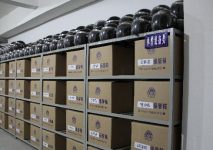
Intelligent management system of Internet of Things public installation and standby database
[ad_1]
1 System background
1.1 Project background
Over the years, with the continuous acceleration of the process of scientific and technological development, my country’s informatization construction has made considerable progress, and the military, judicial, public security and other state departments have begun to build warehouse systems. In this regard, Chuangyi Technology has a relatively complete set of plans for the management of the information system of the Ministry of Public Security’s equipment warehouse. The main characteristics of public equipment warehouse management are: fewer people and more materials, and diverse materials. Therefore, materials need to be managed in different ways according to specific conditions and management requirements.
Therefore, we must prioritize the establishment of a management system for the combat readiness warehouse, and use the application of the system as a starting point to gradually realize the intelligentization of the military’s logistics support.
Traditional warehouse management generally relies on a non-automated paper document-based system to record and track incoming and outgoing goods. The internal management of the warehouse is completely implemented manually, so the efficiency of warehouse management is extremely low. In this regard, we use a warehouse intelligent management system based on ZIGBEE wireless radio frequency technology, which can enhance the accuracy and speed of warehouse operations, and reduce the illegal entry and exit, misplacement, and theft caused by inadequate management of the entire combat equipment in and out of the warehouse. And the loss of inventory, shipment errors, etc., and minimize storage costs to ensure the safety of war preparations.
2 Demand analysis
Traditional warehouse management generally relies on a non-automated paper document-based system to record and track incoming and outgoing goods. The internal management of the warehouse is completely implemented manually. Therefore, the efficiency of warehouse management is extremely low, and the warehouse that can be managed The scale is also very small.
With the popularization of computer applications, most of the enterprise warehouse management data materials have begun to use computer data systems for management, but the data is still collected and statistically organized by first recording on paper and then manually inputting it into the computer. This not only causes a lot of waste of human resources, but also due to human factors, the data entry speed is slow and the accuracy rate is low.
With the continuous development of the Ministry of Public Security’s intelligence, the number of material types and machines managed by public installations and warehouses is increasing, and the frequency of in and out of the warehouse has increased sharply. Warehouse management operations have also become very complex and diversified. The traditional manual warehouse operation mode and data collection method It has been difficult to meet the rapid and accurate requirements of warehouse management, which has seriously affected the efficiency of the Ministry of Public Security.
At the same time, in recent years, there have been many problems in material transportation and vehicle management, such as few records, missing records, and private vehicles. More and more people have not only caused a serious loss of materials due to this omission, but also formed work habits in the Ministry of Public Security that are extremely unfavorable to long-term development due to inadequate management measures, which have seriously affected the development of intelligence and modernization.
At present, ZIGBEE technology is bringing a huge change to warehouse management, to identify the incomparable advantages of barcodes such as long distance, fast, hard to damage, and large capacity, simplify the complicated work process, and effectively improve the efficiency and transparency of the supply chain. China·Chuangyi Xingsheng Technology Development Co., Ltd. is based on the Internet of Things intelligent combat readiness warehouse management system that introduces ZIGBEE technology into the existing warehouse management, and performs warehouse arrival inspection, warehousing, outgoing, allocation, shifting, and inventory. Automated data collection is carried out on the data of each operation link such as inventory, to ensure the speed and accuracy of data input in each link of warehouse management, to ensure that the real data of the inventory is grasped in time and accurately, and the inventory is maintained and controlled reasonably. Through scientific coding, it is also convenient to manage the batch and shelf life of items. Using the system’s location management function, you can also grasp the current location of all inventory materials in a timely manner, which is conducive to improving the efficiency of warehouse management. At the same time, it will better serve the combat readiness warehouse and provide a favorable guarantee for the accurate and error-free work of the army’s logistics department, equipment department, and training department.
3 System principle
The warehouse management system is mainly used for the automated management of the entry and exit of warehousing supplies, and consists of ZIGBEE electronic tags installed on the outer boxes of war preparations, wireless routing nodes, coordinators, handheld readers, management center network management equipment and management software. When the war preparation materials carrying the ZIGBEE electronic tags pass through the radio frequency sensing area set by the warehouse, the system uses the ZIGBEE electronic tags to realize automatic inventory, pick-up and rapid inventory and material monitoring in the warehouse. Through scientific coding, it is also convenient to dynamically manage the batches and origins of items. Using the system’s location management function, it is possible to grasp the current location of all inventory war preparations in time, which is beneficial to ensure the safety of war preparations and improve the efficiency of warehouse management.
3.1 System structure
3.1.1 Topology diagram of system equipment structure
3.2 Technical route and key technology
3.2.1 Based on SOA architecture design
Adopt J2EE architecture, SOA-based architecture design and componentized design concepts, build through components, develop business application systems based on this platform, adapt to the software architecture’s requirements for inheritance, compatibility, and scalability, and ensure that the architecture is extended and connected Reasonable.
3.2.2 Realization of material query and browsing based on two-dimensional and three-dimensional integrated GIS technology
Combining the characteristics of the military museum material management system, integrating the macroscopicity and integrity of the two-dimensional geographic information system and the advantages of the reality and intuitiveness of the three-dimensional geographic information system, overcoming the abstract ambiguity of the two-dimensional geographic information and the roaming of the three-dimensional virtual scene Feeling lost, design a two-dimensional and three-dimensional integrated GIS platform, realize two-dimensional abstract layers plus three-dimensional modeling to achieve the integration of two and three-dimensional characteristics, increase the support of the three-dimensional geographic information system, increase the personalized customization function of the military museum material management system, and increase The support of unified material management and the addition of platform functions such as material query will provide better support for the military museum’s existing business and future business systems.
3.2.3 Development of mobile applications based on Hybrid App technology
Hybrid App (hybrid mobile application) refers to an app that lies between web-app and native-app. It has both “the advantage of a good user interaction experience with Native App” and “the advantage of cross-platform development of Web App”.
Hybrid App is developed using web language and programming language at the same time, and is distributed through the application store to distinguish mobile operating systems. Users need to install and use mobile applications. The overall characteristics are closer to Native App but are quite different from Web App. Just because webpage language coding is used at the same time, the development cost and difficulty are much smaller than that of Native App. Therefore, Hybrid App has all the advantages of Native App, as well as the low-cost advantage of using HTML5 cross-platform development for Web App.
3.3 The overall design of the system
3.3.1 Construction goals
Develop standardized business processes from both business and system perspectives, and ensure process standardization and information standardization at the technical level. Establish the main framework of material management, focusing on material management specifications/processes/documents/reports/data. Improve work efficiency, reduce labor costs, and realize effective and systematic material management and control, including:
(1) Achieve business support to the museum’s internal material management department and demand department from a system perspective;
(2) Establish a management channel for efficient communication between the management department and the executive department;
(3) Standardization of material management information: define a standardized material management process;
(4) Through the material management system, the entire life cycle of collections and assets can be managed to ensure the optimal display of collections and asset use.
3.3.2 Availability
According to the urgency of application requirements, with actual application requirements as the core, to ensure that the system functions have actual application value, and based on demand analysis, the overall system design is carried out from two perspectives. One is business-oriented functions. The functions and business requirements of the system should be fully considered at the same time, the current business status should be fully considered, the difference between the needs and the status quo should be found, and the scope of the system construction should be located. The second is oriented to the organizational structure. It is clear who the users of this system are, what are the roles of various users, and what functions should be provided to users of various roles. The above two aspects should be implemented throughout the system design.
3.3.3 Security
The system should fully consider the system’s safety protection and redundancy measures, and provide a strong management mechanism and control means. First, it must comply with national confidentiality regulations and requirements; provide a well-established security strategy to ensure the confidentiality, integrity, controllability, and reviewability of the entire system in data storage and transmission; use a reliable authorization mechanism to prevent illegal access And illegal invasion. The second is to do a good job in system and data backup and recovery to ensure that the system and data are safe and reliable.
3.3.4 Scalability
Scalability will be considered from two aspects: one is the host network and system software technical support to expand the system by adding new hardware, considering the integration and application of existing cutting-edge technologies and equipment at home and abroad, to meet the ever-increasing performance requirements; It is easy to expand in the application software structure, horizontal expansion and function expansion of the SOA-oriented architecture system, and reserved interfaces for other application systems and integrated applications of business analysis models. During the construction of the system, advanced technical means should be adopted to realize the subsequent rapid expansion of system functions and adapt to the ever-evolving business needs.
3.3.5 Maintainability
The system will ensure the maintainability of the system from both the server side and the client side. For the client, it is required to minimize maintenance operations; for the server, it is mainly guaranteed from two levels. One is that the network, host, and system software must provide corresponding maintenance tools; the other is that the application system must provide a unified management interface, which is clear The management wizard simplifies the difficulty of system maintenance and provides a detailed system maintenance management operation manual.
4 System features
4.1 Advantages of Public Security Warehouse System
(1) Enhance the accuracy and speed of warehouse operations, reduce illegal entry and exit, and ensure material safety.
(2) Achieve automated operations such as inventory, pick-up, rapid inventory, and material monitoring in the warehouse.
(3) Through scientific coding, it is convenient to dynamically manage the batches and origins of items.
(4) Use the system warehouse location management function to keep abreast of the current location of all inventory war preparation materials in a timely manner.
(5) The system response time is 3-5S, which provides a favorable guarantee for combat effectiveness.
4.2 View monitoring
4.3 Visual management
Video surveillance is based on reading the tags on the materials, analyzing to determine whether the materials are placed in the correct location, whether the materials are in the warehouse, whether the materials are moved, and whether the materials exceed the warning line, etc., to link the alarm to ensure the safety of the materials.
4.4 3D simulation visualization
3D simulation visualization can accurately view the situation of warehouse materials, lines and storage and the location of personnel.
4.5 Scanning material management
4.6 Scanning box search-location alarm
4.7 Handover management of equipment warehouse materials
The management process of museum collections mainly includes the main processes of collection, shipment, admission, temporary storage, appraisal, storage, storage and storage, archiving and cataloging, warehouse management, collection utilization, verification and statistics, and collection cancellation. At the same time, the asset management process includes steps such as purchase, entry into account, put into use, use department, depreciation, and even withdraw from use. The transfer between departments generated during the management process needs to record the work process and collection information in detail, obtain the approval of the superior department, and confirm that the transfer procedures are complete. Therefore, the whole process of the transfer work needs to be managed.
4.8 Inbound and outbound display
4.9 Alarm for illegal delivery
Using the directional card reader at the door of the warehouse, the goods or boxes with electronic tags can be checked out of the warehouse. If the goods are not in the warehouse receipt, an audible and optical alarm will be issued.
4.10 Automatic inventory
Using the card reader in the warehouse, the goods or boxes with electronic tags can be automatically counted, and data can be formed for storage.
4.11 Acousto-optic search
The role of the sound and light position indication label guides the warehouse manager to complete the in and out process faster by sounding and lighting. A command to search for an item can be issued through a computer or a handheld PDA. The software system finds the location information of the item, and the tag receives a sound and light command.
4.12 Warehouse environmental monitoring
Smoke alarms, temperature and humidity sensors, PM2.5 sensors, anti-tilt sensors and other alarms are installed at multiple points in the warehouse. These devices transmit relevant data information through ZigBee networking, and transmit real-time data to monitoring through signal relay In the center, if the preset threshold is exceeded, the system automatically alarms, and records in the corresponding alarm form. Depending on the alarm level, the measures taken are also different. Issue instructions to start (shut down) fans, air conditioners, humidifiers, etc. to achieve real-time monitoring of the warehouse environment, and display the equipment startup (shutdown) and alarm status on the software interface to ensure that the warehouse material storage environment always maintains a normal state .
Temperature and humidity detection system real-time monitoring parameter setting system function
Temperature detection and humidity detection
Smoke detection PM2.5 detection
Anti-tilt detection
Previous day next day today’s environmental status
equipment status
Communication status
4.13 Information Security
The information system (including hardware, software, data, human, physical environment and its infrastructure) is protected from accidental or malicious reasons from being damaged, altered, or leaked. The system operates continuously, reliably, and normally, and information services are not interrupted. , To achieve business continuity. Information security needs to ensure the confidentiality, authenticity, integrity, unauthorized copying and security of the parasitic system, so that internal information is not threatened by internal, external, natural factors, etc.
5 System solution
5.1 Functional design
5.1.1 Management method
According to the difference of equipment, equipment parts and consumables, three material management methods are designed: whole piece management, box management, and flow management.
The RFID material system can support the following three management methods:
(1) Whole piece management
Paste electronic labels and paper labels on each item
Features Automated warehouse entry and exit
Stocktaking automation
Real-time monitoring of a single piece
Important materials with high applicable value and long service life
Relatively few supplies
For example: equipment
Not applicable to large quantities of materials
One-time consumable materials
(2) Group box management
Pack N materials into packages (bundles, bags, sleeves, boxes), and paste paper labels;
Pack multiple packages (bundles, bags, sleeves, boxes) into boxes, and paste electronic labels
The complete set of materials are automatically stored in and out of the warehouse
Manual operation of scattered materials in and out of the warehouse
Stocktaking automation
Real-time monitoring of the entire box of supplies
Suitable for materials with small size, various types and large quantities, such as: equipment parts
Not suitable for bulky materials
(3) Flow management
Do not stick labels to materials
Manage receipt and delivery, warehouse entry and exit through documents
Manual operation of materials in and out of the warehouse
The results of manual inventory are more reliable
No monitoring
Suitable for one-time consumption, low-value, large-volume materials
For example: consumables
Not applicable to important materials with high value and long service life
5.2 Function details
5.2.1 Flow chart of public installation
5.2.2 Flow chart of public installation spare parts
6 Project Management Plan
6.1 Project progress management
Compile a scientific and reasonable overall construction schedule plan, use professional management software to dynamically control the project plan; and decompose a clear project stage plan on the basis of the master plan. The project manager grasps the main contradictions and arranges the work strictly according to the plan. Focus on the construction of key processes. Regularly check the implementation and completion of the plan, and adjust the construction schedule in time to ensure that the progress of the project can be completed on schedule; during the construction process, according to the progress of the construction and the changes in various factors, the project plan is continuously optimized to ensure that the development of the project The connection of phases and the connection between the various departments of project research and development.
6.2 Project quality management
According to the actual situation of this project, during the development and implementation of the project, GB/T19001, the 2000 version of the ISO9001 national standard should be strictly followed.
At the same time, the following quality control should also be emphatically considered.
1. The content of quality control not only relies on product quality inspection, but also emphasizes the quality design (injection) into the product to ensure high quality in all important aspects of the project: quality plan and test plan; requirements check, outline design check; detailed design review and Inspection; program code review and inspection; unit test, system test.
2. Peer inspection: The work results delivered by each project personnel, including requirements documents, design documents, source programs, test cases, etc., are guided, inspected and approved by higher-level project personnel, and formal inspection documents may be required; quality Ensure that the personnel independently check whether the work of the project personnel conforms to the standards and specifications stipulated by the organization, track and manage the problems found, and require the formation of formal inspection documents.
3. Monitoring and measurement: use quantitative methods to monitor project work products and work processes, obtain important data required for quality analysis and management decision-making, and provide a basis for product release and process improvement.
4. Software defect tracking: record, track and correct each software defect found.
5. Stage summary meeting: At the end of each project work stage, the project manager convenes a stage summary meeting to analyze existing problems and propose and take improvement measures.
6. Binary quality control: the work results of each stage must be submitted to the formal review meeting; the meeting is presided over by the senior manager, and the project manager, quality assurance personnel and related personnel attend the meeting. The review meeting must give a decision on whether to pass or not. If the review is not passed, the project manager must draft and implement the corresponding rectification plan, and then submit it for review again.
The quality control of each main stage of project implementation is shown in the following table.
Quality control table for the main stages
Stage document quality control methods
Signing the contract, the project specification and the standard inspection of the document
Plan a software development plan
Normative inspection of quality management plan documents
Review the development plan and quality plan
System Design System Design Plan
Outline design specification
Outline design specification
Review Form
Detailed design specification
Detailed design specification review form document normative inspection
Review the design specification
Coding software development programming guide
Software Implementation Plan
Source code listing
Regulatory inspection of user operation manual documents
Normative review of the software source code
System integration system integration report document normative inspection
Test test plan
Test instructions
Test case
Test BUG list
Standard inspection of test analysis report documents
Review the test plan and other test documents
Installation and commissioning application software configuration record
Regulatory inspection of application software installation records
Supervise execution
Operation and maintenance trial operation record
Software maintenance manual document normative inspection
Supervise execution
Acceptance project acceptance report
Project development summary report document normative inspection
Acceptance report review
Run support service reports
User Satisfaction Survey Form
Software problem report
Software modification report document normative inspection
Supervise execution
Configuration Management Configuration Management Plan
Software configuration item plan list
Regulatory inspection of the actual list of software configuration items
Substantive inspection according to the document
6.3 Other related management
A sound management system and standardized operation and maintenance work are important guarantees for doing a good job in the operation of the system. According to the characteristics of the construction and operation and maintenance of the project, it is necessary to organize the strength to study and formulate relevant management systems and operation specifications in a timely manner, so that after the completion of the system construction task, the operation and maintenance team can jointly abide by the implementation specifications and make the system go into operation smoothly.
Formulate the “System Operation and Maintenance Management Measures.” The organization structure, work mode, information sharing and update, information security management, emergency response, technical services, responsibilities of operation and maintenance units, performance appraisal, and use of operation and maintenance costs are made in principle for the operation and maintenance phase. This management method has a guiding role for the following other management methods and regulations in the system operation and maintenance stage.
Formulate “System Information Sharing and Update Management Regulations.” Clarify the rights, responsibilities and obligations of the information management department in the provision, use, and maintenance of information; clarify the content, classification standards, provision methods, and update frequency of the information provided; clarify the scope of users, operation rights, and copyright protection for sharing information; clarify the information Management organization, use of funds, reward and punishment measures, and information security and confidentiality measures, etc.
Formulate the “System Security and Confidential Management Regulations.” Make specific provisions on system network security, equipment security, computer room security, information security, system security, operation security, management security, and confidentiality requirements.
Formulate the Implementation Rules for Performance Evaluation of System Operation and Maintenance. For system management coordination, information sharing, application promotion, operation and maintenance, and security and confidentiality, performance evaluation indicators and evaluation methods are respectively proposed.
Formulate “System Data Service Center Management Rules.” Provisions are made on the responsibilities, work specifications, operation and maintenance service content and technical support of the data service center.
[ad_2]