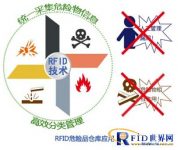
RFID system solution for dangerous goods warehouse
[ad_1]
Since dangerous goods have dangerous characteristics such as flammable, explosive, toxic, harmful or corrosive, from their production to use, storage, transportation and operation. If the control is improper, accidents are prone to occur, such as fire or explosion, poisoning or casualties, pollution of the ecological environment, etc.At present, the management task of dangerous goods warehouse in our country is still very arduous. Xindao has been engaged in the research and development and application services of RFID technology for a long time. This article describes the RFID application case of dangerous goods.
RFID
Technology to strengthen the safety management of dangerous goods warehouses to avoid possible harm and loss to life, property, health and the environment.
This RFID application case is the unified collection and management of dangerous goods information through RFID technology, which can realize the efficient classification of dangerous goods, avoid two or more interactions that will cause safety accidents, and prevent manual management from loopholes. Accident. Through the management of chemical information, it is convenient to understand the status of chemicals, dispatch personnel to inspect in time, and report the situation to manufacturers at the same time. The management system can greatly improve the efficiency of dangerous goods management, make supply chain management more scientific and solve The management blind spots in the logistics of dangerous goods are eliminated, and the safety and quality of dangerous goods are guaranteed.
RFID application case display:
The customer is a chemical company, and has long needed to manage a large number of chemical dangerous goods. Their warehouse management still stays on the basis of manual operation. All the inbound and outbound data has to be entered by the warehouse staff one by one. This primitive Warehouse management operation mode seriously affects work efficiency. Many inbound and outbound data cannot be updated in the system in time, and effective location management is not implemented in system management. The system cannot understand the distribution status of materials in the warehouse and the warehouse storage. Ability, when workers are placing and receiving materials, there is no system to guide them, and materials may be placed in the wrong position or incorrectly received. The above drawbacks have seriously affected the efficiency of management, reduced the storage capacity of the enterprise’s warehouse, increased the cost of warehouse management, and restricted the development of the enterprise.
1. Cargo location management
An electronic label is installed on each dangerous chemical product. The label records various performance and characteristics of the dangerous product, such as storage location, production date, manufacturer, name, hazard, storage method, use safety matters, and transportation safety matters And other information. Then transfer this information to the company’s management database, so that the company can quickly understand the distribution status of chemicals in the warehouse, storage time and other information.
2. Inbound and outbound operations
Scan the barcode through the wireless terminal, efficiently handle the warehouse entry and exit, clearly understand the situation of chemicals entering and exiting the warehouse, and implement real-time updates of the warehouse data. It can clearly reflect the proportion of various chemicals in sales in the database, and at the same time, it can avoid the time wastage caused by man-made reasons and the illegal use of dangerous goods by others. Ensure the safety of safety products.
3. Inventory
Scan the electronic tags of cargo location and material electronic tags through the wireless terminal, and check the material inventory in real time. In the system, random spot checks can be divided into warehouses, regions, and cargo locations, and spot checks can also be made for specific types. At the same time, the entire system can be checked regularly. A comprehensive inventory and a difference table are generated to facilitate the analysis and tracking of which materials belong to the materials with low inventory accuracy. At the same time, some materials that have not been used for a long time are dynamically analyzed and warnings are issued.
4. Quality traceability
Through the safety traceability system, you can learn about the production time, manufacturer, and expiration date of hazardous chemicals. In the course of use, once it is found that the chemical does not meet the safety standards, it is necessary to take effective measures in time to report the situation to the manufacturer in a timely manner. Avoid causing greater safety accidents.
5. Inquiries, statistics, reports:
Including customer shipment statistics query, product tracking, channeling management, serial number query and other management reports, inventory dynamic query/detailed list, query, statistics, and report generation of various documents. Form textual content. Convenient for review.
The new guide RFID application case of dangerous goods reflects the application of RFID in the management of hazardous chemical production, storage and transportation. It can not only improve the efficiency of hazardous chemical management, make the supply chain management more scientific, and solve the problem of hazardous chemicals. The management blind spots in logistics ensure the safety and quality of hazardous chemicals. It is believed that in the not too long future, RFID technology will penetrate into my country’s modernization construction like bar code technology, and will gradually extend to all aspects of the chemical industry. It will surely cause a change in the field of hazardous chemical logistics management and improve operational efficiency and Economic benefits play a key role, increase the income of the industry, and promote a brand-new leap in my country’s national economy.
[ad_2]