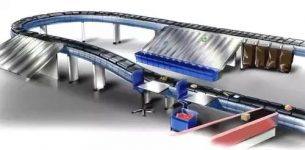
Automated logistics system solution for cigarette factory mouth sticks
[ad_1]

Logistics automation: the picture comes from the Internet
Guiyang Cigarette Factory’s automatic logistic system for nozzle sticks was installed in November 2009, commissioned in March 2010, and fully put into trial operation after the relocation of the packaging equipment in December 2010.
The basic flow of mouth stick logistics is shown in the figure below:

Basic flow chart of mouth stick logistics
Incoming tow tray
The auxiliary material system automatically transports the tow and paper trays to the forming unit through the AGV system according to the outgoing task. The tow trays are sent to the waiting station of the forming machine, and the tow trays are sent to the work station, resulting in empty trays. After being sent to the empty pallet platform, it is sent back to the auxiliary material warehouse by the AGV trolley (the size and mode of the AGV interface are provided by the customer).
Empty tray supply
In the initial state of the system, the empty trays are first stored in the filter rod warehouse in the form of 12 trays/groups and 13 trays/groups. When the forming unit needs them, the computer scheduling system will transmit the tasks to 1#/2# laneway stack. Stacker, lane stacker take out the empty tray group from the designated cargo space, send it to the empty tray conveyor of the tray loader, and separate the empty tray group into a single group by automatic conveying and empty tray separation mechanism The empty trays are picked up by the lifting shifter and sent to the upper tray of the tray loading machine, and then sent to the tray loading machine one by one in order.
Real material tray storage
The filter rod full tray comes out of the tray loader to the lower tray of the tray loader, and is smoothly conveyed to the full tray conveyor. The RFID read-write head writes the brand and production time of the filter rods in the tray to the RFID . When the full tray conveyor reaches 12 or 13 trays/group, the tray separator starts to isolate the following full trays, and at the same time, the information is transmitted to the upper management system. The upper scheduling system dispatches the 1#/2# lane stacker to the corresponding conveyor to take out the full tray group and transport it to the designated storage location for storage and natural curing.
Full tray out of storage
When the transmitter group needs filter rods, the computer dispatching system will issue the unloading task to the 3#/4# laneway stacker, and the laneway stacker will take out the full tray group on the designated cargo position and send it to the full tray of the unloader On the conveyor. The RFID read-write head reads the RFID information and compares it with the outbound brand issued by the dispatching computer. If it is relatively correct, the conveyor is started, separated into a single full tray by a separation mechanism, and the full tray is sent to the unloading machine smoothly. Taiwan, waiting for unloading. If the tray information is wrong, it will alarm and deal with it manually.
Empty tray group returned to warehouse
The filter rod empty tray comes out of the unloader to the lower tray of the unloader, and is smoothly conveyed to the empty tray conveyor of the unloader through the tray transition section of the unloader empty tray conveyor. When the empty tray reaches 12 or 13 trays/group, the tray separator starts to isolate the empty trays behind, and the information is transmitted to the upper management system at the same time. The upper dispatching system dispatches the 3#/4# lane stacker to the corresponding conveyor to take out the empty tray group and transport it to the designated storage space for storage.
Sampling inspection, error material tray in and out of storage
The upper scheduling system dispatches the lane stacker to take out the random inspection/error material trays from the vertical storage and send them to the corresponding manual platform (forward and reverse conveyor). In this mode, the conveyor does not need to be driven, and the stacker is manually processed. Then send the tray back to the warehouse for storage.
Withdrawal
The upper level dispatching system dispatches the lane stacker to take out the return material tray from the vertical warehouse and send it to the corresponding manual platform (forward and reverse conveyor). In this mode, the conveyor is manually operated by the start and stop buttons on the side of the platform Jog operation, manual removal of the return tray from the platform.
Return to the library
When rebranding production or holiday breaks, manually take out the empty/solid trays from the unloader and transport them to the manual platform. The empty tray is manually entered on the computer terminal, and the full tray is entered by the read-write head to the RFID. The upper dispatching system dispatches the lane stacker to store the empty/real material trays in the warehouse.
When rebranding production or holiday breaks, the material tray returned from the coiling unit can also be sent from the manual station to the warehouse for temporary storage.
[ad_2]