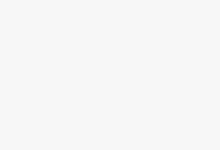
Wireless remote single lamp control system
[ad_1]
The existing urban lighting control system generally adopts multiple switch cabinets to control the entire city lights in pieces. Each switch cabinet is generally responsible for the “on” and “on” and “Off”, “On” is fully open, and “Off” is fully “Off”. As a result, not only is it often impossible to adjust and control the number of lights on and off and the specific working methods of each light according to actual lighting needs, but also, when a street light or line is damaged or stolen, The control center could not find and deal with it in time. As a result, there is not only a large amount of energy waste, (this is obviously not consistent with the spirit of our country and the whole world, which regards energy conservation and emission reduction as a top priority), but also because of the need to accurately find the damaged lights and wiring equipment In order to arrange personnel for timely repairs, the management department often sends a large number of vehicles and personnel to conduct manual inspections every night. This approach not only requires a large amount of manpower and material input, but also greatly increases the operating and management costs of the management department. It is also inefficient and is basically useless to prevent theft.
Based on this need, Beijing Sulian Technology, using its own unique technology, newly developed a wireless remote single-lamp control system. This system can be directly connected to the monitoring center computer through the central control module, and the wireless public network (GPRS/CDMA1x), wired public network (ADSL), local area network (RS485/Ethernet), or RS232 interface connected to it, So as to realize the independent control of each lamp and other facilities within a radius of 1000-2000 meters with the central control module as the center, and automatically detect and report whether each lamp is working normally, whether there is abnormality (theft), and The control of other working parameters of the controlled lights effectively reduces the energy consumption and eliminates the trouble of manually searching for faulty lights. At the same time, it can detect the theft of the equipment in time, so that the management department can deal with it in time. Greatly improve the work efficiency of each lamp, and the overall system management efficiency. Undoubtedly, this system will bring you higher efficiency! More returns!
The content of system control includes:
“On” and “Off” of controlled lights;
Detect the current of a single lamp in real time to determine whether the lamp is working and how many lamps are working;
Can provide light temperature monitoring (+/- 0.5C);
Multi-channel control interface can be provided to control other working parameters of the lamp, such as controlling the adjustable brightness rectifier;
In order to avoid the need of urban lighting when the central control module fails, the single-lamp control terminal will automatically restore the controlled lights to the original system working mode when it detects that the wireless connection with the control center fails. The control range depends on the working environment of the control system, the antenna gain used, and the antenna installation height.
1. Operation manual and wiring relationship of remote single lamp control system
1. Terminal module wiring relationship (as shown in the figure)
620)this.style.width=620;” border=0>
1>. This control terminal equipment is driven by 220v AC mains power.
2>. Place the terminal control equipment in the direction shown in the figure above (the opening of the terminal is over), and the two terminals on the right of the above figure are respectively connected to the live and neutral wires of the 220V AC power supply.
connect.
3>. The live wire of the controlled lamp is connected to the second terminal from the left in the figure above (light control wire output live wire).The zero line of the lamp is connected to the first terminal on the right in the figure above (AC
Input terminal 220V zero line) phase connection. The first terminal on the left is connected to the ground.
4> The maximum power of the lamp that can be controlled by this control device is 2000 watts (10 A)
5> This terminal control equipment is a test product, and the outer package size can be adjusted according to user needs.
Note: The wiring relationship of the terminal module must be connected strictly in accordance with the provided wiring relationship.
Second, the central module serial port test assistant operation
1. The wiring relationship of the central module (as shown in the figure)
620)this.style.width=620;” border=0>
2. Operation steps
●Start the computer
●Start the test software (serial port debugging software SSCOM3.2)
●Connect the module
●Settings of serial port debugging software
●Turn on the module power
●Use serial port for wireless control of the module.
3. Operating software usage and settings
1>, the setting of the serial port number (according to the user’s computer)
620)this.style.width=620;” border=0>
2>, the baud rate setting (the baud rate setting must be consistent with the baud rate of the module)
620)this.style.width=620;” border=0>
3>. Our data is hexadecimal, so hexadecimal is required to send and receive.
620)this.style.width=620;” border=0>
4>. Enter the data to be sent into the send data box, and click send. The receiving area of the receiving module should receive the same data sent.
620)this.style.width=620;” border=0>
5>. The blank area at the top of the test software interface is the receiving data area.
3. The setting command and communication format are as follows:
1. Data communication parameters
Baud rate: 9600
Data bits: 8
Parity check; none
Stop bit: 1
2. Data packet format: packet header + command word + terminal ID number + switch flag + verification
Description Baotou (2B): 55 AA
Command word (1B): 01 control command
02 Status detection command
Terminal ID (1B): FF means all control
00~FE means designated street light number control
Switch mark (1B): 00 means off
01 means even off and odd bright
02 means odd off even bright
FF means bright
Check (1B): the sum of all the previous data
3. Examples of commands
1>, the designated No. 1 light is on: 55 AA 01 01 FF 00
Designated No. 1 light off: 55 AA 01 01 00 01
2>. Designate all lights to be on: 55 AA 01 FF FF FE
Assign all lights off: 55 AA 01 FF 00 FF
3>, specify even off and odd on: 55 AA 01 FF 01 00
Specify odd off and even on: 55 AA 01 FF 02 01
4>, read the status of No. 1 street light: 55 AA 02 01 00 02
Return the current of No. 1 street lamp: 55 AA 02 01 XX VV (XX is the current value, VV is the calibration)
5>. Data packet error response: 55 AA AA AA AA AA
Note: When the central module separately controls the terminal modules, the ID number of the sending control terminal must be the same as the ID number of the terminal module, otherwise it cannot be controlled.
Fourth, the connection between the central module and the control center
1. The central module can be directly connected to the control center computer through RS232 or RS485 bus (local area lighting control);
2. The number of single lights that can be controlled by the central module is basically unlimited, as long as the controlled lights are within the wireless communication range between the central module and the control terminal module; generally 100-
1000;
3. The central module can be connected to the monitoring center through the mobile public network through the GPRS/CDMA1X module (the two can be connected by a serial port for wired connection);
4. The central module can be connected to the control center computer through ADSL, Ethernet or its own wireless relay.
Five, use, maintenance and precautions
use
1>. Make sure that the power supply is correctly connected before turning on the power, and pay attention to the power supply voltage not to exceed 240VAC.
2>, confirm the data line interface; RS232.
3>. Ensure that all wiring must be effectively connected.When using the RS232 to USB interface cable, you must pay attention to the normal operation of the adapter cable (the general adapter cable on the market has more problems.
Much), before making a wireless connection, it is best to use wired communication to check whether the patch cord is working properly?
maintain
1>. The module has no user-maintainable parts, and the user is not allowed to disassemble the module by himself. Avoid hitting, squeezing the module and causing physical deformation of the module during transportation or installation.
Precautions
Attention should be paid to the distance test of the module:
1> Test environment: There should be no shelter between the two test modules, including vegetation (dense vegetation has a greater impact on the communication distance); the virtual connection between the two modules is separated
The farther away from the ground, the better, the closer to the ground, the closer the transmission distance; dense vegetation absorbs more transmission signals, so in actual use, avoid two modules as much as possible
They are all placed in the woods, and at least one of them should be installed at a high place outside the vegetation to reduce the thickness of the radio frequency signal penetrating the vegetation.
2>. The height of the module (above 3 meters) should be maintained during distance testing, and the antenna should be installed perpendicular to the ground; metal objects close to the built-in antenna will affect the communication of the module.
The signal distance, the built-in antenna should be at least 3mm away from the metal surface, the closer it is, the greater the impact. When using an external antenna, if you need to install the antenna on a metal surface,
The antenna must be perpendicular to the mounting metal surface, otherwise it should be a certain distance away from the metal surface. DC power supply must ensure that the ripple of the power supply is less than 30 millivolts, and it is best to use a battery for power supply.
3>, RS232 we have a standard DB9 connector, which can be directly connected to the PC serial port.
Six, common problems
When you follow the aforementioned steps, connect the modules (including power-on), and start the serial port test program for control testing. On the serial port test software interface, after sending data, the terminal control has no corresponding response.
1. Check the power supply line: whether the power supply line is effectively connected, whether the power supply is supplied according to the requirements of the module, and whether the power supply voltage is normal (a multimeter can be used
test).
2. Check the data line: check whether the data line is correctly and effectively connected—determine the interface of the data line.Then follow the wiring relationship provided by us to ensure that there is no
error. If an RS232 to USB interface adapter cable is used, the adapter cable should be used to check whether the wired signal transmission works normally, otherwise the adapter cable should be replaced.
3. Check the settings of the serial port test software: for example; whether the selection of the serial port is valid, the determination of the baud rate, the determination of the data format, and the determination of whether it is hexadecimal sending and receiving
receive. (For specific operations, refer to the use and settings of the serial port operating software)
4. Check whether the baud rate is correct.
5. Whether to choose hexadecimal for sending and whether to choose hexadecimal for receiving.
When the module is controlling the terminal, it can be controlled, but the distance is not enough.
1. Check whether the power supply is supplied as required (if you are using a general battery to supply power, please check the voltage of the battery. When checking, check the voltage with load; if you use it)
For other power supplies, including AC power, solar battery power, and battery power converted by a transformer circuit, you need to check whether the auxiliary circuit brings noise, that is
After these auxiliary circuits, whether the ripple coefficient of the power supply can still meet the requirements (the ripple must be less than 20 millivolts). This is also the most easily overlooked and problematic place.
2. Check the connection of the radio frequency line: whether the antenna is intact, whether the connection part is tightly connected, the installation position of the antenna includes the distance from the metal body and the installation direction (generally required
See if the vertical metal surface and the ground), antenna installation direction and test environment, etc., meet the requirements in the preceding precautions.
3. Check whether there is a strong interference source near the test: WIFI and other 2.4Ghz, communication equipment, although national regulations, in urban areas, use 2.4Ghz frequency band wireless communication equipment
The maximum transmit power should be less than 0.1 watts. This limit can be exceeded in the suburbs but needs to be filed. However, in reality, violations are very common. When our test system,
It is very close to other high-power 2.4G transmitters, and when the channels used overlap each other, the communication distance will also be affected.At this point, we can change to another environment to test
Try, or install our antenna as far away as possible from the interference source antenna (note that in theory, the signal strength is inversely proportional to the square of the distance) or use a directional antenna to reduce
Less such interference. If it is impossible to avoid such interference, we can also choose a new channel, as far as possible from the frequency of the interference source. (Our company will launch low-cost
Clean channel detector)
Seven, working environment parameters
1. Module working temperature: -35℃~+75℃.
2. Rated voltage: AC 220V±10%.
3. Relative humidity: ≤90%.
[ad_2]