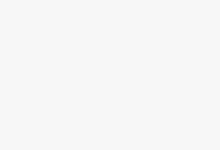
RFID mine vehicle management and intelligent weighing system solution
[ad_1]
1. Industry background and application requirements
1. Industry background
Automobile intelligent weighing management system has become an important part of the information management of many enterprises, forming a new type of weighing management mode that is efficient, accurate, fast and anti-cheating. The following uses a power plant application as an example to introduce the basic framework of system implementation.
The so-called intelligent automobile weighing management system is to add the automatic identification function of weighing vehicles realized by long-distance RFID technology to the original automobile weighing management system, and merge the automatically collected weighing vehicle information into the weighing management system middle. The intelligent weighing management system applied to the power plant has increased the passing speed of the metering department of the fuel department of the power plant by 3-4 times. Through the automatic identification and precise measurement of the vehicle number, the economic loss of the power plant caused by man-made fraud is effectively prevented. In addition, after the implementation of the system, the labor intensity of the staff and the error rate of manual weighing have been greatly reduced, the transparency of the fuel management process has been improved, and the informatization process of the power plant has been promoted.
2. Application requirements
The automatic metering system of the coal yard aims at the fully automated (without human intervention) data collection of automatic metering, weighing and skinning (empty cars) using cars as a means of transportation to ensure the accuracy of the original data collection. Through the realization of automatic measurement, the operating time of each operation link can be greatly shortened, the connection and unloading ability of the measurement system can be improved, and the working environment of the measurement personnel and the car driver can also be improved, and the labor intensity can be reduced.
2. Project implementation goals
The implementation of the project is divided into two phases, the first phase is the transformation of the existing system, and the second phase is the realization of unattended operations. The automatic metering system of coal yard mainly includes the following six parts:
(1) Queue management of transportation vehicles. Vehicle queue management mainly completes the queue of transport vehicles, prevents vehicles from jumping in line, and improves the order of vehicle transportation.
(2) Sampling. Sampling The sampling of incoming coal is completed (the sampled coal is used for coal quality analysis).
(3) Weighing. Weighing mainly completes the measurement of the gross weight of coal-carrying vehicles.
(4) Peeling back. Treading mainly completes the measurement of the empty weight of the vehicle, and finally calculates the net weight.
(5) Real-time monitoring. Real-time monitoring mainly completes real-time monitoring of the process of sampling, weighing, and skinning, so as to know the situation of sampling, weighing and skinning vehicles in time for timely processing.
(6) Monitoring and management system. The monitoring and management system mainly completes the management and maintenance of basic system information, and the selection and setting of operating modes, etc.
Three, system design
1. The topology of the system
The network topology of the system is shown in Figure 1. Including: monitoring management system, vehicle queue management, weighing host, sampling host, skinning host, real-time monitoring, database server and other online workstations, etc. The unit systems are connected together through the intra-plant LAN to realize data sharing.
Figure 1 Network structure diagram of automatic metering system of coal yard
2. System workflow
Figure 2 Work flow of automatic metering system
Before entering the coal yard, all transportation vehicles first go to the vehicle queue management office to sort the queues. Only the transportation vehicles that have been sorted can enter the coal yard. After the transportation vehicles are sorted, they enter the sampling platform for sampling. When sampling, it is necessary to judge whether the vehicle jumps into the queue, if it is a jumper vehicle, it will not be sampled. After the sampling is completed, the vehicle drives into the truck scale for gross weight measurement, after the measurement is completed, the coal is unloaded, and after the coal unloading is completed, it drives into the truck scale for tare weight measurement, and the net weight is automatically calculated after the measurement is completed. If an abnormal phenomenon occurs during the weighing and peeling process, the system will automatically notify the real-time monitoring system, and the monitoring personnel can deal with it in time to ensure the normal operation of the system. The system workflow is shown in Figure 2.
Four, system operation
Software Environment:
Serial number name:
1 Operating system: Windows XP/NT/2000/2003
2 Database: SQL Server 2005
3 Development language: c#
4 Development environment: Microsoft Visual Stdio.Net 2008
5 Architecture: C/S architecture
Hardware list:
Device name Unit Model
1 UHF fixed integrated reader station RURI-3180
2 UHF electronic label sheet RUTW-8630
3 UHF handheld card reader SUHR-8088
4 UHF card issuer RURH-9688
According to the system workflow, the operation of the system is described in five parts below.
1. Vehicle queue management
The vehicle queue management realizes the management of the transportation vehicle queue, thereby reducing the occurrence of queue jumping and improving the traffic rate of vehicles. Automatic vehicle queue management is accomplished through the automatic vehicle number recognition system.
The automatic identification system of vehicle number mainly includes microwave radio frequency card, reader, radio frequency cable, antenna and automatic identification software of vehicle number. Each transport vehicle is equipped with a microwave radio frequency card, and each microwave radio frequency card corresponds to a vehicle number. The automatic identification of transportation vehicles can be achieved through the microwave radio frequency identification card. Every time a transportation vehicle passes, the automatic identification system of the vehicle number automatically generates a queue number for the vehicle as a sampled queue sequence. The advantage of using the automatic vehicle number recognition system is that there is no human intervention, and the vehicle queue is objective and accurate.
2. Sampling
An automatic vehicle number recognition system is installed at the sampling platform. When the transport vehicle enters the sampling platform, the automatic vehicle number identification system will automatically read the vehicle number information and determine whether the vehicle is a queue-jumping vehicle, and if it is, the sampling will be rejected.
3. Weighing
Figure 3 is a schematic diagram of the automatic weighing process. Among them, Figure 3a shows that the truck scale is in a weighing ready state, Figure 3b is a weighing state, and Figure 3c is a post-weighing state. When the weighing is ready, the green indicator light is on, and the car stop is closed at the same time. After the sampling is completed, the truck scale can be driven into the truck scale for measurement when the truck scale is ready for weighing.
Figure 3 Process diagram before, during and after weighing
After the vehicle enters the truck scale, the red indicator light is on (as shown in Figure 3b), and the automatic vehicle number recognition system reads the vehicle number information. After the vehicle is positioned successfully, the metering software starts to measure. After the meter is successfully measured, the car stopper opens and a voice prompts the vehicle to drive out Truck scale, and display the measurement through the electronic display screen, as shown in Figure 3c. After the vehicle is completely driven out of the truck scale, close the stopper and turn on the green indicator light, and wait for the next measurement.
In the course of measurement, when there are other situations, such as the vehicle cannot be located, the vehicle number cannot be read, etc., the measurement software will automatically give voice prompts and alarm the monitoring center to prompt the management personnel to deal with it. During the whole weighing process, no human operation is required.
4. Peel back
The process of peeling back is basically the same as weighing. The difference between the two is mainly in the content of some voice and alarm information.
5. Real-time monitoring
All information in the four operation processes of vehicle queue management, sampling, weighing and skinning are fed back to the monitoring center host in real time, and the management personnel can understand the status of each work process in real time through the monitoring software system. For example, there are vehicles that jump in line at the sampling site, the vehicles cannot be positioned during weighing and skinning, and the vehicle number cannot be read, etc., can all be understood in the monitoring center.
In order to ensure the uninterrupted work of the coal yard, the automatic metering system adopts two working modes: automatic mode and manual mode. Under normal circumstances, the automatic method is adopted. When some hardware equipment in the system fails and cannot work in automatic mode, manual operation can be used to ensure the normal production of the coal yard. When the hardware equipment is repaired, switch to Automatic way. The manual method is a backup method.
5. Equipment selection criteria
The automatic identification technology adopted by the intelligent vehicle weighing management system is the long-distance RFID system. The electronic tag (car card) is affixed to the inside of the front windshield of the transport vehicle. The identification distance of the RFID system is required to be greater than 5m. There is no special requirement for the identification speed, no special requirement for the data capacity of the label, and whether the label has rewrite There are no special requirements for functions. The RFID system is required to have high reliability. The working environment of the equipment usually requires dustproof, temperature and humidity according to industrial-grade application standards.
It is worth noting that attaching the electronic label to the inside of the windshield usually reduces the reading distance of the label, so the influence of the glass substrate should be considered in the design of the electronic label. In addition, the application generally also proposes the anti-dismantling function requirements after the label is attached.
Six, application effect analysis
The automobile intelligent weighing management system has played an important role in customer automation management. On the one hand, it greatly improves the efficiency of fuel coal storage measurement management, prevents the loopholes of manual operation, and improves the working conditions and labor intensity of weighing measurement and transportation vehicle drivers. On the other hand, it has greatly promoted the pace of enterprise informatization construction, and has established an example of successful application of new technologies for the industry.
Solution company: Mobile (Tianjin) Electronic Technology Co., Ltd.
Contact: Zhang Bo
Tel: 15102250550, free service hotline: 400-0086-890
website:http: //www.myiot.org
[ad_2]