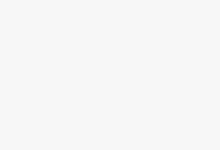
RFID container management
[ad_1]
The global circulation of goods uses containers as carriers, especially sea containers. There are about 2 million containers produced in the world every year, and more than 50% are produced in China. In 2004, the global container holdings were about 21.87 million. Container manufacturers and container transportation management companies undertake a large number of heavy statistical management tasks such as production and transportation, finished product transportation, and stacking storage. After the container leaves the factory, it is impossible to know the location and status of the container in real time, and whether it has arrived safely at the yard. The complicated procedures for entering and exiting the yard lead to long queues of consignment vehicles. In addition, find the designated container on the huge yard Very difficult, not only a waste of time but also error-prone. Since it is impossible to know the number of containers on the yard and the vacancies in real time, the utilization rate of the yard is invisibly low, and enterprise resources are wasted.
The ACTIVE RFID technology of Shenzhen Bisha Technology Co., Ltd. can adapt to the harsh environment of the container production line and the metal box group of the yard. It can track the containers and consignment vehicles in real time during the product offline and transportation links, and realize the container (container production management) , Automatic management of consignment vehicles and storage yard (container storage status) management. The RFID-based container management system uses 2.4GHZ active electronic tags. The 2.4GHz active electronic tag has the function of target recognition and/or micro-area positioning. It adopts advanced CMOS 0.18 um low-power integrated circuit, which meets the design of small size and low-power performance, and can be used in high-risk environments. Without affecting the transmission distance, the battery life is more than 4 years.
Electronic tags (container electronic tags and trailer electronic tags), readers, on-board reader systems, factory exit monitoring subsystems, yard automatic management subsystems, and central monitoring subsystems.
Factory monitoring subsystem: monitor and record the information of the factory container, the information of the consigned vehicle, the occurrence time, the operator, etc. Statistically analyze the delivery status of various containers.
Yard container management system: monitor and record the information of the containers passing through the gate, the corresponding hauling vehicle information, the time of the incident, the operator and other information, the management of the container stacking position information in the yard, quickly and accurately find the status of the container; the image of the 2D container The storage yard map and the function of placing and finding boxes.
Three, the system process
The normal working process of the system is as follows: install the electronic tag with the information of the container on the container of the new production line, confirm the container number during the operation of the stacker, and then leave the factory. At the gate of the factory, the system automatically collects container information and consignment vehicle information. When consignment vehicles enter and exit the yard, the system automatically collects container information and consignment vehicle information, and dispatches the stacker to command the stacking container location through the transmission system.
The RFID container management system pioneered the use of long-distance RFID technology for container tracking and management, and realized the automatic identification of boxes and vehicles, which greatly shortened the time required for the previous manual operation mode, and accelerated the delivery of offline products. The speed of transportation and yard storage; it also reduces the error input of information and improves the accuracy of information collection. These will achieve good economic benefits in the company’s cost control, and enhance the competitiveness of the company. In addition, its social benefits should not be underestimated. It improves the working environment of the staff, reduces the amount of manual work of the staff in harsh environments, and truly serves the purpose of increasing productivity with technology.
Five, system advantages
All equipment of this program meets industrial-grade standards for dustproof, shockproof, and high temperature. Active 2.4GHZ electronic tag, stable reading and writing, long reading distance, parameters can be set according to user needs, easy to use. Readers are installed at key points such as the entrance of the container factory and the entrance and exit of the yard to realize dynamic reading of tags without stopping. It speeds up the delivery, transportation, and yard storage of offline products, improves the accuracy of information collection, and reduces the manual work of staff in harsh environments.
1. Technical application: In fact, major trading countries in the world, including China and Japan, have opened up 433MHz based on the ISO 18000-8 standard for active RFID products. The Global Radio Frequency Committee is working hard to promote the use of unified high frequency, ultra high frequency and microwave frequencies, so that RFID can be used smoothly on a global scale.The 2.45GHz active electronic tags and readers produced by Bisha Technology are a model for long-distance identification applications.
3. Time limit features. A typical RFID device can only read the historical data stored in the RFID tag or electronic seal when the goods and the container pass through the reader. However, it is more effective to transmit the relevant data of the container directly to the truck driver during application. For example, when there is a problem with a refrigerating unit on a trailer, it is more effective for the driver of the trailer, rather than the headquarters staff who are thousands of miles away, to take measures.
4. Cost issues. On some containers that use electronic seals, we need some handhelds to perform operations, but most occasions and applications do not require handheld devices. Although the use of satellites to track containers does not require RFID-like handheld devices, it does need to subscribe to satellite services-it will incur continuous costs, and RFID handhelds only need to pay for the purchase. The most prominent problem with cost analysis is the lack of understanding of the business model: shippers of containers, not freight forwarders, need to pay for the use of RFID tags or satellite equipment. Port and warehouse owners pay to install RFID equipment at their own expense. Because the use of RFID can bring benefits to shippers, ports, and warehouse operators, the cost of RFID systems can be shared by multiple parties. However, the use of satellite equipment requires the owner to bear all the costs.
[ad_2]