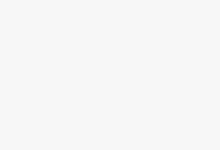
RFID warehousing material management system solution
[ad_1]
1. System overview
Warehousing management is an important link between enterprise production and operation and the logistics supply chain. With the rapid development of modern logistics, it is the goal pursued by the logistics industry that a single corporate logistics and the social logistics that it constitutes together achieve efficient and sustainable development, and the use of corporate warehousing functions is related to the development of the entire logistics chain.
According to the use requirements of various objects such as material users, purchasers, financial personnel, decision-making management personnel, and through the management of each module, the system comprehensively reflects the procurement, warehousing, loss and use of personnel and various departments. At the same time, the system combines automatic identification technologies such as radio frequency (RFID) and two-dimensional barcodes to comprehensively track and manage materials in all stages of warehouse management. Enterprise managers can rely on the powerful query and report functions of the system to understand various material information in a timely and accurate manner, providing a convenient management platform for enterprise decision-making, speeding up the turnover of materials, improving economic benefits, and reducing enterprise management costs.
2. System function
Procurement management: procurement demand management, procurement plan management, supplier information, quality and price comparison management, contract order management, payment and invoice management, delivery management, report management, etc.;
Inventory management: Inbound management, outbound management, requisition management, borrowing management, inventory management, carry-over management, query reports, label/barcode management, etc.;
Basic data: material classification management, outsourcing material management, approval process management, enterprise barcode management, measurement unit management, engineering management, etc.
Three, system characteristics
The system replaces the traditional manual accounting method, effectively improving work efficiency;
Support multiple ways of entering and exiting the warehouse, combined with automatic identification technologies such as RFID and QR codes to track the materials throughout the process;
The unique purchasing volume calculation function integrates purchasing requirements, inventory and in-transit volume, and automatically obtains the available volume;
Through the establishment of supplier files, excellent suppliers are selected to reduce future procurement risks;
The system increases the management function of tools, and records the borrowing, returning, using, and scrapping of tools;
Rich report query function, report details can be modified according to user needs;
Powerful authority management, set functions and data read and write authority for different personnel and departments;
Extensive data interface design meets the requirements of data transmission with different financial software.
Four, typical users
Shandong Huanghai Shipbuilding Co., Ltd.
Haiyang Nuclear Power Equipment Manufacturing Co., Ltd.
Weihai Guangwei Fishing Tackle (Group) Co., Ltd.
Five, application areas
For logistics, electric power, manufacturing, medicine, wholesale and retail industries, logistics distribution centers and warehouses.
Sales Hotline: 0631-5698111
[ad_2]