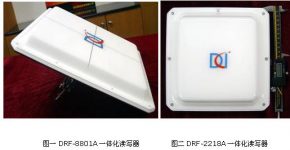
RFID-based logistics warehousing distribution center solution
[ad_1]
Overview
SHENZHEN DDCT TECHNOLOGY Co. Ltd is a high-tech enterprise specializing in the development, production and sales of new generation radio frequency identification products, satellite communication positioning and navigation products and wireless communication systems.
The company has a large number of radio frequency technology and communication system technical personnel, and the core technology of radio frequency identification is in a leading position in the country. Independently developed and formed a series of products such as RFID, GpsOne, satellite communications, and digital radio frequency modules. It has unique and extremely strong product development capabilities in the industry to meet the product needs of different user groups, and its sustainable development capabilities are gradually being strengthened.
The company’s radio frequency identification equipment adopts the most advanced technical design solutions, which has substantially improved the technical performance of the company’s RFID series products. Using the 18000-6B, EPC dual protocol compatible solution, for passive radio frequency tags, it successfully solved the identification problem of long-distance, high-speed moving target markers, and at the same time, it greatly reduced the cost and solved the fatal weakness of the product’s poor anti-collision ability. . On the basis of ensuring the performance of high technical indicators, the product greatly meets the green environmental protection standard of low emission power. The DRF8800, DRF-8900, DRF-6800, and DRF-900X series products of Modern Communication are in a leading position in the industry in terms of their technical indicators.
In this plan, in view of the characteristics of the company’s RFID reader products and the workflow of the logistics industry, especially the characteristics of warehousing, a series of solutions based on the company’s existing technology are put forward in a targeted manner. Aiming at each link in the logistics, help the logistics management personnel of the enterprise to carry out comprehensive control and management of the operations such as the inbound, outbound, moving, inventory, and ingredients of the inventory items, effectively use the warehouse storage space, and improve the warehouse’s warehousing capacity. Realize first-in, first-out in the use of materials, and ultimately improve the utilization rate of the storage space of the enterprise’s warehouse and the quality and efficiency of the enterprise’s material management, reduce the cost of enterprise inventory, and enhance the competitiveness of the enterprise in the market.
1. Scheme process
This solution is mainly used for the automatic identification management of the warehousing, storage, sorting and outgoing of bulk goods in the distribution center. It consists of the radio frequency tags installed on the goods or pallet turnover boxes, the radio frequency identification system installed in each link of the distribution center process, and the intermediate Components and WMS software. When the tagged target passes through the set signal collection point, the tag immediately emits a radio frequency signal with representative identity characteristics, which is received by the system, processed by the middleware, and sent to the WMS system. The WMS system sends out a series of instructions to achieve Functions such as information collection, warehousing and storage, regular inventory, and sorting out of the goods.
2. Scheme composition and design basis
(1) Elements of the plan
The RFID-based distribution center solution consists of multiple sets of radio frequency identification systems, middleware, database systems, and warehouse management information systems (WMS). in:
—-Radio frequency identification system: It is composed of various types of readers, mainly used to read/write information on electronic tags.
—-Middleware: Between the reader and the back-end database and application software, it provides mechanisms for program management, signal filtering and collection, event management, security management, and network management.
—-Database system: input, analysis, output and management of various data information.
—-Warehouse Management Information System (WMS): controls the actions of each link in the process, completes receipt and storage management, inventory allocation management, picking and delivery management, as well as data backup, data query, data statistics, and report generation of the entire system , Report management.
(2) The basis of the scheme design
1. Features and advantages of RFID technology
RFID is a flexible application technology that is easy to control, simple and practical, and especially suitable for automatic control. The identification work does not require manual intervention. It can support both read-only working mode and read-write working mode without contact or aiming; Can work freely in a variety of harsh environments: short-distance radio frequency products are not afraid of oil stains, dust pollution and other harsh environments, and can replace bar codes, such as tracking objects on the assembly line of a factory; long-distance radio frequency products are mostly used in traffic, and the identification distance can be Up to tens of meters, such as automatic toll collection or vehicle identification. Its unique advantages are beyond the reach of other identification technologies. There are mainly the following aspects:
Convenient and fast reading: Data reading does not require a light source, and can even be carried out through the outer packaging. The effective identification distance is greater. When passive tags are used, the effective identification distance can reach more than 8 meters; according to different types of reading devices, the maximum reachable distance is 2 meters, 4 meters, and 8 meters.
Fast recognition speed: as soon as the tag enters the magnetic field, the reader can read the information in it instantly, and it can process multiple tags at the same time to achieve batch recognition;
The label data can be changed dynamically: the programmer can write data to the RFID label, which gives the RFID label an interactive portable data file function, and the writing time is less than that of printing a bar code;
Better security: It can not only be embedded or attached to products of different shapes and types, but also can set up password protection for the reading and writing of label data, thus having higher security;
Dynamic real-time communication: The tag communicates with the reader at a frequency of 50-100 times per second, so as long as the object attached to the RFID tag appears within the effective recognition range of the reader, its position can be dynamically tracked and monitored .
2. Description of the characteristics of RFIDTAG electronic tags
Anti-collision technology: Compared with barcodes, it does not need to be directly aligned and scanned, and the reading and writing speed is fast. It can recognize multiple targets and recognize in motion, and can recognize up to 50 at the same time per second.
International frequency: 915Mhz ±13MHz
Flexible internal storage space: manufacturers can define the storage capacity of each model product and the number of bytes in each sector according to their own needs, and the read-write device can read the memory configuration information, which is convenient for operating different tags in a comprehensive application product.
Large data capacity: The two-dimensional barcode (PDF417) with the largest data capacity can only store up to 2725 numbers; if it contains letters, the storage capacity will be less; RFID tags can be expanded to dozens of K according to the needs of users;
Internationally unified and non-repetitive 8-byte (64bit) unique identifier (UID), of which the first 1-48 bits are fixed as “EO”.
It can be read and written repeatedly and the sector can be locked once independently, and can lock important information according to user needs; existing products generally use 4-byte sectors, and the memory ranges from 512bit to 2048bit.
Long service life (≥10 years or 100,000 times of reading and writing), no mechanical wear, no mechanical failure, and can be used in harsh environments. (Working temperature: -25 degrees ~ +70 degrees)
Flexible packaging, diversified packaging: its ultra-thin and a variety of different sizes, so that it can be packaged in paper, plastic products (PVC, PET), can be used in different occasions, can also be laminated to make cards.
3. Engineering plan
In view of the characteristics of the logistics industry, this plan is divided into two parts: one is warehousing management; the other is the management of transportation links in the logistics transportation chain.
(1) Warehousing, logistics and distribution management
1. The design ideas of the warehouse management system
With the continuous growth of business volume and the continuous improvement of customer demand, warehouse management is also facing more and more challenges. How to reduce inventory investment, strengthen inventory control, reduce logistics and distribution costs, and increase the utilization rate of space, personnel and equipment , Shortening the order process and replenishment time has become a common concern of all warehousing departments. Among the outstanding problems can be summarized into two:
The first is the control of warehousing operations. In traditional logistics systems, warehousing operations have always played the most important role, but now that the manufacturing technology and transportation systems are quite developed, the role of storage operations has also become more important. And the amount of change. Although its original function of adjusting production and demand has not changed, in order to meet the small and diverse needs of the market today, the importance of picking, shipping, and distribution in the logistics system has been more important than the storage and storage function. .
Modern warehousing must not only realize the storage function of goods, but also have clear marks on the types, quantities, owners, and storage locations of the goods in the warehouse. The stored goods should have a clear upstream and downstream data connection in the supply chain.
Schematic diagram of warehousing goods storage
The second is the storage plan management problem
The current market development trend is that each order is getting smaller and smaller, but the total number of orders is increasing, and the operation time is getting shorter and shorter. Customers are asking suppliers to provide more and more sophisticated products and services. , The price that can be provided to the enterprise is constantly decreasing-this is a common problem faced by current suppliers.
In the warehouse operations of many companies, the problems they face are poor planning, unclear inventory, no pre-notification for receipt and delivery, and no automatic warning method for the upper and lower limits of inventory. Such problems have brought about changes in the implementation of warehousing operations. Requirements.
At present, in enterprise applications, the solution to the first problem above is to introduce control technology (bar code, wireless data communication, POS machines, etc.) for warehouse control. The solution to the second problem above is to introduce ERP (Enterprise Resource Planning) The system is used for warehouse management.
According to the usual implementation method, the ERP information system and the warehouse control system are run on two different platforms (hardware, software and network). The ensuing problem is that it is difficult to call between different platforms, because each platform provider has its own standards, and therefore cannot be integrated. In addition, there are also problems with the integration of business processes within each platform within its own scope. Through IRFID technology, the two systems are organically combined, so that enterprises and enterprises can share information resources and effectively reduce inventory costs.
2. Application of RFID in inventory management
Electronic tags are suitable for application in current scientific inventory management systems because of their anti-collision, arbitrarily packaging, long service life, and reusable characteristics.
The current inventory management system usually supports its own inventory management by means of barcode labels or manual inventory management receipt writing. However, the barcode is easy to copy, non-smudge-proof, non-moisture-proof, and difficult to read.
There are also unavoidable shortcomings such as the cumbersomeness of manual document writing and easy to cause man-made losses, so that the current domestic inventory management supply chain always has defects. With the application of electronic tags, the latest technology products, the above-mentioned problems can be fundamentally solved.
Seal the electronic label into a card shape, stick it on the package or pallet of each goods, and write the specific information, storage location and other information of the goods in the label. At the same time, the detailed information of the delivery party can be written when the goods enter and leave the warehouse, and fixed or portable card readers are installed in the warehouse and various distribution channels to identify and detect the flow of goods. The advantages of using electronic tags to support the current inventory management system are:
Effectively manage cargo packing operations;
Information collection automation;
Check the source of the product;
Product quality audit in each stage of the manufacturing process;
The information on the electronic label can be changed without changing the product packaging;
Effectively manage loading;
Automatic management results can more effectively complete quality supervision;
The logistics of inventory goods can be tracked throughout the process, and losses and errors can be reduced to the lowest point.
The main function:
• Basic information settings
Including the management of basic information related to raw materials, finished products, suppliers, customers, and system authority management.
• Warehouse Management
Support multiple warehouses and multiple regions, and realize full utilization of warehouse space according to location division.
• Warehouse Management
Warehousing management establishes an interface with the ERP purchase plan and arrival plan, and carries out strict process control from material warehousing to warehousing inspection and shelf storage. Automatic identification technology is adopted to speed up the warehousing operation, and the storage location (location) of the materials can be designated according to the established rules, so that the materials can be stored in an orderly manner. And to achieve accurate batch management.
• Incoming Quality Management
Whether it is a production enterprise or a logistics enterprise, the inspection work of the warehouse purchase is necessary, supporting rapid inspection entry, and providing quality analysis of the goods and the source of the goods (such as raw material suppliers).
• Move library management
Support for moving warehouse operations within and between warehouses.
• Dynamic inventory
Warehouse inventory uses handheld terminals for real-time batch processing operations, with fast inventory speed and high accuracy. Supports dynamic inventory, the inventory process does not affect the normal warehouse operation, and provides accurate dynamic inventory management for continuously operating warehouses.
• Packaging Management
Provide product internal and external packaging management functions, by setting the system to directly generate internal and external packaging barcodes, employees can operate the reading and writing equipment to directly read the finished product out of the warehouse.
• Shipping Management
The system can receive (or directly enter) the delivery plan, automatically generate a list of delivery locations and quantities according to the delivery settings, provide delivery guidance for employees, and cooperate with delivery scan prompts to ensure the correctness of the delivered goods.
• Outbound management
The outbound operation specifies the specific location and quantity of the outbound items according to the outbound plan, and uses the scanning outbound method to improve the outbound speed and accuracy, and avoid manual errors.
• Statistical Analysis
It provides functions such as inventory turnover analysis, warehouse utilization analysis, etc., and alarms for stranded goods.
(2) Distribution center management
1. Flow chart of distribution center
According to the distribution center process, an electronic label is fixedly installed on each pallet, turnover box or goods, and the information of the goods on the pallet or turnover box is bundled with the electronic label and entered into the database. The DRF-8801A long-distance integrated reader is installed at the entrance of the distribution center to read the relevant information carried by the electronic tag on the pallet and transmit it to the WMS system, which will arrange the storage location according to the cargo location information.
1) The DRF-8801A long-distance integrated reader is installed in the picking area of the distribution center to read/write the selected goods information into the electronic label on the turnover box.
2) The DRF-8801A long-distance integrated reader is installed in the sorting area of the distribution center to realize automatic rechecking and out of the warehouse while distributing goods.
3) The forklift truck body is equipped with a DRF-2811A close-range integrated reader to identify the relevant information carried by the electronic tag on the pallet, and perform corresponding operations based on the information.
2. Information flow of distribution center
(3) Management of vehicles in logistics connection
1. Electronic license plate system of customs terminal
For the loading and unloading, entry and exit, and customs clearance of a huge amount of goods at ports and piers and customs, a considerable part of them are transported by vehicles. Therefore, there are many vehicles traveling between ports and customs, and they may belong to different units in different industries such as customs, shipping companies, shipping agencies, freight forwarding companies, port authorities, container yards, etc. It is difficult to dispatch and manage without uniform measures. Customs clearance and the circulation of goods have brought great difficulties. The electronic license plate management system implemented by RFID technology can effectively solve this problem.
The system manages the registration and issue of on-board electronic tags for the vehicles passing by, and installs RFID reading devices at key entry and exit monitoring points, so that the supervised vehicles with electronic license plates can be identified by the system accurately and timely when they pass the monitoring channel. Identify to complete the requirements of vehicle data collection. At the same time, information technologies such as wireless communication are used to submit the collected vehicle information to the management system to complete the verification of vehicle identity, as well as query and statistics, and dispatch functions. Through the application of the electronic license plate system of the customs terminal, the traffic capacity of customs vehicles can be effectively improved, real-time statistics and monitoring of vehicle information can prevent misdetection and missed detection, improve customs clearance efficiency, and prevent organized theft and combat smuggling.
2. Cargo transportation scheduling management system
The vehicle dispatching management system is an important part of the intelligent logistics system. It adopts advanced information and communication technology to collect dynamic and static road traffic information and conduct real-time analysis. According to the analysis results, the vehicle’s driving route and travel time are arranged to achieve Make full use of the limited transportation resources, improve the efficiency of the use of vehicles, but also understand the operation of the vehicles and strengthen the management of the vehicles.
RFID technology can be used as an effective means of information collection in the logistics dispatch system and can be applied in the vehicle dispatch management system. For example, the use of RFID in the freight yard vehicle management system can realize the automatic, accurate, long-distance, and non-stop collection of information for freight vehicles entering and exiting the yard, so that the dispatching system can accurately grasp the real-time dynamic information of the in and out of transport vehicles. Through the implementation of this system, the management level of mobile cargo can be effectively improved, and the collected data can be used for computer research and analysis, so that the law of vehicle operation can be grasped, and the loopholes in the management of logistics vehicles can be eliminated. At the same time, in response to the needs of special groups of users, the company’s GpsOne navigation communication user machine (gps satellite/and China Unicom CDMA base station positioning communication network-to solve the positioning in underground parking lots, tunnels, etc.) is combined with RFID technology. It is convenient to monitor and dispatch off-site vehicles online from time to time, and keep track of materials, personnel, and the status of the vehicle itself.
3. Intelligent vehicle weighing system based on RFID
A vehicle-based intelligent weighing system can be realized by combining the weighing system and the remote RFID automatic identification technology. The system adds the automatic identification function of weighing vehicles realized by long-distance RFID automatic identification to the original weighing management system, and merges the automatically collected weighing vehicle information into the weighing management system. The application of the intelligent weighing management system can improve the weighing efficiency and reduce the waiting time of the vehicle at the place to be inspected. At the same time, the automatic identification and accurate measurement of the vehicle number can effectively prevent the economic loss caused by man-made fraud. In addition, the implementation of the system has greatly reduced the labor intensity of the staff and the error rate of manual weighing. Therefore, the intelligent vehicle weighing system based on RFID realizes the perfect combination of identification, measurement and monitoring. The system can be flexibly applied to non-box-packed materials in logistics transportation, such as coal-based mineral materials and petroleum-based liquid materials. For example, automatic weighing at high-speed intersections to control overloading, and material distribution centers such as docks can speed up vehicle weighing speed and reduce congestion, which has great application value.
Four, concluding remarks
The application of RFID technology can effectively solve the information management related to the flow of materials in the warehouse: RFID tags can be affixed to pallets, boxes or components in the warehouse, and the tags contain information such as component specifications, serial numbers, etc., when the materials pass the installation When the RFID reader at the preset location can complete the automatic inventory information, the wireless local area network transmits the data to the background management information system for sharing, and the command center can obtain real-time material storage information. The entire process no longer requires custodians to use handheld barcode scanners to scan warehouse materials one by one, which will greatly speed up the circulation of materials in the logistics supply chain, reduce manual operation errors, reduce management costs, and improve the efficiency of warehouse management. At the same time, the use of RFID can enable warehouses to quickly and accurately understand their own inventory levels, and prevent possible out-of-stocks due to loss of goods and statistical errors. Effectively support MRP and ERP systems. It is more suitable for the production and logistics operation method with JIT as the purpose. The use of RFID technology can also quickly and accurately locate from a large amount of materials, find urgently needed items, and realize automatic and systematic management in the true sense.
[ad_2]