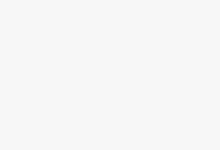
Mine locomotive monitoring and management system based on RFID/Wi-Fi technology
[ad_1]
A mine locomotive monitoring and management system based on RFID/Wi-Fi technology is proposed. Radio frequency identification technology has technical advantages such as high communication speed, strong anti-interference ability, strong confidentiality, long-distance and high-speed moving object identification, which makes it suitable for complex and harsh underground operating environments. Use WIFI wireless local area network for data transmission, save cables, and reduce the workload of line installation and maintenance. The management center database analyzes and counts the information, realizes the operation management of locomotives and T workers, and improves the efficiency of underground locomotive transportation management.
1. Principles of coal mine locomotive management system
1.1 RFID technology
RFlD radio frequency identification is a non-contact automatic identification radio frequency technology, which automatically recognizes the target object and obtains relevant data through radio frequency signals, and the identification work does not require human intervention. The RND system is mainly composed of readers, antennas and tags. The reader mainly reads electronic tag information; the antenna is responsible for transmitting radio frequency signals between the tag and the reader; the tag is composed of coupling elements and chips, and each RFID tag has a unique electronic code attached to the object to identify the target object. The main features of RFID are:
(1) RFID technology realizes fast scanning of tags and meta-barrier reading. Its reading and writing range is up to 3,600, and the reading and writing distance can reach tens of meters. It can identify electronic tags of high-speed moving objects, and it can also be taken when there are objects in the middle.
(2) RFID tags carry electronic information, which not only improves the anti-pollution and anti-destructive ability of the tag, but also greatly increases the memory capacity of r data, and the writable chip can write data multiple times, according to needs Change the information in the electronic chip.
In view of the harsh underground environment and many obstacles of mine transportation, the mine locomotive monitoring and management system uses RFID long-distance radio frequency identification technology to accurately record the information of locomotives and transportation staff T in real time, and return to the ground management center so that dispatchers can understand The dynamics of underground locomotive transportation.
1.2 Wi-Fi technology
Wi-Fi is also known as the 802.1ib standard. It uses 2.4GHz direct sequence spread spectrum. The maximum transmission rate is 54bit/s. The transmission rate can be adjusted to 5.5bit/s, 2bit/s and 1bit/s according to the signal strength. License-free on 2.4GHz and 5GHz frequency bands. Its main characteristics are: fast speed, high reliability, in an open area, the communication distance can reach 305m, it is convenient to integrate with the existing wired Ethernet network, and the cost of group mocking is lower. The networking system mainly includes wireless sites, AP nodes, and network servers. The sites and nodes can be connected in cascade or form a local area network, and the site can implement all the functions of the Hub.
In the mine locomotive monitoring and management system, WIH wireless network and TCP/IP protocol are used as the basic architecture, and the mine T industry Ethernet ring network is used as the transmission platform of the entire system, forming a combination of wired backbone and U-wire terminals, covering the mine Track area. Utilizing the technical advantages of WIFI network technology such as high transmission rate, short access time, wireless transmission, etc., it can provide real-time transmission of vehicle RFID data, quickly establish a connection, and no chain establishment delay.
2. System principle
2.1 System implementation
The system consists of vehicle/RFID tag, reader, wIn network module, industrial Ethernet and management database system.
A certain number of readers are set up in the underground parking lot, the entrance of each branch inspection road, the coal bunker, and important track sections according to the specific needs of the site. Each locomotive is equipped with a vehicle-mounted RFID tag. When the tag enters the range of the RFID read-write antenna, the tag receives the radio frequency signal from the reader, and uses the energy obtained by the induced current to send the information stored in the chip. After the RFID reader reads the information, it transmits the data to the WIFI wireless data transmission terminal through the RS485 interface, and the data passes through the wireless local area}. 4 Pass to the industrial Ethernet, and pass to the management center server via the backbone network. In this way, the database of the central station host computer can determine the specific information of the mine locomotive and the operator (such as: who it is, where to live, and the specific time) by analyzing the collected data, and it can be displayed on the large screen or computer display of the management center. Screen, and make a backup. The manager can indicate a certain area every week based on the distribution on the large screen or on the computer, and the computer will count and display the personnel in this area. The database management system of the management center automatically turns into locomotive transportation and staff operation statistics, realizing the operation management of locomotives and personnel.
2.2 System design
2.2.1 Hardware design
The hardware includes information storage, acquisition and transmission equipment, which is the basis for real-time dynamic information transmission of the underground mine to the management center to monitor and manage the locomotive.
(1) Electronic chip. The basic information of the locomotive is stored in the electronic chip, including locomotive type, serial number, maintenance record, and the name, age, gender, team, position, validity period, etc. of the corresponding locomotive staff. Install RFID electronic tags on each locomotive. Since the information in the electronic chip has to be changed according to changes in the attributes of the car and the staff, a writable chip is used in the design to facilitate the change of the data in the chip.
(2) Reader. RFID readers are installed at the underground parking lot, the entrance of each branch roadway and important road sections, and one reader is installed in the coal bunker of the mining area. A different ID number is set for each reader, and a database with an ID number matching the reader is established in the system database. After the installation is completed, the reading distance of each reader needs to be adjusted according to the mining area. The reading range of the reader is subject to 10m. Too long distance not only needs to increase the power of the reader, but also may cause multiple readers to read an electronic chip at the same time, making the positioning inaccurate.
(3) Communication module. Each reader is equipped with a WIFI wireless data transmission terminal. The staff information and locomotive information obtained by each reader are wirelessly transmitted to the underground Ethernet ring network.
The wireless transmission network is IEEE802.1lg standard, and the wireless frequency of 2.4GHz is adopted in the physical layer. In the MAC sublayer of the data link layer, the “Carrier Sense Multiple Access/Conflict Avoidance (CSMA/CA)” media access control (MAC) protocol is used.
The wired connection part adopts the IEEE802.3 standard. Because the node is both wired and wired, it needs to support 802.3. 802.3 describes the realization method of the MAC sublayer of the physical layer and the data link layer, and is used in a variety of physical media. A variety of speeds use CSMA/CD access mode, and the implementation method described in this standard for high-speed Ethernet has been expanded.
2.2.2 Software design
The locomotive information collected from the mine is calculated by computer software to realize the locomotive positioning function, the locomotive operation management function and the staff management function.
(1) Locomotive positioning. The reader collects the information that passes through the locomotive’s electronic tag at a certain time and returns the ID number together. The server finds the database that matches the ID number, determines the section to which the reader belongs, and determines the specific location of the locomotive. At the same time, in the database, establish a city to locate the reader table, record the ID number of the reader; establish a roadway node table; record the coordinate value of the node; establish a city routing table. Record the node ID and the coordinate value of the node that a reader passes through to the neighboring reader, and the system traces the movement trajectory of the underground working vehicle based on these data.
(2) Locomotive operation management. By analyzing the time when the locomotive enters and exits the coal bunker in the mining area, the server counts the number of times each locomotive has been carried in a certain shift. It can also count the times in different time periods, and can generate shift reports, monthly reports and quarterly reports based on the statistics. Determine whether the locomotive needs to be overhauled based on the locomotive’s maintenance records and overhaul years.
(3) Staff operation management. This part of the work is automatically completed by the database management system for the work management of the staff, which mainly includes: registering the entry and exit of each staff, working time information, the team of each staff, the locomotive used during work, and automatically generating attendance work statistics And reports.
3. Database management system
Mine locomotive monitoring and management database, using MicmmftVisualstudio2005 as the development platform, using Microsoft SQL Server 2000 as the database management system, using NetFramework-based component technology to improve development efficiency and make the system easy to maintain and expand. On the basis of system function analysis, the function modules of the system are set. The mine locomotive monitoring and management system database is designed as a 3-layer distributed structure. According to the needs of locomotive management in the mining area, the data management system is designed with 7 functions to enable managers to monitor the operation of underground locomotives, make decisions, and generate relevant operating statistics.
The functions of the database are as follows:
(1) Display the time when the locomotive gets in and out of the well and enters and exits the coal bunker in the mining area.
(2) Query the real-time actual position of one or more locomotives.
(3) Record a series of information such as the arrival/departure time and total detention time of the locomotive at any location, and give an alarm to the locomotive overtime.
(4) Query the occupancy of the underground track and warn the track area where conflicts may occur.
(5) Generate a statistical table of the number of locomotives carried.
(6) Establish a database for the use and maintenance of locomotives.
(7) Generate a statistical table of staff attendance and workload.
4. Conclusion
Through this system, the trajectory of each locomotive in the whole mine can be clearly understood, and the number of locomotives carried and the operations of the staff can be counted at the same time. Use WIN wireless local area network for data transmission, saving cables and reducing the workload of line maintenance. From the perspective of economic benefits, the mine locomotive monitoring and management system based on RFID/Wi-Fi technology reduces construction, maintenance and management costs, and improves the efficiency of underground transportation management. From the perspective of social benefits, the system can reflect the locomotive’s underground position in real time, facilitate the supervision and control of dispatchers, and improve the safety of underground transportation.
[ad_2]