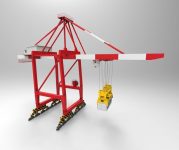
Automation of Crane in Inland Yard of Container Port
[ad_1]
RTG’s container loading and unloading function has not yet been fully automated. The automated systems it is equipped with mainly include Global Position System (GPS), Container Position Detective System (PDS), Tire Crane Automatic Deviation Correction System ( Automated Guided Sling System (AGSS), truck anti-lift protection system (Chassis Lift Protection System, CLPS), container number recognition system (Container Number Recognition System, CNRS), etc. These cranes are semi-automatic cranes. The automation function is mainly embodied in the addition of some automation systems to assist the driver in the loading and unloading of containers, such as the cart operation assistance system, the trolley operation assistance system, the spreader pairing and the container loading self-assisted system, etc. These systems reduce cranes to a certain extent The manual operation of the driver improves the loading and unloading accuracy and speed of the crane, shortens the time for loading and unloading containers, and improves the operational efficiency of the entire inland yard. However, at present, this type of crane is still mainly operated manually and supplemented by automated system functions, and the fully automated operation of unmanned crane operation has not yet been realized.
RMG is currently the main form of container automation inland yard cranes in the world. Compared with RTG’s automation system, RMG is equipped with more automation systems and is more comprehensive. RMG’s automation systems mainly include automatic voice guidance system (Public Address, PA), truck lift protection system (Chassis Lift Protection System, CLPS), truck position scanning system (Chassis Alignment System, abbreviated as CAS), Container Number Recognition System (CNRS), Final Landing System (FLS), Crane Video Management System (CVMS), remote network vision system
(Remote Vision System/Network Video Recorder, RVS or NVR for short), Spreader Position Control System (SPCS), Spreader Profile Scanning System (SPSS), Truck number recognition System (Prime Mover Number Recognition System, PMNRS for short). The unmanned fully automated RMG loading and unloading efficiency is very high, reducing the detention time of container ships, especially large container ships, and greatly increasing the container throughput of the port, thereby bringing huge economic benefits to the container port. At present, a single automation system has been integrated into one or more electrical system components. Automated port container inland yard cranes use RFID radio frequency identification, far-infrared ray sensor technology, position monitoring technology, laser scanning imaging and positioning, camera identification and Monitoring and other technologies carry out rapid information interaction through network communication protocols, so as to realize intelligent sensing, scanning, identification, positioning, monitoring and other operations. The article takes Singapore’s PSA Pasir Panjang terminal container yard automation RMG as an example to briefly explain the automation system of the container port inland yard crane.
1 Automatic human voice guidance system
When the truck enters the dedicated lane outside the yard and approaches the rail hoist, the moving truck will be guided by voice through the scanning and positioning system of RMG, so that the truck will arrive at an accurate parking position. When the truck needs to continue to move forward, the PA system will continue to send out the voice prompt of “forward”. When the truck arrives at the predetermined accurate position, the PA system will issue a voice prompt of “stop”; when the truck exceeds When the parking position is reserved, the PA system will continue to issue a “back” voice prompt, and the truck will retreat to the predetermined accurate position, and the PA system will issue a “stop” voice prompt. Through the voice prompt of the PA system, the driver can be guided to park the truck to a predetermined location in a short time, so as to ensure that the automated crane can perform fast container loading and unloading operations.
2 Anti-lifting protection system for trucks
When the RMG spreader is locked and the container loaded on the truck is lifted, if the lock on the truck that locks the container is not opened, the spreader will lift the container together with the loaded truck. The situation can easily cause damage to trucks and even threaten the personal safety of truck drivers. RMG’s CLPS system can scan the position of the truck. For example, when the CLPS scan truck rises to a height of 1 m above the safety setting, RMG will stop the lifting operation to automatically protect the truck, driver, and container. The role of.
3 Truck vehicle location scanning system
When trucks enter the RMG container loading and unloading area, the CAS system automatically scans the trucks. The CAS system can not only identify whether the trucks are single-deck trucks or double-deck trucks, but more importantly, It can scan and identify the moving position of trucks and interact with trucks’ position information and traffic lights. The lights and arrows of the traffic lights guide truck drivers to accurately move forward, back or stop, so that the trucks The truck arrives at the predetermined parking place in a short time so that the track crane can accurately and quickly carry out the grasping or loading action of loading and unloading containers.
4 Container Number Identification System
RMG saddle beams, outriggers, etc. are installed with multiple CNRS cameras that identify the front and back, side and top numbers of the container. When the truck loaded with the container arrives below the RMG side, the image of the container number is transmitted to the RMG through the camera function of the CNRS camera. CNRS system. After that, the CNRS system uses image recognition technology to identify, read and record the number of the container, convert the number of the container into numbers and letters that can be recognized by the computer, and transmit the read container number to the RMG control system and yard management system.
5 Carrying system
The FLS system uses cameras or lasers installed on the four corners of the spreader to identify the position of the container, and to identify and adjust the position of the spreader. The FLS system, which uses laser components as position detection, emits laser beams through the laser limits installed on the four corners of the spreader, and the four laser beams are parallel to the vertical four sides of the container. When the spreader moves, such as the laser beam irradiates the container, the FLS system will collect the feedback information of the laser beam, adjust the position of the spreader to keep the laser beam parallel to the vertical four sides of the container to be lifted, so that the spreader can Carry out the box movement accurately to avoid placing the spreader on the container slantingly.
6 Crane camera management system
The CVMS system uses multiple cameras installed on the RMG to monitor the yard conditions, lane conditions, and the operation of other RMGs in the same yard in real time, and synchronously transmit the monitoring images corresponding to each part to the CVMS system information processing center and the terminal. Control remote control operating room (ACOC for short). The CVMS system is a comprehensive management system for all the picture surveillance cameras installed by RMG. The system checks and monitors the storage yard, driveway, RMG operation and other conditions and status in accordance with the requirements of ACOC. At the same time, the CVMS system can also switch camera pictures as needed , To view and monitor the situation around RMG without blind spots.
7 Remote network vision system
The RVS/NVR system adds screen detection on the basis of the camera screen monitoring, and compares and analyzes the obtained real-time monitoring screen with the preset Video Encoder screen to detect whether the RMG’s hand and automatic operating conditions are within the set operating range Inside. The system also has the storage function of the monitoring screen, so that the monitoring screen can be called up for analysis later.
8 Spreader position control system
The SPCS system detects the position of the spreader and the container in real time during the lifting and lowering of the spreader through the two SPCS scanners installed under the RMG trolley frame and the reflective bottom plate installed on the spreader. When loading or unloading containers, the SPCS system automatically detects whether the position of the spreader and the container is tilted and instructs the spreader to perform tilt adjustment based on the detected position information, so as to ensure the position accuracy of RMG loading and unloading containers.
9 Container Stack Scanning System
The SPSS system is used to scan and detect the stacking layers and stacking height of a single row of containers under the RMG spreader. If the detected container stacking height needs to be consistent with the height set in the ABMS system, the container can be loaded and unloaded. Keep running. The SPSS system can also detect whether the parallel movement of the spreader will collide with the stack of containers. When the SPSS system scans and detects that the running spreader and container stacking height data is inconsistent with the height set in the ABMS system, the spreader It may hit the container stacked on the ground, and the SPSS system will stop the operation of the trolley and spreader, so as to prevent the RMG spreader from hitting the container in the yard.
10 Truck Number Recognition System
PM is used to connect quayside container cranes and RMG to transport containers within the terminal or external trucks. The loading and unloading of containers needs to identify, check and record the number of the front of the truck, which is the main function of the PMNRS system on RMG. Each truck is equipped with a tag with truck information on the front side of the truck. When the truck is close to the rail crane, the PMNRS system installed on the RMG saddle will read the tag of the truck through the RFID radio frequency identification function. The data on the label, so as to obtain the truck information.
In recent years, the construction of automated terminals in my country has developed extremely fast. Fujian Xiamen Yuanhai Automated Terminal, which has been put into actual operation, is my country’s first automated terminal and the subsequent Tianjin Port terminal has also successively adopted automated crane equipment for operation. The Shandong Qingdao Port fully automated container terminal that has been put into actual operation is the first fully automated terminal in Asia. Within 7 hours of its first actual loading and unloading operation, 12 inland yard cranes were operating at the same time, and a total of 854 containers were loaded. The efficiency of 22 Move/H and the 3% failure rate per 100 loading and unloading containers have greatly improved the loading and unloading efficiency of terminal containers and increased their throughput capacity. Its economic benefits far exceed those of traditional manually operated cranes. The port has provided a strong equipment foundation guarantee to face the challenges of the world’s container shipping industry in the age of big ships. The fourth phase of the automated container terminal of Yangshan Port is the container terminal with the highest degree of comprehensive automation in the world, and it is also the largest fully automated container terminal in the world. Fully automated operation of container transportation and loading and unloading in the yard. Under the fully automated operation of unmanned cranes on the crane, 24-hour non-stop operations can be carried out. The loading and unloading efficiency of the entire terminal will reach 40 Move/H, which is far beyond the reach of traditional manual operations. Loading and unloading efficiency.
RTG’s container loading and unloading function has not yet been fully automated. The automated systems it is equipped with mainly include Global Position System (GPS), Container Position Detective System (PDS), Tire Crane Automatic Deviation Correction System ( Automated Guided Sling System (AGSS), truck anti-lift protection system (Chassis Lift Protection System, CLPS), container number recognition system (Container Number Recognition System, CNRS), etc. These cranes are semi-automatic cranes. The automation function is mainly embodied in the addition of some automation systems to assist the driver in the loading and unloading of containers, such as the cart operation assistance system, the trolley operation assistance system, the spreader pairing and the container loading self-assisted system, etc. These systems reduce cranes to a certain extent The manual operation of the driver improves the loading and unloading accuracy and speed of the crane, shortens the time for loading and unloading containers, and improves the operational efficiency of the entire inland yard. However, at present, this type of crane is still mainly operated manually and supplemented by automated system functions, and the fully automated operation of unmanned crane operation has not yet been realized.
RMG is currently the main form of container automation inland yard cranes in the world. Compared with RTG’s automation system, RMG is equipped with more automation systems and is more comprehensive. RMG’s automation systems mainly include automatic voice guidance system (Public Address, PA), truck lift protection system (Chassis Lift Protection System, CLPS), truck position scanning system (Chassis Alignment System, abbreviated as CAS), Container Number Recognition System (CNRS), Final Landing System (FLS), Crane Video Management System (CVMS), remote network vision system
(Remote Vision System/Network Video Recorder, RVS or NVR for short), Spreader Position Control System (SPCS), Spreader Profile Scanning System (SPSS), Truck number identification System (Prime Mover Number Recognition System, PMNRS for short). The unmanned fully automated RMG loading and unloading efficiency is very high, reducing the detention time of container ships, especially large container ships, and greatly increasing the container throughput of the port, thereby bringing huge economic benefits to the container port. At present, a single automation system has been integrated into one or more electrical system components. Automated port container inland yard cranes use RFID radio frequency identification, far-infrared ray sensor technology, position monitoring technology, laser scanning imaging and positioning, camera identification and Monitoring and other technologies carry out rapid information interaction through network communication protocols, so as to realize intelligent sensing, scanning, identification, positioning, monitoring and other operations. The article takes Singapore’s PSA Pasir Panjang terminal container yard automation RMG as an example to briefly explain the automation system of the container port inland yard crane.
1 Automatic human voice guidance system
When the truck enters the dedicated lane outside the yard and approaches the rail hoist, the moving truck will be guided by voice through the scanning and positioning system of RMG, so that the truck will arrive at an accurate parking position. When the truck needs to continue to move forward, the PA system will continue to send out the voice prompt of “forward”. When the truck arrives at the predetermined accurate position, the PA system will issue a voice prompt of “stop”; when the truck exceeds When the parking position is reserved, the PA system will continue to issue a “back” voice prompt, and the truck will retreat to the predetermined accurate position, and the PA system will issue a “stop” voice prompt. Through the voice prompt of the PA system, the driver can be guided to park the truck to a predetermined location in a short time, so as to ensure that the automated crane can perform fast container loading and unloading operations.
2 Anti-lifting protection system for trucks
When the RMG spreader is locked and the container loaded on the truck is lifted, if the lock on the truck that locks the container is not opened, the spreader will lift the container together with the loaded truck. The situation can easily cause damage to trucks and even threaten the personal safety of truck drivers. RMG’s CLPS system can scan the position of the truck. For example, when the CLPS scan truck rises to a height of 1 m above the safety setting, RMG will stop the lifting operation to automatically protect the truck, driver, and container. The role of.
3 Truck vehicle location scanning system
When trucks enter the RMG container loading and unloading area, the CAS system automatically scans the trucks. The CAS system can not only identify whether the trucks are single-deck trucks or double-deck trucks, but more importantly, It can scan and identify the moving position of trucks and interact with trucks’ position information and traffic lights. The lights and arrows of the traffic lights guide truck drivers to accurately move forward, back or stop, so that the trucks The truck arrives at the predetermined parking place in a short time so that the track crane can accurately and quickly carry out the grasping or loading action of loading and unloading containers.
4 Container Number Identification System
RMG saddle beams, outriggers, etc. are installed with multiple CNRS cameras that identify the front and back, side and top numbers of the container. When the truck loaded with the container arrives below the RMG side, the image of the container number is transmitted to the RMG through the camera function of the CNRS camera. CNRS system. After that, the CNRS system uses image recognition technology to identify, read and record the number of the container, convert the number of the container into numbers and letters that can be recognized by the computer, and transmit the read container number to the RMG control system and yard management system.
5 Carrying system
The FLS system uses cameras or lasers installed on the four corners of the spreader to identify the position of the container, and to identify and adjust the position of the spreader. The FLS system, which uses laser components as position detection, emits laser beams through the laser limits installed on the four corners of the spreader, and the four laser beams are parallel to the vertical four sides of the container. When the spreader moves, such as the laser beam irradiates the container, the FLS system will collect the feedback information of the laser beam, adjust the position of the spreader to keep the laser beam parallel to the vertical four sides of the container to be lifted, so that the spreader can Carry out the box movement accurately to avoid placing the spreader on the container slantingly.
6 Crane camera management system
The CVMS system uses multiple cameras installed on the RMG to monitor the yard conditions, lane conditions, and the operation of other RMGs in the same yard in real time, and synchronously transmit the monitoring images corresponding to each part to the CVMS system information processing center and the terminal. Control remote control operating room (ACOC for short). The CVMS system is a comprehensive management system for all the picture surveillance cameras installed by RMG. The system checks and monitors the storage yard, driveway, RMG operation and other conditions and status in accordance with the requirements of ACOC. At the same time, the CVMS system can also switch camera pictures as needed , To view and monitor the situation around RMG without blind spots.
7 Remote network vision system
The RVS/NVR system adds screen detection on the basis of the camera screen monitoring, and compares and analyzes the obtained real-time monitoring screen with the preset Video Encoder screen to detect whether the RMG’s hand and automatic operating conditions are within the set operating range Inside. The system also has the storage function of the monitoring screen, so that the monitoring screen can be called up for analysis later.
8 Spreader position control system
The SPCS system detects the position of the spreader and the container in real time during the lifting and lowering of the spreader through the two SPCS scanners installed under the RMG trolley frame and the reflective bottom plate installed on the spreader. When loading or unloading containers, the SPCS system automatically detects whether the position of the spreader and the container is tilted and instructs the spreader to perform tilt adjustment based on the detected position information, so as to ensure the position accuracy of RMG loading and unloading containers.
9 Container Stack Scanning System
The SPSS system is used to scan and detect the stacking layers and stacking height of a single row of containers under the RMG spreader. If the detected container stacking height needs to be consistent with the height set in the ABMS system, the container can be loaded and unloaded. Keep running. The SPSS system can also detect whether the parallel movement of the spreader will collide with the stack of containers. When the SPSS system scans and detects that the running spreader and container stacking height data is inconsistent with the height set in the ABMS system, the spreader It may hit the container stacked on the ground, and the SPSS system will stop the operation of the trolley and spreader, so as to prevent the RMG spreader from hitting the container in the yard.
10 Truck Number Recognition System
PM is used to connect quayside container cranes and RMG to transport containers within the terminal or external trucks. The loading and unloading of containers needs to identify, check and record the number of the front of the truck, which is the main function of the PMNRS system on RMG. Each truck is equipped with a tag with truck information on the front side of the truck. When the truck is close to the rail crane, the PMNRS system installed on the RMG saddle will read the tag of the truck through the RFID radio frequency identification function. The data on the label, so as to obtain the truck information.
In recent years, the construction of automated terminals in my country has developed extremely fast. Fujian Xiamen Yuanhai Automated Terminal, which has been put into actual operation, is my country’s first automated terminal and the subsequent Tianjin Port terminal has also successively adopted automated crane equipment for operation. The Shandong Qingdao Port fully automated container terminal that has been put into actual operation is the first fully automated terminal in Asia. Within 7 hours of its first actual loading and unloading operation, 12 inland yard cranes were operating at the same time, and a total of 854 containers were loaded. The efficiency of 22 Move/H and the 3% failure rate per 100 loading and unloading containers have greatly improved the loading and unloading efficiency of terminal containers and increased their throughput capacity. Its economic benefits far exceed those of traditional manually operated cranes. The port has provided a strong equipment foundation guarantee to face the challenges of the world’s container shipping industry in the age of big ships. The fourth phase of the automated container terminal of Yangshan Port is the container terminal with the highest degree of comprehensive automation in the world, and it is also the largest fully automated container terminal in the world. Fully automated operation of container transportation and loading and unloading in the yard. Under the fully automated operation of unmanned cranes on the crane, 24-hour non-stop operations can be carried out. The loading and unloading efficiency of the entire terminal will reach 40 Move/H, which is far beyond the reach of traditional manual operations. Loading and unloading efficiency.
[ad_2]