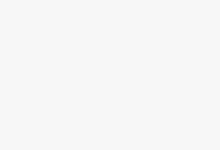
New Ideas of Applying RFTD Technology to Mining Plants and Enterprises
[ad_1]
The intelligent vehicle weighing management system launched by Shenzhen Xianshi Technology Co., Ltd. was applied to Wuhan Iron and Steel Plant, Shijiazhuang Iron and Steel Plant, Xiangtan Iron and Steel Plant and many other enterprises. After that, it is used for the automatic management of ore and fuel storage, and the monitoring of vehicles entering and leaving the factory. Important role. On the one hand, it greatly improves the efficiency of the measurement management of the entry and exit of raw materials and finished products, prevents the loopholes in manual operation, and improves the working conditions and labor intensity of the weighing measurement and transportation vehicle drivers. On the other hand, it has greatly promoted the pace of enterprise informatization construction, and has established an example of successful application of new technologies for the industry.
620)this.style.width=620;” border=0>
The gate bayonet management system of Wuhan Iron and Steel Plant Automatic Metering System of Shijiazhuang Iron and Steel Plant Mining Area Automatic management of fuel storage in Xiangtan Iron and Steel Plant
one,Industry background and application requirements
1.business background
The intelligent automobile weighing management system and the factory gate bayonet management system of Shenzhen Xianshi Technology Co., Ltd. have become an important part of the information management of Wuhan Iron and Steel Plant, Shijiazhuang Iron and Steel Plant, Xiangtan Iron and Steel Plant, etc., forming an efficient , Accurate, fast and anti-cheating new weighing management mode. The following takes the application of Wuhan Iron and Steel Plant as an example to introduce the basic framework of system implementation.
The vehicle weighing system of the Wuhan Iron and Steel Plant: The so-called intelligent vehicle weighing management system is based on the original vehicle weighing management system.RFIDThe technology realizes the automatic identification function of weighing vehicles, and merges the automatically collected weighing vehicle information into the weighing management system.The intelligent weighing management system applied to the Wuhan Iron and Steel Plant increased the passing speed of the metering department of the plant3-4Through automatic identification and accurate measurement of vehicle number, it effectively prevents the economic loss caused by man-made fraud to the mine. In addition, after the implementation of the system, the labor intensity of the staff and the error rate of manual weighing have been greatly reduced, the transparency of the fuel management process has been improved, and the informatization process of the power plant has been promoted.
The gate bayonet management system of Wuhan Iron and Steel Plant: The so-called gate bayonet management system refers to the management of various vehicles entering and leaving the factory.It has the functions of automatic identification, intelligent control, alarm prompt, information recording, data communication, query, statistics, analysis, etc., Vehicles entering the factory area at different timesNot only many, but also important to make the vehicle in and out convenient, fast and safe, adopt Shenzhen First TechnologyRFIDThe high-tech products of the management system realize the intelligent management of vehicles,The transparency of the management process has promoted the informatization process of vehicle management.
2.Application requirements
The automatic measurement system of the mining area is aimed at the fully automated (without human intervention) collection of automatic measurement, weighing and skinning (empty car) data using automobiles as a means of transportation to ensure the accuracy of the original data collection. Through the realization of automatic measurement, the operating time of each operation link can be greatly shortened, the connection and unloading ability of the measurement system can be improved, and the working environment of the measurement personnel and the car driver can also be improved, and the labor intensity can be reduced. For the management of the gate checkpoint, the vehicles entering and leaving the gate can be monitored from time to time, and the specific time of the vehicle entering and exiting can be inquired.RFIDIntelligent management of the gate bayonet improves the safety management of materials in the factory.
2. Project implementation goals
(1) Queue management of transportation vehicles. Vehicle queue management mainly completes the queue of transport vehicles, prevents vehicles from jumping in line, and improves the order of vehicle transportation.
(2)sampling. Sampling The sampling of the incoming ore is completed.
(3) Weighing. Weighing mainly completes the measurement of the gross weight of coal-carrying vehicles.
(4) Back to the skin. Treading mainly completes the measurement of the empty weight of the vehicle, and finally calculates the net weight.
(5)real time monitoring.Real-time monitoring mainly completes the real-time monitoring of the sampling, weighing, and peeling process, and timely understands the sampling, weighing and
The situation of the recovered vehicle in order to deal with it in time.
(6) Monitoring and management system. The monitoring and management system mainly completes the management and maintenance of basic system information, and the selection and setting of operating modes, etc.
(7) Factory gate management. Real-time monitoring of incoming and outgoing vehicles, and query the historical entry and exit times of vehicles.
Three, system design
1.System topology
The network topology of the system includes: monitoring and management system, vehicle queue management, weighing host, sampling host, leather backing host, gate bayonet management, real-time monitoring, database server and other online workstations, etc. The unit systems are connected together through the intra-plant LAN to realize data sharing.
2.System workflow
Before entering the mine, all transport vehicles first go to the vehicle queue management office to sort the queues. Only the transport vehicles after sorting can enter the factory area. After the transportation vehicles are sorted, they enter the sampling platform for sampling. When sampling, it is necessary to judge whether the vehicle jumps into the queue, if it is a jumper vehicle, it will not be sampled. After the sampling is completed, the vehicle drives into the truck scale for gross weight measurement. After the measurement is completed, it is loaded and unloaded. After the loading and unloading is completed, it drives into the truck scale for tare measurement. After the measurement is completed, the net weight is automatically calculated. If an abnormal phenomenon occurs during the weighing and peeling process, the system will automatically notify the real-time monitoring system, and the monitoring personnel can deal with it in time to ensure the normal operation of the system.
Four, system operation
According to the system workflow, the operation of the system is described in five parts below.
1.Vehicle fleet management
The vehicle queue management realizes the management of the transportation vehicle queue, thereby reducing the occurrence of queue jumping and improving the traffic rate of vehicles. Automatic vehicle queue management is accomplished through the automatic vehicle number recognition system.
The automatic identification system of vehicle number mainly includes microwave radio frequency card, reader, radio frequency cable, antenna and automatic identification software of vehicle number. Each transport vehicle is equipped with a microwave radio frequency card, and each microwave radio frequency card corresponds to a vehicle number. The automatic identification of transportation vehicles can be achieved through the microwave radio frequency identification card. Each time a transportation vehicle passes, the automatic vehicle number identification system automatically generates a queue number for this vehicle as a sampled queue sequence. The advantage of using the automatic vehicle number recognition system is that there is no human intervention, and the vehicle queue is objective and accurate.
2.sampling
An automatic vehicle number recognition system is installed at the sampling platform. When the transport vehicle enters the sampling platform, the automatic vehicle number identification system will automatically read the vehicle number information and determine whether the vehicle is a queue-jumping vehicle, and if it is, the sampling will be rejected.
3.Weighing
When the weighing is ready, the green indicator light is on, and the car stop is closed at the same time. After the sampling is completed, the truck scale can be driven into the truck scale for measurement when the truck scale is ready for weighing. After the vehicle enters the truck scale, the red indicator light is on, and the vehicle number automatic recognition system reads the vehicle number information. After the vehicle is positioned successfully, the metering software starts to measure. After the meter is successfully measured, the car stopper opens and a voice prompts the vehicle to leave the truck scale, which is displayed electronically The screen will display the measurement. After the vehicle is completely driven out of the truck scale, close the car stop and turn on the green indicator light, and wait for the next measurement. In the case of other situations during the measurement process, such as the vehicle cannot be located or the vehicle number cannot be read, the measurement software will automatically give voice prompts and send an alarm to the monitoring center to remind the management personnel to deal with it. During the whole weighing process, no human operation is required.
4.Peel back
The process of peeling back is basically the same as weighing. The difference between the two is mainly in the content of some voice and alarm information.
5.real time monitoring
All information in the four operation processes of vehicle queue management, sampling, weighing and skinning are fed back to the monitoring center host in real time, and the management personnel can understand the status of each work process in real time through the monitoring software system. For example, there are vehicles that jump in line at the sampling site, the vehicles cannot be positioned during weighing and skinning, and the vehicle number cannot be read, etc., can all be understood in the monitoring center.
In order to ensure uninterrupted work in the plant area, the automatic metering system adopts2Two working modes: automatic mode and manual mode. Under normal circumstances, the automatic method is adopted. When some hardware equipment in the system fails and cannot work in automatic mode, manual operation can be used to ensure the normal production of the factory. When the hardware equipment is repaired, switch to automatic Way. The manual method is a backup method.
5. Equipment selection criteria
The automatic identification technology used in the intelligent vehicle weighing management system and the factory gate bayonet management system is remoteRFIDsystem.The electronic label (car card) is mounted on the inner side of the front windshield of the transportation vehicle, and it is requiredRFIDThe recognition distance of the system is greater than6~
Attached:Sense-1830Integrated reader:
l Sense-1830The integrated reader is produced by Sincere Technology completely based on independent intellectual property rights902~928MHzThe integrated frequency reader fully embodies the leading innovative technology of Sincere Technology in long-distance readers, integrating advanced microchips, high frequency identification, low power, multi-protocol and high-speed data processing technology combinations;
l Built-in12dBi Linear horizontal polarization antenna, the farthest reading distance can reach
l compatibleEPC,ISO-18000-6,SaharaAnd many other protocols, can read and write in accordance withAmtech Intellitag,Philips UCODEEqualEPC Class0 Class1EPC GEN2High-frequency third-generation standard“electronic label“;
l The product is an all-weather industrial-grade product for outdoor use. It has an industrial aluminum alloy shell with anti-interference, lightning and waterproof capabilities, and is suitable for use in logistics, vehicles, personnel management and other occasions.
Attached:Sense-1830Integrated reader:
l Sense-1824The multi-channel reader is produced by Sincere Technology completely based on independent intellectual property rights902~928MHzFrequency4The channel reader, fully embodies the leading innovative technology of Sincere Technology in long-distance readers, integrating advanced microchips, high-frequency identification, low-power, multi-protocol and high-speed data processing technology combinations;
l Can be connected via high-frequency cables4Panel antennas with different gains extend the effective range of card reading and reduce user hardware costs. The farthest card reading distance can reach
l ReaderI/OThe interface has a two-way trigger function, which can be connected to an optoelectronic or mechanical trigger device to control the working status of the reader;
l compatibleEPC,ISO-18000-6,SaharaAnd many other protocols, can read and write in accordance withAmtech Intellitag,Philips UCODEEqualEPC Class0 Class1EPC GEN2High-frequency third-generation standard“electronic label“;
l The product needs to be installed indoors or in an industrial-grade product in a waterproof box. The industrial aluminum alloy shell has anti-interference, lightning and waterproof capabilities, and is suitable for use in logistics, vehicles, personnel management and other occasions.
[ad_2]