/eliminate paper work.
5) Work in progress tracking query (WIP)
Provide tracking query on the status of products being manufactured on the production line. Through this module, managers can quickly and timely understand the production situation of the production line, real-time monitoring of product quality and production efficiency. The background is connected to the corresponding database, which can display the basic information of the corresponding work order, pallet information, product distribution status, process and maintenance status, detailed component information, etc. during the relevant period. With WIP, you can understand the location and specific conditions of the product on the production line anytime and anywhere, prevent the accumulation of faults, and help reduce the number of products in progress.
-
Set automatic refresh and refresh interval
-
Query the production status of the production line and the production status of each product
-
Query the status of work section and group
-
Query the assembly status of the main parts of each product
6) Product life cycle archive
Understanding the entire life cycle of a single product is very useful in many situations, and product tracking is one of the essential functions of manufacturing management software. In addition to meeting the requirements of quality assurance, statistical analysis, inventory management, etc., it also allows users to go back to any production step and any processing data, even for special processing procedures.
7) Quality and performance analysis query
-
QC: Quality Control: display the product qualification rate of the online inspection; display the total number of products inspected, that is, display information such as output and quality; query the inspection results according to the model and other parameters for bad phenomena.
-
QA: Quality Assurance: Use random inspection methods to inspect products on a batch basis. If the defect rate is higher than the standard, QA has the right to return the whole batch. QA must confirm that the product quality meets customer requirements. export.
-
QM: Quality Management: Provides comprehensive production quality information query, analysis and statistics of product qualification rate, repair rate and straight-through rate and other parameters that reflect the overall performance and efficiency of the system, and reflect the quality of the workshop in real time.
-
SPC: Statistics Process Control (Statistics Process Control): Quality Statistics Control (SPC) is an advanced function of quality management. It collects quality data from the production process, applies statistical analysis techniques, and scientifically distinguishes random fluctuations in product quality during the production process. With abnormal fluctuations, an early warning is given to abnormal trends in the production process, so that managers can take timely measures to eliminate the abnormalities and restore the stability of the process, so as to achieve the purpose of improving and controlling quality.
-
IQT: Incoming Quality Tracking: Responsible for the quality tracking of raw materials, and connects with the supply chain management system (SCM), records incoming inspection information and statistical analysis of supplier supply quality, and performs input selection and control Good basic data work. In this way, once a batch of products has quality problems due to raw materials, it can be quickly traced or claimed.
8) Internet applications
The Internet application module uses advanced network visualization technology, WEB technology, .NET technology, middleware technology and extensible program structure to provide a secure architecture, common navigation methods and a friendly graphical user interface (GUI) to obtain The windows, reports, files, alarms, history and real-time information generated by the system conversion provide simple information channels for the company’s internal, customers and external supply chains. At the same time, a standard browser is used as the client interface to reduce the cost of system installation and maintenance. .
-
Authority management function, easy to control the range of functions that users can use
-
Realize BTO (Build to Order) production on the Internet
-
OEM customers can know the production and quality of the commissioned products at any time
-
The external authorized maintenance department can inquire the production records of the repaired products in time
-
Headquarters can understand and manage the production and quality status of local branches
-
Managers can keep abreast of the situation of the factory through the Internet when they are away on business
4. Implementation effect of RFID in manufacturing MES application
The RFID MES system implemented in a southern parts manufacturing limited liability company (as shown in Figure 4-1) speeds up the development of new products, improves logistics management, improves market resilience, and solves problems such as insufficient delivery rates. The improvement has greatly reduced production costs, and the economic benefits obtained (specific data are shown in Table 4-2) are as follows:
- Improve logistics management, increase production efficiency, and save production management costs.
After the processing data is informatized, the logistics management of the production process is improved. The processing status of various products, product quality and the completion of each order can be reflected in real time, which facilitates the control of front-line commanders and business managers. The logistics between procedures is smoother, and the production efficiency is increased by more than 10%; at the same time, it saves the investment in plant and equipment; the application of the system can also reduce the management personnel and reduce the labor cost. - Real-time monitoring of the production process and product quality reduces the scrap rate.
Real-time monitoring of the production process and production quality is conducive to reducing the scrap rate. - Clarify quality responsibility.
Realize full quality tracking, clarify quality responsibilities, ensure product quality, and improve customer satisfaction. - Overcome the confusion of products such as mixed materials, and overcome the processing confusion of cross-process processing, missing process processing, and leftover mantissas.
The implementation of informatization projects will fundamentally eliminate product confusion such as mixing that is difficult to overcome in the “multi-variety, small-batch” production process, and eliminate cross-process processing, missed process processing, leftover tails, product loss and other confusions. - Realize the reasonable arrangement of the production plan, and the finished products will be delivered in time.
The system releases the production plan in place, manufactures in time, and realizes the management and tracking of the work-in-progress and the real-time monitoring of the data collection of equipment information, working parameters and production conditions. It is convenient to adjust the production plan and ensure the supply. At the same time, it is conducive to the subsequent analysis and analysis of production information Arrange the prior control of the production plan. - Realize paperless process and reduce mistakes.
The production terminal directly obtains the process to avoid human error in distributing process documents, thereby avoiding wrong process production. - Realize the real-time collection of detection data, and the management of measuring tools is more convenient.
The system can obtain real-time detection data through the connection of the digital measuring tool and the terminal; and can make the management of the measuring tool more convenient through the terminal broadcast mode. - Speed up the development of new products.
Combined with the wide application of CAD/CAPP, it shortens the preparation time of production technology and speeds up the development of new products. - Solve the problem that the ERP software cannot be connected with the on-site manufacturing in the workshop, and provide basic data support for ERP.
The foundation of enterprise informatization is the real-time and accuracy of data collection. The application of this project fundamentally solves the problem of accurate collection of basic data. - Improve market resilience.
Through the information integration of each link of production and operation, it supports the integration of technology, and then from the integration of technology to the integration of technology, operation and management, and people and organizations, and finally achieve the integration of logistics, information flow, and capital flow and optimize operation, thereby improving This improves the company’s market competitiveness and resilience. - Energy saving and consumption reduction, more environmentally friendly.
The application and implementation of RFID technology in industrial process automation improves the process speed and production efficiency of enterprises, while also improving marginal benefits, saving energy and raw materials. From this perspective, the system also indirectly reduces the environmental protection of manufacturing enterprises. And the destruction and impact of natural resources; at the same time, the application of the system has realized the company’s “paperless process” management, greatly reducing the use of paper, and achieving greater environmental benefits.
Figure 4-1 Application of RFID technology to manage machinery processing plants
If you have any questions, please contact
Address: Yumin East Road, Xicheng District, Beijing5No Ruide Building0811room
[ad_2]