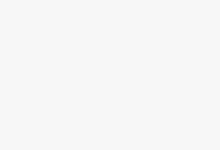
Forklift positioning application case
[ad_1]
1. Project overview
1.1 Project background
With the continuous development of the scale of the enterprise, the types of materials managed by the warehouse continue to increase, the frequency of forklifts entering and leaving the warehouse has increased sharply, and the warehouse management operations have been very complex and diversified. The traditional ones rely on a non-automated, paper-based document. The system of forklift management in the warehouse is completely manually implemented. Because of its low scheduling management efficiency, it has become increasingly unable to meet the fast and accurate requirements of today’s large-scale warehouse management, which has seriously affected the operating efficiency of the enterprise and has become one of the constraints on the development of the enterprise. Big obstacle.
As the internal layout of the warehouse is consistent, the forklifts have a fixed and unified driving route when working inside the warehouse, which provides a basis for unified deployment, access monitoring, and real-time positioning of forklifts. In order to meet the business requirements of the enterprise and the needs of future development, timely deal with the problems that need to be solved in the process of warehouse management and forklift scheduling, and improve the competitiveness of the enterprise in the complex market environment, our company uses RFID technology to build a complete and feasible Forklift Positioning, Dispatching and Monitoring System, and a solution to the system modification-“Forklift Positioning, Dispatching, Monitoring and RFID Management System Solution” has been compiled
1.2 Technical background
Radio Frequency Identification (RFID) technology is a non-contact automatic identification technology realized by radio frequency communication. The radio frequency identification system is mainly composed of RFID readers and antennas and RFID electronic tags.
The data information in the agreed format is stored in the electronic tag, which is embedded or attached to the surface of the article in the application, and the reader is used to identify and read and write; the reader reads the information in the tag and enters it into the network information system The device uses wireless induction to exchange information with the electronic tag, reads the data information in the electronic tag or writes the data information in the agreed format into the electronic tag, establishes communication and transmits data between the application software and the tag, Connect with the information system to realize data exchange.
Compared with other recognition technologies such as IC card, magnetic card, bar code, camera, etc., radio frequency automatic identification technology has the advantages of long reading distance, fast moving recognition, simultaneous recognition of multiple targets, fast reading and writing, repeated use, large amount of information processing and accuracy. In recent years, it has become the main development direction of automatic identification technology. Radio frequency automatic identification technology solves the problem of information collection, has become an important foundation and means to promote the development of national economic informatization, and is an important part of the informatization application system of various industries. Especially after RFID technology is combined with Internet, communication and other technologies, it is widely used in logistics, manufacturing, traffic management, military applications, public information services and other fields. It can realize global tracking and information sharing of items, which is very important for greatly improving management and Operational efficiency, cost reduction, promotion of social informatization level, promotion of sustainable economic development, improvement of people’s quality of life, enhancement of public security and national defense security have far-reaching influence and important strategic significance.
1.3 The overall goal of the project
The goal of this project is to build a comprehensive RFID management system for forklift positioning, scheduling, monitoring, warehouse personnel scheduling, warehouse forklift scheduling, task distribution management, forklift access monitoring, forklift real-time positioning, personnel attendance, forklift usage time data query, etc. , Integrated into a unified platform, unified processing, in order to adapt to the development idea of ”data concentration, platform integration”.
The comprehensive forklift positioning, scheduling, monitoring, and RFID management system needs to be designed to fully consider the impact of changes in the composition ratio of different businesses, and has strong adaptability. In addition, it is designed for software and hardware, network transmission performance and data capacity, and backup and reliable security. All aspects must be considered in order to meet the internal management requirements of the enterprise warehouse.
In order to strengthen the internal management of the warehouse, improve the control and supervision mechanism, reduce forklift operation accidents, prevent work sabotage, the system realizes the electronic data of personnel management, forklift management, operation time, and shift records, and data collection is automated to eliminate the influence of human factors. Ensure the accuracy of warehouse management and the timeliness of task execution.
2. Project demand analysis
2.1 Overview of needs
● When the forklift enters and exits the warehouse, its entry and exit information needs to be determined in time and uploaded to the management system so that the background can switch and locate the data source.
● When a task is issued, the information of forklifts and personnel without tasks shall be counted in time, so that the dispatching administrator can allocate forklifts and personnel.
● After the task execution of the forklift is completed, its task execution status needs to be switched in time for the dispatcher to make statistics. Personnel attendance records are saved in the database so that reports can be formed and printed at the end of the month.
● The usage time and maintenance records of the forklift are saved in the database so that the administrator can notify relevant personnel for maintenance in time.
● When the forklift is driving inside the warehouse, its position information needs to be uploaded to the management system in time for every 20 meters forward, so that it can be deployed by the dispatcher.
● Before the forklift performs its task, the system automatically calculates its best driving route. When the forklift is operating in the warehouse, its driving route and speed must be calculated and uploaded to the management system in time before the forklift is operating in the warehouse. When an employee is slow to work, the dispatch administrator issues a warning to him.
2.2 System performance index requirements
● The accuracy rate of forklift recognition and personnel recognition of the access control system reaches 99.99%;
● The automatic forklift identification success rate of the positioning system reaches 99.99%;
● All equipments in the system have reliable performance, and the mean time between failures in continuous operation is more than 6000 hours;
● The use time of each forklift, the time of entering and leaving the warehouse, and the attendance records of each personnel must be completely and accurately recorded in the system database, and the data records have backup plans;
● The identity data of forklifts and personnel is guaranteed to be unique and cannot be copied;
● Install a reader antenna every 20 meters on the line, work at the same time, do not interfere with each other, and do not read each other;
● In the access control system, use a split reader and install two antennas to ensure that the card reading areas of the two antennas do not overlap
● All UHF RFID electronic tag automatic identification systems are restarted every night to ensure the reliable operation of the system software and ensure an average of 1 year of trouble-free operation.
● The automatic identification of electronic tags fails, and the system provides manual error correction function to ensure 100% completion of forklift personnel identification.
Three, the overall design of the system
3.1 Overview
The forklift dispatching and positioning monitoring and management system is a closed-loop real-time information processing system based on the international advanced RFID technology for data collection in a long-term uninterrupted local area network environment. It requires high-performance processing efficiency, highly reliable security strategies, and flexible and convenient system configuration. , Easy to install, maintain, upgrade, promote and use. Therefore, the system needs to be comprehensively considered in terms of advancement, stability, security, openness, and scalability in terms of RFID reading and writing system equipment, software system architecture, host platform, database platform, and application server platform.
Based on the understanding of the project objectives of this phase, our company has designed the overall scheme of the RFID management information system for forklift dispatching, positioning and monitoring based on the core framework design based on the RFID-based WEB service system. The system adopts a centralized deployment mode, including data collection, data storage, database, application services and interface applications covering the entire process of forklift entry and exit, transportation, and stop. The system comprehensively uses .NET and C++ as the core technology system framework, and adopts flexible configuration and the separation of business and process control to ensure the efficient operation of the RFID management information system for forklift scheduling and positioning.
Our company believes that a centralized forklift dispatching and positioning RFID management information system should follow the following principles when constructing:
Adaptability: to meet the requirements of the company’s existing network organization, business management, service quality, etc., and to consider and adapt to the status quo of the company and the status quo of modern logistics process management during design and construction.
Flexibility: The system is capable of enterprise development, flexible design, adjustment of business processing procedures and organizational structure, and can adapt to future business development and changes, making the system forward-looking.
High reliability and stability: This system is an RFID management system supporting enterprise warehousing and logistics operations. The reliability, safety and accuracy of the system are very important. The use of RFID technology and computer technology is to improve the ability of dispatch management. The selection, configuration, installation and deployment of RFID equipment are all to improve the level of customer management and the timeliness of information processing. If the reliability of the system cannot be guaranteed , It greatly reduces the availability of the system. Therefore, the system should have strong fault tolerance, disaster tolerance, complete system security mechanisms, and reliable error correction and recovery capabilities.
Advancement: The system’s RFID reading and writing system equipment, host system, network platform, database system, and application software should use the current international advanced, mature and applicable technologies, and adopt international standards and specifications. Among them, the RFID reading and writing system equipment adopts the UHF RFID reading and writing system equipment that Sincere Technology has independent property rights, product performance is comparable to similar foreign products and can replace foreign products.
Effectiveness: For the accurate and fast RFID management information system of the escort integrated business information processing, high-sensitivity and high-performance RFID read-write system equipment and multi-process concurrent operation can greatly enhance the efficiency and accuracy of system data collection Performance, real-time and processing capabilities of collected data. RFID reading and writing system equipment has demonstrated strong data collection capabilities in application practice. The system application platform has a parallel mechanism to process data in parallel to improve the processing efficiency of large data volumes.
Openness: The system should adopt a unified system platform, a unified RFID read-write system device interface, a unified data dictionary, a unified data format, and a unified interface between modules. The construction of the system fully considers the openness and adapts to the rapid development of warehousing and logistics business.
Maintainability: The system adopts standard interface design and modular design to make it have good maintainability. At the same time, a friendly application operation and maintenance interface is provided, and the maintenance operation is simple.
Ease of operation: a unified style of friendly operation interface, complete operation process and operation manual, easy for operators to learn and master. The construction of the system should focus on satisfying the scientific, convenient and reasonable habits of forklift dispatch management.
The design of the RFID management information system for forklift dispatching, positioning and monitoring is a highly abstract summary based on a full analysis of the status quo and development direction of the warehousing logistics management business. In the design, various factors are comprehensively considered, and a reasonable trade-off is achieved to achieve a balanced compromise between the accuracy of data collection, the efficiency of data processing and the flexibility of the system.
3.2 System composition
According to the requirements of warehouse management, the framework of the forklift dispatching and positioning monitoring management system can be divided into four levels, namely the equipment layer, the collection layer, the integration layer and the application layer:
Device layer
The equipment layer constructs the application environment of RFID, including tags (identifying personnel, forklifts, etc.), antennas, readers, computer hardware, servers, network equipment, terminal equipment, etc.
Acquisition layer
Forklift and personnel information collection based on RFID technology, the information in the RFID tag is collected through a reader, and the information is transmitted to the integration layer after decoding, anti-collision, multi-channel information deduplication, information filtering, classification and other information preprocessing.
Integration layer
The integration layer is the supporting platform for RFID applications, supporting the input, acquisition, transmission, processing and collaboration of RFID information. Including RFID middleware, integration platform, information transmission, etc.
●RFID middleware solves information semantic definition, reader information collection, information writing (one-time writing or segment writing) and database interface.
●The integration platform adds interfaces with third-party applications on the basis of middleware (providing data interfaces for various application systems) to make various application software compatible with RFID.
●Information transmission completes the transmission structure of information between different places and points, and the security structure of system information transmission in different places, and realizes the distribution and circulation of information.
Application layer
The application layer is the RFID back-end software system and application system interface, forming a customizable application system. The forklift dispatching and positioning monitoring and management system is composed of application systems such as the task distribution system, the forklift dispatching query system, the personnel dispatching query system, the forklift positioning system, and the forklift access monitoring system.
[ad_2]