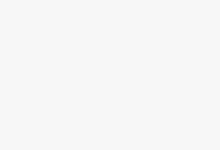
RFID management plan for concrete precast parts
[ad_1]
1 Overview
By pre-installing RFID electronic tags in the concrete precast parts, the whole life cycle management of the production process control, delivery management, on-site management and traceability of the concrete precast parts can be realized.
2. Demand analysis
The specific application requirements are described as follows:
Production management: Automatically identify prefabs in batches, record prefabs’ “complete time, completed quantity, specifications” and other related information, and synchronize them to the management platform in real time.
Factory management: Automatically read the prefabricated parts loaded on the vehicle in batches, record the factory information, match the order, and automatically transmit the information to the background.
Project site admission management: automatically read the prefabs that enter the site, and synchronize the information to the system platform.
Yard management: Read batches of prefabs in the yard, monitor their quantity changes, and synchronize them to the background.
Installation management: When the tower crane hoists the prefab, it can automatically record the installation time of the prefab.
Traceability management: For prefabs that have been installed, you can read a single piece through the handheld, and display the prefab information.
3. Technical Solution
3.1. RFID electronic tag selection
Considering that the electronic tags need to be embedded in concrete and need to be read in batches over long distances, the active 2.45G + 915M RFID composite electronic tags are selected.
3.2. Application process
Production management: When the production of the prefab is completed, use the RFID mobile phone to read the electronic tag data, enter the completion time, completed quantity, specifications, etc., and synchronize it to the background.
Factory management: Install RFID readers inside and outside the factory gate, read the prefab tags loaded on the vehicle, determine the direction of entry and exit, match the order information, and automatically synchronize to the background.
Project site admission management: Install an RFID reader on the project site to automatically read the prefabricated RFID tag data that enters the site, and synchronize the information to the system platform.
Yard management: Install RFID readers in the yard to automatically read the prefabricated parts in the yard, monitor their changes, and automatically synchronize to the background.
Installation management: Install an RFID reader on the tower crane. When the tower crane hoists the prefab, it will automatically read the prefab label and automatically record the prefab installation time.
Traceability management: For the prefabs that have been installed, the single piece is read through the RFID handset, and the information of the prefab is displayed.
3.3. System Networking

3.4. Solution products
3.4.1. Active electronic tags

Model: ZCT311
Can be combined with 900M UHF, taking into account the intensive reading and traceability management of the metal environment
Use high-strength shell material, waterproof, high temperature resistance, impact resistance
Strong anti-interference, adapt to complex application environment
Long reading distance, low power consumption, anti-collision, maintenance-free

3.4.2. Universal Reader

Model: ZCR811
Long reading distance, effective distance up to 300m
Efficient anti-collision algorithm, read more than 1000 tags at the same time
Integrated, waterproof/lightning protection suitable for outdoor application environment
Flexible wireless configuration of tags
Multiple interfaces, suitable for different applications, provide SDK and underlying communication protocol


3.4.3. Communication Gateway

Model: ZCM311
Efficient entry and exit judgment algorithm to accurately realize personnel entry and exit judgment
Large-capacity data storage, offline automatic data storage, online automatic upload
Multiple interfaces, supporting GPRS/3G/Ethernet data interface environment
Remote monitoring of equipment status
Built-in switching power supply, wall-mounted installation

3.4.4. RFID handset

Model: ZCH311
Built-in active RFID reading module to realize remote reading and control of active electronic tags
Industrial three-proof machine design, sturdy and durable
8-inch industrial Android tablet, large screen, high performance, easy to handle various complex applications
Large capacity battery, durable

3.4.5. System Platform
The list of system platform functions is as follows:
1) System management: equipment management, account management, configuration management
2) Prefab management: prefab type management, prefab information management
3) Label management: label data management, association management
4) Entry and exit management: entry and exit point configuration management, entry and exit management, online monitoring management
3.4.6. RFID handheld APP
The functions of RFID mobile phone software are as follows:
1) Scanning of prefabs
2) Inventory of prefabricated parts
3) System configuration
4) Label test
[ad_2]