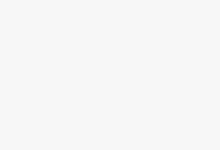
Radio Frequency Identification (RFID)-find your car
[ad_1]
Radio Frequency Identification (RFID)-Make the production process transparent and allow individuals to continuously monitor the production process. In the production process, no matter how strict the monitoring is, it is not excessive. In fact, the monitoring of the production process is not too strong, but too small. Gabriel system can provide a new and improved radio frequency identification (RFID) system that makes transparent production possible.
“Radio Frequency Identification” (RFID) is a method of reading and storing data in a non-contact and invisible manner. Four factors determine whether a radio frequency identification (RFID) system is suitable for use: distance, speed, amount of data, and ease of integration into existing automation systems.
The buyer makes the final decision
With the development of the “personalized car” trend, the automobile manufacturing industry has become a pioneer in the field of radio frequency identification (RFID) systems (the automobile manufacturing industry is also a pioneer in many other fields). Nowadays, buyers can customize cars, and almost every car will have some personalization. Therefore, it is necessary to mark the individualized places required by customers, so as to achieve transparency in the entire production process.
Since automobile manufacturing involves almost all traditional manufacturing processes, and there is no universal solution for all production processes, manufacturers usually have to adopt a variety of methods to achieve transparency in the production process. In addition to mechanical engineering technology, some transportation technology, processing technology, logistics, ordinary metal processing technology, printing technology, etc. may also be used.
Due to the numerous processes, different requirements, and inter-related processes, this is very different from a process that only involves the distribution of goods.
Although there are many differences in the treatment process, the monitoring system should be safe, fast, durable, anti-interference and resistant to high and low temperatures. Each radio frequency identification (RFID) system includes a data carrier (Tag), a read-write head (Reader), an interface module, and a high-level controller. According to specific requirements, there are sometimes logistics systems and installation software.
There is a clear difference between a barcode system and a radio frequency identification (RFID) system. If we replace the data carrier with bar code labels and replace the scanner with a transceiver, we can get a bar code system-this system has its own advantages as well as its own shortcomings. However, if we pay attention to the special aspects of the radio frequency identification (RFID) system and compare it with other systems, we will discover the huge difference between the radio frequency identification (RFID) system and other systems.
Cold and hot
Whether it is a one-dimensional bar code label or a two-dimensional bar code label, they can only be read in one direction. Since the original data carrier only had a read-only memory function, the superiority of radio frequency identification (RFID) technology was not prominent at the beginning. Compared with traditional bar code systems, the biggest advantage of radio frequency identification (RFID) technology is that it is not sensitive to stains and humidity, and can read data through opaque media. Radio frequency identification (RFID) has some other advantages. Current data carriers use serial electronically erased programmable read-only memories (EEPROMs), which have multiple write memory capabilities. Using non-volatile ferroelectric random access memory (FRAM) technology, the memory capacity can even reach 2kB. Serial electronic erasable programmable read-only memory (EEPROMs) can only be rewritten 105 times, while non-volatile ferroelectric random access memory (FRAM) can not only rewrite 1010 times, but also faster. If the speed requirements are high, or if the data must be stored on the data carrier again, then non-volatile ferroelectric random access memory (FRAM) will become the only choice. If data is written into the serial electronically erased programmable read-only memory (EEPROM) every second, the security of the memory becomes unreliable after a day. But for non-volatile ferroelectric random access memory (FRAM), the security of the memory will become unreliable after 300 years. The development of transmission characteristics has gone through a similar process. Initially, according to the data transmission quasi-standard, the transmission frequency is 125kHz, occasionally dedicated frequency such as 1.5MHz. Now, many different frequencies are in use.
Companies that conduct global operations choose only one of these frequencies to use. In the field of industrial system technology, people focus on using the 13.56MHz technology of the ISO15693 standard, because this frequency can directly activate the data information in the data carrier through the radio frequency field. Compared with the 125kHz technology, it not only has a faster transmission speed, but also can bypass the interference of industrial interference fields.
In addition to being affected by interference sources, these data carriers are also affected by high or low temperatures in many manufacturing environments. Generally speaking, the temperature range that these data carriers can withstand is -40 to +210°C. However, there are some special data carriers that can withstand temperatures outside this range.
Bener Aiden HT solution can be universal due to its small footprint and standard data carrier. The same read-write head can read and write HT data carriers as well as “ordinary data carriers” with more attractive prices.
Utilize sensor technology to provide better functions
Compared with barcode systems that can only be scanned and outdated radio frequency identification (RFID) systems (which are still using read heads from the “read-only data” era), the new radio frequency identification systems can read and write data at the same time. “Reader” means “read” and “write” together. In industrial applications, people have adopted a standard encapsulated design in the field of sensor technology. After years of development, the technology is now very mature. These sensors can be well integrated into the communication environment. Every technician knows how to install, and all accessories are readily available.
During the installation process, you must consider some restrictive factors. These restrictive factors are similar to the restrictive factors when using inductive sensors, such as flushing, necessary wiping, or no flushing to avoid interference between sensors. The opening and closing function of the dedicated switch is also very helpful, so that the two read-write heads do not affect each other. The interaction problem between the data carrier and the read/write head, or the problem of “achievable distance, speed, and data quantity”, is a crucial problem encountered by many users.
Since these parameters are well known to users, the first problem you encounter is this problem. The setting of variables (such as: “recommended reading and writing distance: 40mm” or “data transfer: 2kbps”, etc.) will only be useful when performing complex calculations, because each type of data carrier and reading and writing are used for complex calculations The combination of the heads will produce different variables. At this time, the simulation is very useful. For example, the Bener Aiden configurator will automatically complete the communication calculation, and then the user can appropriately modify the application variables to meet their own application needs.
Direct connection to higher level controller through interface module
The interaction between the data carrier and the transceiver is one of the most basic elements of all radio frequency identification systems. However, when connected to the control system, some troubles will come unexpectedly. These troubles are sometimes manifested as poor communication channels, so the number of responses and application speed will be reduced, leading to unnecessary increase in manufacturing costs.
BL-ident relies on separation technology for asynchronous processing of individual needs. Correspondingly, the read and write requests independently stored in the data carrier in a physical form can be stored in an element called “air interface” in the interface module transceiver. Once the data carrier enters the “air interface”, the data on the carrier will be processed immediately.
For details, please contact our company. Phone: +86 (10) 62029007
This article is the author’s original submission. The copyright of the article belongs to the author. If you want to reprint it, you must obtain the author’s consent. thanks!
[ad_2]