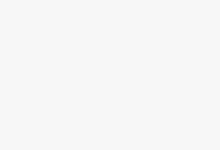
RFID technology-based implantable medical device asset warehouse management system
[ad_1]
The inventory management of implantable medical devices has always been the job of hospital procurement managers. However, the entire link also involves other important functions and financial departments, including suppliers, surgeons and nurses, and procurement.
Ourense General Hospital in Spain has passed theoretical certification and believes thatRFIDThe technical implantable medical device asset warehouse management system is based on two points: the development of the medical service management system and the periodic monitoring of third-party warehouses. Without these two points, the development of this application will require more complex, more urgent, and more comprehensive solutions.
RFID technology-based implantable medical device asset warehouse management system
Optimize inventory management process
After the hospital receives a product, the RFID warehouse management system enters the product information into a specific database, and at the same time assigns a unique code to each product. Minor number, serial number, etc.). Currently, there are three ways to enter data, namely: manually enter product data and variable data into the system; use a barcode reader to scan GS1-128 barcodes; and use EDI DE? SADV messages (electronic data interchange). After the data exchange is completed, the staff sends the information to the RFID department, which prints the RFID label, saves the relevant information in the label, and records it in the database, just like storing the product in a smart storage cabinet in a warehouse.
Smart storage cabinet
The smart RFID asset storage cabinet is a temporary cabinet made of stainless steel. By using RFID technology to control the products entering and exiting the cabinet, it can store more than 230 products at most. There are 6 antennas in the smart storage cabinet, and the RFID reading device manages these antennas through a multiplexer. After the RFID reader reads the personal ID, the application of the smart storage cabinet opens. After verification is completed, the storage cabinet opens. When the door is closed again, a switch activates the smart tag reader, which uses the antenna to identify the life cycle of each product.
RFID technology realizes inventory management of implantable enterprises
The obtained information is compared with the previously read information. The replacement information or moving information is recorded and saved in a temporary file of the staff who opened the storage cabinet. The file will record the time, the product being moved, etc. information. Each time the storage cabinet is closed, it updates the list of products stored in it for 30 seconds and uploads inventory information.
Surgical procedures and medical records
If a planned operation requires some equipment in the warehouse, then obtain the clinical data, use RFID to enter and record the patient’s information and medical record number in another smart tag. After the operation is completed, the smart label of the used item will be pasted on the implanted instrument table, and at the same time, the information of all the products used in the operation will be entered. This information is stored in a temporary file that will be checked against the product information recorded from the storage cabinet. When the RFID tag reading device reads, once a product is recorded, the product will be considered “consumed”, and the form that records this information will upload the information to the purchasing department.
Approved
The RFID implantable medical device asset warehouse management system runs a reconciliation and inventory system every day to read the products stored in the RFID storage cabinet to obtain accurate inventory information. Based on this information, the system approves the update of the number of products required for the next operation and the information in the table of used products and implanted devices.
After the entire process is completed, the supplier will get a list of products that need to be replenished and a list of existing inventory that will be sent to them via EDI within 24 hours. When the supplier obtains this information, the work of replenishing, invoicing, and purchasing will begin.
Tests have proved that RFID technology is feasible and can be used to solve these problems. The integration of RFID management system and technology does not require much effort to master accurate information.
[ad_2]