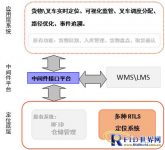
Intelligent warehousing logistics management plan
[ad_1]
Requirements overview
With the rapid development of domestic production enterprises and the logistics industry, more and more attention has been paid to efficient operation mechanisms. The scientifically managed modern warehousing can not only speed up the flow of materials in the enterprise, reduce the operation cost of the enterprise, but also realize the effectiveness of resources. Control and management. The original warehouse management system based on bar code and RFID system can no longer meet the development requirements of users. Manufacturers and logistics industry have put forward more refined management requirements for real-time positioning of cargo location, optimization of forklift task scheduling, and timely warning of production safety. , The special problems are as follows:
(1) The original identification method is inefficient, the original bar codeRFIDThe cargo identification system needs to be further optimized to speed up the identification of goods, further reduce the participation of personnel, and speed up the production schedule.
(2) The cargo location records are inaccurate. Many warehouses and workshops basically rely on the experience of forklift drivers and self-defined rules to locate and store materials. The storage location cannot be quickly found, and location management is chaotic.
(3) The lack of visualized warehouse management, the inability to know the specific location of goods in real time during the warehousing, loading, and distribution process, the inability to track the production progress, and the lack of visual supervision.
(4) Forklift scheduling lacks optimal allocation, and there is no system on site to optimize forklift scheduling. It is impossible to select the nearest forklift, idle forklift and the best delivery route, and the work allocation is unreasonable.
(5) The ability to find and correct errors is poor. There is no clear location management for different batches of materials. When quality problems are found, it is impossible to quickly find the problematic batches of materials in a timely manner, which affects quality control.
(6) There is no systematic guarantee for production safety. Generally, the factory area strictly regulates the walking route of personnel and forklifts, but it cannot cope with special circumstances and has potential production safety hazards.
Implementation plan
Based on more than 10 years of RTLS industry application experience, combined with domestic mature warehousing and logistics management systems, Dunn Technology launched an intelligent warehousing logistics management system, consisting of barcodeRFID identification system, RTLS (real-time location) system, and self-developed intelligent warehousing management system composition. The development of the warehouse logistics management system based on barcodeRFID identification is very mature, and there are unified international and domestic standards, which realize the application of remote identification of asset information, rapid batch identification, centralized management, and encryption authentication. Companies at home and abroad provide very mature high-precision RTLS positioning products, which can meet the precise real-time positioning of goods, forklifts, carts, personnel and other objects in the warehousing and logistics industry. Combined with the WMSLMS warehousing and logistics supply chain management system, the warehouse Real-time positioning of goods and forklifts, workshop materials and carts will further optimize inventory management and production scheduling management.
The system adopts one or more positioning products with different positioning accuracy according to customer needs, such as: UWB positioning system can achieve high-end positioning with high precision of 10cm in three dimensions, and EPS system based on 2.4G can achieve cost-effective positioning with two-dimensional accuracy of 50cm. Specific solutions Recommendations will be made according to the user’s on-site environment and needs, and specific functions can be customized on the intelligent warehousing platform system according to user needs.
System functions
Visual warehousinglogistics |
|
• real time monitoringForklift andMHE’s location,sportsandstate; • Warehousing and picking up, Quick confirmation of deployment, automatic display; • Provide speed limit and parking warning for vehicles in the warehouse,Height limit reminder,restricted areaConfirm to improveProductionSafety; |
• Make warehouse managementsystemrightin stockBlending andPosition status is fully visualized,Optimize deployment; • Simulate the warehouse in 2D or 3DAnd workshop, Realize process visualization and communicate withWMSLMSSystem seamless integration; |
Asset safetytrack |
|
• RealizationHeavyConfirm the location of the piece of cargo andTraceable; • Error preventionAnd tracking,operateFalse alarmandSystem record; • Unauthorized address,time,ID operationTimeautomaticCall the police; |
• Injury prevention,Ensure personnel, automatically detect collisions, reduce the impact on goods andInfrastructure bringsdamage; • Can be combined withCombination of Six Sigma to improve processefficientAnd standards; |
Advantages
1. The warehousing and logistics process is completely visualized, with active positioning and identification. After the RTLS positioning system is combined with RFID, accurate location information can be added to the original identification, making the warehouse management completely spatially visible.
2. Goods allocation and forklift allocation, real-time controllable status. The warehouse location information of cargo allocation is updated in real-time in the WMS system, and forklift work scheduling and route optimization are automatically assigned reminders to improve production efficiency.
3. The path track is recorded in real time, and the event can be traced back. All cargo dispatch information can be recorded in real time, forklift information, personnel information, time information, and path trajectory can be retrieved in time, and loss and safety events can be traced.
4. Logistics production analysis and process improvement in the warehouse. Real-time monitoring of the operation status of logistics in the warehouse, early warning of abnormal behaviors such as incorrect scheduling, route crowding, production errors, and illegal operations, and gradually optimize the process of warehouse production.
5. Safety guarantee and speed improvement. By analyzing the real-time location and route of vehicles and personnel, recommend driving routes, slow down or stop where there is a possibility of collision, to ensure high-speed driving in other areas, and to ensure the safety of personnel and production in the warehouse.
Application area
Company Profile
Jiangsu Tangen Technology Co., Ltd.-a leading provider of wireless positioning technology products and solutions in China, was established in 2004. The company has a professional technology research and development and project implementation team, providing professional positioning products, application solutions and technical services for ports, automobiles, warehousing, electric power, airports, military, retail, discrete manufacturing, education and scientific research and other industries, and improve the management of the industry. Level of chemistry and automation.
[ad_2]