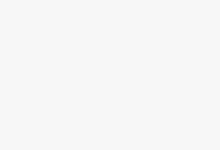
RFID asset life cycle management solution
[ad_1]
basic concepts
The product life cycle referred to in this plan refers to the service life of the product. After a product enters the use link, its use value and product attributes will change over time, presenting a process from more to less, just like human life, from birth, growth to maturity, and finally to decline. It is the product life cycle phenomenon.
System background
With the rapid development of the global economy and the development of the computer information industry, management tasks such as improving production methods, improving operating efficiency, reducing operating costs, and improving service quality have become the top priorities of all enterprises and institutions. As fixed asset management has the characteristics of wide distribution, large quantity, frequent adjustments, etc., in the current management mode, information distortion and lag caused by human factors in the transmission of asset change information cause the account to be inconsistent and cannot be optimized in time. Allocation has caused a large number of high-value assets to be idle and wasted, which seriously affects the authenticity of financial reports.
As a bridge between fixed assets and information systems, RFID technology can effectively integrate daily asset management activities with asset management systems, so as to achieve real-time synchronization of physical information and system information. Therefore, it has become possible to establish a set of product life cycle management system based on RFID technology to realize automatic management.
A good example of this trend is the use of high-value electronic equipment, such as high-value electronic equipment and laptop computers. In this field, manufacturers are keen to install smart labels for these products, the purpose is not only to track the use of the product, but also a means to record information throughout the product life cycle. Smart labels not only play a role in high-efficiency assembly lines, but also provide key data in the process of manufacturers using products. In addition, the new WEEE clause requires manufacturers to bear the processing costs at the end of the product’s life. Based on the above factors, it can be seen that the product smart label that can retain the manufacturer’s information is not just a luxury, but a real need for the product from the cradle to the grave.
System flow
RFID asset management system uses radio frequency technology (RFID), equip each fixed asset with an electronic tag with a globally unique ID number, and use a handheld reader for asset inventory, which can quickly read the electronic tag information on the device, and use the built-in communication method to read the tag information The wireless communication module is sent to the background server for processing. The fixed reader is used for access control, and the antenna adopts a circularly polarized antenna, which can ensure multi-angle tag recognition. In order to realize the comprehensive and accurate supervision of the physical fixed assets from the acquisition, requisition, transfer, inventory, cleaning to scrapping, etc., combined with the asset classification statistics and other reports, the “accounts, cards, and objects” can be truly matched.
Because RFID electronic tags have the technical characteristics of large storage capacity, fast transmission speed, non-counterfeiting, and concurrent identification, with the support of the asset management platform database, asset-related information can be recorded in the tag reliably and in real time, so as to perform real-time Asset management supervision has improved operating efficiency and reduced costs. The clear operation interface and accurate and timely data processing make the system as a modern operation mode, providing a more reliable basis for enterprise asset evaluation and decision-making, and avoiding hidden dangers that may be caused by the enterprise in the fixed asset management link.
We should look at radio frequency identification technology rationally. It is definitely not a burden in the production process, but a unique tool that can play an important role in the four stages of the product life cycle. The four stages of the product life cycle are production, circulation, after-sales service, and final treatment. Here is an example of a computer manufacturer to illustrate the advantages of radio frequency identification technology:
production process
In the middle of the computer production process, the readable and writable label records all the detailed information of the production process, including the supplier details of the part number, microprocessor, power supply, modem, interface card, etc. If necessary, these data can be transmitted through radio frequency technology to update the warehouse’s ordering procedure or automatically start the ordering procedure when the stock is insufficient. In addition, from assembly to test and final inspection in the production process, there are smart tags for full tracking and real-time recording. Here you can use handheld personal digital assistants (PDAs), or automatically use radio frequency identification at the entrance of the conveyor line.
This not only implements strict management of process supervision, but also records data in real-time in each process, allowing the management department to investigate the production situation on-site, eliminating the need to connect to the database through radio frequency. In addition, because the radio frequency technology covers key production data and real-time monitoring of the process, the management department can continuously evaluate and optimize the production process.
Circulation field
After the product enters various links in the circulation field, the advantages of radio frequency identification technology are more obvious. The circulation process generally includes logistics and warehousing, during which there must be sorting and shipping operations. Radio frequency identification can provide a device for products, so that the data of the product label can be partially updated, mainly referring to the detailed information of the goods received and sent. This method is applicable to both tray-packed and box-packed items. The data update can be done manually by a personal digital assistant with radio frequency identification, or it can be done automatically on the conveyor line by radio frequency entrances, compartment doors, and antennas on the trailer. Items, trays or boxes with radio frequency identification tags in the process of sorting and transportation have good traceability. The data formed is particularly useful to other circulation companies, because they can automatically determine the location of the goods through the network tracking service.
Use link
Product use link management includes operations such as addition, allocation, idleness, scrapping, maintenance, and inventory of assets. It includes the entire process of equipment from leaving the factory, putting into use, and scrapping. The equipment is equipped with electronic tags when leaving the factory, and the asset information is written in the tags. Every time an asset management operation is performed, the reader will read the electronic tags on the assets and send the information to the server for processing, thereby realizing asset tracking management .
1) Asset addition operation: Fill in the relevant information (site name, asset barcode, model, name) of the equipment to be managed in the card issuance program, and save the record in the database. Attach electronic tags with asset information (or hang on assets) as required.
2) Asset transfer operation: prepare the assets to be transferred, open the door that controls the travel switch, and the reader is in the state of reading tags at this time. Take out the asset with the electronic label, walk out from the door, observe the sound and light prompt on the reader and the LED display to show the number of assets, and confirm that the electronic label on the device is read. After closing the door, the assets have been transferred from the base station. Bring the asset to the destination that needs to be allocated, open the door, bring the asset into the base station, and confirm that the electronic tag on the asset is correctly read. Close the door and complete the asset allocation operation.
3) Asset maintenance operation: prepare the equipment that has failed, and open the door that controls the travel switch, so that the reader is in the state of reading tags. Take out the faulty device, observe the digital tube display on the reader, and confirm that the label is read correctly. Close the door of the base station, and the malfunctioning device will be transferred away from the base station. Take the equipment to the warehouse maintenance area, press the reader control button (the indicator light on the button is on), confirm that the label information on all equipment is correctly read, press the reader control button again (the indicator light on the button) Off), the device is now under maintenance.
4) Asset scrapping operation: prepare the scrapped equipment, open the door that controls the travel switch, and make the reader in the state of reading tags. Take out the end-of-life equipment and confirm that the label is read correctly. Close the door of the base station, and the scrapped equipment will be removed from the base station. Take the equipment to the scrap area of the warehouse, press the control button of the reader in the scrap area, and confirm that the label information on the equipment has been read correctly. Press the reader control button again to complete the equipment scrapping operation.
5) Asset inventory operation: press the “I/O” switch of the handheld to turn it on. At the top of the interface, click to open the connectivity window, click to connect to GPRS, and start the inventory program.
Scrap processing
According to the latest WEEE regulations, manufacturers of various electronic meters and other electronic products such as kitchen appliances, refrigerators and other white goods must bear the cost of recycling. After products have smart labels, this work can be simplified a lot. With the label, the product is effectively registered during recycling and disposal, which facilitates the logistics process, confirms the code of the processed item, and can calculate the remuneration that the recycling department should receive.
System Features
1) The entire system has the characteristics of long-distance rapid identification, high reliability, high confidentiality, easy operation, and easy expansion.
2) Establish safe and reliable asset files, strengthen asset supervision through high-tech, rationally allocate resources, reduce resource waste, and prevent asset loss.
3) Fully consider the actual situation of the company, study the problem from the perspective of professional technology, and effectively solve the chaotic, disorderly and poor real-time problem in asset management. Provide an advanced, reliable, and applicable digital platform for automatic identification and intelligent management of incoming and outgoing assets, so that the company’s ability to manage internal assets in real time and dynamically is qualitatively improved.
4) Make full use of the RFID automatic collection and communication wireless remote transmission functions to realize the real-time consistency of asset change information and system information, and realize the effective real-time monitoring and recording of the work process by the back-end system, so that managers can be timely in the office Understand the allocation and use of assets.
5) All asset data are entered at once, and the system automatically judges the asset status based on the data collected by RFID readers in different regions.
System benefits
1) Realize asset life cycle management and automatic asset management
Using RFID technology, radio frequency automatic identification and GSM communication network wireless remote transmission functions, realize the intelligent dynamic real-time tracking and centralized monitoring and management of the asset life cycle (new addition, allocation, idle, scrap, maintenance, etc.) process, the entire management process does not need Any manual intervention. It provides accurate reference data for enterprise investment decision-making and rational asset allocation, effectively increases the marginal benefit of investment and increases the utilization rate of assets, and reduces unnecessary equipment investment and idle waste.
2) Realize the synchronization management of people, place, time and things in asset management
The system organically embeds the daily asset management work into the asset management system, realizes the recording of the tasks, locations, objects, time and other information involved in the daily operation process of the assets, and introduces the SMS reminder and alarm function, and the system realizes the daily work The effective supervision of the company reduces the pressure of daily asset management, saves the cost of investing a large amount of manpower and material resources for asset inventory and unnecessary allocation every year, avoids asset loss caused by various factors, and improves corporate management efficiency.
3) Eliminate the workload and error rate of manual recording and information transmission
Through the implementation of the system, the workload and error rate of manual recording and information transmission have been completely eliminated, and the expected application effect has been achieved within a certain range.
[ad_2]