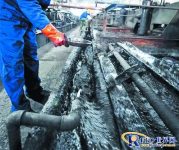
Talking about the application of RFID in the steel industry from the innovative model of Shougang
[ad_1]
In recent years, the informatization process of the metallurgical and iron and steel industries is gradually developing towards core technologies. Only relying on introduction and imitation will not make a difference. Only continuous independent innovation is the driving force for the informatization of iron and steel enterprises. The proposal of the integration of industrialization and industrialization has pointed out the development path for the intelligentization and informatization of iron and steel enterprises. In the next step, if Chinese iron and steel enterprises want to achieve steady and sustainable development, what should they focus on in the application of intelligentization and informatization? where? Perhaps Shougang Group’s exploration and innovation model in this regard can bring some enlightenment to the steel industry.
As Guo Yuchun, director of the Shougang Automation Research Institute, said, on the way for enterprises to explore the development model of independent innovation, enterprises need to have the sensitivity to assess the situation and dare to apply new technologies. “In the post-ERP era,” Guo Yuchun said, “The basic process has been determined, so how should process management and production process optimization be carried out? The Internet of Things can effectively solve this problem.” In the production process, Shougang has adopted the “one package to the end” process, saving more than 20,000 tons of raw coal each year, and the application of the Internet of Things in it has begun to take shape.
As we all know, since 2001, my country’s large steel conglomerates have successively carried out comprehensive informatization selection or construction, covering the construction of hardware network platforms, enterprise resource planning (ERP), manufacturing execution systems (MES), and enterprise quality systems. , Basic automation and process automation transformation, etc. Through the implementation of informatization, the enterprise has built a relatively complete enterprise management information platform and established a system application framework for the sustainable development of the enterprise.
However, due to my country’s national conditions, combined with the actual situation of the steel industry and the actual situation of the enterprise, various resistances and difficulties have been encountered in the construction of informatization, and the implementation effect is not as ideal as expected. These are mainly manifested in the disconnection between the management software and the enterprise’s basic logistics information collection, which makes it impossible to establish an integrated and unified information application platform during the enterprise informatization process. Only some modules have been practically applied locally. With the vigorous development of RFID technology and its market in recent years, like Shougang, more and more steel companies have accelerated the application of RFID automation and intelligent construction.
So what are the applications of RFID in the management, production, warehousing, and transportation processes of steel companies? Combining Shougang’s experience in the application of the Internet of Things and further orientation discussion, Shenzhen Yixintong Software Co., Ltd. believes that the Internet of Things will show its talents in the following aspects:
Carry out production automation control
In the production process of a steel plant, the automatic positioning control of the production locomotive or equipment is very important. The various technologies used in the previous control schemes have the disadvantages of being greatly affected by the environment and the surface of the object, the distance to read the data is limited, or the cost and operating cost are high. The RFID technology has strong adaptability to the environment, and can resist interference from dust, oil, vibration or obstructions, and achieve all-weather work. In addition, there are many data that can be stored in the electronic tag, the data reading distance is long, and the data reading accuracy is high. These technical characteristics enable RFID technology to be well applied in the automatic control of the production process, and truly realize the goal of an intelligent factory.
For example: In the automatic control system of the three major coking locomotives of a steel plant, the electronic tag with the heat number information is installed on the key position of the track of the coke pushing car, the coke blocking car, and the coal loading car. When the reader is installed When the coke pushing truck, coke blocking truck, and coal filling truck pass these tags, the data in the tags can be read and uploaded to the main control computer. The main control computer then accurately controls the running state of the locomotive based on these data. Since the implementation of the system, the degree of automation of coking production has been greatly improved, human operation errors have been avoided, and labor productivity has been improved.
Production information management for the entire product line
Place electronic tags on the surface of some products (such as blooms and round steel bars), which can read the information and data of each process of the product on the production line, and convert the information into a data format that can be recognized by the computer and provide it to Monitoring platform to realize automatic tracking management of products on the production line. The RFID system basically does not require human involvement in the whole work process, and the system has a high degree of automation. The electronic tag can be read and written repeatedly for more than 100,000 times, so it can save a lot of manpower and material resources.
Material tracking and production process tracking
Material tracking and production process tracking are one of the application points of the Internet of Things represented by RFID technology. Steel companies can continuously improve and optimize the supply chain management system by applying RFID to raw material procurement, inventory, sales and other fields, which can not only improve the efficiency of the supply chain, but also effectively reduce costs for the company and enhance its competitive advantage in the market.
Since iron and steel enterprises have many difficulties in the production and transportation process, the high temperature of molten iron requires extremely high environmental and electronic equipment is one of the more prominent problems, which not only easily causes heat loss, but also increases costs and reduces efficiency. Based on the special requirements of the steel industry for RFID technology, Shougang has successfully used RFID technology to track the ladle, that is, the “one package to the end” process. The process is to process the molten iron produced by the blast furnace through RFID tracking and distance measurement, and directly transfer the molten iron smelting method to the converter smelting in a production organization mode without changing the molten iron ladle. Compared with the torpedo tanker hot metal transportation method commonly used by iron and steel enterprises, this technology has obvious advantages in low carbon and environmental protection. It is the initial application of the Internet of Things in the production process control of iron and steel enterprises.
Equipment status monitoring
The iron and steel industry is an equipment-intensive industry. The key parameters of each equipment need to be collected. Only by grasping the status of the equipment in advance can the production process proceed smoothly. Therefore, in order to realize the optimization of the production process and process of iron and steel enterprises, the operating status of the equipment can be grasped through the RFID system.
For example, the cause of product quality defects can be found by analyzing the status of monitoring equipment. Therefore, the use of RFID technology to collect accurate data during the production process can help improve product performance and conduct effective product quality monitoring.
Environmental monitoring
RFID technology can be applied to real-time monitoring of various pollution sources and key indicators of pollution control during the production process of iron and steel enterprises (such as the monitoring of unsafe gas leakage, etc.). Through RFID technology, not only can the equipment in operation be shut down remotely , Can also prevent the occurrence of sudden accidents.
Energy system monitoring
The use of RFID technology can effectively allocate and dispatch water, electricity, gas and other energy sources, improve efficiency, and reduce energy consumption and costs. Since iron and steel enterprises belong to a high energy consumption industry, they will use a lot of energy in the production process. The use of RFID technology to build an advanced energy management center system (EMS for short) is an integrated management and control system based on automation and information technology. With the help of software technology, it can realize dynamic monitoring and management of energy production, transmission and distribution and consumption information, and improve And optimize the energy balance, achieve energy saving and consumption reduction and improve environmental quality.
Mine safety monitoring
Real-time tracking through RFID, the status of mining equipment, personnel, and the environment can be reflected in the system in real time, predict potential safety hazards in advance, improve safety management measures in mining, and at the same time improve the rational exploitation of mining resources and effectively prevent Random excavation is carried out to ensure the utilization rate of mine resources.
In addition to the above, as with the application of RFID in other fields, the application of RFID in the iron and steel industry will also cover personnel management, RFID access control management, factory material tracking, warehousing and logistics, and intelligent weighing in iron and steel enterprises. According to relevant sources of Shougang Automation Technology Co., Ltd., Shougang has successively launched applications in these fields since 2009, and has achieved great success, which fully shows that the Internet of Things with RFID technology is increasingly being affected by the steel industry. The “new favorites” of all walks of life in the industry provide a good intelligent technology platform for the manufacturing industry to usher in a new round of development, and realize the call of the country’s scientific development concept.
Shenzhen Yixintong Software Co., Ltd., as a professional RFID solution and product supplier, has long been committed to the promotion and application of RFID technology-based manufacturing execution system solutions, and successfully implemented the Shenhua Guohuataishan Power Plant The RFID production management project has been well praised by customers. With the widespread application of the Internet of Things and RFID technology, Yixintong people have been fully prepared to provide high-quality and reliable services for the intelligent upgrade of iron and steel enterprises by virtue of their own innovative technology research and development advantages.
Zheng Qiusheng
Shenzhen Yixintong Software Co., Ltd.
Phone: 0755-26710568
Mobile phone: 186-755-20227
Fax: 0755-26711002
Q Q: 541569768
Mail:
[email protected]
website:
www.onerfid.com.cn
[ad_2]