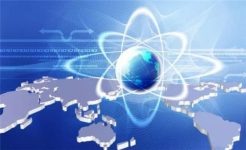
The overall solution of MES system in the electronics industry
[ad_1]
The solution of MES system
The MES solution provides enterprises with an effective way of transparent management of the production process, and makes up for the defect that ERP or MRP focuses on the management and control of the plan and cannot monitor the execution of the manufacturing site. Through the transmission of information, the entire process from the issuance of the production order to the completion of the product is compensated. Optimal management of the production process.
Through the use of barcode scanning technology, digital connection terminals, device chip storage, RFID and other automated data collection methods, the implementation of the acquisition of quality information in the production site, materials and manufacturing processes. Establish an integrated production site control and quality management platform and a complete production process database to meet the enterprise’s real-time monitoring and comprehensive traceability requirements of the production process. Through quality management and after-sales service, it can help the company to continuously improve product quality, so as to achieve corporate sustainability. The need to improve customer satisfaction.

Features of Micro Associated MES
The Weida MES-E manufacturing execution system is developed by Beijing Weida Software Zhibo Technology Co., Ltd. on the basis of many years of enterprise information construction experience and ERP system implementation experience, using advanced bar code technology and combining with the actual needs of users. A set of production line control system.
Micro-association MES-E manufacturing execution system is the leading MES tool for global production and process optimization in the electronics industry. It provides flexible standard components and flexible customization to complete basic functions, and can provide a customized open platform for the special needs of individual systems. All components comply with the ISA standard S-95 (ISA is the abbreviation of the Automation Industry Standardization Organization). Because of their modular structure, these components can not only communicate with the ERP system but also with other manufacturers’ applications using their standardized interfaces Program communication.
The Weida MES-E manufacturing execution system is based on the actual operation process and management mode of a large number of electronic assembly companies, and is fully integrated into the management methods of modern enterprise informatization, using bar code technology, RFID, wireless local area network, GPRS and ERP, MES and other technical means , Realize the timely collection of factory data and process control, and achieve the timely interaction of all information of factory personnel, equipment, materials, tools, products, processes, etc., providing the most advanced means for establishing a digital factory and a transparent information factory.
The Weida MES-E manufacturing execution system is based on a large number of network hardware equipment and barcode scanning equipment. The normal operation of these equipment ensures the stability of the system and is a prerequisite for the safe, efficient and stable operation of the production workshop management system. The main hardware equipment includes: Servers, barcode printers, barcode scanners, data collectors, barcode labels and consumables, billboards, etc.
The manufacturing execution solution of Weida Software fully integrates the MES-E-ERP system of Weida Software and the production line code acquisition system, and designs interfaces that integrate with other related information systems, such as ERP, MRP, CRM, etc., and SAP, ORACLE Mainstream ERP systems such as Yonyou and Yonyou have successful integration experience.

System function design
1. Data collection and product traceability:
Collect key materials, test results, test data, maintenance status, random inspection status, heavy industry status and other information through a variety of methods for the full traceability of the product. The collection methods are: terminal collection, such as DCT, DCN; PC collection; data files Manually import, the collected data includes: work order attribution information; work order separation information; IQC information; material preparation information; loading information; cutting information; good/bad product information; test data information; maintenance status information; heavy industry status information; Serial number conversion information; software version information; packaging information; aging information; warehousing information; shipping information, etc.
2. The process is foolproof and error-proof:
Through the establishment of the production model, it can control unauthorized operations, feeding errors, site errors, abnormal information alarms, etc. during the production process. Including: authorization information verification, shift personnel verification, barcode rule verification, operation process verification, material information verification, integrity verification, usability verification, existence verification, conflict verification, production status verification, compatibility verification, etc.;
3. SMT patch loading:
Carry out SMT loading error prevention, material shortage warning, material tracking, material inventory, steel plate control, solder paste control, feeder control, and MSD component control.
For companies with SMT equipment, after implementing data collection, product traceability, and process foolproofing, the SMT function will be a key consideration.
4. Production progress monitoring and early warning reminder:
Monitor the completion of work orders and evaluate whether there is an impact on customer orders. When the customer inserts the order, it can help evaluate the delivery date. Real-time monitoring of key indicators, warnings through Mail, SMS, Kanban, etc. when abnormalities occur, changing passive management to active management, including: Cpk indicators, bad parts indicators, defect indicators, through rate indicator early warning, etc.;
5. Workshop Kanban management:
Real-time monitoring of the output of each production line, real-time monitoring of the through rate of each production line, and real-time monitoring of the distribution of defects in each production line;
6. Output analysis:
According to the seven dimensions of machine type, product, work order, section, production line, process, and equipment, according to different time types, such as time period, shift, day, week, and month, analyze the transition of input and output and the status of different objects Compare the situation in order to track down the problem and improve the direction. If it is found that the same product is produced on two lines, and the output of one of the production lines is more than that of the other production line, then the analysis of the reasons for the high-efficiency production line becomes the focus, find out the outstanding places, and then promote it.
7. Yield rate analysis:
According to the seven dimensions of machine type, product, work order, section, production line, process, and equipment, analyze the progress of defective rate, through rate and M according to different time types, such as time period, shift, day, week, and month Compare the situation with different objects in order to track down the problem and improve the direction. If differences are found, then the points of difference will become the focus of analysis, identify outstanding areas, and then promote them.
8. Qualified rate of one-time delivery:
Whether the effective output of the production line is high depends mainly on the pass rate of one-time inspection. Effective output refers to the good products that can be sold to customers, and these products can be used for profit by the manufacturing company. The low pass rate of one-time delivery means that the rework of the production line will increase, and more energy will be spent on repairing the leakage of existing products, rather than on the output of new products. This will result in high cost input, but only Lower output. Therefore, the pass rate of one-time verification often becomes the focus of quality control.
9. Analysis of repair defects:
Quickly find out the defects that need to be focused on improvement based on the principle of Plato, and find out effective improvement measures based on the cross-analysis of the defect and the cause of the defect, the defect and the solution, the defect and the position, the defect and the responsible department; the sales of the finished product after leaving the factory Effectively manage quality-related issues in the service process, realize the root cause traceability of quality issues in the after-sales service process, and implement quality management throughout the entire life cycle of the product.
10. Work in progress query:
Real-time monitoring of the work-in-process status of the production line to help identify bottlenecks in the production line. At the same time, because of the electronic work-in-process data, the data transfer can be completed quickly when shifting shifts, shortening the shifting time and improving the efficiency of production preparation.
11. Data interface:
This system can be seamlessly integrated with mainstream ERP systems such as SAP, ORACLE, UFIDA, Jindie, etc. It can also provide secondary development according to user needs to meet the needs of personalized management for growing enterprises.
12. System permissions:
System user management, authority management, log management, system settings, announcements and notifications, online short messages, data backup and recovery, password modification, ERP interface, LED interface and other functional modules.
Implementation benefits and value
(1) Through the barcode technology to track the product from production, inventory, sales and after-sales service process, open up the entire process of product from production to sales, after-sales service, to achieve the unity of logistics, information flow, and capital flow.
(2) Change the original manual entry process to achieve accurate, timely, and fast data collection, avoid human input errors, and more importantly, enable field production personnel to concentrate on business operations and improve work efficiency.
(3) After-sales and claim settlement data are collected accurately and processed in a timely manner, which reduces the workload of claims settlement, simplifies settlement procedures, and shortens the settlement time, thereby improving the entire claims settlement work and better providing customers with satisfactory services.
(4) The product traceability link makes the product clear and transparent during the entire processing, delivery and sales process, quickly discovers the cause of quality problems, and formulates targeted measures to solve quality bottlenecks and reduce quality costs.
(5) Through the bar code association in the procurement, sales, and production process, it provides a basic data source for product production process traceability and after-sale traceability; at the same time, it can check whether it is fake or shoddy products and skewed products.
(6) Real-time recording and monitoring of the completion of processing tasks in each process of the production line, personnel work, labor productivity, equipment utilization, product qualification rate, rejects, etc., through the system’s comprehensive statistical information query function, timely discover problems in the implementation process.
*Improve production efficiency, improve planning and scheduling
*Optimize resource utilization, reduce downtime and increase output
*Enhance visibility of factories and production processes
*Improve the real-time response ability to abnormal events in the factory
*Improve material circulation performance and provide comprehensive product tracking and tracing
*Improve interaction between operators and standardize operating procedures
*Accurately calculate key performance indicators, analyze and optimize processes
[ad_2]