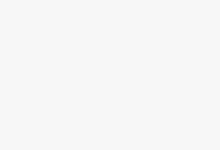
Office supplies in and out of warehouse management
[ad_1]
I. Overview
Warehousing logistics management is widely used in various industries, designing and establishing a complete set of warehousing management processes, improving warehousing turnover rate, reducing the occupation of operating funds, turning frozen assets into cash, reducing the cost caused by warehousing elimination, and improving the company An important part of production efficiency.
Warehouse management systems usually use barcode labels or manual warehouse management documents. These management methods have obvious disadvantages:
Barcode management: easy to copy, not stain-proof, not moisture-proof, and can only be read at close range
Manual entry: cumbersome work, large amount of data, easy to make mistakes and omissions, increase labor costs in warehousing
The workload of manual inventory is large, which leads to a long inventory cycle, and the missing or stolen goods cannot be found in time
The introduction of RFID radio frequency technology has made enterprise warehouse management transparent and more efficient. Encapsulate the electronic label in a bar code label, stick it on the package or pallet of each goods, and write the specific information and storage location of the goods in the label. At the same time, the detailed information of the delivery party can be written when the goods enter and leave the warehouse, and a fixed or hand-held reader can be installed in the warehouse to identify and monitor the circulation of the goods. The main advantages are:
Labor can be reduced by 20-30%;
99% of warehouse products are visualized, reducing the risk of missing goods;
Improved supply chain management will reduce work service time by 20-25%;
Improve the accuracy and reliability of storage information;
Efficient and accurate data collection provides operational efficiency;
Automatic collection of incoming and outgoing data to reduce human error;
Reduce enterprise warehousing logistics costs.
Today, with the rapid development of logistics automation technology, with the help of RFID fast scanning, barrier-free reading, etc., data collection and processing can be carried out quickly and accurately to achieve standardization and efficient operation of warehouses. Realize quick check and find goods, intuitive storage, scientific and reasonable. Through modern advanced network technology, real-time sharing of warehouse management information such as inbound, outbound, and inventory is realized in the course of enterprise operations. It is convenient for the company to supervise the goods; it is convenient for the warehouse to carry in, out, inventory, and picking of the goods; it is convenient for the company to understand the situation of the company’s goods in the warehouse.
2. Demand analysis
(1) Realize real-time monitoring and management of office supplies in and out of the warehouse;
(2) Realize real-time monitoring and management of personnel entering and exiting the warehouse;
(3) Realize the inventory status management of office supplies.
3. Scheme design
3-1. Item storage
After purchasing, after confirming the shopping list with the merchant, the list is sent to the library management, and the library management can make full use of the time to write the label in advance according to the list. At this time, the label status is not in storage. When the item arrives at the door of the warehouse, the warehouse manager takes the written label and scans it with a handheld machine, finds the corresponding item, attaches the label, and automatically uploads the information to the management software. After all items are confirmed to be correct, put it on the shelf and complete the entry. Library program, and the label status in the management software is changed to storage.
3-2. Collect items
The employee goes to the warehouse and finds the library manager to read the employee card. The management software records the card reading time and displays the number of items that the employee has received, whether he has the authority to claim it again. The library manager checks the inventory status and location of the item in the management software. After the warehouse manages the required items and scans them with the handheld device, the items are automatically registered in the employee’s information, and the employee takes the items out of the warehouse, and the management software records the time and changes the inventory status to out of the warehouse. To ensure that the outbound items are correct, it also allows the library manager to know the types and quantities of items out of the library in detail, and upload them directly instead of manually counting and registering on the computer as before.
[ad_2]