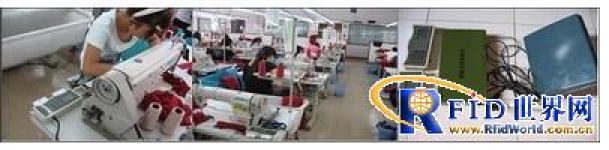
Electronic work ticket solution
[ad_1]
1. The status quo and trend of industry informatization
China is a major textile country in the world. It has concentrated a large number of low- and medium-end clothing suppliers in the world. With tens of thousands, the number of domestic industrial workers engaged in the clothing industry is even a very large number. In this field, there are many large and small clothing companies, and the information construction of the clothing industry is uneven, but it can be divided into the following stages:
1. In the initial stage (manual calculation): Workers record the products, quantities, and procedures they produce in a notebook. When calculating wages at the end of the month, the notebooks are unified and statistics are provided by specialized personnel.
2. The stamping stage (paper label stage) means: the work ticket (label) used by the worker is printed on a fixed piece of paper in the pattern of a seal, a large label ticket for each tie, and a small label for each process , When workers produce a certain process, they use scissors to cut off the small labels of the corresponding process as a voucher for the number of products they produce, and then collectively summarize them.
3. Semi-computerized stage (barcode meter labeling stage) That is: with the help of a computer and a printer, the large labels on a bundle of goods are printed out by barcode in each process
4 Automation stage (electronic work ticket stage) Electronic work ticket is based on IC card technology and data terminal collection technology. The information of each tag ticket is stored in the IC card. , Processing content (process) and other information are directly sent to the computer to complete the labeling work.
Second, the advantages of electronic work tickets
High real-time
The electronic label solves the problem of real-time information. Under normal circumstances, workers need to cut the work ticket with scissors and hand it in at the specified time. The worker who calculates the wages of the worker scans the label into the computer, so the time for the intermediate process is at least one day The time, even more, can reach 1 month. The electronic tag device directly completes the process, directly enters the computer, and displays the result to the worker, so that the worker knows whether the goods have been paid for themselves.
safe and stable
The bar code label is subject to the clarity of the bar code. The IC card converts the information into a digital mode for transmission. The bus adopts the 485 communication mode to ensure the safety and stability of the data. Even if there is a problem, the worker will find it immediately, not until the end of the month.
Upcoming and releasing, information sharing
The electronic label establishes a connection channel for managers, company executives and front-line workers in the workshop. Each worker’s production progress can be directly fed back to the manager, and the manager’s instructions (such as notifications, etc.) can also directly reach the worker’s screen. Build a bridge between workers and senior management
Analyze the flow and solve the blockage
Whether the arrangement of procedures in the garment production process is reasonable, and whether the deployment of various electric sewing cars is reasonable greatly affects production efficiency. The most primitive data obtained through the electronic label, the computer directly informs the relevant personnel in the form of charts and large LCD screens, and the procedures and personnel can be rationally deployed based on numbers and experience.
save costs
The IC card is recycled. After the production is completed, the IC card can be recovered and used for the next product. The cost of printing consumables and paper is no longer incurred every month, and the job position of the scanner can be eliminated. This saving is continuous Yes, the benefits to the company are constantly increasing.
Improve management
The smooth flow of information in the company will improve management. For example, managers can easily see the progress of each product, the production process of each shipment, who will produce it, and when it will be produced. Quantify and summarize information that was previously difficult to quantify, analyze problems, and avoid errors in advance.
Recycling, green and environmental protection
The recycling of IC cards saves a lot of paper resources. Everyone in clothing companies knows very well that a large number of paper labels will be produced every month to complete the production mission. Electronic tags are very consistent with my country’s current green environmental protection policy.
Solve the data collection problem of the software.
All software has its own advantages, but they all have a common disadvantage: the correct result can be guaranteed only when the original data is correct. The source of the original data is mainly: manual input, barcode scanning, but these are some data that can be collected after a lot of procedures, and cannot be guaranteed to be completely correct; the electronic label extends forward on the basis of manual input and barcode scanning One step: Collect data directly on the production line, reduce the process of manual intervention, greatly improve the correctness of the original data, and ensure the integrity and authenticity of the results.
Three, work flow
When cutting and bundling, it is equipped with a smart material card to replace the barcode work ticket or the top sign.
Install a card reader with dual reading heads on each sewing machine or the post where piece counting is required.
When an employee is working, he swipes down the card reader, the reader displays the employee number, and the material card is swiped down after each tie, and the reader displays the number of each tie, the process completed by the employee, the color and size, etc.
The system automatically records which work orders are being made by employees during which time period, and how long each process takes.
When the quality controller finds a defective product, he only needs to press the card reader, and the system automatically records which employee, which process, and how many defective products are present.
Four, system characteristics
(1) Operation: automatic, simple and intuitive computer automatically collects production data; simple operation process, does not change traditional operating habits, cutting beds and parking spaces do not require special training; through the terminal display screen, you can directly view the piece and wages of the day or a specified day condition;
(2) Management: standardized, fair and accurate piece counting, efficiency and transparency, effectively reducing employee turnover; solving production bottlenecks and improving production efficiency; process allocation, responsibilities to individuals, effectively reducing defective products and reducing repair rates;
(3) Information: accurate, real-time and real-time monitoring of production bottlenecks and parking space status; optimizing the production process and shortening the product cycle; precise calculation of production capacity and life cycle; automatic generation of intelligent analysis reports;
(4) Cost: saving and environmental protection, completely eliminating traditional work tickets (Fei Zai, Fei Zai), saving costs; reducing manpower and saving wages; accurate time-sharing wage statistics, effectively eliminating the problem of employee hiding work tickets;
5. System implementation benefits
(1) Discover production bottlenecks in real time, monitor the production capacity of each parking space in real time, and balance production line production capacity.
(2) Real-time automatic statistics of worker production progress and automatic statistics of worker output and working hours of each process.
(3) It is possible to completely prevent workers from falsely reporting output, accurate piece counting, and reasonable and fair wage rates.
(4) Save time for employees to cut work tickets, no need for specialized statistics personnel, reduce personnel, and save wage costs.
(5) The RFID card can be reused for more than 10 years, saving the cost of work ticket paper and printing work ticket.
(6) Process improvement, instantly find out which employee is doing the same process faster, and it takes a few minutes and seconds. Compared with the reasons for others’ quickness, individual small improvements become improvements for all employees, and the company’s production efficiency is continuously improved and optimized .
(7) The product quality control is more complete, with immediate feedback of the defective product information of the production line, and timely control and adjustment.
(1) Data can be stored and work offline.
(2) Built-in wireless transmitting and receiving module, wireless network wiring. With 232 interface, it can be connected with barcode gun.
(3) Built-in menu function, you can customize the display content, such as employee name, output of the day, current model number, tie number, process name, color, size, quantity, etc.
(4) The employee selects the production process in the reader menu, and the transfer is quick.
(5) Double reading heads are used to more accurately count the effective working time.
(6) Soft keyboard, users can customize the function of function keys and customize the appearance of the keyboard.
[ad_2]