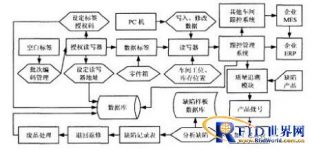
Work in progress RFID tracking system
[ad_1]
Chapter 1. Background analysis
1.1. Project background
along withInternet of ThingsWith the rise of technology, the domestic manufacturing industry generally recognizes that through the Internet of Things and other technologies combined with enterprise information MES and other management systems, through the Internet of Things wireless sensor network, RFID tags and other technical means, real-time process tracking and data collection of the manufacturing assembly line production process are realized. , So as to improve the visualization and controllability of the manufacturing process in the workshop, and increase the production efficiency of the enterprise. The visualization and controllability of the production process is an important reference factor for the formulation of production plans and the on-time delivery of products. The realization of the important role played by the digitization of production management, visualization and control of the production process has brought considerable economic benefits to the enterprise.
Sany Heavy is one of the world’s top 50 construction machinery manufacturers, the world’s largest concrete machinery manufacturer, the top 500 Chinese companies, the most comprehensive and competitive company in the construction machinery industry, the Forbes “Top Enterprise in China”, and the most independent growth in China Brand, the most competitive brand in China, the iconic brand in China’s construction machinery industry, and the top 500 Asian brands. Introduced advanced foreign management ideas and methods, and developed information management systems such as SAP and MES. These systems have now played an important role in product manufacturing management and have brought huge economic benefits to the enterprise.
At present, Sany Heavy Industry has built 8 major industrial parks covering the country, and is actively adopting advanced digital technology to improve the efficiency of Sany Heavy Industry in all aspects of production and manufacturing. This case is to use Internet of Things and other technologies to collect key processes/stations. Information, to achieve immediate reporting to the body company’s three major processes (welding, painting, and final assembly) production lines.
1.2. Current situation analysis
my country’s traditional manufacturing industry generally has problems such as weak informatization foundation and low production efficiency. Therefore, the implementation of informatization in the manufacturing industry, especially the traditional manufacturing industry, is an urgent task that needs to be solved. How to collect and manage workshop-level production information to achieve the effect of “pre-predictive planning, in-process analysis and control, and post-track management” for production has become one of the directions of manufacturing informatization.
At present, the monitoring of the production process of Sany Heavy Industry Hunan Automobile Manufacturing Co., Ltd. is still through the management personnel to the workshop site to understand the situation, and then manually input the data to record and statistics to form the workshop report. The workload is large and the efficiency is low, and it is impossible to track the work in process in real time. Processing status, data cannot be shared. The following problems exist:
When the process is changed (up/down), the process information of the work-in-process among the three major processes is not tightly coupled.
The tracking of the current work position and work step of the work-in-process cannot be done in a full, timely and automated manner.
It is impossible to grasp the actual working hours of various products in real time and accurately, which restricts the effectiveness of planning and scheduling, and at the same time, it is impossible to carry out value engineering.
Due to the non-real-time tracking of the production process and assembly process of the work-in-process, the timeliness of job scheduling and on-line material distribution is poor. At the same time, it also restricts the complete inspection of assembly materials, which in turn affects the production and distribution efficiency of warehouses, supporting manufacturers and the supply chain, and restricts the JIT production model.
Poor traceability, lack of tracking and tracing of the genealogy of the entire vehicle, including information such as assembly time, operating workers, working hours, assembly parts, etc., affects the efficiency and quality of quality control and after-sales service.
The collection of important information requires workers to scan codes manually, which is relatively inefficient. In addition, the barcode is easily affected by oil stains during use, and it is easy to fall off and the information cannot be read. For critical parts with special geometric features, barcode scanning is inconvenient.
The assembly of key parts and the host is prone to misassembly, and matching verification cannot be performed before assembly, and there is a lack of corresponding early warning mechanisms and effective solutions.
Reporting work through the MES terminal requires resolution of screensavers and identity verification, which often results in reporting for multiple products at once, resulting in a backlog of job reporting tasks and delays in reporting jobs.
The non-real-time tracking of the production process prevents planners from grasping the completion of the production plan in a timely and accurate manner.
1.3. System function goals
This project intends to adoptRadio Frequency Identification (RFID) TechnologyTo realize the real-time tracking and automatic reporting of work in the whole process of the work-in-progress. Through the implementation of this project, the following goals can be achieved:
1. Real-time status tracking of the whole process of work-in-progress. Accurately understand the location and status information of the work-in-progress.
2. Integrate with MES and PLC to realize the seamless coupling of information when converting between the three major processes of the product.
3. Provide data support for the 3D operation guidance and logistics of the assembly line.
4. By using the reader to trigger the reporting method in real time, the reporting time can be reduced and the reporting accuracy can be improved.
5. Through the tracking and real-time monitoring of the production process of the work-in-process in the assembly line, understand the processing and assembly process of the work-in-process, reduce the abnormal processing time, and improve the on-time completion rate and delivery rate.
6. Tracking management of the genealogy of the work-in-progress (historical processing/source information of the entire vehicle and its components) is convenient for quality traceability.
7. Integrate the collected production process information with SAP, MES and other business systems to drive the efficient and high-quality operation of business modules such as material management, distribution management, production scheduling, planning and scheduling, quality control, and after-sales service.
8. RFID collection equipment can adapt to the complex working environment on site.
1.4. Expected effect
The expected effects achieved by the system implementation include:
Use automatic identification and data collection methods such as RFID to replace manual processing of information to improve management efficiency and enhance the enterprise’s resilience;
The information system will be extended to the bottom of automation. Input a large amount of real-time data from the bottom layer to the system through RFID, which makes the information system inevitably expand to the bottom layer automation and improve the flexibility of the assembly process;
Bridging the gap between planning and execution time in the enterprise’s production system. Information systems that apply RFID and other automatic identification and data collection methods can obtain real-time production data in a timely manner, realize automatic tracking of products in the whole process, and seamlessly integrate data and applications through network information transmission channels to provide decision-making support for enterprise management , It bridges the gap between plan issuance and production execution, reducing the blindness of plan;
The concept of safety stock and manufacturing lot size changes. The application of RFID in factories and warehouses will make the incoming materials of upstream processes (or enterprises) and the needs of downstream processes (or enterprises) completely transparent, thereby realizing just-in-time (JIT) and mass customization (MC) production methods.
Chapter Two, System Scheme
2.1. The overall structure of the system
The overall structure diagram of the system scheme is shown as in Fig. 1. The whole system is roughly divided into three parts: management execution layer, data communication layer and data acquisition layer.
1. Production Executive
The data collection layer is composed of two parts: the device terminal and the data collection system, including physical devices such as RFID handheld devices, high-temperature/corrosion-resistant RFID electronic tags, and so on.
Mainly related to the final assembly, electrophoresis and other workstations used for the production of products in process. The production execution layer completes the underlying data collection, data transmission, data submission and production guidance.
RFIDReader: The reader is the core component of the RFID data acquisition system, which mainly completes the collection and data interaction of electronic tag data.
RFID electronic tags: The choice of RFID electronic tags should be determined according to the actual characteristics of the products on the car body. In this case, a specific high temperature resistant metal label is used to ensure that it can work normally under the conditions of this case.
The entire system structure is composed of data acquisition, network transmission, and system operations.
On-site information display: On-site information can be displayed through MES terminals, electronic billboards and other equipment to realize the generation and management of spare parts batch numbers, as well as online real-time query and display of production plans, production processes, production status information, production equipment information, and quality analysis information. Input, realize the paperless operation in the workshop.
RFID tag card issuing equipment: the card issuer receives and executes write instructions from the control computer. According to the record of a production process, the label is then hung or installed on the production equipment.
2. Data communication layer
The data communication layer is the middle part that connects the management control layer and the production execution layer, and realizes the data communication and information interaction between the management layer and the execution layer. The main physical devices include the corporate intranet (Intranet) and communication servers.
Enterprise intranet: In combination with the existing network environment of the enterprise’s production workshop, the data communication layer realizes the connection between the management layer and the executive layer through Gigabit Ethernet, and realizes the data transmission and information communication between the two based on the TCP/IP protocol.
3. Management and monitoring layer
The management and monitoring layer mainly completes a series of processes from middleware to production management and scheduling and data storage, and responds to the command request of the data terminal transmitted from the bottom layer, or the instruction sent by the middleware to the bottom data terminal. The management control layer includes three parts: database server, management server and upper management computer:
Middleware technology: Middleware refers to software modules that provide program management, data filtering and collection, event management, security management, and network management between the front-end data collection system and back-end database and management and monitoring system.
The middleware provides a two-way transparent interface, precise control of the underlying equipment and real-time data collection, and provides the required underlying data for the upper application software and database, so that the upper application software shields the complexity and diversity of the underlying hardware. Software that realizes the same function more conveniently under different hardware environments.
Database server: It mainly stores real-time data collected by the production execution layer for real-time monitoring of the entire production status.
Management server: It mainly stores all kinds of information required for the production management of the enterprise, which is used for the daily management of production and the overall planning and decision-making management of the enterprise;
The data server and the management server are connected to the local area network through the network interface.
Upper management computer: It is a comprehensive platform used by production managers for production management, mainly used for real-time monitoring of production status and issuing production instructions.
System software architecture
2.2. System business model design
This system is used in the 18 workstation areas of the final assembly, and realizes real-time monitoring of the production progress of the workshop through scanning and reporting.
Business process description:
1. Before the system goes online, the RFID tag card is issued at the card-issuing workstation, and basic information such as the order number, specification model, and manufacturing process of the work-in-process is written in the label. The WIP label goes with the car.
2. After the product arrives at a certain station, read the product arrival time through a fixed reader, and start to check the accessories information, including the number of accessories and specifications and models. At the same time, the reader writes the operating information of the current station into the work-in-process tag, including assembly worker information, starting time, reporting time, etc., and transmits relevant information to business systems such as MES and SAP;
3. During the installation process on the products or parts, if you encounter problems with accessories, equipment failures, etc., feedback to the designated personnel through the station button, and the red light will be on; until the problem is solved.
4. The system automatically reports work. When all the work of the current station is completed, the following methods can be used to report for work:
(1). Confirm the job report with one key through the industrial control button.
(2), button to report work. Click the station confirmation button and the system confirms the completion of this process.
(3) MES terminal report for work. Identity verification, remove the screen saver, and report to work for confirmation.
2.3. Key technologies and advantages of the program
In this plan, the key technologies/products and difficulties involved include the following aspects:
IoT integrated management platform:
Quick customization, adapting to various industry application systems through interface scripts;
Support mainstream RFID reader products, provide Http, Soap, JMS and other protocol support for the upper layer, and provide Web Service interface;
Provide monitoring, configuration and management of RFID readers.
Provide a flexible and expandable framework, support the upgrade of the ALE specification and quickly integrate new RFID readers;
Mount the label precise positioning module, support high-precision label positioning;
Provide automatic label data generation module;
Provide enterprise-level operation quality, stable, efficient, safe, manageable, and scalable.
Distributed reader technology:
Support low-cost large-scale incremental networking;
Ultra-large-capacity reader unit, more than 50 times more than traditional;
Flexible networking model combining wired and wireless;
The reader control unit can be independently deployed in the core computer room for centralized maintenance;
The control unit supports hardware upgrades;
A single reader can control more than 2000 RF nodes;
The coverage can be dispersed through the Internet.
Continuous, accurate, real-time radio frequency positioning technology:
Tracking the value target can determine the subtle activities within the coverage area;
Low-power design, optimized active tag collision algorithm saves half power;
Precise positioning, the world’s leading RF positioning algorithm;
It can automatically record the storage location of the box;
Only need to deploy a small number of positioning readers according to a specific algorithm;
Need strong algorithm research support;
RFID label packaging technology:
In the process of flip-chip packaging, along with the evolution of the bonding interface and the realization of I/O interconnection, the combined effects of force, heat, fluid, vibration, ultrasound and other multi-physical fields have become an impact on packaging reliability, efficiency, and electrical/ The main factor of mechanical connection performance. The multi-physical field action in the packaging process has the characteristics of multi-parameter time-space coupling, strong nonlinearity and uncertainty, and its action mechanism is very complicated. The high-performance and low-cost RFID packaging process relies on people’s discovery of the formation mechanism of the packaging interface under the action of heat, force, fluid and other multi-physical fields, as well as the precise operation of small objects, precise positioning based on vision guidance, high-speed and high-precision motion control, and more Breakthroughs in theoretical methods and key technologies such as on-line precision measurement of physical parameters and coupling control, optical-mechanical-electrical integration design, etc.
One of the core difficulties in this case is the design of RFID tags that are resistant to high temperature, corrosion, and electrical pulses. The tag design needs to meet the following key indicators:
High temperature resistance: working temperature (-200C~800C), storage temperature (-200C~2400C), continuous temperature 60′.
Corrosion resistance: acid-base strength is 3≤PH≤12
Resistance to electric field: It is mainly to be able to move or store in the electric field, the performance of the RFID tag is not destroyed by the intensity of the electric field.
Industrial grade: It can work in environments such as dust, humidity, oil, coolant, dust, harmful gases, etc., and meets the requirements of IP66 protection type, namely dustproof and waterproof.
[ad_2]