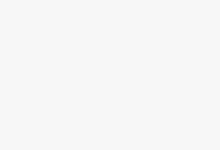
General solution for rfid logistics industry
[ad_1]
1. The status quo of modern logistics management of Chinese enterprises
The modern logistics industry, as an emerging compound industry, has been developing rapidly in my country, and the demand for social logistics has continued to grow at a high speed. The added value of the logistics industry has steadily increased, and the total cost of social logistics has stabilized. Market competition is becoming increasingly fierce, and improving production efficiency and reducing operating costs are of vital importance to enterprises. At present, warehouse management systems usually use barcode labels or manual warehouse management documents to support their own warehouse management. However, the bar code’s characteristics such as easy copying, non-fouling, non-moisture-proof, and cumbersome operation, and the cumbersome nature of manual document writing, are likely to cause human losses, which make the current domestic warehouse management always have defects.
The application of radio frequency identification (RFID), the latest technology product, can fundamentally solve the above-mentioned problems. According to the actual situation and needs in logistics, RFID solutions for the logistics industry have been developed.
1.1. Traditional management concepts affect the improvement of logistics efficiency
Affected by the traditional planned economic system, many Chinese enterprises still retain the “big and complete”, “small and complete”, “integration of production, supply, and sales”, “one-stop warehousing and transportation” business organization, logistics organization The activities mainly rely on the self-service completion of the internal organization of the enterprise, so that the procurement, warehousing and distribution functions cannot be fully integrated, and the integrated internal supply chain management cannot be implemented. This is not conducive to the socialized professional division of labor. This decentralized, low-level management Activities will inevitably lead to unclear logistics cost responsibility subjects, and it is difficult to highlight the benefits of logistics management.
1.2. The enterprise’s understanding of logistics services is not comprehensive and profound enough
With the development of the economy, customers’ requirements for logistics services are becoming more and more individualized and diversified. Logistics services have become an important part of a company’s sales differentiation strategy. However, when many enterprises in our country formulate logistics service elements and service levels, they evenly distribute limited logistics service resources to all customers and all products, which often affects the specific logistics service performance and the resulting customer satisfaction. In addition, the logistics service management is only carried out by the logistics department alone and the implementation of the logistics service is not checked regularly, etc., which affect the value realization of the logistics service.
1.3. The management methods of enterprise logistics are backward
First of all, the logistics infrastructure of my country’s enterprises is not yet perfect. The old storage facilities have single capacity, obsolete equipment, low operating efficiency and low operating quality, which are difficult to meet the needs of modern logistics industry operations. Secondly, due to the low level of logistics infrastructure and equipment, and the lack of unified and standardized standards, it is difficult to achieve an integrated and full flow of goods in the transportation, loading and unloading, and warehousing links. Furthermore, the application and popularity of modern information technology in my country’s logistics field is not high, and the development is not balanced. There is no information interface between enterprises, and it is difficult to realize the networking and supply chain management between logistics enterprises and users. In the modern logistics management of enterprises, many enterprises are still stuck in the era of paper and pen. Although some enterprises are equipped with computers, they have not yet formed a system, let alone a network. At the same time, they lack expertise in EDI, personal computers, and artificial intelligence in logistics operations. With the application of advanced information technologies such as systems, communications, bar codes, and scanning, the level of automation in logistics operations is low.
2. Application of RFID in the logistics industry
In RFID system management, electronic tags are affixed to the packaging or pallets of each goods, and the specific information, storage location and other information of the goods are written in the tags. At the same time, when the goods enter and leave the warehouse, the detailed information of the delivery party can be written, and fixed or hand-held readers are installed in the warehouse and each distribution channel to identify and detect the circulation of the goods. This system can be selectively used in various business links and processes from procurement, storage, manufacturing, packaging, loading and unloading, transportation, circulation processing, distribution, sales to service. Enable companies to accurately grasp the flow and changes of business flow, logistics, information flow and capital flow in the entire supply chain in real time. The following mainly introduces the specific application of RFID technology in logistics management in the four links of procurement, warehousing, retail, and transportation:
2.1 Purchasing link
In the storage link mentioned above, there are card readers on each shelf of the warehouse. The card reader can read the classification and quantity of the goods on the shelves read by the card reader, and the system can set a limit value. When the quantity of goods on the shelf reaches this limit value, the reader will send out an alarm to remind the warehouse management staff to pay attention to the purchase. At the same time, the system will notify the purchaser through a variety of transmission methods, which goods are out of stock, need to be purchased, and the quantity to be purchased. After receiving the notification, the purchasing staff can purchase the corresponding goods according to the prompts. After purchasing, hand over the goods to the warehouse management staff to complete the warehousing and other links mentioned above. So far the procurement process is over.
System advantages
√Inventory quantity setting;
√Timely notification of out of stock;
√ Multiple notification methods;
√The buyer accurately obtains out-of-stock information;
√Accurate procurement;
√ Put in the warehouse in time after the purchase, which is accurate and convenient;
√Data can be checked at any time.
2.2 Warehousing
In the radio frequency antenna working area, all data on the RFID tag of the goods (such as manufacturer, product name, quantity, batch number, code, production date, shipping address and destination address) are transmitted to the reader through the antenna, and finally input to the computer In the database, it realizes efficient background information management, intelligently manages the goods in the successful warehouse, and can also monitor the temperature and humidity of the warehouse.
As shown in the figure:
Warehousing link
2.3 Retail Link
The RFID reader will automatically scan the product information purchased by the consumer, pass it to the terminal management system, and then directly deduct the payment from the consumer’s credit card. Through this system, it is possible to accurately track the sales and inventory of various commodities and place orders at the right time, thus shortening the ordering cycle, meeting customer needs in time, and greatly improving the quality of service.
Using RFID tag information, retailers can better provide after-sales service to consumers, even if the customer’s shopping credentials have been lost. Retailers can provide services to customers by accessing the RFID tag information of commodities in the back-end information management system, which is also conducive to determining the link causing the problem.
The following problems are mainly solved in the RFID retail link:
(1) Reduce items out of stock and increase shelf utilization
What goods to supplement, when to supplement, and the specific quantity to be supplemented. A certain percentage of out-of-stocks is caused by poor shelf management. This seemingly small proportion often causes millions of dollars in losses for the enterprise, and is even an important factor affecting the survival of the enterprise. Smart tags can monitor the expiration date of some time-sensitive commodities. In this way, using RFID technology, manufacturers, logistics providers, and retailers can grasp the real-time inventory of commodities, replenish them in time, and shorten the inventory turnover period.
(2) Strengthen product safety management
According to the instant information provided by the electronic label, the supermarket administrator can learn about the relevant information of the product, such as whether the product is fresh and has a value. The use of RFID electronic tags to implement supply chain management for fresh food greatly saves resources, improves efficiency, and can carry out full control of food to ensure food safety.
(3) Improve data collection
As the amount of data processed by retail managers continues to grow, so does investment in information technology. Several key areas where retail companies invest in additional information technology include supply chain, customer management, and data warehouse solutions, all of which require a large amount of accurate data as a basis.
(4) Reduce labor costs
At this stage, labor costs in my country’s retail industry account for more than 30% of total costs. The design of RFID can realize the automation of commodity registration, no manual inspection or scanning of barcodes is required during inventory, which is faster and more accurate. When shopping, you only need to select the goods you want and put it into your shopping cart. At the exit of the mall, the scanner can scan the entire vehicle with RFID tags at one time, and it can automatically read from the customer’s settlement card Deduct the corresponding amount, this process is done automatically, no cashier is required.
2.4 Transport link
The RFID tag installed on the outer packaging of the goods has GPS+gprs function on the label, which realizes the specific positioning of the goods, and also realizes the visual management of the transported goods, and understands the specific location of the goods in real time. If the GPS/GIS system is used in conjunction with it, full information monitoring and tracking of the transportation process can be realized.
3. Product selection
3.1 Label selection:
There are many types of equipment in logistics, with different specifications and mainly divided into a few categories. Among them, metal and liquid are the problems that RFID has always needed to solve. The carton label is 4*2, 4*4, 4*6 Label made by E41B , Pallets and some metal outer packaging goods can use anti-metal labels.
Label selection
3.2 Reader type selection:
Fixed reader
Impinj Speedway reader, Impinj Speedway revolution reader, Impinj xPortalRFID integrated reader.
Fixed reader
Handheld
Handheld
[ad_2]