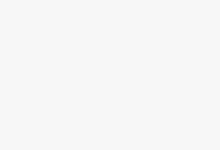
RFID home management system solution
[ad_1]
1 Overview
With the continuous expansion of domestic furniture manufacturing enterprises, the amount of raw material warehouse material receipts and expenditures and procurement information is also increasing. Traditional manual management fundamentally cannot meet the needs of enterprises. Sichuan Kailuwei has been engaged in the application of RFID technology for a long time. , We believe that the combination of RFID technology and the furniture warehouse management system can make the daily management of the warehouse have a more convenient, concise and efficient operating environment. The furniture warehouse management system can easily realize basic information entry, receipt, delivery, checkout, payment, installation and other functions, efficiently complete the statistics, calculation and summary of various warehouse management information, and quickly and accurately output the query results , Print out all kinds of reports, real-time reflection of warehouse inventory, supplier payables and other information.
At present, the domestic furniture warehouse management is still in the most basic manual management stage. Since the components of each different product are different, the required raw materials and accessories are various in varieties and specifications, manual operation can easily cause confusion in warehouse management and difficult control of warehouse inventory. When the production of each batch of products is about to end, there is always a shortage or excess of this accessory, which causes delivery delays or inventory backlog; each reconciliation takes a lot of time, and often makes mistakes, it is difficult to reconcile the accounts, and the actual inconsistency is serious. .
RFID is a radio frequency identification, inductive electronic chip or proximity card, proximity card, non-contact card, etc. It is a non-contact identification technology, which has the advantages of large amount of information storage, rapid identification, and label not easy to damage.
2. Introduction to RFID Technology
RFID (Radio Frequency Identification), or radio frequency identification, is an automatic identification technology that emerged in the 1990s. A typical RFID system consists of three parts: a radio frequency electronic tag, a reader or reader, and an antenna. It integrates multiple technologies such as coding, carrier, identification and communication. The main principle is to use radio waves to read, write and identify a marked medium. Non-contact is its obvious feature.In practical applications, the reader writes data in a specific formatRFIDLabel, and then attach the label to the surface of the object to be identified. The reader can also read and identify the electronic data stored in the electronic tag without contact, so as to realize the functions of long-distance, contactless collection and wireless transmission of object identification information.
2.1. The working principle of RFID
The process of using radio waves to read, write, and identify a marked medium, and non-contact is its obvious feature. In practical applications, the reader writes data in a specific format into the RFID tag, and then attaches the tag to the surface of the object to be identified. The reader can also read and identify the electronic data stored in the electronic tag without contact, so as to realize the functions of long-distance, contactless collection and wireless transmission of object identification information. RFID technology can identify high-speed moving objects and can identify multiple tags at the same time, and the operation is quick and convenient.
The RFID system consists of three parts:
Electronic tag (Tag): Composed of coupling components and chips, each tag has a unique electronic code, attached to the object to identify the target object;
Reader (Reader): a device that reads (and sometimes writes) tag information, which can be designed as a handheld or fixed type;
Antenna: Transmit radio frequency signals between the tag and the reader.
After the tag enters the magnetic field, it receives the radio frequency signal from the reader, and uses the energy obtained by the induced current to send out the product information stored in the chip (PassiveTag, passive tag or passive tag), or actively send a signal of a certain frequency (ActiveTag) , RFID tag or active tag); after the reader reads and decodes the information, it is sent to the central information system for relevant data processing.
3. System function
(1) Warehouse management
Deploy fixed RFID readers at the door of the warehouse, and carry out radio frequency planning according to the on-site environment. For example, four antennas can be installed up, down, left and right to ensure that RFID electronic tags are not missed. After receiving the warehousing order, put the product into the warehouse according to certain rules. When the RFID electronic tag (ultra high frequency) enters the electromagnetic wave range of the RFID fixed reader, it will be activated automatically, and then the RFID electronic label and RFID fixed reading The writer communicates. When the RFID tag is collected, it will be compared with the order to check whether the quantity and model of the goods are correct. If there are errors or omissions, they will be processed manually. Finally, the goods will be transported to the designated location and placed in accordance with the rules. The main advantage of RFID in warehouse management applications is non-contact long-distance identification, and can be read in batches, which improves efficiency and accuracy.
(2) Outbound management
According to the pick-up plan, the goods out of the warehouse are sorted and processed and managed out of the warehouse. If the quantity out of the warehouse is large, push the goods to the door of the warehouse in batches, use a fixed reader to communicate with the tags, collect the RFID electronic tags of the goods out of the warehouse, and check whether they correspond to the plan. If there are errors, manually as soon as possible deal with. For a small amount of goods, RFID handheld terminals can be used to collect information from RFID electronic tags (handheld scanners or RFID tablet computers). When an error occurs, an alarm will be issued, and the staff should deal with it in time, and finally send the data to the management center Update the database to complete the delivery.
(3) Warehouse search management
When looking for furniture or semi-finished products, you only need to set the required conditions on the corresponding handheld terminal, and use a mobile reader to scan the area where the furniture is stored. The information stored in the RFID file is continuously transmitted to the reader through wireless signals, and the reader will The received information is automatically compared with the set conditions, and a prompt will be issued after the comparison is successful, and the staff can immediately confirm the location of the required file, so that the required furniture can be extracted quickly and accurately.
(4) Installation and implementation management
On-site installation of materials is based on the installation requirements through the RFID reader to scan to confirm the required furniture panels. Avoid the inability to complete the assembly of the furniture at the user’s site due to the lack of plates. Improve installation efficiency, improve work quality, and customer satisfaction.
(5) Inventory management
In accordance with the requirements of warehouse management, conduct regular and irregular inventory. The traditional inventory is time-consuming, labor-intensive, and error-prone. All these RFID solves these problems. When there is an inventory plan, the RFID handheld terminal is used to carry out the inventory scan of the goods, and the information of the inventory can be transmitted to the back-end database through the wireless network and carried out with the information in the database. Comparing, the generated difference information is displayed on the RFID handheld terminal in real time, and it is provided to the inventory staff for verification. After the inventory is completed, the inventory information is checked with the database information in the background, and the inventory is completed. In the inventory process, the system uses RFID non-contact reading (usually within 1 to 2 meters) to read clothing goods information very quickly and conveniently. Compared with the traditional model, it will improve a lot of efficiency and inventory accuracy. sex.
(6) Basic information management
Set and manage the attributes of the goods, the main functions are, add, edit, delete, and query the basic attributes of the goods stored in the warehouse. In this way, it can be set according to the attributes of the operating products of different enterprises, and ensure that it meets the individual needs of each enterprise. The warehouse can also be divided into locations, which can be divided into units such as warehouses, areas, and locations, so that large-scale warehouses can be managed more accurately. Warehouse managers at all levels can query and perform related business operations for inventory information of different dimensions.
(7) System information management
Fully consider the scalability and security of the system, and provide reasonable tools to ensure system security. System management mainly completes the correction and maintenance of system operating parameters. Complete permissions assignment, add, modify, and delete data forms. At the same time, it has a complete login program (user name and password). Different personnel are given different permissions, which are set by the system administrator. The system also provides a one-key data backup and recovery function to further ensure the security and continuity of business data.
(8) Statistical analysis of data
The system can form statistical reports according to time, quantity and other elements, clarify the turnover period and efficiency, and facilitate the planning and control of the inventory management business process. The unified operation can speed up the speed of goods in and out of the warehouse, thereby increasing the throughput of the inventory center, and can provide Managers and decision makers provide timely and accurate inventory information, which can improve the accuracy of goods inquiries, reduce inventory levels, and improve the efficiency of the logistics system to strengthen the competitiveness of enterprises.
The furniture warehouse management system integrates RFID technology for data collection and daily business management, establishes a furniture information RFID management platform, supports important business processes of clothing warehouse management, and improves the efficiency of core business processes such as warehousing, outgoing, and inventory. Effect. Realize automatic identification, information sharing and tracking, and bring improvements in productivity, accuracy, profitability and customer service.
[ad_2]