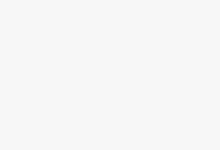
Chuangyi Technology RFID Manufacturing Smart Warehouse Management System
[ad_1]
System background
Warehouse management occupies a core position in logistics management. The traditional warehousing industry is based on the business model of collecting storage fees, and hope that their warehouses are always full. This model runs counter to the purpose of logistics. Modern logistics takes the responsibility of integrating processes and coordinating upstream and downstream. The smaller the static inventory, the better. Its business model is also based on the assessment of the total logistics cost. Since these two types of warehouse management have essential differences in business models, they are difficult to distinguish in specific operations such as warehousing, outgoing, sorting, and tallying. Therefore, we must pay attention to their similarities and differences in analysis and research. Similarities and differences will also be reflected in the structure of the information system.
As the manufacturing environment changes, product cycles are becoming shorter and shorter, a variety of production methods are available, and the requirements for inventory restrictions are getting higher and higher. Therefore, it is necessary to establish and implement a supply chain management system, with the help of computerization and information technology to connect suppliers, Manufacturers and customers are closely united to share inventory risks. Warehousing management can be briefly summarized as 8 key management modes: tracking-receiving-checking-storing-picking-issuing-stocking-returning.
The optimal control part of inventory is to determine the business model of the warehouse, that is, to determine the management objectives and management mode of the warehouse (according to the requirements of the previous design). If it is an execution link in the supply chain, it is a cost center. With service quality and operating costs as the control objectives, we pursue reasonable inventory or even zero inventory. Therefore, an accurate understanding of warehouse item information is very important to the system, so we propose to solve accurate warehouse management.
Warehousing management and precise positioning play a very important role in the entire management process of an enterprise. If timely and accurate purchase, inventory control and delivery are not guaranteed, it will bring huge losses to the enterprise, which is not only manifested in the management of the enterprise. The increase in costs will also make it difficult to guarantee the quality of customer service, and ultimately affect the market competitiveness of the company. Therefore, we proposed a new RFID-based warehouse system solution to solve the problem of precise warehouse management. Let’s analyze the economic benefits brought to the enterprise by adopting radio frequency identification technology.
System advantages
Convenient and fast reading: Data reading does not require a light source, and can even be carried out through the outer packaging. The effective identification distance is longer. When the active tag with its own battery is used, the effective identification distance can reach more than 30 meters;
Fast recognition speed: as soon as the tag enters the magnetic field, the reader can read the information in it instantly, and it can process multiple tags at the same time to achieve batch recognition;
Penetration and unobstructed reading: The barcode scanner must be at a close distance and there is no object blocking the situation before it can read the barcode. RFID can penetrate non-metallic and non-transparent materials such as paper, wood, and plastics for penetrating communication. It does not require a light source and has a longer reading distance. But it does not recognize through conductive objects such as metals.
Large data capacity: the capacity of the one-dimensional barcode is 50Bytes, the maximum capacity of the two-dimensional barcode can store 2 to 3000 characters, and the maximum capacity of RFID is several MegaBytes. With the development of memory carriers, the data capacity also has a trend of continuous expansion. In the future, the amount of information that items need to carry will become larger and larger, and the demand for tags that can expand the capacity will increase accordingly.
Long service life and wide range of applications: its radio communication method allows it to be used in dust, oil and other highly polluted environments and radioactive environments, and its closed packaging makes its lifespan much longer than printed barcodes; the carrier of traditional barcodes is paper, Therefore, it is easy to be contaminated, but RFID has strong resistance to water, oil, chemicals and other substances. In addition, because the barcode is attached to the plastic bag or the outer packaging carton, it is particularly vulnerable to damage; the RFID label stores the data in the chip, so it can be protected from contamination, and the RFID has strong anti-pollution ability and durability.
The label data can be changed dynamically: the programmer can write data into the electronic label, thus giving the RFID label interactive portable data file function, and the writing time is shorter than printing a bar code;
Better security: RFID electronic tags can not only be embedded or attached to products of different shapes and types, but also can set password protection for the reading and writing of tag data, thus having higher security;: because RFID carries electronics Information and its data content can be protected by a password, so that the content is not easy to be forged and altered, and the security is higher.
Dynamic real-time communication: The tag communicates with the reader at a frequency of 50-100 times per second, so as long as the object attached to the RFID tag appears within the effective recognition range of the reader, its position can be dynamically tracked and monitored.
Small size and diversified shapes: RFID does not need to match the fixed size and printing quality of paper for reading accuracy. It is more suitable for the development of miniaturization and diversified forms to facilitate embedding or attaching to products of different shapes and types.
system introduction
The precision warehouse process generally includes several processes: receiving, putting on shelves, picking, replenishing, shipping, and inventory. The following six processes illustrate the specific implementation process of the RFID warehouse management system:
? data preparation
-All delivered goods need to be imported into WMS in advance by EDI, Excel or manual entry
– All customer orders need to be imported into WMS in advance by EDI, Excel or manual entry
? In order to support the use of modern logistics equipment such as RFID or electronic tags, conveying and sorting lines in the logistics center, barcode planning and design are required in the following links.
— Barcoding of all operation units in the warehouse, including pallets and turnover boxes. Paste the fixed serial number label directly on the job container.
— Barcoding of storage locations in warehouses.Encode the cargo location and paste the barcode label in the order of library-rank-position-layer
— Barcode of job documents and job instructions.
— Print the barcode of the document number and product code on the warehousing list, and assist the receiving staff to use RFID for receiving operations
— By printing picking labels, guide pickers to obtain picking tasks and facilitate the identification of goods on the conveyor line
Labels for different purposes
? Receipt
– Use RFID in the receiving area for code discs (if required) and receiving operations. All goods stacked in the receiving area must have a unique pallet
No., the pallet number is pasted on the pallet as a barcode label
– If the SO has not been delivered, the system instructs to send the goods to the temporary storage area
? Tally
– The system designates a corresponding shipping area for the order according to the vehicle information and volume information of each order
– The system automatically matches the received goods with SO, and generates a distribution task for each pallet of goods in the receiving area.
– Tally staff scan the label of each pallet in the receiving area, and move the goods to the temporary storage area or the waiting area of the corresponding order according to the instructions.If needed
To distribute the goods to multiple orders, you need to confirm each shipping area and quantity separately. Use a new pallet when distributing goods and confirm the new pallet number.
– When goods need to be distributed from the temporary storage area, RFID instructs the tally staff to pick the goods from the temporary storage area and then perform the distribution.
? Review
-After the order is distributed, the system prompts the reviewer to review the product and quantity
? Ship
– Scan each pallet in the to-be-delivery area in turn, confirm the vehicle number for delivery
All aspects of warehouse management
The six links of warehouse management:
Receipt
Specific receiving and warehousing operations
(1) Receipt inspection
Key inspection:
Whether the delivery note is consistent with the purchase order;
Whether the arrival of the goods is consistent with the delivery note;
If it does not match, refuse to accept.
(2) Make and paste labels
The specific method is as follows:
Use the selected item coding scheme to encode the inbound items;
Make goods label: write the coding information into the electronic label, and print the paper label at the same time (for manual verification), and then glue the paper label and the electronic together to become the goods label.
Fixing tags on inventory: Considering the high cost of tags, in order to facilitate the recycling of electronic tags, the tags are generally fixed to the items by hanging. If it is not recycled, it can be fixed by pasting.
(3) The on-site computer automatically allocates the location, and gradually downloads the location number and corresponding item number of each operation to the wireless data terminal (handheld terminal or forklift terminal);
(4) The operator transports the goods to the designated storage location and sends the goods into the storage location after checking the location (if necessary, modify the cargo number and quantity information recorded in the location label);
(5) The wireless data terminal sends the actual status of warehousing to the on-site computer to update the inventory database in time.
On the shelf (in storage)
Each box of goods is affixed with a barcode, and after the box is packed, a passive label is installed on the box. The boxed goods with the passive label are palleted according to the storage location read by the PDA in the hands of the staff. An active electronic label is installed on the tray. Put the goods on each pallet on the corresponding shelf;
Pallet indication
Find locations according to different warehouse areas
Assign different locations according to different packages (pallets, boxes, pieces)
According to the attributes of the products (normal products, damaged products) allocation of storage locations
Limited volume, limited weight, limited quantity, limited length, width and height
Mixed batch number and mixed product limited
Combine products of the same batch number
Adjacent selection of similar products
Different order types can be put on shelves in different locations, such as normal purchase orders and return orders
According to the ABC activity of the product, the storage location is allocated
Different shelves
Display on the shelf
Pick up
Picking trolley
1: Trolley downloads batch orders on any terminal of the WMS system
2: According to the optimal path, the system automatically instructs the trolley to sort the goods by SKU;
3: Confirm the picking position information, the trolley will automatically indicate the quantity of “sort while sorting” according to the light system, and press the light to confirm after sorting the goods;
4: The trolley automatically receives system instructions and guides the operator to the next picking position in real time until all batch orders are completed.
Picking location management mode
?Fixed picking
-The picking location needs to set the lower limit and upper limit of the inventory. When the inventory balance is lower than the lower limit, an alarm will be issued to remind the need to replenish.
–Sometimes in order to meet special picking requirements, you can set up a box picking location or a piece picking location. When the box picking inventory balance is below the lower limit, apply for replenishment from the storage area. When the piece picking inventory is left When the quantity is lower than the lower limit, apply for replenishment from the bin picking location or storage area.
– The picking location is set based on the analysis of inventory flow, which will inevitably sacrifice a part of storage space while improving access efficiency.
?Dynamic picking
– Due to seasonal changes in product sales, the ABC dynamics of products will change periodically.
– The use of fixed picking positions will greatly increase the workload of system managers. FLUX WMS supports the setting of dynamic picking positions and dynamically allocates picking positions for products according to the ABC dynamics of the products.
– Set up the FCL picking area and the unpacking picking area in the warehouse.
Different picking operation modes
? Picking tasks can be dispatched in 3 ways
– RFID automatic acquisition
– Print picking labels
– Print a list of picking tasks
?Different picking methods
– Order picking
– Wave picking
? Sorting while sorting-fruit picking style
?First sorting then sorting-sowing type
Replenishment (movement)
When the warehouse needs to be moved, the computing system sends instructions to the PDA in the hands of the operator. After seeing the instructions, the operator locates the corresponding goods, corresponds to the quantity, moves the goods to the corresponding target warehouse, and modifies the corresponding label information after completion, and Send the corresponding data back to the system computer;
? The system supports 2 different replenishment modes
– Timed replenishment: the regular replenishment mode of the logistics center
– Order-driven replenishment: trigger replenishment tasks based on order requirements in emergency
? The picking position sets the minimum inventory, maximum inventory, and minimum replenishment unit.A replenishment task is generated when the stock of the picking location is lower than the minimum stock
? Replenishment tasks can be obtained in the following three ways
– RFID direct access
– Print replenishment label
– Print the replenishment list
? Replenishment operation steps
– Single step operation
-Replenishment off the shelf and replenishment on the shelf
Shipment (out of warehouse)
When it needs to be out of the warehouse, the system computer sends out the warehouse instruction to the operator’s PDA. The operator locates the corresponding medicine and quantity, takes out the passive label on the medicine box, revises the corresponding data, and sends the data to the system computer .
Delivery indication
? Support different types of outbound orders such as sales order outbound, purchase return, inter-warehouse allocation, etc.
? Full tracking of delivery progress
– Order creation
– Partially allocated, fully allocated
– Partial picking, full picking
– Partially boxed, fully boxed
-Partial shipment, full shipment
-Order closed
– cancel the order
? Different levels of delivery control
– Ship by wave
-Ship to order
-Shipment by order line
-Shipment by tracking number
-Shipment according to picking details
-Shipped according to the loading order
? Support the outbound process based on RFID or documents
inventory
The inventory operation process is as follows:
A fixed reader is installed on the smart shelf. The fixed reader scans the passive tags in the fixed area and transmits the scanned data to the system computer. You can also use the PDA in the hands of the operator to scan the stock medicines and send them to the terminal computer.
?Taking inventory model based on process management
– Apply for inventory
-Approval of inventory
– Release inventory
-Print inventory label or list
-Perform inventory
– Confirmation of inventory results
– Inventory post
?Different cycle counting mechanism
– ABC cycle inventory
-Inventory of specified conditions
– Inventory of activities
-Exception inventory
-Random inventory
-Difference inventory
System functions
? Location query function
-Precise positioning of the goods in the warehouse
-Query function for goods in the warehouse
? For the alarm system in the warehouse, such as:
– The product has passed the shelf life
-The product is below the lower limit of the stock or higher than the upper limit of the stock
– The warehouse age is more than half a year
-The order has not been processed for more than 24 hours
– The replenishment task is not executed within 1 hour
-Not on the shelves within 12 hours of receipt
? How the alarm occurs
– SMS
– FAX
– System monitoring interface
Hardware products
This system is a comprehensive solution. The hardware involves barcodes, passive tags, active tags, PDAs and fixed card readers. Among them, barcodes have a unified standard and low technical content, so you can directly choose barcode manufacturers to purchase. Our company mainly introduces active labels and PDAs with higher technical content.
Passive tags
Active tag
Fixed reader
PDA device
Concluding remarks
The application of the intelligent warehouse management system ensures the speed and accuracy of data input in all aspects of cargo warehouse management, ensures that the company can grasp the real data of the inventory in a timely and accurate manner, and reasonably maintain and control the company’s inventory. Through scientific coding, it is also convenient to manage the batch and shelf life of the stocked goods. Using the system’s location management function, you can also grasp the current location of all inventory goods in a timely manner, which is conducive to improving the efficiency of warehouse management.
Beijing Chuangyi Xingsheng Technology Development Co., Ltd.
Phone: 010-58077045 010-58077046
Fax: 010-58077046
URL:www.radio99k.com
Address: 2501, Block B, Riyuetiandi Building, South Second Ring Road, Beijing
Create a better wireless experience
[ad_2]