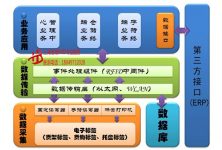
Warehousing logistics and supply chain management
[ad_1]
1. Project background
1.1. Analysis of current situation of logistics and supply chain management
Logistics and supply chain management play a very important role in the entire management process of an enterprise. If the timely and accurate supply chain management such as warehousing, outgoing, logistics and inventory control cannot be guaranteed, it will bring huge losses to the enterprise. It is not only manifested in the increase of various management expenses, but also makes it difficult to guarantee the quality of customer service, and ultimately affects the company’s market competitiveness.
The traditional logistics and supply chain management model mainly relies on manual management, with poor transparency. Logistics and supply chain management personnel do not have a good understanding of the entire warehouse storage situation and lack real-time tracking management. Although with the popularization of computer applications, most companies’ logistics and supply chain management data have begun to use computer data systems for management, but the data is collected and statistically organized by first recording on paper and then manually inputting it into the computer. This not only causes a lot of waste of human resources, but also due to human factors, the data entry speed is slow and the accuracy rate is low.
With the continuous development of the scale of enterprises, the number of types of logistics and supply chain management items is increasing, and the frequency of in and out of the warehouse has increased sharply. Logistics management and warehouse management operations have also become very complex and diversified. The traditional manual warehouse operation mode and data collection The method has been unable to meet the rapid and accurate requirements of warehouse management, which has seriously affected the operational efficiency of the enterprise. Therefore, there is an urgent need to build an intelligent warehouse management system to improve logistics and supply chain management, increase the utilization of warehouse space, speed up the execution efficiency of warehousing operations, rationally allocate labor, and improve production efficiency; so as to achieve human resources, equipment utilization, logistics and supply The effective optimization of chain management improves the core competitiveness of the enterprise.
1.2. The application of RFID in logistics and supply chain management
based onRFIDThe logistics and supply chain management system of the company introduces RFID technology into the existing logistics and supply chain management to automate the data of each operation link from warehouse to cargo logistics, distribution, warehousing, outgoing, warehouse shifting, inventory counting, etc. Data collection ensures the speed and accuracy of data input in all aspects of logistics and supply chain management, ensuring that companies can accurately grasp inventory and real data in transit in a timely manner, and maintain and control inventory reasonably. Using the system’s location management function, you can also grasp the current location of all inventory items in time, which is conducive to improving the efficiency of warehouse management.
By attaching RFID electronic tags to the materials, the system can realize the rapid and batch identification of the materials, and accurately obtain the relevant information of the products at any time, such as the type of materials, suppliers, delivery time, expiration date, inventory, etc. Wait. The RFID logistics and supply chain management system can realize real-time monitoring of materials from storage, storage, inventory, transfer, etc., which can not only greatly improve the degree of automation, but also greatly reduce the error rate, thereby significantly improving the logistics and supply chain Management transparency and management efficiency; the application of RFID in logistics and supply chain management helps companies reduce costs and gain competitive advantages. Information flow is conducive to controlling and reducing inventory, and reducing costs (including labor costs), so that companies are in warehousing The management of materials is more efficient, accurate and scientific.
2. System architecture and design
2.1. Overall design ideas
The RFID logistics and supply chain management system uses RFID electronic tags as the information carrier of items in the logistics and supply chain management process, and uses RFID readers and handheld devices as information collection equipment to realize storage and storage in the logistics and supply chain management process. The rapid, automatic, effective, and batch collection of information in key operations such as delivery, inventory, and transfer, realizes the automated management of information collection in logistics and supply chain management, and improves the level and efficiency of logistics and supply chain management.
2.2. System logical architecture
Figure 1 Logical structure diagram of logistics and supply chain management system
The above figure shows the logical relationship between the components of the RFID identification system and the logical relationship with the user’s existing business system. Each application module management center business, warehousing terminal business, handheld terminal business and middleware of the upper application exchange data; the middleware manipulates the hardware equipment (including fixed readers, handheld Type data collector, RFID card issuer), and obtain the data returned by the hardware device; the hardware device reads or prints the electronic label according to the instructions of the middleware, and the middleware is also responsible for the data exchange between the application and the database.
The standard data interface is reserved during the overall design of the system to facilitate data exchange with the user’s existing business system (ERP system).
2.3. System topology
The logistics and supply chain management system consists of a central management subsystem, a warehouse operation management system, and a handheld terminal operation system. These systems are connected to each other to realize the labeling, warehousing, outgoing, inventory, and transfer of warehousing materials. The fast and accurate data collection of each operation link ensures that the company can timely and accurately grasp the real data of the inventory, reasonably maintain and control the company’s inventory, effectively improve the efficiency of warehouse management and reduce operating costs.
Figure 2 Topological structure of logistics and supply chain management system
Among them, the management center subsystem is the business core of the entire logistics and supply chain management system. Its main functions include data collection, data backup, and various application business modules such as: warehousing order issuance, material outgoing order issuance, material transfer Issuance of warehouse orders, material inventory receipts, material query management, basic data management, warehouse authorization management, etc.
The label issuance subsystem is the starting point of the material in the storage life cycle. Its main function is to add electronic tags that write material information to the newly added materials to complete the information identification of the materials in the system.
The identification and collection subsystem plays a supporting role in the warehouse management system. It mainly uses RFID fixed readers and RFID handheld devices to complete the collection of material data information in each operation link of the entire storage life cycle, and upload the collected data to the database , Support system operation.
The whole system adopts BS architecture, and the management center can support the management of multiple warehouses at the same time.
2.4. Interfacing with third-party systems
In the information construction and application of logistics and supply chain management, there may be third-party systems that need to be connected, such as enterprise ERP systems, ERM systems, etc. The logistics and supply chain management platform provided by Shanghai Yingxin Information provides standardized interfaces and open communication protocols to facilitate third-party systems to access the logistics and supply chain management platform through a unified interface, share data, and realize data exchange.
3. System features
3.1. Multi-warehouse support
The system fully supports multi-warehouse management requirements. It can quickly realize centralized management of the warehouse network of customers distributed across the country through a set of systems. And effectively provide differentiated logistics and supply chain management services for a large number of different warehouses. Related warehouses can achieve linkage operations to build an integrated inventory service system; centralized deployment, a global perspective, global mastery and partial coordination of various businesses, real-time viewing of analysis and statistical reports.
3.2. Global inventory visualization
The system fully realizes the visualization of the global inventory of materials. Through centralized management, all warehouse inventory is mastered, and the total inventory and distribution of inventory can be viewed from different angles. Realize precise warehouse management, inventory turnover control, and provide basis and support for the allocation between warehouses and the shift in warehouses.
3.3. Powerful job rules and strategies
The system provides powerful warehousing strategies, shelf strategies, picking strategies, and inventory strategies; when the operation instructions arrive at the warehouse, the system can meet various warehouse management requirements (such as first-in first-out, last-in-first-out) according to pre-defined strategies. , On the basis of batch delivery, etc.), optimize the warehouse operation line, save the workload of the operators, solve the operation bottleneck, and optimize the inventory placement layout.
3.4. Lean library operation management
The system subdivides various operation modes in the warehouse according to material receiving, warehousing, putting on shelves, picking, outgoing, shifting, and inventory, etc., and queues them according to tasks, and the operators in each warehouse area will automatically receive them. Go to the homework task. Through the inventory log, the system completely records every system operation action and inventory changes. When a cargo difference occurs, it can be documented.
3.5. Detailed material attribute management
The system provides category management according to material categories and subcategories, and it also supports the management of detailed attributes of materials, including: packaging, specifications, suppliers, origin, color, batch, batch number, shelf life, etc. It can make up for the shortcomings of the ERP system that cannot distinguish the materials in detail and guide the operation. Material attributes provide warehouse managers with a means to manage differences in the details of the same materials.
3.6. Advanced RFID data collection operations
The system adopts advanced RFID data collection operation method, which can realize the fast and accurate collection of data in each key operation link in the warehouse management system: inbound, outbound, inventory, and shifting data, ensuring that the company can accurately grasp the real data of the inventory in a timely and accurate manner , Provide an effective basis for corporate decision-making.
4. System software function
The logistics and supply chain management system is mainly divided into three parts: the warehouse management center system, the warehouse operation management system, and the handheld terminal operating system.
The entire system architecture is a combination of B/S+C/S architecture.
In the logistics and supply chain management center system, the B/S structure is mainly adopted. The biggest advantage of the B/S structure is that it can be operated anywhere without installing any special software. It can be used as long as there is a computer with Internet access. The scalability of the system is very easy, as long as you can access the Internet, and then the system administrator assigns a user name and password, you can use it. It is convenient for personnel with different authority in the logistics and supply chain management center to query and view relevant warehousing data at any time.
The warehouse operation terminal mainly adopts the C/S architecture. The biggest feature of the C/S architecture is that it is more convenient and quick to drive, manage and operate the local hardware equipment. Because the RFID warehouse management system is for the warehouse operation end, access There are many hardware equipments. In order to facilitate local management and operation convenience, we mainly develop the system based on the C/S structure on the warehouse operation side system.
4.1. Software functions of the warehouse management center
The logistics and supply chain management center is the core part of the whole system. Its main functions are: material requisition management, material in transit management, material arrival management, material storage management, material delivery management, material inventory management, material allocation management , Daily query, daily report, basic data maintenance, system management and other functions.
4.1.1. Material requisition management
The internal staff of the company can log in to the system, fill in the material requisition form in the system, fill in the relevant information of the material to be collected, and apply for the relevant material.
Relevant leaders of the company can view the current material requisitions that need to be approved by logging in to the system, and view related detailed information, and can pass or reject subordinates’ requisition applications.
4.1.2. Material arrival management
Material arrival management is mainly developed for the asymmetry of material arrival information between the warehouse management center and the warehouse, especially between the management center and the agency storage, which leads to the inability of the materials to be put into the warehouse in time, and the management center can not learn the relevant information of the goods in time. Its main function has two functions: arrival check and arrival processing.
4.1.3. Material storage management
The material warehousing management of the Logistics and Supply Chain Management Center is divided into two functions: warehousing notice production and warehousing notice approval according to the authority of different personnel, which realizes the production and issuance of warehousing notices, and facilitates the warehouse operation end according to The warehousing notice is used to check and accept the goods and warehousing.
4.1.4. Material delivery management
The management center material outbound management is mainly divided into two functions: material outbound notice making and material outbound inquiry and approval. After approval, the outbound notice will be submitted to the warehouse, and the warehouse administrator will carry out the follow-up operation of the outbound material.
4.1.5. Material inventory management
The logistics and supply chain management center’s inventory of materials mainly has three functions: inventory sheet production, inventory sheet approval, and inventory post-processing.
The warehouse management center bases the inventory according to the materials that need to be counted, according to the warehouse inventory or the customized materials that need to be counted, and forms an inventory list. After passing the approval, the inventory list is issued to the warehouse operation end, and the warehouse management personnel carry out the actual inventory operation. After the feedback of the inventory results, the management center will carry out the subsequent inventory loss and inventory profit processing operations.
4.1.6. Material allocation management
The allocation and management of materials is mainly for materials between different reservoir areas, and related processing needs to be carried out when mutual materials are transferred. The warehouse management center actually adds or deletes the material types, quantities, warehouses, etc. that need to be allocated according to actual needs, forms an allocation notice, and submits it to the system, which is approved by relevant leaders and submitted to the warehouse administrator for follow-up operations.
4.1.7. Daily query
The logistics and supply chain management system based on RFID technology provides a wealth of daily query functions, including: single material query, inventory detail query, material storage query, daily alarm query and other functions. After logging in to the system, users can enter relevant query conditions to query relevant data information.
4.1.8. Daily reports
The system can provide a variety of reports to facilitate the warehouse management center to view the inventory information. The report types mainly include: no dynamic list, low-inventory material early warning form, material classified inventory list, material receipt and storage list, material receipt and storage summary table, etc.
4.1.9. Basic data maintenance
For a new logistics and supply chain management system, it is necessary to carry out preliminary data maintenance and import of the relevant basic data of the warehouse to ensure the normal operation of the entire system.
The maintenance of basic data mainly includes the following two aspects: material information maintenance and storage area information maintenance.
4.1.10. System Management
System management mainly includes log management, role management, and user management.
Log management is mainly to query all the operations of the system and provide a basis for a field of processing. It is mainly based on the query conditions to find out the relevant operations performed by the user in the system.
Role management is mainly the management personnel with the highest authority in the system, which defines all the role information that exists in the system. And can add or delete relevant role information at any time according to actual use.
User management mainly realizes the addition of users and the assignment of user roles.
4.2. Software functions of warehouse operation terminal
Warehouse operation management is mainly the warehouse management personnel in accordance with the instructions issued by the warehouse management center to carry out warehouse related operations. Its main functions include: material arrival operations, material storage operations, material delivery operations, material inventory operations, and material allocation operations , Material query, daily reports, basic data maintenance, system management, alarm information prompts, etc.
4.2.1. Material arrival operations
The material arrival operation is mainly for the warehouse management staff to check and accept the quantity, quality, model, specification, etc. of the goods after the materials arrive, according to the content of the warehousing notice, and fill in the relevant arrival acceptance report and the deviation of the goods. Report.
4.2.2. Material labeling operations
After the materials are delivered, the warehouse management personnel will complete the labeling operation of the materials, and select different labels and pasting methods according to the different packaging materials of the materials. At the same time, the relevant information of the materials, such as the type, model, and supplier of the materials, will be written in the tags to complete the information identification of the materials in the RFID warehouse management system. And through the storage warehouse designated by the system, the materials will be prepared for storage.
4.2.3. Material storage operations
After the materials have completed the labeling operation, the warehouse management personnel can carry out the warehousing operation of the materials according to the warehousing notice.
Material storage: When the material enters the warehouse, the material information is read through the RFID reader at the door and uploaded to the system. After the system confirms the information, the warehouse staff prompts the information and arranges the material to be put on the shelf;
Material on the shelf: When the material is placed on the designated shelf, the library manager reads the material label information and shelf label information through the handheld device, completes the association between the two, and uploads the system to complete the material storage;
4.2.4. Material delivery operations
The warehouse management personnel complete the operation of corresponding materials out of the warehouse according to the outbound notice.
Generation of outbound orders: The outbound orders are mainly issued to the warehouse management personnel through the warehouse management center, and the warehouse management performs the operation of material out of the warehouse;
Material off-shelf: The library manager downloads the out-of-warehouse list through handheld devices, and completes the off-shelf operation of the materials in accordance with the material information on the out-of-warehouse list. The library manager reads the material label information and shelf label information through the handheld device, disassociates the two, and completes the removal of the material;
Material delivery: After the material is off the shelf, the relevant information of the material can be read through the RFID reader at the door and uploaded to the system. The system will check the material’s delivery information to complete the material’s delivery;
Material unlabelling: For labels that need to be reused, label unlabeling and initialization will be carried out.
4.2.5. Material inventory operations
The warehouse manager completes the inventory operation of the warehousing materials according to the inventory information issued by the outbound management center, and generates corresponding (inventory profit, inventory loss, inventory balance) reports.
Generation of inventory list: The actual situation of the outbound management center can choose the scope of inventory. One is to inventory all spare parts, and the other is to inquire out spare parts according to certain conditions through inquiries, and inventory only this part of the spare parts.
Inventory counting: After generating the inventory list, the warehouse manager downloads the inventory list information to the handheld, and uses the handheld to count the materials that need to be inventoried (scan the material labels). After the inventory is completed, the inventory results are the same as the inventory list information Make a comparison, generate this inventory report and upload it to the system for subsequent processing.
4.2.6. Material allocation operations
The warehouse management personnel complete the allocation of materials according to the allocation notice issued by the warehouse management center. Transfers are divided into transfers within warehouses and transfers between warehouses.
4.2.7. Material inquiry
As the warehouse management terminal, the system provides a wealth of query information to the warehouse staff, including: single material query and inventory detail query.
4.2.8. Daily report
The system provides a wealth of daily report functions for warehouse managers, mainly including low-inventory material early warning form, material classification list, material receipt and storage list, emergency material list, material capital report, etc.
4.2.9. System Management
As a warehouse management terminal system, its system management mainly has the following functions: log management, warehouse maintenance, warehouse data initialization, system freezing, emergency supplies setting, equipment management, etc.
4.3. Handheld terminal software function
The handheld terminal is mainly used by the warehouse management personnel to issue related instructions through the warehouse operating system to perform inventory management related operations, which mainly include: label and label management, material on-shelf, material off-shelf, material transfer, material query, and inventory query , Daily inventory and other functions.
4.3.1. Label labeling management
The labeling management is mainly used to paste the RFID electronic label of the materials when the materials are in the warehouse. The warehouse management personnel complete the labeling operation of the materials according to the material storage information on the storage notice through the handheld device.
4.3.2. Material listing
When materials need to be put on the shelves, the warehouse management personnel obtain the information of the materials that need to be put on the shelves through the system. And scan the material label through the handheld device, and select the material that needs to be placed on the current shelf. When the goods are placed on the shelf, the shelf label information is scanned through the handheld device to complete the information association between the material and the shelf. At the same time, the relevant information is uploaded to the server to complete the shelf positioning of the materials in the outbound management system.
4.3.3. Picking up and removing materials
The outbound management personnel carry out the operation of picking up and unloading materials according to the material outbound list. The outbound management personnel read the material label information through the handheld device, and confirm the selection to complete the material picking operation. For materials managed by category, the quantity of goods in the label will be changed,
4.3.4. Material shift
The warehouse manager can scan the label of the material that needs to be shifted through the handheld device. When the material is moved to other shelves, the new shelf label information can be scanned through the handheld device, and the two information can be re-associated to complete the material shift. Operation.
Warehouse management personnel can scan material labels through handheld devices to obtain detailed information about materials, such as material names, specifications, and models.
4.3.6. Daily inventory
The warehouse manager generates the inventory list according to the warehouse management center and downloads the inventory list information to the handheld, and uses the handheld to count the materials that need to be inventoried (scan the material label). After the inventory is completed, the inventory result is the same as the inventory list The information is compared, and this inventory report (inventory loss, inventory profit, and inventory balance) is generated, and uploaded to the system for subsequent processing.
V. Introduction to the functions of RFID dedicated hardware equipment
In the RFID warehouse management system, the hardware devices used mainly include RFID fixed readers, RFID handheld readers, electronic tags, RFID desktop card issuers, RFID label printers, RFIDPortal, etc. These devices jointly complete the information identification and process identification of the storage materials in the RFID storage system.
5.1. Fixed RFID reader
Fixed RFID readers are mainly used in warehousing management to quickly and batch collect information on incoming and outgoing materials to improve the efficiency of materials in and out of the warehouse.
5.2.RFIDPortal
RFIDPortal is mainly used in warehousing management to quickly and batch collection of information on incoming and outgoing materials to improve the efficiency of materials in and out of the warehouse. At the same time, RFID Portal integrates sound and light alarms, which can provide early warning of abnormal conditions in and out of the warehouse, and reduce the fleeing of materials in and out of the warehouse.
5.3. Handheld data collector
The RFID handheld reader is mainly used for warehouse operators to carry out the functions of in and out of the warehouse, inventory, shifting, and materials in the warehouse.
5.4. Electronic label
RFID electronic tags are mainly used to install electronic tags for materials when they are newly put into the warehouse, and are used for information identification of materials in the entire RFID warehouse management system.
According to different label installation and use, warehouse management electronic labels are mainly divided into printing electronic labels, anti-metal electronic labels, and special-shaped electronic labels.
Printing electronic labels mainly uses RFID label printers to print relevant material information on the surface of the label. At the same time, the material information is written into material-related information through the reader device embedded in the label printer to complete the material in the RFID warehouse management system. Information identification.
The anti-metal tag mainly takes into account the impact of metal materials on the performance of the label. Therefore, on the metal materials, anti-metal electronic tags will be pasted or installed to ensure that the label information can be collected by the RFID warehouse management system to ensure that the label is on the metal materials. Reading distance.
Special-shaped electronic tags are mainly used for irregular surfaces of materials and are mounted on materials by hanging or special methods.
5.5. Desktop card issuer
Desktop card issuers are mainly used to write material-related data in special material tags, such as anti-metal tags and special-shaped electronic tags, to complete the information identification of materials in the RFID warehouse management system.
5.6. RFID label printer
The RFID label printer is used to print material-related information on the surface of the printed label and write relevant data inside the label.
[ad_2]