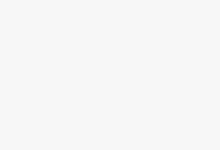
RFID-based production line management system solution
[ad_1]
1. Project background
With the globalization of the economy, traditional intensive processing and manufacturing industries, such as clothing, electronics and other industries, have higher and higher single-product manufacturing costs and lower and lower processing profits. In order to improve the overall profitability of the enterprise and optimize enterprise management Process, through information transformation to improve production efficiency has become one of the effective means.
In the production process of traditional manufacturing enterprises, most of the production modes are based on the one-piece production mode. The biggest disadvantage of this production line mode is that there is usually a large backlog of semi-manufactured products in certain bottleneck processes. If the process is complicated and With more production links, this phenomenon will become more serious. These problems have weakened the management staff’s ability to predict, control and respond to the production cycle, and it has become increasingly difficult to cope with the market requirements of large orders and short delivery times.
2. System introduction
The production line management system based on RFID technology has become one of the effective solutions to the above problems. By adopting RFID technology, the system can automatically collect production data and equipment status data, provide production managers with “real-time data” of all process links in the production line, and can Combining the process characteristics of each process equipment and related process and quality index parameters, conduct online monitoring and analysis of production information such as process parameters and equipment operating parameters of important links in production, helping enterprises to realize the measurement of semi-finished and finished processes in the production process , The automation and information integration of warehousing and exit management, so as to achieve automatic real-time tracking of production operations, can effectively supervise each production post, and supervise the stability of product quality and the implementation rate of process parameters.
The RFID production line management system uses electronic work tickets instead of traditional paper work tickets, uses an RFID tag for each single product on the production line, and installs an RFID data collection terminal at each station. When a worker completes a job, the system automatically sends the information of the workpiece directly to the computer system through the RFID collection device, and the system automatically completes piece rate calculations and various production statistics, providing a complete solution for the enterprise.
Third, the overall system architecture
The RFID production line management system is a MES project that uses RFID card swiping to complete the process flow and data collection to solve the problem of production process control. At the same time, based on the successful experience of implementing ERP and MES systems in the past, it completes the process from procurement, inventory, sales to finance The whole set of accounting information system planning realizes the organic integration of sales, purchase, inventory, production, finance, quality, cost, equipment, technology, and personnel management, and realizes the company’s comprehensive informationization and paperlessness.
Four, system process design
Taking a complete clothing production line as an example, the design process is as follows:
1) The cutting department picks materials, spreads cloth, cuts according to the production plan, and fills in the cut sheets;
2) After cutting, bundle the multi-layer garment pieces of the same part according to the rules of size, cloth layer, color, etc., and bind the binding slip entered and printed out according to the cut sheets on each bundle of garment pieces. The binding slip records the The attributes of garment pieces, such as style number, size, color, batch, cutting bed number, and information such as process number, tie number and number of pieces;
The function of the binding sheet is to indicate the attributes of the garment pieces, the batch to be cut, indicate the processing procedures that need to be performed for the garment piece and the number of products in this batch, and record the workload information of each station.
3) The sewing workshop goes to the cutting department to pick up the bundled pieces, bundle the pieces of the same bundle number together according to the production process, and deliver them to the corresponding workstations by hand;
Workers rely entirely on the information on the bundle to perform production operations to ensure that each piece of clothing is sewn from the same attributes in accordance with the planned process.
4) After the worker at the station receives the garment piece, perform the operation of the specified process. After the operation is completed, sign the job number on the stub of the tie, and cut off a piece of the tie (called the fly) as the calculation piece. Proof of salary;
5) The tie-up worker collects the semi-finished products completed in the previous process, bundles them with other parts of the same tie number, and manually transfers to the next process;
6) Repeat steps 4 and 5 until all procedures are completed, and the finished products are packaged and stored.
Five, system characteristics
1) Strong controllability, can accurately plan the allowable range of data collection;
2) The content of the label can be read and written, and can be reused, saving costs;
3) Provide automated means for information systems to obtain real-time data;
4) Realize fine production and on-time production;
5) Optimize the production process, improve production and management efficiency;
6) Cost saving;
7) Analysis of production bottlenecks and alarms;
8) High real-time, safe and stable;
9) Realize product quality traceability.
Sales Hotline: 0631-5698111
[ad_2]