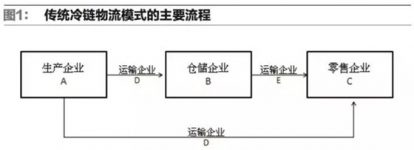
Application scheme of RFID technology in the field of railway cold chain logistics
[ad_1]
As we all know, railway transportation is suitable for long-distance, large-volume cargo transportation, especially long-distance transportation over 1000km has obvious advantages. my country has a vast territory and the production and marketing of refrigerated food are far apart, which provides favorable external conditions for railways to develop cold chain logistics. However, at present, the volume of railway refrigerated transportation in my country is relatively small, accounting for less than 1% of the total demand for refrigerated transportation in the society, and the advantages of railways in long-distance transportation have not been fully utilized.
Facing the growing refrigerated transportation market, China Railway Corporation has accelerated the transformation of railway cold chain transportation to modern logistics, and launched a series of new measures for railway cold chain logistics services. The author’s work unit, the National Railway Testing Center of the Chinese Academy of Railway Sciences, plans to build a railway cold chain logistics center and an intelligent transportation laboratory to build a railway cold chain logistics application demonstration platform, an inspection platform and a railway cold chain logistics technology innovation platform. This article discusses the application of RFID technology in the field of railway cold chain logistics after the completion of the railway cold chain logistics center.
1. Traditional cold chain process and main problems
1. The main process of the traditional model (Figure 1)

(1) After the product is produced and packaged in company A, it is stored in the manufacturer’s cold storage. Products are stacked directly on the ground or on pallets.
(2) Transportation. The manufacturer A informs the transportation company to deliver the goods, which can be directly delivered to the retail enterprise C. Or enterprise A rents part of the warehouse in storage enterprise B, and the goods are sent to storage enterprise B, and when necessary, they will be distributed through B.
2. The main problems of the traditional model
(1) The transportation process is not transparent. In order to reduce costs during transportation, third-party transportation companies may turn off the refrigerator during transportation and turn on the refrigerator when it is almost at the destination, and cannot achieve the entire cold chain. When the goods are delivered, although the surface of the goods is freezing well, the quality has actually deteriorated.
(2) The storage process is not transparent. Due to cost considerations, storage companies may use the valley electricity period to turn on at night to reduce the temperature of the storage to a very low level, and the refrigeration equipment is shut down during the day, and the temperature of the cold storage fluctuates more than 10°C or higher, which directly causes the food shelf life to decline.
The traditional monitoring method usually uses a temperature recorder to measure and record the temperature of the entire carriage or cold storage. This method requires wired connection and manual intervention to export the data, and the data is in the hands of the carrier and warehousing companies, and the cargo owner cannot easily obtain the data.
Due to concerns about the above problems, some large domestic pharmaceutical companies or food companies would rather invest large sums of money to build their own cold storage and transportation fleets than to use the services of third-party cold chain logistics companies. Obviously, the cost of such investment is extremely huge. of.
(3) Invalid handling. When the transportation company picks up the goods from the production company A, if the pallets cannot be transported, the workers need to move the products from the pallets to the refrigerated truck; after the goods arrive at the storage company B or the retail company C, the workers need to unload the goods from the refrigerated truck Put the back yards on the pallets and then count them into the warehouse. In this way, the goods will be dumped and transported again, which not only takes time and labor, but also easily causes damage to the packaging of the goods, which affects the quality of the goods.
(4) The warehouse management efficiency is low. It is necessary to provide paper export and warehouse receipts when leaving and entering the warehouse, and then enter the computer manually, which has slow entry efficiency and high error rate.
(5) Waste of human resources. The loading and unloading of goods and the palletizing require a lot of labor. In warehousing enterprise B renting a warehouse, warehouse management personnel must also be set up.
Two, optimization strategy
Aiming at the main existing problems of the traditional cold chain logistics model, the optimization strategies proposed are as follows:
1. Build a modern railway cold chain logistics center to provide a complete set of services such as transportation, warehousing, testing, sorting, and distribution of goods.
2. Pallet applications based on RFID technology. Research on the introduction of RFID technology into the field of cold chain logistics has already been carried out. As a basic digital management unit, pallets facilitate the realization of accurate digital management of large quantities of goods. Realizing the electronic informationization of pallets is an important means for timely, convenient and accurate management and effective supervision and control of the supply chain logistics system. It is of great significance for improving the level of logistics management and reducing logistics costs. Therefore, RFID temperature tags can be embedded on the tray.

Embedding RFID tags on the pallet can cooperate with the warehouse management system to achieve real-time inventory, accurate
The tag is equipped with an antenna, an RFID chip, a temperature sensor, and an ultra-thin button battery that can last for more than three years. Because it has both digital identification and temperature information, it can meet the requirements of cold chain temperature monitoring. Require.
3. Introduce the concept of tray sharing. Provide pallets with embedded temperature labels or lease them to cooperative manufacturers for free for use in railway cold-chain logistics centers to achieve consistent transportation of pallets and speed up the distribution of pallets among manufacturers, transportation companies, cold-chain logistics centers, and retail companies. To promote pallet intermodal transportation and mechanized operations, improve logistics efficiency, shorten supply time, and greatly reduce logistics costs.
3. Optimized cold chain logistics model

1. Storage. A company will install the produced products on the pallet provided by B company (with built-in RFID tag), and bind and write the basic information of the pallet goods through the handheld terminal at the same time, including the production date, type, name, weight, quantity, etc. Then store it in the cold storage.
2. Transportation. Company B sends a refrigerated container transport vehicle to Company A to pick up the goods. Company A transfers the pallets and the goods to the refrigerated container, and closes the door and seals the container after loading. After the refrigerated containers are transported to the railway freight yard, they are transported to Enterprise B by train. From the moment the goods leave the company A, the temperature sensor in the electronic tag can collect temperature information at any time. This information can not only be stored in the RFID chip in real time, but also can be transmitted to the company A in real time through the GPRS system, so that the managers of the company A can Grasp the real-time temperature situation in the car in front of the computer. Once the temperature is abnormal, the system will automatically alarm, and the management personnel of A and B enterprises can take immediate measures to avoid the risk caused by human negligence.
3. Storage. After the train arrives at the destination, the refrigerated container is directly transported to the loading and unloading platform of the B company’s cold storage for dismantling, signing and inspection, and entering the warehouse after passing the test. The forklift removes the goods with pallets and places them on the conveyor line. There is a detection door at the front of the conveyor line, and a fixed reader is installed above the door. After the RFID tags on the cargo boxes and pallets enter the radiation range of the reader, they include the cargo information written in the chip by the company A and the pallet information. The instant the pallet passes through the inspection door, it is captured by the reader and transferred to the computer system. middle. The staff can grasp a series of data such as the quantity and type of this batch of goods by just looking at the display screen, and there is no need to manually inspect the goods. If the cargo information displayed on the screen is consistent with the invoice provided by company A, it means that it is qualified. The worker presses the confirmation button next to the conveyor line. The cargo and pallets will be stored in the warehouse management system through the conveyor line and automated stacker. On the cargo space.
4. Out of the library. Company B is the storage center of Company A in this place, and all customers of Company A in this area or designated area obtain goods from this warehouse.
(1) Distribution. After A company receives the order from C company, it informs B company to distribute the goods. According to the order sent by A company, B company arranges the sorting of goods, updates the RFID information of the pallet goods, loads the sorted goods into a new pallet, and binds the new goods information to the RFID tag and puts it on the temporary storage shelf, waiting for dispatch Ship. The goods are sent to the C enterprise with pallets, and the C enterprise is unloaded after acceptance, and the pallets are brought back by the B enterprise.
(2) Customer mentions. After the customer’s vehicle arrives at Enterprise B, the driver and the cold storage manager check the pickup information, and the automated storage equipment transports the goods from the cold storage to the loading and unloading station. The loading and unloading workers directly unload the goods from the pallet and load them onto the customer’s transport vehicle. Provide trays.
4. Plan implementation goals
Through the above design process, we can understand that the application of RFID technology and pallet sharing system can achieve the following goals:
1. Increase the transparency of cold chain management. The core of RFID technology is the EPC (product electronic code) on the label. Since EPC provides a unique identification of physical objects, the use of EPC can realize the logistics tracking of goods throughout the cold chain, and the RFID temperature tag can also provide temperature monitoring , To ensure the quality and safety of goods in the cold chain logistics process.
2. Simplify the operation process and improve logistics efficiency. In the railway cold chain logistics center, inspection, unloading, and loading operations account for a large proportion. Embed RFID tags on the pallets and install readers at the entrances and exits of the storage center, so that automated equipment can be used to send goods out of/into the warehouse, which not only greatly reduces labor, saves time in and out of the warehouse, but also improves operational efficiency.
3. Improve the quality of inventory operations. Due to the RFID tags attached to the pallets and the warehouse management system, real-time inventory and precise height can be achieved.
4. Reduce costs and increase revenue. RFID is applied to inventory management, which can reduce manual review work, ensure the safety and accuracy of the quality of stored goods, and reduce the management cost of B enterprise; for the production company A, it can understand the inventory status in real time to prevent B company from being out of stock This phenomenon can also improve customer service quality, increase sales opportunities, and increase corporate income.
5. Reduce labor costs. The value-added services provided by the railway cold chain logistics center can enable A company to reduce manpower input and reduce costs.
6. The advantages of the railway cold chain logistics center are prominent. The application of RFID technology and pallet sharing can reduce transportation costs and improve the competitiveness of railway cold chain logistics centers.
V. Conclusion
The application of RFID technology has brought a turning point for the informatization and intelligent management of cold chain logistics centers. As the technology continues to mature, RFID will be more widely used in the entire cold chain supply chain. Prioritizing the application of this technology in the field of railway cold chain can enhance the attractiveness and competitiveness of railway cold chain transportation, expand the market share of railway cold chain logistics, and create new growth points for railway transportation.
[ad_2]