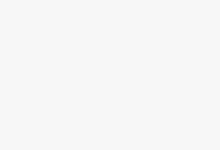
Oilfield production pressure and flow wireless monitoring system program
[ad_1]
1. Basic situation:
An oil production plant in an oil field consists of multiple oil wells, metering stations, manifold valves, transfer stations, joint stations, crude oil export systems, oil tanks, and other dispersed facilities in the oil field. Then the various facilities of the entire oil production plant work The status and data of the produced oil (mainly temperature, pressure, flow, etc.) are directly related to the stability of oil field production and the quality of crude oil. At present, most of the manual inspections of equipment operation status and measurement and statistics of oil production data are carried out daily. Due to the large number of oil wells and the distribution area of several hundred square kilometers, the labor intensity of workers will inevitably increase, and the real-time and even accuracy of equipment monitoring and oil production data will be affected. There are also hidden dangers such as clerical errors and fraud. This will result in the upper-level not being able to understand the on-site situation in time, and will not be able to formulate more effective and flexible processing plans based on the actual labor, electricity, and raw material consumption data consumed in production. Therefore, it is extremely prominent to improve the automation and informatization level of oil production plants.
With the rapid development of network information and the accumulation of production data, the traditional management methods and manual data recording mode can no longer meet the development requirements of modern enterprises. The real-time collection of production information, the networking of data statistics and query has become an effective means for modern enterprises to improve work efficiency and reduce production costs. To realize real-time collection and data analysis of on-site data and equipment information, remote command delivery, and equipment control, there is an urgent need for widely distributed on-site production data to be networked.
2. System plan:
2.1. System overview:
The oilfield production information intelligent monitoring and management system uses temperature sensors, pressure sensors, flow sensors and three-phase multi-function meters installed on the head of the pumping well to realize the detection of oil well electrical parameters and expand other parameters of the oil well, such as wellhead temperature. , Pressure, motor temperature, current curve, indicator diagram, etc., with the control functions that can be achieved on the oil well (alarm, dry pumping control, timing start-stop control, real-time energy-saving control, lack of phase load over-limit shutdown control, start-stop Remote control, etc.). Due to the large range of oil fields, the distance between monitoring points and between monitoring points and the monitoring center is very long, it is difficult to set up a wire network, even if the oil field with better conditions is to set up a wire network, the initial investment and maintenance costs are very high.So this plan adoptsGPRSThe wireless networking mode realizes the transmission of information and data between the monitoring points and between the monitoring points and the center.
The oilfield production information intelligent monitoring and management system can do effective statistics and analysis of this data. The monitoring center is usually located in the wired local area network in the factory area and is connected to the office management network. The management server of the monitoring center is responsible for the release of all data within the network. Relevant personnel of the plant management can directly log in to the server of the information center through the office local area network to perform real-time monitoring and query various report data. You can also browse the data through the Internet interface for engineers on business trips in other places.
2.2. System composition:
2.21. Data management layer (monitoring center):
The hardware mainly includes: workstation computers, servers (Telecom, China Mobile or Unicom fixed IP dedicated line or dynamic IP domain name method);
The software mainly includes: operating system software, data center software, database software, oilfield production information intelligent monitoring and management system software platform (using B/S structure, can support browsing and viewing on WAN), firewall software;
2.22 Data transmission layer (data communication network):
Use the mobile company’s GPRS network to transmit data, and the system does not need wiring to build simple, fast and stable;
The mobile GPRS wireless networking mode has the characteristics of high data transmission rate, wide signal coverage, strong real-time performance, high security, low operating cost, and low maintenance cost;
2.23. Data collection layer (front-end hardware equipment):
Complete set of remote measurement and control equipment: measurement and control terminal;
Sensing and measuring equipment: pressure sensors, temperature sensors, flow meters, three-phase multi-function meters, solenoid valves;
2.3. System topology diagram:

3. System function:
01. Collection function:
Oil well motor: three-phase voltage;
Oil well motor: three-phase current;
Oil well motor: active power;
Oil well motor: reactive power
Oil well motor: total electricity;
Oil well head: pressure value;
Oil well head: temperature value;
Oil well head: flow value;
02. Alarm function:
Power failure alarm, power parameter, pressure, temperature, flow fault alarm, measurement and control terminal alarm;
State change alarm prompt: alarm state change. If the pressure suddenly increases or decreases;
Motor overload, overvoltage, undervoltage, phase loss, phase failure, undercurrent, three-phase unbalance and other faults
03. Storage function:
Power parameters, pressure, temperature, flow information, real-time data, event records, and operation records are stored in the database;
04. Query function:
Power parameters, pressure, temperature, flow information, historical records, historical curves, event records, operation records, historical reports;
05. Statistics function:
Report function: daily report, monthly report, annual report;
Curve function: daily curve, monthly curve, annual curve;
06. Printing function:
Power parameters, pressure, temperature, flow information, historical records, historical curves, event records, operation records, reports;
07. Safety function:
Password function: a password must be entered to enter the system;
Authority function: different operators have different functions;
User switching: different operators can switch in the system when handing over;
08. Extended functions:
Power parameters, pressure, temperature, flow volume: users can add or delete sites.
Remote control: remote control: in the case of adding battery to the valve, it can output the remote control valve or the opening of the motor;
09. Setting function:
Site information entry and modification;
Collection cycle setting and modification;
10. Remote maintenance function:
Remotely set the working parameters of the site (electricity parameters, pressure, temperature, flow);
4. System features:
01. Practicability: The oil field and oil well sites are geographically dispersed, so the wide coverage GPRS network is used for high signal capture. It is necessary to use a high-gain antenna to ensure the normal operation of the network;
02. Real-time: Using the latest communication and software and hardware technologies, a clear and reasonable system architecture has been established, which can realize multi-threaded remote concurrent communication. In a few seconds, hundreds of measurement and control terminals can be transmitted in real time. Go to the monitoring center for centralized monitoring and remote scheduling to realize timely alarm of fault information;
03. Scalability: The system reserves the interface, which can carry out unlimited expansion of the system or software and hardware modules, which is convenient for long-term upgrade and maintenance, and extends the life of the system. By updating the components, the system can continue to exist, but not the entire system. Paralyzed, causing a lot of investment losses;
04. Easy maintenance: The system can execute corresponding remote operation commands to the measurement and control terminal, including remote parameter setting, remote control, remote data copying, remote terminal reset, remote measurement and control terminal upgrade, etc.;
05. Ease of operation: The system software has perfect functions, modular, graphical design, full Chinese help throughout the process, and the operation is simple and convenient;
[ad_2]