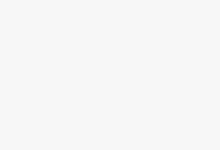
Distribution center solutions
[ad_1]
Demand analysis
This solution is mainly used for the automated identification management of bulk goods in storage, storage, sorting and outbound in the distribution center. It consists of radio frequency tags installed on goods or pallet turnover boxes, radio frequency identification systems installed in each link of the distribution center process, Middleware (optional) and WMS software composition. When the tagged target passes the set signal collection point, the tag immediately emits a radio frequency signal with representative identity characteristics, which is received by the system, processed by the middleware, and sent to the WMS system. The WMS system issues a series of instructions to achieve Cargo information collection, warehousing storage, regular inventory, sorting out of the warehouse and other functions.
Scheme composition
The RFID-based distribution center solution consists of multiple sets of radio frequency identification systems, middleware, database systems, and warehouse management information systems (WMS). in:
-Radio frequency identification system: mainly used to read/write information on electronic tags.
-Middleware: Between the front-end hardware module and the back-end database and application software, it provides mechanisms for program management, signal filtering and collection, event management, security management, and network management.
-Database system: input, analysis, output and management of various data information.
-Warehouse Management Information System (WMS): Control the actions of each link in the process, complete receipt and storage management, inventory allocation management, picking and delivery management, as well as data backup, data query, data statistics, report generation, and report management of the entire system .
Scheme construction
According to the distribution center process, an electronic label is fixedly installed on each pallet and turnover box, and the cargo information on the pallet or turnover box is bundled with the electronic label and entered into the database.
1. According to the goods information provided by the supplier, after the goods are sorted into pallets or turnover boxes, use the handheld reader to write the goods information into the label and transmit it to the WMS system, and the system will arrange the storage location according to the cargo location information. After the goods are placed in the designated location, the handheld machine and the background confirm.
2. When the goods need to go out of the warehouse, the handheld computer and the background network are used to search for the location information of the goods. After the goods are found and picked, the label information on the pallet or turnover box is read, and the relevant data is transmitted to the WMS system, after which the operator removes the label.
3. An identification system is installed in the sorting (loading and unloading) area of the distribution center. If the label information collected in step 2 is read in this area, it indicates that the label has not been removed or the removed label is placed in a nearby location, prompting the operator to make further processing.
4. The goods enter the delivery area and wait for delivery.
Program advantages
1. Pallets and turnover box labels are reused.
2. Optimize and adjust the distribution center process, the information anti-collision function of the automatic identification system, can read multiple different labels, realize the automatic review of the outbound, greatly improve the outbound speed, and reduce the labor cost of the distribution center.
3. Accurate inventory management enhances the planning, turnover, and distribution capabilities of the distribution center, and reduces losses and adjustment costs.
4. Research surface: The application of RFID solutions can increase the efficiency of the distribution center by 10% to 20%, while the inventory and delivery accuracy can reach 100%.
[ad_2]