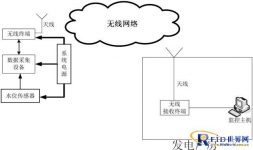
Design scheme of wireless transmission for water level detection
[ad_1]
1. System background and design goals
This system completes the water level detection, and transmits the data of the water level sensor back to the power station monitoring center through the wireless network. In this way, there is no need to carry out long-distance construction and wiring like traditional data collection methods in order to be able to transmit data back to the control center, reducing the difficulty of installation and maintenance.
The automatic water level detection and wireless transmission equipment of this scheme achieves the following design goals:
1. The equipment is a self-contained system, except for the power supply, no additional hardware equipment support is required, and the detection data is directly output through the serial port;
2. Simple installation and maintenance;
3. The system comes with network configuration software, which is easy to operate.
In the scheme, the field data acquisition equipment and the data receiving equipment in the power plant (converting wireless data into RS485 bus data) all adopt traditional design schemes. In the design, there are several alternatives. The main difference is that the specific methods for long-distance transmission of data are different, but they all use wireless transmission.
Second, the composition of the system
This system is composed of system power supply, water level sensor, data acquisition and control equipment, wireless data transmission and sending terminal, and wireless data receiving terminal. Among them, the first four parts constitute the front-end collection equipment, which is installed at the water level collection site. The system power supply provides a stable and reliable power supply for the whole machine; the water level sensor completes the detection of the water level; the data acquisition control system completes the collection and analysis of the RS485 signal output by the water level sensor. In addition, complete the control of the wireless module and the hard reset system; the wireless terminal completes the network transmission of data. The wireless data receiving terminal is a wireless terminal, which obtains the data obtained by the front-end acquisition device through the wireless network, and converts the wireless data into RS485 bus data output.
2.1. The composition and characteristics of the detection system
The system adopts a wireless detection system with wireless network technology. The output signal of the water level sensor is sampled by AD, converted into data that can be transmitted by the wireless network, and transmitted to the power station monitoring center, realizing real-time online detection of the water level, and truly achieving a long distance telemetry.
The system is real-time: real-time online monitoring; flexibility: users can set parameters flexibly and conveniently according to their own needs; security: whether it is products, tools, and maintenance, all have system security and reliability; collection methods : Features such as real-time collection.
Figure 1 Schematic diagram of system structure
1) Sensor part
The MPM4700 intelligent liquid level transmitter of the Sino-US joint venture Mike Sensor Company is selected. The sensor is characterized by: all stainless steel structure, small size, and the enclosure protection level can reach IP68; the material in contact with the medium is ceramic, which can resist strong Pressure shock; the top stainless steel cap can be removed, which can imitate accidental damage of the diaphragm, and is convenient for regular cleaning; the pressure-sensitive diaphragm has a large contact area with the medium and is not easy to be blocked.
2) Wireless data transmission equipment
In this solution, three wireless data transmission methods are designed, each of which has advantages and disadvantages. The three wireless transmission methods are described in detail below.
A. Wireless GPRS data transmission method
Figure 2 Wireless GPRS terminal
The GPRS module needs to install a GPRS module respectively in the water level detection point and the power station monitoring room, which mainly completes the long-distance data transmission. GPRS is actually a packet switching protocol for mobile phones to connect to the Internet, which can make the GPRS device an Internet device, facilitating data transmission.
The company’s GPRS module, on the basis of the common module, adds the TCP/IP protocol, and at the same time comes with an AT command interpreter. Using the RS485 interface, the data transmission part adopts a transparent transmission method, which is convenient to connect to various existing mature equipment without changing the existing data transmission protocol.
B. GSM SMS transmission method
Figure 3 SMS module
In wireless data transmission, short messages are currently used very much. As long as users are familiar with AT commands, they can use SMS to transfer the collected data to a remote SMS receiving module.
3) System power
The system power supply adopts an external 220VAC 1A power supply. The system power supply module uses an isolated switching power supply. First, the 220AVC power supply is converted into a 12VDC DC power supply, and then converted into the power supply required by each module.
4) System maintainability design
The system is installed in the field. If there is a problem with the system, engineers need to go to the site for maintenance, which is time-consuming, labor-intensive, and financial. Therefore, two layers of safeguards are designed to prevent system crashes. The first layer of measure is to add “heartbeat” packets to the wireless network. If heartbeat packets are not received for a long time, a soft reset will be performed, and a reset command will be sent to other devices in the front-end system to allow all devices to perform a soft reset . However, the first layer can only be carried out when the front-end equipment does not crash. Therefore, a hard reset method independent of the front-end equipment is required. When the front-end equipment system has a problem, the equipment can be operated to complete a reset and restart. . The second layer of measures is to equip the front-end equipment with a short message module, and the short-message module output IO to control the power supply of the front-end equipment. When there is a problem with the front-end device, the remote control center sends multiple (for example, 3, to prevent miscommunication) short messages to the short-message module of the front-end device. After the short-message module receives the short message, it judges whether it is a reset command. Then turn off the power of the front-end equipment and power on the equipment again after a delay of several seconds, thus completing a system reset.
5) Installation of front-end acquisition equipment
The front-end collection equipment, namely system power supply, water level sensor, data collection equipment, and wireless data transmission and sending terminal, are installed in the open air environment. Therefore, they must be waterproof, rainproof, and lightning-proof, so their structure and installation need to be done. Corresponding design, the following first solves the waterproof and rainproof problems, and then designs the lightning protection in the fourth part.
2.2
Water level sensor installation
Since this detection system measures the water level at the upstream water inlet of the power plant, that is, the liquid level of the flowing water, a steel pipe of about Φ45 is inserted into the water during installation, and several pipes of about Φ5 are opened at different heights in the opposite direction of the water flow. The small holes are used to allow water to enter the pipe, and the cable and the junction box are fixed at the outlet of the pipe. The installation diagram is as follows:
Figure 4 Schematic diagram of on-site installation of liquid level sensor
Figure 5 Fixed tripod and flange
The part that is put in the liquid is a fully sealed stainless steel structure. The sensor and amplifying circuit are all in a stainless steel fully sealed housing, with a protection level of IP68; the junction box is a cast aluminum structure, which is installed in a convenient place for wiring, and the protection level is IP65. The sensor, amplifier circuit, and junction box can be installed in the open.
The waterproof measures adopted for the installation of system power supply, data acquisition equipment, and GPRS terminal are to fix the system power supply, data acquisition equipment, and GPRS terminal installed outdoors in a closed metal case. Among them, external cables, such as antenna extension cables and signal cables for wireless detection terminals, are connected to the outside of the chassis with waterproof and explosion-proof aviation plugs. No matter where the opening is set, the opening should be filled with waterproof material (such as putty paste). The metal case is installed on the other end of the fixed tripod of the water level sensor device, as shown in Figure 4 above.
6) Wireless data receiving terminal
The wireless data receiving terminal is installed in the power plant. Considering that the signal in the plant may be poor, it is necessary to use the radio frequency feeder to extend the antenna outside the plant, as shown in Figure 1. The wireless receiving terminal obtains the water level data and other field parameters from the front-end equipment through the wireless network; on the other hand, it outputs the obtained data to the monitoring equipment of the plant through the RS485 bus, or converts the water level data into a 4-20mA analog signal output.
2.3, wireless sensor network mode
4 2.4GHz wireless data transmission module
2.4. Comparison of three wireless data transmission methods
Transmission distance: The transmission distance of GPRS and GSM short message methods is only affected by the mobile network. These two methods can be used wherever there is a mobile network; wireless sensor network, the reliable transmission distance is 3Km, due to the water level measurement point The distance from the power plant is up to 9Km, and there are mountains in the middle. Therefore, relay nodes must be added and relay transmission can be used to send data back to the power plant. In addition to the measurement point and the plant, at least 3 relay nodes are required.
Real-time data transmission: GPRS mode, because the device is always in the GPRS network, two GPRS devices form a point-to-point network, so data can be transmitted faster with a delay of less than 10s; GSM short message mode, the sending and receiving of short messages is very important The mobile network is still a relatively complicated process. The party sending the text message must first send the text message to the text message center, and then the text message center finds the destination mobile phone number, and then sends the text message to the target. The message may be blocked and the signal is good or bad. The delay varies from a few seconds to a day; the wireless sensor network, because it is a self-organizing network, is not affected by the mobile network. Once the network is established, it can transmit data faster, generally with a delay of about 2s.
Maintenance fee: GPRS data is charged according to the flow rate. Generally, the monthly rent is 5 yuan, and the flow rate can be 30Mbytes. It can basically meet the requirements of most output transmissions, and the usage fee is low; SMS mode, if there is no data, you need to send one Short message, although the capacity of short message can reach 140 bytes per message, it is basically a short message for a few bytes, so if there are 5 short messages per minute, the monthly cost is very amazing; wireless sensor Since the network uses an ad hoc network and is an application-free 2.4GHz frequency band, there is no cost requirement during the use process.
Reliability: Because the three methods all use imported components and mature solutions, and all three methods have been used in multiple engineering projects, the reliability and technical maturity are relatively high. Considering the real-time nature of installation, maintenance and data transmission, the GPRS method has certain advantages among various methods, but it has to bear a certain use cost; if the use cost is a problem, you can choose the wireless sensor network method, but it needs to be increased. Follow the installation and maintenance of the node. Considering comprehensively, it is recommended to use GPRS.
2.5, GPRS network setting software
If you choose the GPRS mode, considering the particularity of the GPRS network and the flexibility of use, this system needs to be equipped with a network setting software to set the serial port baud rate, working mode, DTU mode, etc., the software interface is as shown in the figure below Show.
Figure 7 GPRS module network configuration software interface
3. System lightning protection design
The waterproof and rainproof design of the front-end detection equipment has been completed before, and the following is designed for lightning protection.
3.1 Ways of lightning damage
Since the front-end equipment is installed outdoors, thunderstorm weather will affect the equipment, which may be caused by the following
This way damages the system.
① Direct lightning strike: Lightning strikes directly on the front-end equipment in the open air and causes equipment damage; lightning strikes directly on the power supply or detection cable, causing the cable to fuse.
② Lightning wave intrusion: When the power line, signal transmission or other metal pipelines are struck by lightning or are induced by lightning, the lightning wave invades the equipment along these metal wires, causing potential difference and damage to the equipment.
③Lightning induction:
When lightning strikes the lightning rod, a strong transient electromagnetic field will be generated around the down conductor. Detection equipment and transmission lines in the electromagnetic field will induce a large electromotive force. This phenomenon is called electromagnetic induction. When a charged thundercloud appears, a charge opposite to the thundercloud will be induced on the buildings and transmission lines under the thundercloud. This kind of induced charge can reach 100KV on low-voltage overhead lines and 40-60KV on signal lines. This phenomenon is called electrostatic induction. Studies have shown that the surge caused by electrostatic induction is several times that caused by electromagnetic induction.
Electromagnetic induction and electrostatic induction are called induced lightning, also called secondary lightning strike. Its damage to equipment is not as severe as a direct lightning strike, but it has a much greater chance of occurrence than a direct lightning strike. According to the statistics of the former Ministry of Posts and Telecommunications, lightning strikes caused by induced lightning accounted for about 80% of the total lightning strikes.
3.2 Lightning protection measures for wireless equipment
Based on the structural analysis of wireless devices and the possible path of lightning intrusion, the following lightning protection solutions are designed. The front-end equipment should be placed within the effective protection range of the lightning rod (lightning rod or other lightning conductor). When the front-end equipment is installed independently, in principle, in order to prevent the transient high potential of the lightning rod and the down conductor, the distance between the lightning rod and the front-end equipment is 3-4 meters. If it is difficult, the lightning rod can also be erected on the chassis of the front-end equipment, and the down conductor can be directly used by the metal rod itself or choose Φ8 galvanized round steel. In order to prevent electromagnetic induction, the power line and signal line should be passed through the metal pipe to achieve the shielding effect, and both ends of the shielding metal pipe should be grounded.
In order to prevent lightning waves from invading the front-end equipment along the line, appropriate lightning arresters, such as power lines, signal lines, and control lines, should be installed on each line in front of the equipment.
For details, please contact
Chongqing Qinzhi Technology Co., Ltd.
Phone: 023-68691867
Fax: 023-68696923
Contact: Hu Dingjun
websitewww.spriew.com
15th Floor, Gaochuang Jinye Building, 18# Yuzhou Road, Shiqiaopu, Jiulongpo District, Chongqing
[ad_2]