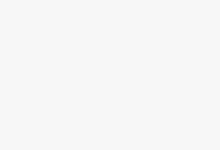
RFID home appliance production line management solution
[ad_1]
-
1. Application background
In the process of establishing and continuously improving the quality system of home appliance manufacturers, the product production line is required to have a set of clear, complete, easy-to-access and retrieve quality records. The current bar code-based production management system enables various quality analysis and control to be easily realized. The traditional bar code system has its advantages, but also has obvious disadvantages, such as easy contamination, breakage, and the need to stop waiting for scanning one by one. The batch reading efficiency is not high, and it cannot meet the needs of fast and accurate.
2. System introduction
fully useRFIDTechnology advantage, adopted in home appliance production lineRFIDTechnology, not a completely new set based onRFIDProduction management system, but willRFIDInformation is integrated with the existing bar code-based production management system to integrateRFIDThe application is organically incorporated into the overall structure of enterprise informatization.
useRFID, Barcodes, sensors collect real-time data on the production line, and transmit the read data to the upper equipment (controller, computer) through the network (wired or wireless).To manage loose sensors requires a brand-new management mechanism that can automatically discover and organize the network, deployRFIDReaders, and establish reader network connections at the same time to solve the problems of planning, optimization and control of the reader network.On the itemRFIDLabel, cooperate with the networkRFIDReader, every recognition means tracking of items.
not only,RFIDThe system can also provide a variety of applications and services, including: Production line status monitoring, employee behavior monitoring, production management, quality management and tracking, material management, job scheduling, on-site operation guidance, real-time upload of production data.
The entire network architecture must provide the function of information tracking. According to the identification code of the product, all the information of the product and the information of each flow point can be listed. In order to ensure that the tracking information is complete and the information chain can be queried in real time, the information chain backup function is provided, so that the tracking information can be found even if there is a little interruption.
RFIDApplication system includesRFIDapplication server,RFIDData server,RFIDcomputer,RFIDIt is composed of reading and writing equipment, and the electronic tag is associated with the home appliances in the production line. As the home appliance production process proceeds, the data in the electronic tags are updated at any time. The home appliance production line is shown in the figure.
620)this.style.width=620;” border=0>
Three, the function of each module of the system
1, Some modules of data collection
■ Manual data collection: Provide a means of direct manual intervention.
■ Electronic tag reading and writing data middleware: Mainly responsible for the read and write operations of electronic label data to ensure the correctness and integrity of the data.
■ Electronic label data driver software: Mainly responsible forRFIDData collection, sorting and sorting.
2, Some modules of data processing software
■ System exception handling: Main treatmentRFIDAbnormal conditions that may occur during system operation, such asRFIDHandling of abnormal conditions such as abnormal reading and writing of equipment and errors in data reading and writing.
■ Information Integration Platform: RFIDThe information integration platform is responsible for the internal information interaction in the workshop, the information interaction between the workshop and the information interaction between the enterprise and the service registry, so thatRFIDThe information can be applied within the scope of the enterprise.
■ RFIDCoding system: According to the home appliance production system, give a suitableRFIDApply item coding system.
3, Some modules used by data
■ Online setting software: The online setting function is used to complete the preparation work of the system before starting operation, mainly including the station (station) setting. It is based on the basic process information and needs the support of “system maintenance” information. Its main function is to arrange work tower. The user of the online setting function is mainly the administrator of the production line. He makes the above settings according to the released production plan and prepares for online. After it is ready, the system enters the standby state, waiting for the material to be officially launched.
■ Run schedule: The operation scheduling function is the core of the correct and efficient operation of the system.The operation scheduling function mainly includes the following functions: Control material movement, priority scheduling, production synchronization, etc. The operation control function is the background function of the system, and there is no specific user type.
■ Production monitoring: The production monitoring function is provided to general users, enterprise managers, leaders, etc., to keep abreast of the production progress in a timely manner. It mainly includes real-time monitoring of order execution, real-time monitoring of process production, and real-time monitoring of station (set) production. These real-time monitoring functions provide users with overall or partial production execution information, so that users can adjust production in time according to actual conditions.
[ad_2]