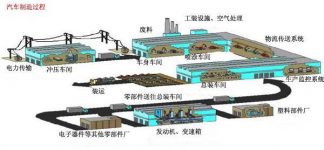
RFID automotive industry solutions
[ad_1]
Warehouse management:
Spare parts management: establish complete supplier delivery quality records and batch information: each supplier can carry out label records for the parts that each supplier enters the enterprise according to the electronic version, and understand its model, type, batch, production date, etc., Carry out warehouse-in and out-warehouse management.
Real-time monitoring of the production line:
Carry out the entire production process from the product entering the assembly workshop to the final inspection of the vehicleRFIDTracking management.
Cost Control:
Use modern logistics theory to improve the storage of auto parts and complete vehicles, save costs, and save the waste of production and temporary inventory in each workshop of the enterprise.
Product traceability:
my country has formally implemented the automobile recall system, which puts forward higher requirements for product traceability. Product traceability requires detailed production site records, including all aspects of production, quality, and materials.
According to the RFID tag information, the production and manufacturing information of each key station in the assembly workshop of the car can be inquired in real time, such as production time, operator, inspector, batch, serial number, quality data, process data, test data, etc., and understand Information about the manufacturing process, such as repair and processing results.
According to the RFID tag information, you can query the quality information of the car at important stations, including defect data and measurement data, as well as various data such as the process capability of the station;
According to the RFID tag information, it is possible to trace the quality information of the important parts and safety parts of the car, the information of the manufacturer of the main accessory parts, the specific details of the installation and other related information;
According to product information, it can be traced back to product batches and key component batches to find out other products of the same batch;
Upward can be traced to materials and components, and downward can be traced to end users.
Defect management:
The whole vehicle production is mainly assembled and involves a large number of parts (including in-house self-made parts and outsourced parts). Various defects will inevitably occur during the assembly process. Some of them come from parts, some are produced in this process, and there are also previous processes. produced. In order to improve the quality and reduce the repair rate, it is necessary to monitor the defects of each car in real time, record them in real time, and take timely measures.
Application effect:
1. The electronic tag can be read multiple times (up to 100,000 times)
2. RFID electronic tags can be stably read by the reader (low error rate).
3. A lot of manpower and time can be omitted.
4. The command of the main system to the production process is comprehensively improved.
5. The whole production process and the main system are connected together, and the production efficiency is greatly improved.
Principles of the plan
Establish a unified central database on the site of the enterprise workshop as an information platform for the circulation of goods to facilitate overall standardized management. In the industrial link, RFID technology is used to assign an identification number (ID) to each work-in-progress component, which is the name of the component in the information network. Through RFID technology, the production status and inventory status are mapped to the information network and registered in the information network. In the field center database, it is transmitted to the information system (such as ERP, MRP), etc.
basic structure
A typical RFID automatic identification system consists of the following parts: data carrier, read/write unit and interface module. The interface module is connected to PLC, PC and other control units by bus or serial communication.
[ad_2]