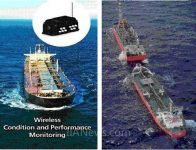
Application of wireless sensor network in the field of ship machinery monitoring
[ad_1]
In 2004, BP began to come into contact with a wireless network technology called Mote. This 2 x 2 inch device includes a processor, a permanent non-volatile memory, a wireless communication module and an I/O board that can be connected to the sensor. Mote can connect sensors to wireless networks and transmit data to terminal devices. These Motes are usually used in research institutions by academia or laboratories, but the industry still holds a wait-and-see attitude. At that time, no company produced commercial products for wireless sensor networks.
BP Loch Rannoch tanker
Harry Cassar, director of BP’s digital communications technology department, said: “When we first came into contact with this new technology, we were thinking about whether it could work in our environment. These Motes seem to be circuit boards with sophisticated designs and almost no protective casing. We I want to know whether it can be placed in an environment where metal equipment is scattered and high-temperature and high-frequency vibration such as a refining field; whether Mote can operate normally in such an environment after packaging. The only way to verify this idea is to test. Thus, the Loch Rannoch project was born.
Project Introduction
The Loch Rannoch project started with the testing and evaluation of Mote, but it did not stop at this stage. In fact, the purpose of this project is to develop a commercial wireless sensor network system that can be used in BP’s global industrial production. At each stage of this project we will encounter some difficulties, but we have overcome them one by one.
The first difficulty for BP was deciding where to implement the project. Most of BP’s projects require the use of safe equipment. In order to test this uncertified wireless network technology, BP needs to find a harsh environment with lower security requirements. As a result, the company selected a 1,000-foot-long, 132,000-ton oil tanker, Loch Rannoch, to travel between the Schiehallion oil storage vessel and the oil processing station in the Sullom Voe area of Shetland Island.
The tanker has more metal equipment than the refinery, so the radio frequency environment here is more harsh and complicated. Not only that, the cabins of oil tankers are closed by metal watertight doors. In addition, strong vibrations from the engine, generator and propulsion engine, as well as the high temperature of 80°F to 100°F in the engine room, will all be unfavorable factors for the normal operation of Mote.
BP’s main technical department and BP transportation department are very concerned about this test plan. “If you want to test on the Loch Rannoch tanker, I hope to get more practical value, not just a test to test whether Mote can communicate with each other.” Cassar also pointed out: “BP transportation department very much hopes to be able to collect the engine Vibration data of the chamber mixer.”
system introduction
The BP plan is to establish a predictive maintenance system to monitor machines with strong vibrations such as motors and pumps. These machines are placed in the engine room of the Loch Ronnach tanker. Vibration information is used to monitor the working status of the system, and when abrasion or tear occurs, a warning is sent through wireless communication.
“Vibration information can help predict the wear and tear of the machine and predict when maintenance is needed,” Cassar points out. “The system can tell you whether the spindle is bent or which machine is out of balance. It can save you from regular maintenance every 500 hours. Get free from work and only do necessary maintenance when you need it.”
Based on 150 Rochwell accelerometers, we built the entire measurement system. Each machine is equipped with 6 sensors, one for each of the three axis directions, two auxiliary measurement points, and a tachometer that monitors machine rotation and provides angle phase. The sensor is encapsulated in a metal shell and placed 2 inches away from the machine, and is connected to the Mote by wire. Each Mote can drive 10 sensors at a time, although BP does not use all of them.
The predictive maintenance system of the Loch Rannoch project monitors the working status of the pumps and motors in the engine room. Approximately 150 accelerometers are installed in these mechanical equipment. The vibration data detected by the accelerometer is used to evaluate the current operating environment. When wear or tear occurs, Mote and the gateway in the wireless sensor network send a warning through wireless communication.
Several Motes form a subnet controlled by the gateway. Mote forwards the collected data to the gateway through the direct spread spectrum modulation technology of IEEE 802.15.4. Due to the restrictions of the British government, the working frequency band was adjusted to the British standard 868MHz. However, the working frequency band of the system is adjustable, but it is extremely important for working in an international environment. Because the licensing standards of different countries are often different.
A mesh network is constructed between the gateways through IEEE 802.11, and all data is passed to the master gateway. The gateway transmits the data to the back-end data storage server. Each gateway has 2GB of memory, which ensures that when the gateway loses connection with the ship’s network, it can still collect and temporarily store data from Mote.
Problems and solutions
In the Loch Rannoch project, BP, Crossbow, and Intel have encountered many problems, which need to be resolved before the project is implemented. The metal structure of the hull and dense mechanical equipment make the possibility of radio frequency transmission in the engine room extremely small. “Metal is a powerful reflector of radio frequency energy,” said John Suh, senior application engineer at Crossbow Technologies. “Metal has a bad influence on radio frequency signals, so there is no way to get information through the transmitter and receiver.
To solve this problem is to build a mesh network. In this kind of network, every node can communicate with its neighbors. The data on the node will be forwarded again and again by neighboring nodes until the data reaches a controller or collection station. Such multiple paths of data transmission make this network very reliable. Once a node expires, other nodes can still communicate with each other directly or through one or several relay nodes.
“Unlike traditional point-to-point connections, mesh networks provide a large number of different routes,” said BP’s Cassar. “Each node can detect information in any corner in cooperation with other nodes. This function cannot be achieved in a peer-to-peer network. The flexible performance of the mesh network solves such problems.”
Equipment safety
Another issue related to the environment is to design a safer enclosure that can hold Mote and batteries. Another task of Crossbow at this stage is to develop a commercial system suitable for BP equipment. “We have fully studied the packaging technology and designed a special case with a high safety factor and suitable for engineering applications and environments.” Suh said.
How to process all data
In the final stage of the project, the project team faced a serious problem, that is, to accurately determine the location of the mechanical problem, a large amount of vibration data must be obtained and analyzed. The challenge lies in how to coordinate the collection of large data volume sensor monitoring data and the low-rate network transmission protocol (IEEE 802.15.4) used in the communication between Mote and the gateway.
The specific solution is to reduce the amount of data transmitted to the gateway by processing a large amount of data on Mote. In the beginning, Mote used an 8-bit processor, but this proved to be insufficient for large amounts of data processing. So Intel and Crossbow used Intel 32-bit X-Scale processors to replace the original 8-bit processors.
“When you look at sensor network applications, you will find that different sensors have different data bandwidth requirements.” Crossbow’s Suh said, “In some practical applications, you may need to collect temperature through a temperature sensor. Obtaining data does not require too much processing. But in this project, we used a high-bandwidth vibration sensor. We decided to use a microprocessor with more power than an 8-bit processor. So we adopted a 32-bit microprocessor Device.”
Intel has further enhanced Mote’s processing performance through software. “The most typical thing is that you can perform FFT and other calculations on Mote to extract the frequency characteristics of the data.” Intel’s sensor network system director Ralph Kling said, “In order to do some more advanced processing, we got it from Rockwell Use the license of its interface IP intellectual property core, and transplant many of its experience algorithms in this field to Mote, so that Mote can better implement monitoring. Our purpose is to carry out a large amount of data processing within the network boundary without Transfer all the data back to the back-end server as before.”
Intel has also added software that can parse data into XML format on the gateway. “We have an XML-based data system that can abstract and retrieve data.” Kling said, “XML is a common middleware format used for data exchange between gateways and back-end servers. The gateway also provides a connection back-end The Rockwell server interfaces and processes the data into a format acceptable to the server.”
Energy supply
In the process of BP’s development of wireless sensor network commercial systems, a series of energy consumption issues such as how to obtain energy, how to use energy, and how to ensure sufficient energy have been paid more and more attention. In order to solve these problems, the research team adopted the low-power radio IEEE802.15.4 standard, and implemented energy security management mode on Mote.
In addition, the preprocessing of data reduces the amount of data transmission, which also saves power consumption. “We reduce the amount of wireless transmission,” Cassar said, “RF components consume most of the power, and the amazing processing power of the new processor reduces the amount of data, thereby greatly improving battery life.”
Another task is the acquisition of electrical energy. “The other technology we tested on Loch Rannoch is to obtain the energy generated by the vibration of the machine, thereby converting the kinetic energy into electrical energy,” Mr. Cassar, “We tried two ways, one is to use a rechargeable lithium battery to test whether It can fully support Mote’s work. The other is to use rechargeable large-capacity capacitors as storage media. We recognize that Mote’s energy harvesting method plays an important role in this project.”
test results
The Loch Rannoch project realized an efficient automatic data collection system for system monitoring and predictive maintenance. Most of these tasks were done by people before. “Operators can directly obtain state monitoring data of various rotating machines through handheld devices, such as PDAs, and detect an acceleration reading at the same time.” Cassar said, “In the past, for each machine, the operator recorded the position of the measuring instrument and measured it. A few seconds of data. This is a very tedious job, but it must be done every six to eight weeks, sometimes longer. However, the data they collect each time is actually very small, because it is only a few times a year. We collect data every time. We now set the network to collect data every 18 hours. Instead of holding a handheld device to test the device every 8 weeks, instead of automatically collecting data every 18 hours.”
Other lessons learned from the Loch Rannoch project
◆The sensor network can work well in harsh environments.
◆The choice of radio frequency and network structure is very important. Both of these can improve the reliability of communication.
◆The advanced platform can work well with this special application, because the preprocessing within the network boundary greatly reduces the amount of data transmission.
[ad_2]