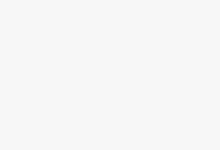
Chongqing New District i3RFID Manufacturing Logistics Collaborative Management System
[ad_1]
1. Project overview
1. Brief analysis of background
The joint development of manufacturing and logistics has become a general consensus between manufacturing and logistics. With the rapid development of information technology and the globalization of the manufacturing industry, the global coordination of business flow, logistics, information flow, and capital flow in the manufacturing industry increasingly depends on the universal application of information technology. RFID technology, with its non-contact, long-distance, real-time and accurate, dynamic and massive interactive item information characteristics, avoids manual intervention in the tracking process, enabling enterprises to grasp the flow of information and information in the entire supply chain in real time, accurately and efficiently. Changes to enhance the degree of enterprise informatization and competitiveness.
At present, low-frequency passive RFID is widely used, but low-frequency technology determines that it cannot meet the requirements of ultra-long-distance automatic identification; Active RFID is equipped with its own battery, which can provide power for all devices to work, and the effective reading distance It has also increased compared with the former. However, UHF tag readers that achieve long-distance (several meters to hundreds of meters) reading and writing are often bulky, difficult to install, and costly, and long-distance recognition is mostly achieved by increasing the transmission power of the reader Yes, in addition to electromagnetic pollution to the environment, it may also cause potential harm to users. In short, the existing active electronic tag technology cannot meet the comprehensive requirements of manufacturing logistics such as ultra-long distance, low transmission power, long tag life (power saving), high collision resistance, precise location of the area, and high reliability.
2. Project innovation
The solution adopted in this project is based on the i3RFID patented technology system of West Valley’s completely independent intellectual property rights, using 2.4GHz military direct sequence spread spectrum (DSSS) multi-channel collaborative technology system, which can fully meet the requirements of manufacturing logistics for ultra-long distance and precision. Special requirements for positioning, mass reading and writing, and flexible power saving.
Different from ordinary active tags, West Valley i3RFID tags have a transmission power of about 0.1W and a read-write distance of more than 2000 meters. Most of the time, they are in a deep sleep state. The tags will only switch when they enter the working range of the read-write locator. To the low-power monitoring state; if a work instruction is received, the tag will complete the work in milliseconds, and then switch to the low-power monitoring state; the work instruction is over, the tag will automatically enter the deep sleep state; fundamentally reduce the battery energy Consumption, while avoiding external environmental electromagnetic pollution, avoiding multi-tag read-write conflicts, and ensuring information security.
620)this.style.width=620;” border=0>
In response to the special requirements of all aspects of manufacturing logistics, West Valley i3RFID tags can be used in as many as 25 working modes according to the instructions of the coordinator (ordinary active card, monitoring, regional positioning, precise positioning, mass read-write mode, etc.) On-demand dynamic or adaptive conversion in the air to meet the differentiated needs of various occasions such as procurement, identification and storage, inventory, material positioning, dumping, vehicle delivery, and sales.
2. User needs
The logistics system of the assembly plant in Chongqing New District reflects the diversified and comprehensive needs of the assembly manufacturing industry for logistics information, and puts forward high requirements on the technical level of the RFID system. Users require that turnover containers (trolleys, plastic boxes, storage cages, etc.) be used as the management unit. From the beginning of the procurement process, through warehousing, inventory, material picking, assembly, and even the entire vehicle delivery and dealer links, the entire process will be realized. Collaborative management of automated logistics information for assembly parts such as nuts and finished vehicles from the factory.
620)this.style.width=620;” border=0>
The assembly plant in the new area mainly includes CKD warehouse, maintenance workshop, manufacturing workshop, shipping warehouse, and aisles connecting various areas. The database of the factory area should be able to query the current location of each turnover container in real time, as well as the type and quantity of parts in the container at that time:
1. CKD warehouse area and its passageway realize automatic identification of warehouse entry and exit, and automatic inventory and search at the same time:
The inbound channel is required to automatically identify the supplier’s shipment (delivery means to pack the parts in a turnover container), and allocate a storage space in the warehouse, and at the same time send a receipt confirmation to the supplier through the logistics information management system; The storage area can locate the container in real time and record the confirmation information of entering the storage location; the storage area is fully automated, without manual scanning with a reader;
2. Real-time update of container information in maintenance workshops and manufacturing workshops
Automatic identification records are used for containers entering and exiting the workshop. After the parts in the container are selected, the updated information can be recorded in the container label in time, and the management personnel can query the latest parts utilization information in real time. After the empty container comes out of the workshop, a new storage space is automatically allocated in the empty container area and sent to the container label, and the carrier’s storage space information is prompted at the same time; the container with remaining parts should be sent back to the original storage space of the original warehouse, and the storage should be inspected. Whether the position is consistent;
3. The delivery warehouse realizes the exchange of vehicle distribution information
Assemble the whole vehicle and carry the label, which will be automatically identified and scanned at the factory; the dealer’s warehouse will automatically enter the warehouse and scan and send back confirmation of receipt information. After the vehicle is sold, the label can be recovered and reused.
Three, system architecture
1. RFID hardware composition
West Valley i3RFID Electronic Tag
As the most basic hardware unit, West Valley i3RFID electronic tags are mainly affixed on the surface of turnover containers and large parts, products, etc., to record the contents of the containers;
West Valley i3RFID wireless reader/writer locator/reader:
Installed in passages, warehouses, workshop entrances and exits, factory entrances and exits, etc., mainly used to read or obtain and modify the information in the electronic tags in the working area, and transmit it to the central data collector; long read and write distance, few outlets , Covering a large area, can automatically carry out inventory and logistics monitoring;
West Valley i3RFID handheld reader:
It is used in the occasions where manual participation is required for receiving and counting parts, workshop parts picking, etc., real-time update of the content information contained in the label of the turnover container, and wireless upload to the central database;
West Valley i3RFID Coordinator:
According to different application occasions and needs, dynamically adjust the label working mode, working channel and related working parameters. For example, when regional positioning or precise positioning is required, adjust from the default monitoring mode to the positioning mode, locate the label object in real time, or in a large warehouse The mass reading mode is adopted inside, and the anti-collision high-speed real-time monitoring of the transportation and storage matching information of each container;
West Valley i3RFID Central Data Collector:
Upload the information sent back by the reader to the database of the control center computer.
2. Information Management Software System
Original SCM in the factory
Data interaction subsystem: It is divided into reading module, writing module, action instruction module, and data transmission interface. The system publishes XML files to the SCM system through Webservice, or parses the data in the SCM system and sends it to the RFID system.
Four, function realization
Although the logistics requirements of each workshop or each link are different, the basic processes of multiple links such as delivery, entry, maintenance, and complete vehicles are relatively similar. They can be divided into “automatic identification of inbound and outbound”, “inventory of storage areas”, and ” There are four basic processes including “goods search and precise positioning” and “parts purchase and picking”.
1. Long-distance automatic identification of warehousing and exit
This process covers the automatic identification of containers entering and leaving the factory area, warehouses, passages and workshops. It is also applicable to the warehousing and outgoing links of the vehicle off the assembly line, leaving the factory, and selling by dealers. Through the automatic identification process of entering and leaving the warehouse, the user can know which part of the logistics and the factory area the label object currently exists in.
After the supplier confirms the shipment, the information contained in the i3RFID tag of the turnover container is confirmed. The container arrives at the factory after transportation, and the coordinator installed at the entrance and exit of the factory and warehouse wakes up the electronic tag on the turnover container, so that it enters the state of communicating with the access control reader: i3RFID tag transmits its own ID number and the container tag The stored parts information is sent to the reader and entered into the database via the central data collector, and the tag enters the sleep state again. at this time. The SCM system can then call out the supplier’s shipping list for comparison. In the same way, the coordinator and reader installed at the door can obtain the information of the container in the same way when the container enters the passages between the workshops and areas, and update the location of the container and the parts it carries. information.
Among them, the West Valley i3RFID reader antenna has no directivity limitation, and the read-write distance can reach 2000 meters. For super large logistics warehouses and warehouse areas, only a small amount of simple construction is required to achieve the overall logistics information collaborative management of the entire area. The purpose: The mass read-write mode of tags can better adapt to the information interaction requirements of goods in and out of warehouses and dumps under high throughput.
620)this.style.width=620;” border=0>
2. Fully automatic storage area inventory
Warehouse inventory has always been carried out by warehouse managers traversing all shelves and counting the goods in turn. After RFID technology is applied to the logistics industry, most of the current methods are to use handheld readers to take inventory of containers, containers, barcodes or electronic tags in turn, and the nature of its traversal has not changed. West Valley i3RFID, with its advantages of long-distance multi-channel collaborative technology system, can completely free the inventory from manual intervention and realize fully automatic inventory.
In terms of specific implementation, three or more readers are installed at a fixed point in the warehouse area of the inventory, and the readers can communicate with the central control computer by wireless or wired connection. The central computer sends an inventory instruction to the coordinator, and the coordinator wakes up the electronic tag on the pallet according to the instruction. The tag sends ID information to the reader to confirm that the product is within the inventory area; if necessary, the tag can also be used. At the same time, the list of goods stored in the label is sent, and the information stored in the database location is transmitted to the management information system for comparison.
Not only that, the West Valley i3RFID system can also fully support the traditional inventory method. The user can fix the reader on the forklift or hold the reader by the library personnel, and inspect the electronic tags in the warehouse through a certain inspection route. Unlike the traditional library, the forklift driver or the library personnel do not need to approach The label of each pallet only needs to be inspected by a specific route. Because West Valley i3RFID has an ultra-long reading and writing distance, there is no need to go through all the shelves during the warehouse, and only a specific simple route needs to be arranged in advance, and the reading and writing radius covers all The shelf is fine.
In addition to the warehouse area, this inventory work method can also be used to query information in a specific area. For example, users need to know how many containers are in a workshop or warehouse at a certain time, how many parts are in the containers, and whether there are containers that can be used in other links. They can also check the containers in the area of interest in real time through inventory. With quantity.
3. Goods search and precise positioning
West Valley i3 RFID tags and readers can not only realize the automatic identification of containers entering and leaving the factory area, entering and leaving the warehouse, entering and exiting each channel, entering and exiting each workshop, but also allowing users to know which location of the workshop or warehouse of interest the container currently exists. In this way, detailed searches such as picking parts can no longer rely on database queries or search by warehouse managers. The RFID system that adopts West Valley i3RTLS real-time positioning patent technology can realize the function of precise positioning with RFID hardware conditions. When finding the location and picking up parts, the coordinator sends a wake-up signal to the tag of the target container. When the tag is monitored, it receives an instruction, and its own buzzer and diode indicator start to work to prompt the location of the container; in the manufacturing workshop, coordinate The device commands the tag to enter the positioning mode, and the tag and the reader work together to upload the location of the container in real time.
4. Parts procurement, picking and delivery
CKD components must go through the steps of contracting by the supplier, warehouse storage in the factory, and sorting and sorting of containers, and finally transported to the manufacturing or maintenance workshop for production use. The parts are marked with barcodes or passive labels, and scanning them requires manual assistance, which makes it difficult to realize functions such as automatic warehousing and searching.
The West Valley i3 RFID tag is installed on the container of the parts, which realizes the one-stop information transmission and update service from the supplier link to the application of the parts in the manufacturing workshop.
Purchasing link
We supply the shipping parts with labels for special containers in commercial factories. Every time the parts of a container are counted, the parts list will be written into the label through the wireless reader or hand-held reader directly connected to the computer, and the list information will be sent through the network SCM system. To the factory.
Inventory inventory
When warehousing in the factory area, a wireless reader or a handheld reader connected directly to the computer is also used to read the parts list, open the container and count, update the label information, and confirm the receipt.
Parts sorting
The parts are sorted and sorted according to the parts list required by the workshop, and transported in containers. The sorting office can use the wireless reader or hand-held reader at the warehouse door to write the label of the new unit and indicate the receipt Workshop, responsible person and other information.
Parts shipping
The label of the container with newly written information is transported to each workshop with the container, and wireless readers are installed in the passage and at the entrance of the workshop to track the position of the container and update information in real time.
Five, customer evaluation
The RFID logistics system of the assembly plant in Chongqing New District has successfully realized the full deployment of all workshops, warehouses, passages and other full-scale construction facilities in the entire plant. It has fewer outlets, low cost, read and write distance beyond the original imagination of users, and there is no directional restriction on reading. Perfectly docked with the existing logistics management software system, greatly reversing the inconvenient impression that the traditional RFID system has insufficient reading distance, limited reading direction, and manual scanning of inventory, and further improved the level of manufacturing logistics information management , Is another high-level demonstration project for information technology to enhance the strength of traditional industries.
Appendix: Company Profile
Xi’an West Valley Micropower Data Technology Co., Ltd. is a professional IoT solution and product supplier, with the first domestic 2.4G ultra-low power radio frequency PSoC (Programmable System on Chip) “Tangxin One” IoT Based on the core engine, it has built a multi-channel collaborative architecture radio frequency identification i3RFID technology system with completely independent property rights. It is the drafting unit of the 2.4GHz active RFID national standard and the 2.4G RTLS real-time positioning system national standard.
Xi’an Xigu Micropower Data Technology Co., Ltd.
Address: 5F, National Optoelectronics Base, No. 77, Keji 2nd Road, Xi’an High-tech Zone, China Post Code: 710075
Telephone (86-29) 8845-2611 Fax: (86-29) 8845-2610
URL:
www.saycool.cn
Email:
[email protected]
Technical service: 400-6688-186
[ad_2]