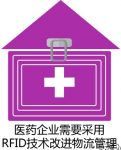
Adopt RFID technology to meet the needs of modern medical warehouse management system
[ad_1]
The medical warehouse management system realizes perfect enterprise warehouse information management through functions such as warehouse-in business, warehouse-out business, warehouse allocation, inventory allocation and virtual warehouse management. Tianjin Little Bee believes that modern pharmaceutical logistics has put forward new requirements for the original warehouse management system, especially the new version of “Pharmaceutical Business Quality Management Regulations” and other laws and regulations. Generally speaking, pharmaceutical logistics and other industries have greater the difference:
1. Pay attention to the management of the drug inspection list
2. Pay attention to drug flow tracking
3. Pay attention to batch number management and specify batch number to be released
4. Pay attention to the record of maintenance
5. Pay attention to the electronic supervision of drugs and the tracking management of the unique device code throughout the process
It can be clearly seen from the above points that a small process improvement in the medical warehouse management system may save a lot of time and labor, and a small oversight can waste more time and labor. We must do everything possible to reduce the labor intensity of employees, reduce unnecessary operations, shorten the movement line, and reduce repetitive operations on the basis of improving efficiency and reducing costs.
This requires synchronous recording of information and comprehensive monitoring of data during transportation.
RFID technology can store more information in the medical warehouse management system, guarantee the reliability of storage, quality assurance and product category management on a larger scale, and can read any number of RFID tags from a certain distance, which greatly reduces the registration of goods At the same time, it also realizes the function of tracking products from the beginning of the drug delivery to the consumer buying the product, which can help companies find and solve the problems in the supply chain as soon as possible. In addition, real-time inventory and smart shelf technology based on RFID ensure the correctness of shipments and returns and the timeliness of replenishment; RFID solutions can provide accurate information about inventory conditions, and managers can quickly identify and correct inefficiencies. Operational situation.
The medical warehouse management system combined with RFID technology can realize the following functions:
1. Inventory management
With the increase of multi-warehouse management and distribution systems and the rise of third-party logistics, the medical warehouse management system will manage more and more warehouses. RFID electronic tags can effectively record the supplier’s batch number, contract number, and batch number. All-round recording of information such as production date and production date. For the medicines stored in the warehouse, the maintenance and temperature records of the goods are transmitted to the medical warehouse management system in real time through RFID technology. At the same time, the storage location and inventory process of the goods can be carried out in real time, which greatly improves the efficiency of inventory management.
2. Warehousing process management
In the receiving process, according to the requirements of the new version of “Pharmaceutical Business Quality Management Regulations”, the medical warehouse management system will check supplier information (including name and seal), supply information, and can print out the corresponding receipts, and pass RFID electronic The label’s information storage provides delivery information (delivery carrier, transportation method, delivery time, delivery person and contact information, etc.), incoming goods temperature (refrigerated goods) and other information. In the acceptance process, the inspectors conduct the drug quality acceptance according to the regulations, and only need to scan the RFID electronic tags on the goods to immediately check the batch number, production date, expiration date, arrival quantity, acceptance quantity, acceptance result, etc. of the drug, after confirmation The medical warehouse management system automatically generates acceptance records. In the shelf link, the system provides the corresponding cargo information to the staff according to the different types of cargo.
3. Delivery link
In the order processing link, the pharmaceutical warehouse management system selects orders according to the owner, transportation method, transportation time limit, etc., and schedules the order processing logic according to different needs (such as: replenishment only, labeling first or labeling later, whether to merge orders Etc.). For upcoming merchants, it is also possible to optimize the algorithm to select orders based on the coincidence rate of order items and inventory placement to improve the efficiency of picking as much as possible. In the outbound review link, the medical warehouse management system provides the staff with verification information, and the staff scans the RFID electronic tags on the goods for verification and records.
Tianjin Little Bee believes that the complete applicationRFIDThe technical medical warehouse management system needs to be combined with the actual situation of the enterprise. During the design and implementation stage, special technical personnel need to be stationed on-site to solve or negotiate various technical problems that occur on the construction site. At the same time, it is also necessary to provide theoretical training and operational training for enterprises that apply the management system to quickly enable enterprises to adapt to the management system as soon as possible and improve efficiency.
[ad_2]