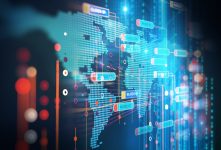
Realize batch warehousing management of machinery and tools through RFID technology
[ad_1]
Smart warehousing is one of the core technologies of modern smart logistics. It is composed of high-rise shelves, laneway stacking or multiple wagons, a variety of storage and exit peripheral equipment, electrical control systems, and warehouse management systems. It can realize automatic storage and management of goods. Improve storage space utilization, work efficiency, and management level. The material management cost is greatly reduced, and the optimal management of warehouse materials can be realized.
1. Introduction to Smart Warehouse Management System
The intelligent warehouse management system is an intelligent system composed of three-dimensional racks, tracked roadway stackers, in and out conveyor systems, information identification systems, automatic control systems, computer monitoring systems, computer management systems and other auxiliary equipment. The system adopts the design of first-class integrated logistics concept, and realizes automatic warehousing operations by coordinating various equipment actions through advanced control, bus, communication and information technology applications. The smart warehouse management system adopts barcode technology and automatic identification technology to create, can seamlessly integrate PDA equipment, SAP system, ERP system, TMS system, etc., to ensure that the system covers all business functions of the enterprise, and real-time information sharing. Coupled with the flexibility, stability and integration of the system, the lean management of the enterprise from business to warehousing is realized.
2. Application value of smart warehouse management system
Smart warehousing management system, a real-time warehousing operation management system specifically designed for enterprise warehouses or distribution centers, covering order management, picking management, receiving management, moving warehouse management, replenishment management, inventory management, personnel performance, and location management , Transportation management, supplier management and report management.
1. Reliable delivery: upload information to the system safely, accurately and efficiently.
2. Intelligent control: Intelligent and precise control of the equipment to achieve refined management.
3. Data fusion: Through its own data processing capabilities, it can process more meaningful information and increase the reference and basis for decision-making.
4. Data recording: Record various data in the warehousing management business, accurately predict the possibility of empty warehouses and warehouse explosions, and make preparations in advance.
5. Reliable integration: integration between the system and third-party software, integration of data collection terminals and business processes, etc.
6. Operation analysis: Record the management behavior data in the warehousing operation process, and optimize the warehousing process management.
3. Advantages of Smart Warehouse Management System Solution
The intelligent warehousing system solution is based on the premise of improving the management level, management precision and operational efficiency of the TOT LCM module warehouse and the GOC domestic sales warehouse. Combining RFID technology, the use of pallet pallets as the finished product storage carrier, and the use of pallet RFID The way the label and the pallet bar code are associated, it is convenient and quick to use RFID tags to realize automatic information collection, verification and error correction in the links of inbound, outbound, inventory, transfer, and transfer, and at the same time realize the unification of information flow and physical logistics .
1. Elevated storage to save land: In China where the “land king” is frequently present, land has become a scarce resource. How to maximize the use of limited land has become the goal of some companies. The intelligent storage equipment system uses high-level shelves to store goods, maximizes the use of space, and can greatly reduce land costs. Compared with ordinary warehouses, ordinary intelligent three-dimensional warehouses can save more than 60% of the land area.
2. Unmanned operation and labor saving: In China, where the cost of human resources is increasing year by year and the demographic dividend is gradually disappearing, the intelligent storage equipment system realizes unmanned operation, which can not only greatly save human resources and reduce labor costs, but also better Adapting to the needs of dark, low temperature, toxic and other special environments, so that the intelligent storage equipment system has a broader application prospect.
3. Machine management to avoid losses: The intelligent storage equipment system uses computers for storage management, which can record and monitor the data of incoming goods, and can achieve “first in, first out” and “automatic inventory” to avoid natural aging and deterioration of goods , It can also reduce the loss caused by the damage or loss of the goods.
4. Account and reality synchronization, saving money: The smart storage equipment management system can achieve account and reality synchronization, and can be integrated with the corporate intranet. Companies only need to establish a reasonable inventory to ensure the entire production process is smooth, thereby greatly improving the company’s cash flow, reducing unnecessary inventory, and at the same time avoiding wrong accounts, missing accounts, bad accounts, and inconsistent accounts caused by human factors. problem. Although the initial investment of the smart storage equipment management system is relatively large, it can benefit from a long-term investment and can save funds on the whole.
5. Automatic control to improve efficiency: The entry and exit of items in the smart storage equipment system is automatically controlled by a computer, which can quickly and accurately transport the items to the designated location, reducing the waiting time for vehicles to be loaded and unloading, which can greatly improve the warehouse Storage turnover efficiency, reduce storage costs.
6. System management and image enhancement: The establishment of a smart storage equipment system can not only improve the system management level of the enterprise, but also enhance the overall image of the enterprise and its position in the minds of customers, win a larger market for the enterprise, and create more Great wealth.
Four, smart warehouse management system program function
The smart warehouse management system is an efficient tool for warehouse video operation events. According to the “real-time” video or warehousing files, disputes in the process of loading and unloading, receiving, and transporting products can be resolved, product availability can be determined, and inventory damage can be investigated. Managers can view and search for events in synchronization with the video surveillance system.
1. Location management: Use PDA equipment and barcode technology to scan the upper and lower shelves of the location management, which can quickly bind and release the location, realize the adjustment of the commodity location anytime and anywhere, and display the location adjustment quickly and in real time based on the Kanban Condition.
2. Sorting management: Usually the warehouse area is large, and the walking distance of personnel is relatively long. The system uses scientific sorting management to improve personnel efficiency and sorting accuracy, and reduce subsequent maintenance pressure.
①Can prompt the location information, sorting does not need to find the goods;
②The system automatically arranges the priority picking path to reduce the walking distance of personnel;
③The system carries out automatic warning and intelligently prompts replenishment information, so there is no need to wait for picking;
④Information prompt on the system shelf to ensure the accuracy of the warehousing information;
⑤ A variety of inventory methods, support cycle inventory, random inspection inventory, daily inspections, etc.;
⑥ Sorting while sorting, the intelligent system sorts information, so that operators will not take the “wrong way” and improve efficiency.
3. Process management: The smart warehouse management system is a control and management oriented to the whole process. Operators use PDA barcode guns to realize the sorting operation, which can realize the entire operation record (picking, packing, shipping, receiving, shelves, replenishment, inventory, etc.). After the sorting list is completed, the system will immediately generate multiple dimensions Employee performance report data (number of jobs, weight, volume and other information, and arrange them), scientifically and easily realize performance registration and assessment. At the same time, the warehouse on-site Kanban can display information, improve the enthusiasm of the staff, and let the staff work consciously.
4. Diversified warehouse management methods: material SKU management, batch management, unique management, box code management, etc. can be realized. It meets the storage management needs of enterprises with a large variety of materials, high frequency of storage and retrieval, and high requirements for shelf life and traceability.
5. Inventory management: Accurate inventory control can be achieved. By setting the upper and lower range values of the inventory, the number of days before the shelf life, etc., the quantity and status of the goods can be grasped in time, so as to carry out reasonable purchases and sales, and achieve the goal of “zero inventory”.
Five, the structure of the smart warehouse management system
The intelligent logistics warehousing management system adopts computer control and management technology to maximize the functions of the three-dimensional library, and can provide enterprises with complete logistics automation solutions from storage, automated transportation, automated production to finished product distribution.
1. Automated conveying system
The moving line parameters are determined according to the processing capacity and upper limit parameters. The width of the general box-type sorting system is 580/620/680/720/780, and the width is determined by the physical size of the goods transported on the moving line. The weight is related; for example, it involves the carrying capacity of the line body, the power selection of the motor, etc. Generally, about 2500 boxes/hour are selected, and the commonly used speed is 32 meters/minute.
2. Automated warehouse
The speed of the pallet stacker is generally below 180 m/min, while the miliload can achieve a maximum of about 240 m/min, and the maximum access times can reach 250 times/hour, generally 200 times/hour. The height can be up to 30 meters, generally less than 24 meters, basically 24 meters and 21 meters; the multi-layer shuttle has a storage capacity of up to 1000 times per hour.
3. AGV sorting robot
The AGV sorting matrix is mainly used in the unmanned warehouse of JD. The concept of the unmanned warehouse is more advanced, but the large-scale application of this small yellow man matrix sorting system is not cost-effective, with high failure rate and background The scheduling program algorithm is complex; and this matrix AGV sorting system belongs to the two-dimensional code navigation, and there is a bottleneck: the more AGV carts, the processing capacity will decrease.
4. Automatic sorting system
Slider sorter, used for box-type sorting, cannot be sorted for goods with flexible packaging; cross-belt sorting, mainly used in subdivision areas, can provide more grid openings, and run at a higher speed , The sorting capacity can be 20,000-40000 pieces, or even higher; a single piece of equipment generally does not exceed 30,000 pieces……
5. Electronic label system
It is mainly used for seeding and fruit picking to solve the problem of sorting error rate. This kind of error rate is low, which effectively improves the efficiency of sorting; the error rate of the general electronic label system is less than five ten thousandths, and the electronic label system is applied. It is more efficient than manual sorting.
6. Dense storage system
I mentioned two kinds of vertical and horizontal rotating warehouses. The vertical rotating warehouse can generally be used on a stand-alone machine, while the horizontal rotating warehouse needs to be used in combination, and its efficiency is 6-10 times higher than that of manual labor. Because the dense storage system can increase the storage density by about 50%, the storage space it can save can reach 50%-60%. At present, the dense storage system is not used much in the e-commerce warehouse.
7. Goods-to-person system
Specifically refers to AGV goods-to-person, carrying shelves to move; there is also a goods-to-person system called an online picking workstation, generally up to 1000 pieces/hour, traditional picking 70% of the time is spent walking, 30% of the time is spent Picking is inefficient; using the goods-to-person system will greatly improve efficiency.
8. Online robot sorting system
The main problem is that the price is relatively high, and the cost-effectiveness is not high for the storage industry, and the efficiency cannot be compared with the manual; but there is an advantage that it can be hyped, and it is good for the image of one’s own brand. The rookie appeared, and other e-commerce warehousing used very little.
6. Technical Features of Smart Warehouse Management System
Smart warehousing can realize real-time understanding of warehouse environment temperature and humidity, abnormal fire-fighting facilities, etc., once there is an abnormal situation, it will be notified in time through various methods such as SMS, APP, internal system, etc; Occurs; visualized operation and maintenance, statistical power consumption, power trend display; energy saving and power saving, remote inspection or control of Internet of Things equipment, unified management and control of the platform, reducing unnecessary waste. You can also choose a combination of strategies according to actual application scenarios to achieve intelligent and automated control of all IoT devices. The mobile APP can view the status in real time, receive alarm information, and operate and maintain anytime, anywhere, all under control.
1. Establish a basic information database of machines and tools
Import or input the basic information of all new warehouse equipment into the system platform in batches. This work can be filled in by each warehouse, and the system will automatically generate a unique equipment code (coding rule: W/H date + date + warehousing serial number). Basic information table.
2. Laser QR code printing to realize the sharing and query of machine tool information
Using the two-dimensional code technology, generate the two-dimensional code label from the basic account (basic information table) of the machine in the system. Since the ordinary QR code printing and sticker labeling methods have problems such as easy falling off and corrosion, it will seriously affect the management of machinery and tools. Through investigations, laser printing can achieve anti-corrosion, anti-dropping, and can be directly printed on a variety of materials including metal products, without media, and specially choose to use laser printing to print the QR code to the appropriate position of the machine. Personnel at all levels can scan QR codes and view information on the on-site machinery and equipment through the APP scanning function in the later stage, and warehouse management personnel can also scan the equipment in and out of the warehouse by scanning the QR code.
3. Realize the batch warehousing management of machinery and tools through RFID technology
Since the two-dimensional code access management method can only scan and exit the warehouse for a single machine, the efficiency is greatly reduced. After investigation, based on RFID wireless communication technology, it is possible to embed or post microchips (RFID electronic tags) on machines, and write the basic information of the machines into the RFID electronic labels in batches, and use radio frequency technology to inductively identify, read and analyze the machines. For detailed information, realize the batch warehousing management of machinery and tools. Implement the RFID electronic label method for management of the equipment with high circulation frequency and not easy to damage.
4. GPS positioning tracking management
For key control equipment (such as tractors, safety protection equipment), install GPS positioning device to achieve rapid positioning and tracking of on-site equipment, and mark and display on the electronic map of the system platform. The APP uses the company’s Yianbao system to realize the positioning and navigation of the equipment.
5. Customize the design of the warehouse identification door
According to the size of the warehouse gate, the non-contact entry and exit door design is carried out, and multiple RFID identification reading and writing devices and antennas are installed, which can quickly identify the chip information of multiple machines (1-200 chip information) at the same time, and display it on the display screen. It can view and display the detailed information of the equipment, and can also automatically generate and print the warehouse receipt, which is quick and convenient to operate.
6. Large screen display
Install a large display screen at a suitable location in the warehouse, and establish a comprehensive display platform to display real-time, unified and dynamic display of the equipment acquisition, inventory, repair and test, scrap and other conditions in the warehouse management on the large screen.
With the continuous development of business scale, the types and quantity of machinery and tools are also increasing, the frequency of in and out of the warehouse is increasing day by day, and the requirements of warehouse management are also complex and diverse. The traditional manual warehouse management mode and data collection method have been unable to meet the current rapid warehouse management. , High-efficiency, accuracy and error-free requirements, and gradually become a major obstacle restricting the development of enterprises. In view of this situation, it is necessary to research and design a set of efficient and intelligent warehouse management system with omni-directional perception, safe synchronous transmission, and visual reproduction.
The smart warehouse management system is a real-time warehouse operation management system specifically designed for enterprise warehouses or distribution centers. It covers order management, picking management, receiving management, moving warehouse management, replenishment management, inventory management, personnel performance, and warehouse management. Position management, transportation management, supplier management and report management and other links. Intelligent warehouse management system to realize optimal warehouse management.
Smart warehouse management system is produced with the continuous upgrading and reform of information technology. Although many companies have not realized the convenient and fast characteristics of smart warehouse management system, its role in warehouse management is unquestionable. Its application It laid a solid foundation for the subsequent creation of smart power plants. At present, the application of smart warehouse management systems in power companies is in its infancy, and many functions need to be continuously improved. However, as more and more companies continue to improve their research and understanding of smart warehouse management systems, smart warehouse management systems will surely be more widely recognized and applied.
[ad_2]